Maximizing Efficiency in Wafer Processing: Techniques and Innovations
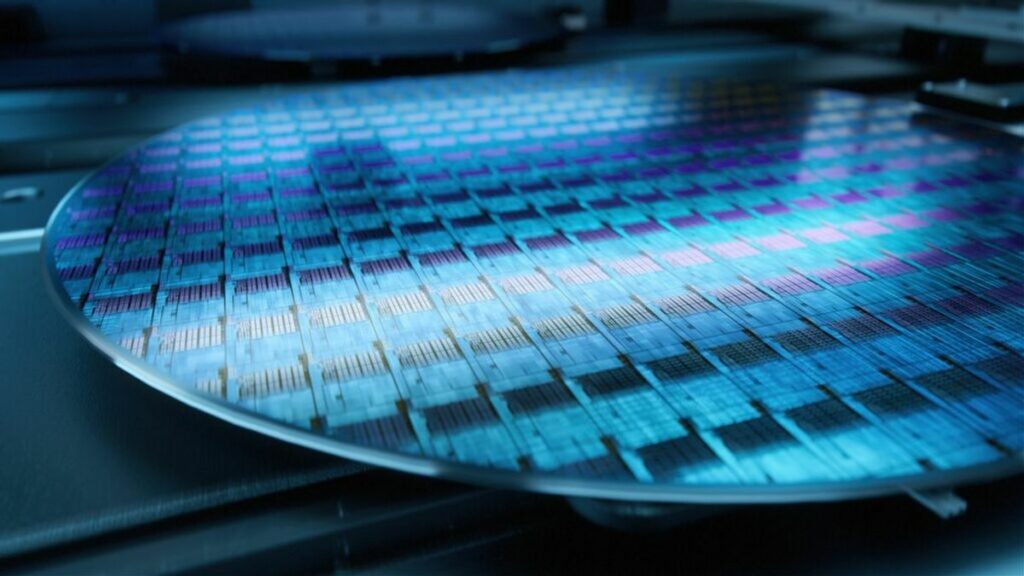
In the ever-evolving field of semiconductor manufacturing, maximizing efficiency in wafer processing is crucial for meeting the growing demands for smaller, more powerful electronic devices. This article delves into various techniques and innovations that have been developed to enhance the throughput and precision of wafer processing steps, from laser-assisted slicing to advanced motion systems and beyond. We explore how these advancements contribute to the efficiency and yield of semiconductor fabrication, ensuring that the industry can keep pace with technological advancements.
Key Takeaways
- Laser-assisted wafer slicing leverages ultra-short pulse lasers to create a weakened region for controlled cleaving, improving yield and reducing material loss.
- Stealth dicing techniques eliminate kerf-loss associated with traditional cutting methods, enabling the production of thinner SiC devices and conserving valuable materials.
- Advanced motion systems, including 3-DOF and 5-DOF stages, enhance the precision of wafer processing, allowing for intricate semiconductor designs with higher manufacturing standards.
- Semiconductor fabrication technologies such as etching and thin-film deposition are integral in transforming silicon wafers into integrated circuits, with innovations in these processes driving efficiency.
- Improvements in photolithography and ion implantation are critical for miniaturization, with advancements in masking and light exposure techniques leading to precision doping and improved transistor operation.
Laser-Assisted Techniques in Wafer Slicing
The Role of Lasers in Semiconductor Manufacturing
Lasers have become indispensable in the realm of semiconductor manufacturing, offering precision and efficiency in wafer slicing. The integration of lasers not only enhances throughput but also significantly improves defect control. This leads to sustainable higher yields, which is a critical factor in the industry’s fast-paced environment.
The use of lasers allows for the implementation of advanced techniques such as stealth dicing, which reduces material waste and increases the number of dies per wafer. Additionally, the ability to guide cracks with external forces like bonding and pressing ensures that the material splits precisely along the laser-conditioned layer.
Advantages | Laser Cutting | Traditional Cutting |
---|---|---|
Throughput | High | Moderate |
Precision | High | Low |
Defects | Fewer | More |
Yield | Higher | Lower |
The quest for a reliable, efficient, and electrically-pumped Si-based laser remains a challenge. However, significant strides have been made in developing quantum dot (QD) lasers, particularly in the 1.3-μm range. Extending this technology to the 1.55-μm telecommunication region is a current focus, with the integration of III-V compound semiconductors on Si-based substrates showing great promise for on-chip applications.
