Advancements in Semiconductor Manufacturing Machines: Driving Efficiency and Precision
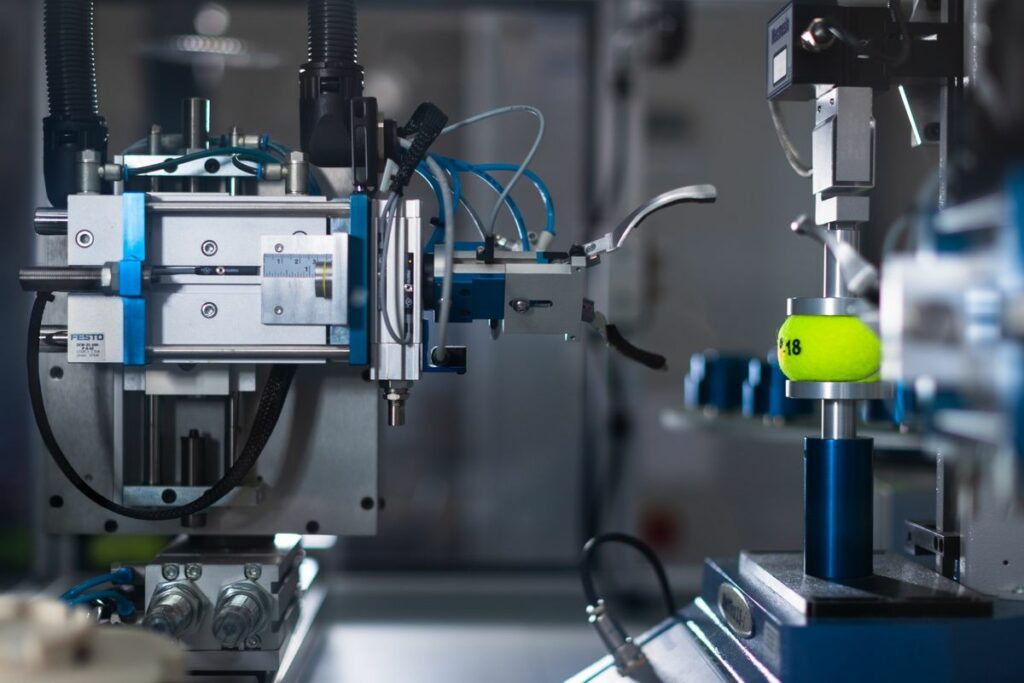
The semiconductor industry is undergoing a transformative phase, marked by rapid advancements in manufacturing machines that are driving unprecedented levels of efficiency and precision. These machines are the backbone of an industry striving to meet the ever-increasing demands for smaller, faster, and more powerful electronic devices. Understanding the innovations in semiconductor equipment, the challenges of miniaturization, the role of government investment, the contributions of subsystem suppliers, and the market dynamics is crucial for stakeholders to navigate this complex landscape.
Key Takeaways
- Digital twins and advanced equipment like the HITACHI M-511AE are accelerating the development of semiconductor manufacturing, enhancing precision and minimizing material wastage.
- The miniaturization trend challenges manufacturers to produce sub-5nm semiconductors, requiring innovative approaches to handle fragile materials and integrate diverse technologies.
- Government funding and policy play a pivotal role in the semiconductor sector, driving R&D and shaping the competitive landscape through investments in fabs and infrastructure.
- Subsystem suppliers are essential innovators in semiconductor manufacturing, providing solutions to address the complexities of highly advanced semiconductor production.
- Semiconductor assembly equipment market dynamics are influenced by trends in AI, HPC, IoT, and government investments, necessitating strategies to compete in a tight market.
Innovations in Semiconductor Equipment for Enhanced Precision
The Role of Digital Twins in Accelerating Development
The advent of digital twins has revolutionized the way semiconductor manufacturers approach the development and optimization of their equipment. By creating dynamic virtual models that mirror physical systems, companies can now simulate and analyze various scenarios without the high costs and risks associated with direct experimentation on the actual systems.
