Revolutionizing Technology: The Era of the Integrated Chip
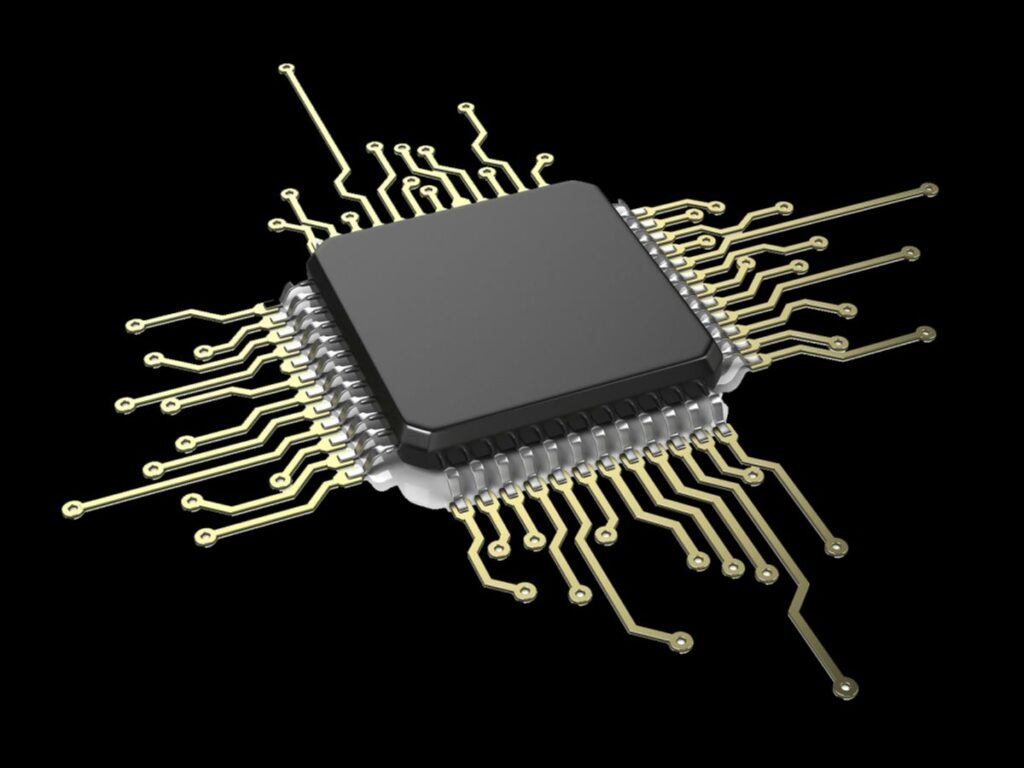
In the realm of semiconductor technology, a transformative shift is underway, heralding the advent of integrated chip design. This article explores the cutting-edge developments in chiplet technology, packaging innovations, and the challenges and opportunities in semiconductor scaling. We delve into how the industry is evolving through collaboration and standardization, and what this means for the future of computing power and efficiency.
Key Takeaways
- The transition from monolithic systems to chiplets marks a significant evolution in microprocessor design, potentially extending Moore’s Law.
- Advancements in 3D design and transistor stacking are revolutionizing chip packaging, enhancing performance and power efficiency.
- Despite the challenges of scaling beyond 2nm, innovations in transistor development and wafer production are crucial for next-generation chips.
- Interface standardization and collaborative efforts across the chip industry are vital for the integration and harmonization of chiplet manufacturing.
- The economic implications of semiconductor advancements underscore the industry’s push for more powerful, efficient, and cost-effective chip solutions.
The Dawn of Chiplet Technology
The Shift from Monolithic Systems to Multi-Chip Modules
The semiconductor industry is witnessing a paradigm shift with the advent of multi-chip modules (MCMs), which represent a departure from the traditional monolithic system-on-a-chip design. This new approach leverages the concept of ‘chiplets’, small, function-specific chips that can be combined to form a complete system. The flexibility of MCMs allows for a tailored configuration, where chiplets are selected and integrated based on the specific needs of a device, leading to optimized performance and efficiency.