Advantages of Laser-Modified Cutting
Laser-modified cutting stands out as a transformative approach in semiconductor manufacturing, particularly in the realm of wafer dicing. Unlike traditional methods that often involve physical contact and can induce mechanical stress, laser cutting employs ultra-short pulse lasers to create a predefined weakened layer within the wafer. This precision enables manufacturers to achieve controlled cleaving with minimal material deformation and without thermal damage to the wafer’s surfaces.
The benefits of this technique are manifold. Not only does it enhance throughput, but it also significantly improves defect control, contributing to sustainable higher yields. Moreover, the absence of kerf-loss, which is common with wire saws, translates into a substantial yield improvement and the potential for thinner device production. The following points encapsulate the key advantages:
- Higher precision and control over the slicing process due to the non-contact nature of lasers.
- Reduced material waste as a result of eliminating kerf-loss.
- Enhanced yield from the same ingot size, thanks to the efficiency of the laser process.
- Improved thermal management, preventing damage to the wafer during cutting.
By optimizing laser parameters and beam delivery, the process can be tailored to different materials and thicknesses, ensuring the integrity of the wafer and paving the way for the production of sub-100 µm thin devices.
Optimizing Laser Parameters for Material Integrity
The integrity of silicon wafers during the cutting process is paramount, as it directly impacts the performance and reliability of the final electronic components. Optimizing laser parameters is crucial for maintaining material integrity while slicing the wafer from the ingot. Ultra-short pulse lasers condition a specific layer within the material, creating a weakened region that allows for controlled cleaving without thermal damage to the interfaces.
External forces, such as bonding and pressing forces, are applied to guide cracks along the laser-conditioned layer, ensuring a precise split. This method contrasts with traditional cutting techniques, offering a fast and cost-efficient solution to the semiconductor industry’s demands. The table below summarizes the advantages of laser-modified cutting:
Aspect | Traditional Cutting | Laser-Modified Cutting |
---|---|---|
Speed | Moderate | High |
Cost | Higher | Lower |
Material Deformation | Significant | Minimal |
Thermal Damage Risk | High | Low |
In the pursuit of high-volume manufacturing, the integration of different materials onto a CMOS-compatible substrate is also a promising application of laser cutting. Performance data from studies suggest that combining ion-cutting with epitaxial growth is a viable approach for creating C-band light sources and other semiconductor devices.
Innovations in Wafer Stealth Dicing
Reducing Kerf-Loss with Stealth Dicing
Stealth dicing, a laser-based technology, has revolutionized the way semiconductor wafers are sliced, offering a novel alternative to traditional methods. By utilizing thermally induced mechanical forces, this process significantly reduces kerf-loss, which is the material wasted due to cutting. The absence of physical contact in stealth dicing means there is no wear on the cutting tool, leading to a more sustainable and cost-effective production process.
The advantages of stealth dicing are not just theoretical; they translate into tangible yield improvements. For instance, in the production of SiC wafers, the reduction in kerf-loss means that more usable wafers can be produced from a single SiC ingot without the need to expand crystal growth capacities. This efficiency gain is particularly beneficial for the production of sub-100
External forces play a crucial role in guiding the cracks along the laser-conditioned layer, ensuring a precise split of the material. By optimizing laser parameters and beam delivery, manufacturers can control material deformation, thus preserving the integrity of the wafer’s top and bottom interfaces. This level of control is unattainable with traditional cutting methods, which often cause thermal damage and material waste.
Motion Control Systems for Precision Slicing
The advent of advanced motion control systems has revolutionized the precision and efficiency of wafer slicing. High-performance multi-axis motion controllers are at the forefront of this innovation, offering configurations that cater to the specific needs of laser micromachining applications. For instance, the A-824, A-826, and A-828 controllers from PI (Physik Instrumente) LP support both incremental and absolute encoders, enhancing the accuracy of laser triggering and synchronization.
These systems are designed to minimize kerf-loss, a critical factor in semiconductor manufacturing where material conservation translates directly to cost savings. The table below summarizes the key features of the multi-axis motion controllers:
Model | Axes | Encoder Compatibility |
---|---|---|
A-824 | 4 | Incremental & Absolute |
A-826 | 6 | Incremental & Absolute |
A-828 | 8 | Incremental & Absolute |
In addition to the controllers, the integration of stages such as the 3-DOF XY-Theta stage and the A-322 XY Planar Stages ensures that the motion is not only precise but also smooth and frictionless. These stages utilize air bearings and direct drive motors to achieve the highest accuracy and speed, crucial for intricate laser slicing processes. The synergy between advanced motion control algorithms and robust hardware paves the way for unprecedented levels of precision in wafer dicing.