Digital twins offer a multitude of benefits, including predictive maintenance, enhanced yield, and improved scheduling, which are crucial for maintaining a competitive edge in the fast-paced semiconductor industry. They enable manufacturers to test and refine their processes, leading to drastically faster development cycles and reduced material waste.
To maximize the return on investment, it’s essential to prioritize the application of digital twins to the most cost-intensive problems. This strategic approach ensures that the most significant fabrication and testing expenses are addressed first, providing a clear path to cost-effective and efficient operations.
Advancements in Wafer Processing: The HITACHI M-511AE
The HITACHI M-511AE is a cornerstone in the realm of semiconductor manufacturing, celebrated for its precision and steadfast performance. It stands as a pivotal component in the intricate process of wafer fabrication, where its advanced features and capabilities are indispensable. However, the full potential of this sophisticated machinery is realized when it is integrated with standardized communication protocols such as SECS/GEM.
By incorporating tools like the EIGEMBox, the HITACHI M-511AE’s functionality is significantly amplified, leading to enhanced productivity and operational excellence. This synergy between machine and communication technology facilitates real-time monitoring and predictive maintenance, which are critical in reducing downtime and maintaining a steady flow of production.
The benefits of integrating SECS/GEM with the HITACHI M-511AE are manifold. Here are a few key advantages:
- Improved Efficiency: Accelerated data exchange and quicker response times between the HITACHI M-511AE and host systems.
- Enhanced Control: Operators can make precise adjustments to the manufacturing processes, ensuring optimal performance.
- Reduced Downtime: Predictive maintenance capabilities allow for preemptive troubleshooting, keeping production lines moving.
To unlock the potential of the HITACHI M-511AE, it is essential to embrace these advancements and consider the integration of SECS/GEM as a step towards achieving greater yields, quality, and market competitiveness.
The Impact of SECS/GEM on Equipment Efficiency
The adoption of the SECS/GEM protocol has been a game-changer in the realm of semiconductor manufacturing, particularly with equipment like the HITACHI M-511AE. This standardized communication framework ensures that machines can ‘talk’ to each other and to host systems with a high degree of efficiency, which is critical in an industry where precision and speed are paramount.
Key benefits of integrating SECS/GEM with systems such as the HITACHI M-511AE include:
- Improved Efficiency: Faster data exchange and response times between equipment and host systems.
- Enhanced Control: Greater precision in manufacturing process adjustments.
- Reduced Downtime: Real-time monitoring and predictive maintenance capabilities.
- Optimized Production: Higher yields and quality, contributing to market competitiveness.
For those looking to harness these advantages, resources like the EIGEMBox offer a robust solution for implementing SECS/GEM, leading to a significant uplift in productivity and a reduction in operational costs. As the industry continues to evolve, the role of such communication standards in driving equipment efficiency will only become more crucial.
The Miniaturization Challenge: Meeting the Needs of Advanced Semiconductors
Sub-5nm Fabrication: Pushing the Boundaries of Precision
The relentless pursuit of sub-5nm fabrication represents a monumental leap in semiconductor technology. At these scales, traditional lithography techniques are pushed to their limits, necessitating innovative approaches to maintain the intricate patterning processes essential for defining chip features. The industry’s transition to such fine geometries underscores the need for new manufacturing paradigms to achieve acceptable yields and throughput.
Recent discussions in the field highlight the challenges faced by current manufacturing tools. Rickard’s analysis points out that, with existing methods, products aimed at the sub-5nm market are hindered by poor yields and low throughput, making large-scale production unfeasible. This bottleneck is a clear indicator that the assembly processes in place today are ill-equipped to manage the delicate nature of these advanced devices.
As we delve deeper into the realm of ultra-precision, the role of subsystem suppliers becomes increasingly critical. Their efforts in pioneering solutions are essential for overcoming the hurdles of fabricating next-generation chips, especially as we edge closer to the sub-5nm frontier. The collective expertise of these suppliers is instrumental in addressing the complex challenges that arise from such a significant downscaling.