The benefits of transitioning to MCMs are manifold. Manufacturers gain the ability to mix and match chiplets, which can include a combination of cutting-edge and legacy technologies. This modular design not only facilitates incremental upgrades but also reduces the need for complete system overhauls, thereby saving costs and time. Furthermore, the adaptability of MCMs caters to a diverse range of customer requirements, making them a versatile solution in the ever-evolving tech landscape.
The shift towards MCMs is not just about flexibility and cost-efficiency; it’s also seen as a critical step in sustaining the pace of technological advancement. As the limits of transistor miniaturization are approached, companies like Intel, AMD, and Apple are turning to chiplet manufacturing as a means to continue the progression dictated by Moore’s Law. AMD’s latest MI300, for instance, utilizes a modular architecture that underscores the industry’s commitment to this innovative direction.
The Rise of Modular Architecture in Microprocessors
The microprocessor industry is undergoing a significant transformation with the adoption of modular architecture. This shift is characterized by the move from traditional monolithic systems to more flexible and scalable multi-chip modules (MCMs). These MCMs combine chiplets, or small chips with specialized functions, to create a cohesive system that rivals the performance of a single large chip.
The advantages of this approach are numerous. Chiplets allow for a more efficient design process, as each module can be optimized for its specific task. Additionally, this modularity facilitates easier upgrades and repairs, as individual chiplets can be replaced without the need to redesign the entire system. The table below outlines the key benefits of modular architecture in microprocessors:
Benefit | Description |
---|---|
Scalability | Enables the system to grow with demand by adding more chiplets. |
Flexibility | Allows for customization and specialization of functions. |
Efficiency | Reduces waste by only using the necessary components for a given task. |
Upgradeability | Simplifies updates and repairs by swapping out individual chiplets. |
The emergence of chiplets as a cornerstone of modern semiconductor design is not just a technical evolution; it represents a strategic pivot in the industry. Companies like Intel, AMD, and Apple have embraced this new paradigm, launching products that leverage the strengths of modular architecture. As the limits of traditional scaling become more apparent, the role of chiplets in sustaining the momentum of Moore’s Law becomes increasingly critical.
The Impact of Chiplets on Moore’s Law
The relentless pursuit of miniaturization in semiconductor technology has reached a pivotal juncture. As the industry grapples with the diminishing returns of traditional scaling, chiplets emerge as a beacon of innovation, potentially redefining Moore’s Law. This paradigm shift from monolithic systems to multi-chip modules (MCMs) represents a strategic pivot to sustain the cadence of technological advancement.
The adoption of chiplet architecture by industry giants such as Intel, AMD, and Apple underscores its significance. AMD’s MI300, for instance, leverages a modular approach to deliver enhanced performance. The transition to chiplets is not merely a design choice but a necessity to maintain the momentum of transistor doubling, as envisioned by Gordon Moore. However, the transition is not without its challenges. The lack of standardized interfaces has been a barrier, impeding the ability to mix and match components from different manufacturers. Despite this, the collective efforts of companies within a consortium aim to overcome these obstacles, fostering a future where chiplets can be seamlessly integrated.
Below is a list of key points highlighting the relationship between chiplets and Moore’s Law:
- Chiplets offer a viable path to continue Moore’s Law beyond the limitations of current lithography techniques.
- Industry leaders are actively integrating chiplet technology into their product lines, signaling a shift in design philosophy.
- Standardization efforts are crucial for the widespread adoption and interoperability of chiplets.
Advancements in Chip Packaging and Power Efficiency
The Evolution of 3D Design and Transistor Stacking
The relentless pursuit of miniaturization in semiconductor technology has led to a transformative approach in chip design: the evolution of 3D design and transistor stacking. This innovative method leverages the z-direction, a previously underutilized dimension, to enhance electrical performance and overcome the limitations of planar architectures. The 3D integrated circuit, a notable example of this trend, represents a significant leap forward from traditional, flat chip layouts.
Engineers are now constructing transistors atom-by-atom, with some structures reaching a mere 50nm in height and switching on and off billions of times per second. The 3D shape of these transistors allows for a dense packing within a chip, with a single square millimeter accommodating up to 200 million transistors. The industry’s ambition doesn’t stop there; plans are underway to integrate a staggering trillion transistors on a single chip in the foreseeable future.