Comparative Analysis with Traditional Cutting Methods
When comparing Stealth Dicing (SD) with traditional wafer cutting methods, the advantages become clear. SD’s ability to eliminate kerf-loss is a game-changer for the industry, leading to a significant yield improvement. This is particularly beneficial for the production of sub-100 \[\mu\]m thin SiC devices, which are becoming increasingly important in advanced applications.
Traditional methods often involve mechanical saws that can cause material loss and damage. In contrast, SD uses ultra-short pulse lasers to create a weakened region within the material, allowing for precise and controlled cleaving. This not only preserves more of the valuable material but also minimizes the risk of thermal damage to the wafer.
Method | Material Loss | Precision | Thermal Damage |
---|---|---|---|
Traditional Cutting | High | Moderate | Possible |
Stealth Dicing | None | High | Minimal |
The table above succinctly illustrates the differences between SD and traditional cutting techniques. By optimizing laser parameters and employing advanced motion systems, manufacturers can further enhance the integrity and quality of the sliced wafers.
Advanced Motion Systems in Wafer Processing
The Impact of 3-DOF and 5-DOF Stages
The introduction of 3-DOF (Degrees of Freedom) and 5-DOF stages has revolutionized the precision and control in wafer processing. These stages enable ultraprecision positioning, which is critical for the intricate tasks involved in semiconductor fabrication. The 3-DOF stages, in particular, offer a combination of linear and rotational axes (X, Y, Theta-Z) that streamline control loops and enhance throughput.
In our lab, the ultraprecision wafer stage developed exhibits exceptional performance. It glides smoothly on a thin film of laminar air, ensuring frictionless and dynamic motion, necessary for tracing intricate trajectories. The stage integrates a flexure coupling between the X and Y axes, allowing for active yaw control, which compensates for any potential yaw, improving overall performance and simplifying operations.
Here is a subset of test data for an XY-Theta air bearing 3DOF stage:
Axis | Dynamic Straightness (μm pp) | Load (kg) | Acceleration (g) |
---|---|---|---|
X | < 0.450 | 20 | 0.75 |
Y | < 0.500 | 20 | 0.75 |
This data, derived from extensive testing, underscores the precision achievable with advanced motion systems. The decoupling effect of magnetic force and torque, evaluated by solving for the current vector at different points along a specific trajectory, further contributes to the stage’s high performance.
Guiding Cracks with External Forces
The precision of wafer slicing has been significantly enhanced by the application of external forces to guide crack propagation. These forces, meticulously controlled during the process, ensure that the material splits along the predefined laser-conditioned layer, maintaining the integrity of the wafer.
External forces such as bonding and pressing are pivotal in achieving the desired precision. For instance, the use of vacuum preload in vertical orientation creates a locking force through friction, which is crucial in maintaining positional stability during critical phases of the slicing process. This technique is particularly effective in preventing unintended X-Y directional movements, which could otherwise compromise the wafer’s quality.
The table below presents key performance metrics for an XY-Theta air bearing 3DOF stage, which exemplifies the level of control achievable with advanced motion systems:
Axis | Dynamic Straightness (μm pp) | Load (kg) | Max Acceleration (g) |
---|---|---|---|
X | < 0.450 | 20 | 0.75 |
Y | < 0.500 | 20 | 0.75 |
These figures highlight the stage’s ability to maintain dynamic straightness under load and acceleration, a testament to the precision offered by modern motion control systems.
Air Bearing Stages for Enhanced Manufacturing
In the realm of semiconductor wafer slicing, air bearing stages have emerged as a pivotal technology for enhancing manufacturing precision and efficiency. These stages utilize a thin film of air to virtually eliminate friction, allowing for smoother and more controlled movements of the wafer during processing.
The implementation of air bearing stages, such as the A-63X series from PI (Physik Instrumente), has led to significant improvements in positioning accuracy. This is largely due to the high-resolution encoders and the direct drive torque motor, which together ensure optimal dynamics and motion performance. The self-locking feature of these stages further contributes to their stability, enabling higher in-position accuracy and repeatability.
Feature | Benefit |
---|---|
Low-profile design | Facilitates integration into existing systems |
High-performance torque motor | Delivers exceptional dynamics and motion control |
High-resolution encoders | Ensures precise positioning |
Self-locking capability | Provides greater in-position stability |
As the demand for smaller semiconductor features increases, the role of air bearing stages in supporting intricate designs and advanced manufacturing processes becomes ever more critical.