The Fragility of New Semiconductor Materials
The advent of innovative materials in semiconductor manufacturing has introduced a new set of challenges. Newer semiconductor materials, such as silicon carbide, are known for their fragility, which can lead to damage during the final stages of manufacturing. This necessitates a rethinking of assembly tools and processes to accommodate the delicate nature of these materials.
The shift towards applications that power sensor networks and the Internet of Things demands materials that can withstand new environments and usage scales. However, the diminishing effects of transistor scaling are prompting a reevaluation of traditional semiconductor design, with a focus on materials that can support advanced applications like 5G and 6G antennas, sensor networks, and thin-film batteries.
To address these challenges, manufacturers must adapt quickly to new device architectures and materials. The use of digital twins, as highlighted by Joseph Ervin from Lam Research, can accelerate the development process by allowing for virtual experimentation. This approach not only speeds up the innovation cycle but also reduces the cost and waste associated with physical materials.
Integrating Diverse Technologies in Compact Devices
The importance of semiconductor packaging technology cannot be overstated in the current landscape of technological convergence. As devices become increasingly multifaceted, integrating a variety of technologies into compact form factors is essential. This integration is critical in improving device performance, particularly in the era of heterogeneous integration.
Semiconductor packaging has evolved to accommodate the integration of diverse components such as 3D stacking, optics, MEMS, chiplets, and sensors. These advancements are not just about miniaturization but also about enhancing functionality and performance. The table below outlines some of the key technologies and their contributions to semiconductor devices:
Technology | Contribution |
---|---|
3D Stacking | Increases density and interconnect efficiency |
Optics | Enables high-speed data transmission |
MEMS | Provides sensing and actuation capabilities |
Chiplets | Offers modularity and cost-effectiveness |
Sensors | Enhances device intelligence and responsiveness |
The challenge lies in the delicate nature of these components, which are often small, thin, and fragile. New approaches in advanced packaging (AP) are necessary to handle these challenges without compromising yield, throughput, or cost. As the industry embraces open-source standards like the Universal Chiplet Interconnect Express, companies are laying the groundwork for cutting-edge systems that balance cost and performance.
Government Influence and Investment in Semiconductor Manufacturing
Funding Semiconductor Fabs and Infrastructure
The semiconductor industry is a critical driver of technological innovation and economic growth. Government funding plays a pivotal role in catalyzing the expansion of semiconductor manufacturing facilities, which are essential for a wide range of electronic devices and systems. These investments are not only about building physical structures but also about fostering a robust ecosystem that supports research, development, and the growth of ancillary industries.
Recent funding initiatives have demonstrated the significant impact that government investment can have on the semiconductor industry. For instance, the announcement of up to $8.5 billion in funding has been a catalyst for private investment from major companies, leading to the development of new facilities across the United States. This influx of capital is expected to stimulate economic activity and create a ripple effect throughout the supply chain.
The table below outlines some of the key investments in semiconductor infrastructure:
Company | Investment Amount | Location |
---|---|---|
Intel | $100 billion | Arizona, Ohio, New Mexico, Oregon |
BAE Systems | $35 million | Not specified |
Microchip Technology | $162 million | Not specified |
GlobalFoundries | $1.5 billion | Not specified |
These investments are a testament to the strategic importance of semiconductors and the commitment to maintaining technological leadership and supply chain security.
R&D Programs Driving Technological Advancements
Research and Development (R&D) programs are crucial for driving technological advancements in the semiconductor industry. These programs are often the birthplace of the innovations that later become integral to the production of advanced semiconductors. With the advent of initiatives like the CHIPS Act, there is a renewed focus on supporting not just established companies but also startups that bring disruptive changes to the industry.