As lateral scaling reaches its physical limits, the industry is shifting its focus vertically. This ‘skyscraper’ approach to chip design is not only a testament to human ingenuity but also a strategic move to continue the trend of increasing power and efficiency within the same spatial constraints. Advanced packaging techniques are evolving in tandem, with a clear trend towards stacking chips vertically to maximize performance and optimize space utilization.
Advanced Packaging Techniques for Performance Enhancement
As the semiconductor industry continues to evolve, advanced packaging techniques have emerged as a cornerstone for performance enhancement. The transition to vertical design, often referred to as 3D packaging, allows for stacking chips, which not only improves performance but also optimizes the use of space. This approach is a departure from traditional horizontal layouts and is seen as a pivotal change in the industry, acknowledging the limitations of planar expansion.
In the realm of advanced packaging, a variety of configurations are possible, each tailored to meet specific performance and efficiency goals. For instance, the integration of chiplets into multi-chip modules (MCMs) represents a significant shift from the monolithic system-on-chip architecture. By combining separate silicon pieces with distinct functionalities, these MCMs function cohesively as a single, more powerful electronic brain.
The advancements in packaging are not just about stacking layers; they also involve innovative bonding techniques and the exploration of new materials. Hybrid bonding, including 2.5D and 3D configurations, is at the forefront of these developments. Additionally, emerging solutions like silicon photonics are gaining traction, offering the potential for even greater performance leaps in fields such as artificial intelligence (AI) and high-performance computing (HPC).
Innovations in Power Delivery with Back-Side Power Architecture
The integration of back-side power architecture marks a significant leap in chip design, addressing the traditional bottlenecks caused by power and signal wires above the transistors. By relocating power wiring to the underside of the chip, efficiency is markedly improved, as this separation allows for a more direct power route and less wire entanglement.
Innovative power management solutions have emerged to complement this architectural shift. These include:
- Advanced Battery Management Systems (BMS) for optimal battery health and performance.
- Efficient Converters that minimize energy loss during power conversion, such as state-of-the-art DC-DC and AC-DC converters.
The implementation of back-side power architecture in upcoming 2nm chip designs is a testament to the industry’s commitment to overcoming the challenges of power delivery. This rethinking of chip wiring not only enhances efficiency but also paves the way for further advancements in semiconductor technology.
The Future of Semiconductor Scaling
Challenges and Opportunities Beyond the 2nm Chip
As the semiconductor industry approaches the 2nm chip milestone, the landscape of chip manufacturing is poised for significant transformation. The transition to smaller nodes is not merely a matter of scaling down; it introduces a plethora of new challenges and necessitates innovative solutions. TSMC’s Cao highlights that transistor advances require novel approaches, such as lateral construction, which diverges from traditional vertical methods.
The pursuit of enhanced power and efficiency has led to a rethinking of chip design. Engineers are exploring 3D designs and transistor stacking as alternatives to the conventional side-by-side arrangement. This shift is driven by the need to overcome the diminishing returns of current processes, which have been plagued by poor yield rates and only marginal improvements in efficiency.
Despite these hurdles, the industry remains optimistic. Intel’s Ben Sell emphasizes that we are in the midst of a transformative era for transistor innovation. Technologies that were once theoretical discussions are now becoming tangible in market-ready devices. The journey ahead is filled with both economic and technological stakes, as advances in chip manufacturing demand extensive R&D investment and confront the perils of working at the nanoscale. Precision, repeatability, and extreme cleanliness are paramount in the clean rooms of fabs, where the slightest contaminant can render a chip defective.
The table below summarizes the key challenges and opportunities facing the industry as it forges ahead into the realm of 2nm chips and beyond:
Challenge | Opportunity |
---|---|
Lateral transistor construction | Exploration of new design paradigms |
Poor yield rates | Advancements in manufacturing precision |
Marginal efficiency gains | Development of 3D stacking techniques |
High R&D costs | Economic benefits of innovation |
Cleanliness in fabs | Improvement in clean room technologies |
The Role of Advanced Transistor Development in Next-Gen Chips
The relentless pursuit of miniaturization in semiconductor technology has led to transistors being constructed on an almost atomic scale. Advanced transistors now stand mere nanometers tall, switching on and off billions of times per second. This incredible density allows for hundreds of millions of transistors in a space as small as one square millimeter, with the ambitious goal of fitting a trillion transistors on a single chip in the future.