Semiconductor Fabrication Technologies
From Silicon Ingot to Integrated Circuits
The journey from a silicon ingot to sophisticated integrated circuits (ICs) is a marvel of modern engineering. It begins with the creation of a pure single-crystal silicon wafer, which serves as the foundation for the intricate electronic circuits that will eventually be formed. The wafer undergoes a series of critical steps, including thermal oxidation and thin-film deposition, each adding layers and patterns that define the circuit’s functionality.
Semiconductor fabrication is a complex and delicate process, demanding the highest standards of cleanliness and precision. Clean rooms are essential to maintain sterile conditions and prevent contamination by air particles, which could otherwise compromise the integrity of the ICs. The table below outlines the key stages in semiconductor fabrication:
Stage | Description |
---|---|
1. Wafer Preparation | Initial creation and preparation of the silicon wafer. |
2. Oxidation & Deposition | Application of various layers and films to build the circuit structure. |
3. Lithography | Patterning of the wafer to define circuit elements. |
4. Etching | Removal of unwanted material to reveal the circuit pattern. |
5. Doping | Introduction of impurities to modify electrical properties. |
6. Metallization | Addition of metal layers to create connections within the IC. |
7. Assembly & Packaging | Final assembly of the IC into a protective casing for use in electronic devices. |
The integration of different materials, such as InP on Si substrates, is achieved through advanced techniques like ion-cutting and surface activated bonding. These processes enable the creation of wafer-scale heterogeneous integration substrates, which are crucial for the development of lasers and other semiconductor devices that require a combination of different material properties.
Key Processes: Etching and Thin-Film Deposition
Etching and thin-film deposition are pivotal steps in semiconductor fabrication, each serving a unique purpose in the intricate dance of circuit creation. Etching is the art of precision, where unwanted material is selectively removed using chemical etchants to shape the various components. This process is not just about subtraction; it’s about ensuring that what remains is perfectly configured for its role in the final product.
In contrast, thin-film deposition is the process of addition, layering materials like silicon dioxide or metals onto the wafer. These layers serve as insulators, conductors, or gate oxides, each contributing to the wafer’s transformation into a functional integrated circuit. The deposition techniques vary, with some of the most common being:
- Chemical Vapor Deposition (CVD)
- Physical Vapor Deposition (PVD)
- Atomic Layer Deposition (ALD)
- Molecular Beam Epitaxy (MBE)
The efficiency of these processes is critical, as the manufacturing of semiconductors is a lengthy endeavor, often involving between 500 and 1,500 steps. With the integration of advanced technologies like electron-beam lithography (EBL) and laser lift-off (LLO), the fabrication and transfer of surface thin films have reached new heights, enabling applications such as flexible devices and nonlinear optics. The challenge lies in maintaining the delicate balance between precision and throughput, ensuring that each step contributes to the wafer’s journey from a simple silicon disc to a complex hub of electronic activity.
Innovative Approaches to Wafer-Scale Material Integration
The quest for efficiency in semiconductor manufacturing has led to the exploration of innovative approaches to wafer-scale material integration. Wafer-scale synthesis of two-dimensional materials is a pivotal advancement, enabling the integration of films over large areas. The two-step conversion method, for instance, has been instrumental in fabricating 4-inch 2D materials films, starting with the deposition of a precursor film on a growth substrate.
Recent studies have highlighted the potential of the ion-cutting plus epitaxy approach. This method promises a cost-competitive solution to integrate dissimilar materials at the wafer-scale by addressing the challenges of lattice and domain mismatches. The resulting high-quality quantum well (QW) active regions and smooth surface morphologies have led to impressive laser performance, with low threshold current densities and high output power.
The table below summarizes key performance metrics achieved using innovative integration techniques:
Technique | Threshold Current Density (kA/cm^2) | Output Power (mW/facet) | Max Operating Temperature (°C) |
---|---|---|---|
Ion-Cutting Plus Epitaxy | 0.65 | 155 | 120 |
These advancements not only enhance the performance of semiconductor devices but also pave the way for new applications in integrated photonics and flexible device platforms.
Improving Efficiency in Photolithography and Ion Implantation
Advancements in Masking and Light Exposure Techniques
The evolution of masking and light exposure techniques in photolithography has been pivotal in defining the intricate patterns necessary for semiconductor devices. The process begins with a photomask, which plays a crucial role in patterning the wafer by selectively blocking light to create the desired circuit designs. This step is essential for delineating the locations of various components such as transistors and capacitors.
Recent advancements have focused on enhancing the precision and resolution of these patterns. Innovations include the development of new photomask materials and the refinement of exposure systems. These improvements have led to a significant reduction in feature sizes, allowing for more complex and powerful semiconductor devices.