Investment in R&D is not just about immediate gains; it represents a long-term commitment to the future of technology. The table below highlights some of the key areas where R&D efforts are concentrated:
Focus Area | Description |
---|---|
AI and Machine Learning | Enhancing chip capabilities for AI applications. |
Energy Efficiency | Developing low-power, high-performance chips. |
Advanced Materials | Exploring new materials for better chip performance. |
Quantum Computing | Investing in the future of computing with quantum technologies. |
These investments catalyze breakthroughs across various sectors, including artificial intelligence, telecommunications, and renewable energy, pushing the boundaries of what’s possible in computing and electronics. As the industry evolves, it spurs innovation, leading to smaller, more powerful, and energy-efficient devices.
The Role of Policy in Shaping the Competitive Landscape
Government policies play a pivotal role in the semiconductor industry, influencing market dynamics and competitive strategies. Policy decisions can either foster innovation or create barriers to entry, affecting the market within each region. The competitive landscape is shaped by a variety of factors, including new service/product launches, partnerships, business expansions, and acquisitions.
The regulatory environment is a complex web of trade laws, intellectual property protection, and compliance requirements. These factors can significantly impact the ability of companies to operate effectively on a global scale. For instance, patent disputes can hinder the development and implementation of new semiconductor equipment.
To navigate this intricate landscape, companies must:
- Identify opportunities and challenges in the market.
- Analyze regional penetration and the competitive positioning of players.
- Compare financial performance among major players.
- Evaluate and adapt strategies in response to policy changes.
Recommendations for companies include staying abreast of policy changes and actively participating in shaping the regulatory framework. This proactive approach can lead to a more favorable competitive environment and ensure compliance with complex regulations.
Subsystems Suppliers: The Unsung Heroes of Semiconductor Innovation
Pioneering Solutions for Next-Generation Chip Manufacturing
Subsystems suppliers are the unsung innovators in the semiconductor industry, often overshadowed by the prominent equipment manufacturers. Their role is critical in addressing the complex challenges of fabricating advanced semiconductors, particularly as the industry ventures into the realm of sub-5nm scales. These suppliers are at the forefront of developing solutions that enable the creation of smaller, more powerful chips that are essential for the latest technological trends.
The challenges faced by subsystem suppliers are multifaceted, ranging from the creation of digital twins for complex designs to the handling of delicate materials required for advanced packaging (AP). As Rickard points out, traditional semiconductor assembly processes are hitting their limits, unable to cope with the small, thin, and fragile nature of next-generation devices. This has led to poor yields and unacceptable throughput using current manufacturing techniques.
To meet the demands of major trends such as AI, HPC, 5/6G, IoT, and EV, new approaches are essential. These trends necessitate the integration of diverse technologies like 3D stacking, optics, MEMS, chiplets, and sensors. The table below highlights the key areas where subsystem suppliers are making significant contributions:
Technology Trend | Challenge | Subsystem Supplier Contribution |
---|---|---|
3D Stacking | Precision | Advanced alignment systems |
Optics | Sensitivity | High-resolution imaging |
MEMS | Miniaturization | Precision etching tools |
Chiplets | Integration | Hybrid bonding techniques |
Sensors | Diversity | Multi-material handling |
Collaboration between equipment manufacturers and subsystem suppliers is crucial to overcome these hurdles and ensure the successful production of next-generation semiconductors.
Addressing the Challenges of Highly Advanced Semiconductors
As semiconductor devices shrink to sub-5nm scales, the challenges faced by subsystem suppliers intensify. The precision required for these minuscule components demands innovation at every turn, from material handling to assembly processes. Traditional methods are reaching their limits, with poor yields and unacceptable throughput when dealing with small, thin, and fragile devices.
The major trends driving the semiconductor industry, such as AI, HPC, and IoT, necessitate a reimagining of assembly processes. These advanced applications require support for diverse technologies like 3D stacking and chiplets, which are not adequately served by existing tools. To address these issues, new approaches are being developed:
- Creation of virtual digital models for complex semiconductor designs and process flows.
- Development of tools capable of handling the fragility of advanced semiconductor materials.