Innovative approaches to transistor design, such as vertical structures and novel packaging methods, are essential as the industry moves forward. The complexity of these designs necessitates a reimagining of chip architecture, with a focus on chip integration as a key battleground for semiconductor advancement.
The transition to next-generation chips, such as those on the 2nm scale, introduces new challenges in the manufacturing process. TSMC’s Cao highlights the need for lateral construction in certain elements, indicating a shift from traditional vertical assembly. Despite the difficulties faced with current 3nm processes, including suboptimal yield rates and only incremental efficiency gains, industry leaders like Intel’s Ben Sell are optimistic, viewing the current phase as a midpoint in the journey of transistor innovation.
The fabrication of each new chip generation is a monumental task, involving over a thousand precise steps. Chris Auth from Intel emphasizes the necessity for bold experimentation in the development of advanced transistors, which are now beginning to appear in consumer devices.
The Economic and Technological Stakes of Wafer Production
The production of semiconductor wafers is a high-stakes endeavor, with each wafer potentially representing thousands of pounds in value upon leaving a top-tier fabrication plant. Yield is the percentage of functional devices on a silicon wafer, and it stands as a critical metric in an industry where the cost of production is exorbitant. The yield rate directly influences the economic viability of semiconductor manufacturing, making it a focal point for ongoing research and development.
The process of creating these wafers is intricate and requires advanced technology, such as the use of extreme ultraviolet light by multi-million-dollar machines to etch fine patterns onto the wafers. This level of precision demands expertise that can be likened to a ‘PhD thesis level of knowledge.’
As the industry approaches the limits of traditional scaling, with the 2nm chip on the horizon, there is a pressing need to innovate beyond just size reduction. The future may hinge on the ability to enhance performance through 3D designs and transistor stacking, as well as the economic implications of wafer production in a market driven by commodification and price competition.
Collaboration and Standardization in the Chip Industry
The Importance of Interface Standards for Chiplet Integration
The integration of chiplets into a cohesive system hinges on the establishment of standardized interfaces. Without a common set of rules for these interfaces, the potential to create a harmonious ecosystem of interoperable components from different manufacturers remains untapped. The vision for a future where chiplets can be mixed and matched like Lego pieces is dependent on this standardization.
The industry’s push towards standardization is evident in the formation of consortia by leading companies such as TSMC, Intel, Samsung, AMD, and Google. Their collective goal is to overcome the barriers to chiplet adoption by agreeing on interface standards that would allow for seamless integration across various chiplet designs. This collaborative effort is a testament to the recognition of standardized interfaces as a cornerstone for the next generation of chip technology.
- Consortium Formation: Leading tech companies unite to set interface standards.
- Interoperability: Standardized interfaces are crucial for chiplet reusability.
- Industry Vision: A future of ‘Lego-like’ chiplet integration is on the horizon.
The commitment to interface standardization is not just about technological advancement; it’s about ensuring the longevity and scalability of chiplet-based systems. As the industry moves forward, these standards will play a pivotal role in maintaining the pace of innovation and keeping Moore’s Law relevant in the era of chiplets.
Consortium Efforts to Harmonize Chiplet Manufacturing
The semiconductor industry is witnessing a pivotal transformation with the advent of chiplet technology. The formation of a consortium by leading companies aims to address the critical challenge of interface standardization. This collaboration includes industry giants such as TSMC, Intel, Samsung, AMD, and Google, who share the vision of interoperable chiplet designs. The consortium’s goal is to create a unified framework that would allow for seamless integration of chiplets from different manufacturers, ultimately enabling a mix-and-match approach to semiconductor design.
At the forefront of this initiative is the Chiplet Summit, an event that brings together stakeholders to discuss the future of chiplet standardization. The summit serves as a platform for promoting the adoption of common standards, with the Universal Chiplet Interconnect Express (UCIe) being one of the key proposals. The UCIe aims to provide a standardized interconnect for chiplets, which is crucial for the technology’s success and widespread adoption.