The table below summarizes the key advancements in photolithography techniques over recent years:
Year | Advancement | Impact |
---|---|---|
2022 | New photomask materials | Improved pattern fidelity |
2023 | Enhanced exposure systems | Higher resolution |
2024 | Advanced light sources | Reduced feature sizes |
These enhancements not only contribute to the miniaturization of semiconductor components but also improve the overall efficiency and throughput of the photolithography process.
Precision Doping with High-Energy Ion Implantation
The technique of high-energy ion implantation is pivotal in the precision doping of semiconductor materials. By bombarding the wafer with ions, specific electrical properties can be tailored, which is essential for the functionality of transistors and other components. The process involves a meticulous control of ion energy and fluence to achieve the desired doping levels without compromising the material integrity.
For instance, a study illustrates the integration of InP on Si substrates using a sequential co-implantation of He and H ions. The precise control of ion energy and fluence during this process is critical for the successful bonding and subsequent layer formation necessary for epitaxial growth. The table below summarizes the parameters used in one such process:
Ion Type | Energy (keV) | Fluence (cm^-2) |
---|---|---|
He | 115 | 2 x 10^16 |
H | 75 | 5 x 10^16 |
Following ion implantation, techniques such as surface activated bonding (SAB) and damage layer removal are employed to ensure a smooth surface for further manufacturing steps. These subsequent processes are as vital as the implantation itself, ensuring the creation of high-quality, uniform wafers ready for the next stages of semiconductor fabrication.
Challenges and Solutions in Miniaturization
The relentless pursuit of miniaturization in semiconductor device manufacturing presents both significant challenges and innovative solutions. The integration of key building blocks with silicon photonics is a primary challenge, particularly the development of a reliable, efficient, and electrically-pumped Si-based laser. This is crucial for advancing optical communications, which are increasingly vital in high-performance computing systems and data centers.
To address the limitations of conventional electrical interconnections, silicon photonics has emerged as a promising solution. It leverages the mature and cost-effective complementary metal–oxide–semiconductor (CMOS) process. However, the indirect band gap of Si complicates the light emission process, necessitating additional momentum for efficient light generation.
In the realm of testing and quality control, automation and analysis have become essential. Solutions like RMS-W/B BPCS and sDM self Diagnostic Machine represent strides in semiconductor test processes, offering centralized recipe management and embedded self-diagnostic capabilities to maintain global equipment quality standards.
Conclusion
In the pursuit of maximizing efficiency in wafer processing, we have explored a range of innovative techniques and technologies that are revolutionizing the semiconductor industry. From the precision and material savings offered by laser-assisted wafer slicing to the intricate patterns achieved through photolithography, each method contributes to the overarching goal of producing higher yields and better-performing devices. The integration of advanced motion control systems, such as the PI XY-THETA stage, and the adoption of ion-cutting plus epitaxy approaches demonstrate the industry’s commitment to overcoming challenges related to material mismatches and thermal damage. As we continue to push the boundaries of what is possible in semiconductor fabrication, it is clear that the combination of these cutting-edge processes will play a critical role in meeting the growing demand for smaller, more complex, and cost-effective integrated circuits.
Frequently Asked Questions
What role do lasers play in semiconductor manufacturing?
Lasers are crucial in semiconductor manufacturing for applications like cutting and slicing wafers. They enhance throughput, improve defect control, and lead to higher yields.
How does wafer stealth dicing reduce kerf-loss?
Wafer stealth dicing eliminates the kerf-loss associated with traditional wire saws by using a laser to create a weakened region within the material for controlled cleaving, which improves yield without expanding crystal growth capacities.
What are the advantages of laser-modified cutting over traditional methods?
Laser-modified cutting is faster and more cost-efficient, offering precise control over material deformation without thermal damage, which is beneficial for the increasing demands and cost challenges in the semiconductor industry.
What is the significance of etching and thin-film deposition in semiconductor fabrication?
Etching selectively removes unwanted material to shape components, while thin-film deposition adds layers that serve as insulators, conductors, or gate oxides, both being key processes in forming electronic circuits on wafers.
How do advanced motion systems like 3-DOF and 5-DOF stages impact wafer processing?
Advanced motion systems, such as 3-DOF and 5-DOF stages, enhance precision and control in wafer processing, guiding cracks with external forces and supporting intricate semiconductor designs.
What improvements have been made in photolithography and ion implantation for semiconductor fabrication?
Advancements in photolithography include more precise masking and light exposure techniques, while ion implantation has seen improvements in precision doping, both critical for miniaturization and creating doped regions for transistor operation.