The consortium’s efforts are not just about technical harmonization; they also represent a strategic move to sustain Moore’s Law. With companies like AMD already launching products with modular architecture, such as the MI300, and others like Nvidia in development, the push for chiplet manufacturing is seen as essential for continued performance gains in the semiconductor industry.
Cross-Company Collaboration to Sustain Industry Growth
The semiconductor industry is witnessing a paradigm shift towards cross-company collaboration, which is essential for sustaining growth and innovation. The formation of consortia, such as those by leading companies like TSMC, Intel, Samsung, AMD, and Google, underscores the commitment to standardization and interoperability. These alliances aim to establish common interface standards that will enable the seamless integration of chiplets from different manufacturers, fostering a more modular and flexible ecosystem.
The benefits of such collaboration are manifold, including accelerated innovation cycles, shared R&D costs, and the pooling of expertise. However, the path to harmonized manufacturing is not without its challenges. The table below highlights the key areas of focus for these collaborative efforts:
Focus Area | Description |
---|---|
Interface Standards | Development of universal protocols for chiplet communication. |
R&D Investment | Joint funding of research to drive technological breakthroughs. |
Intellectual Property | Negotiation of IP sharing agreements to facilitate cooperation. |
Verification Processes | Implementation of hybrid verification methods for enhanced security. |
As the industry continues to evolve, the role of such collaborations will become increasingly critical. They not only promise to push the boundaries of what’s possible in chip technology but also ensure that the pace of innovation does not decelerate due to isolated efforts. The collective push towards a standardized future is a testament to the industry’s recognition that unity is strength, especially when facing the intricate challenges of next-generation semiconductor scaling.
Conclusion
As we stand on the brink of a new era in semiconductor technology, it is clear that the integrated chip is undergoing a transformative evolution. The shift towards chiplets and multi-chip modules represents a paradigm change from the traditional monolithic system on a chip, promising to keep Moore’s Law relevant by enabling further scaling and integration. Innovations in packaging, such as advanced 3D stacking and back-side power architecture, are set to enhance performance and efficiency, overcoming the physical limitations that once seemed insurmountable. The industry’s push for standardization and the collaborative efforts of tech giants signal a future where chiplets could become as interchangeable as building blocks, fostering a new wave of creativity and flexibility in chip design. As these technologies mature and become widely adopted, we can anticipate a surge in computing power that will fuel the next generation of technological advancements, reshaping our digital landscape in ways we are only beginning to imagine.
Frequently Asked Questions
What are chiplets and how do they differ from traditional system-on-a-chip designs?
Chiplets are smaller, modular pieces of silicon that perform different functions and are bundled together to work as a cohesive unit, as opposed to traditional system-on-a-chip designs where the entire microprocessor is built on a single piece of silicon. This shift to multi-chip modules (MCMs) allows for more flexibility and scalability in microprocessor design.
How does chiplet technology impact Moore’s Law?
Chiplet technology is believed to be a key factor in keeping Moore’s Law alive, as it allows for the continuation of increasing the number of transistors in integrated circuits through modular architecture, despite the physical limitations faced by traditional scaling methods.
What advancements are being made in chip packaging for improved performance?
Advancements in chip packaging include 3D design and transistor stacking, which allow for more transistors in the same space by building them vertically. Advanced packaging techniques also aim to improve performance by efficiently bundling chips together.
What is the significance of back-side power architecture in chip design?
Back-side power architecture involves moving power wiring below the transistors, separating it from signal interconnects. This rethinking of chip wiring can significantly improve efficiency by reducing bottlenecks caused by traditional power and signal integration.
Why is collaboration and standardization important in the chip industry?
Collaboration and standardization are crucial for the widespread adoption of chiplets, as they allow for the creation of interface standards that enable mix-and-match of products from different manufacturers. This fosters innovation and sustains industry growth by making chiplet integration more seamless.
What are the challenges faced in semiconductor scaling beyond the 2nm chip?
As engineers approach the 2nm chip, the challenges include managing the physical limitations of transistor size, which is nearing atomic scales, and the economic and technological hurdles associated with developing new fabrication techniques and materials for next-generation chips.