- Implementation of innovative techniques to improve yield and throughput.
The shift towards devices that power sensor networks and the Internet of Things demands a reevaluation of traditional semiconductor design. Subsystem suppliers are at the forefront of this transformation, pioneering solutions that will enable the next generation of semiconductor manufacturing.
Collaboration Between Equipment Manufacturers and Subsystem Suppliers
The symbiotic relationship between semiconductor equipment manufacturers and their subsystem suppliers is a cornerstone of the industry’s innovation. Subsystems suppliers, predominantly from Europe, Japan, and the US, are essential in addressing the intricate challenges of fabricating advanced semiconductors. As the industry pushes towards sub-5nm scales, these suppliers provide the pioneering solutions necessary for next-generation chip manufacturing.
The resilience and innovation within the subsystem supplier sector, despite recent challenges such as export restrictions and revenue declines, indicate a promising return to growth. Subsystems, categorized into segments like process monitoring and thermal control, are crucial for the seamless operation of semiconductor machinery. Companies like ASML and Applied Materials are well-known, but their reliance on suppliers such as Advanced Energy and MKS Instruments is significant. These collaborations ensure the industry’s ability to meet the increasing demands for precision and efficiency.
In the context of market dynamics, the role of standards like SEMI is pivotal. SECS/GEM protocols facilitate efficient data exchange, enhancing the capabilities of equipment and leading to improved productivity. The integration of solutions like the EIGEMBox with machines such as the HITACHI M-511AE exemplifies the benefits of these collaborations. The table below provides a snapshot of the diverse subsystem segments and their contributions to semiconductor manufacturing:
Segment | Function | Key Suppliers |
---|---|---|
Process Monitoring | Ensures accuracy | Zeiss, Zygo |
Power | Supplies energy | XP Power, Advanced Energy |
Wafer Handling | Manages wafer movement | VAT, Edwards |
Thermal Control | Regulates temperature | COMET, MKS Instruments |
The insights from the ASSEMBLY EQUIPMENT SUPPLY CHAIN PROCESS highlight the importance of these collaborations in driving the industry forward.
Navigating Market Dynamics in Semiconductor Assembly Equipment
The Surge of Major Trends Influencing Semiconductor Growth
The semiconductor industry is experiencing a surge of major trends that are reshaping the landscape of chip manufacturing and assembly. The integration of AI, HPC, 5/6G, IoT, and EV technologies is driving the need for advanced packaging (AP) solutions that can accommodate 3D stacking, optics, MEMS, chiplets, and sensors. These innovations are essential for creating devices that are not only powerful but also compact and efficient.
Key factors fueling the growth of the semiconductor assembly process equipment market include technological developments, the increasing demand for consumer electronics, and the widespread adoption of IoT and AI. The automotive industry’s expansion also plays a significant role, as does the emergence of new applications such as autonomous vehicles and 5G technology. The following table summarizes the primary drivers of this growth:
Driver | Impact on Semiconductor Assembly |
---|---|
Technological Advancements | Enables complex AP solutions |
Consumer Electronics Demand | Increases production volume |
IoT and AI Adoption | Requires sophisticated chipsets |
Automotive Industry Growth | Spurs innovation in vehicle electronics |
As companies like NVIDIA report staggering sales increases, it’s clear that the industry is not only recovering from previous shortages but is also thriving. The 2024 outlook from Deloitte suggests that these trends will continue to shape the market in the year ahead, indicating a period of robust growth and innovation.
Adapting to the Evolving Needs of AI, HPC, and IoT
The semiconductor industry is at the forefront of enabling the rapid growth of AI, HPC, and IoT technologies. As these fields evolve, they demand more from semiconductor packaging, pushing the boundaries of what’s possible in terms of performance and form factor. Advanced Semiconductor Packaging (AP) is now required to support a myriad of complex features such as 3D stacking, optics, MEMS, and chiplets. These innovations are critical for the development of devices that are not only powerful but also increasingly small, thin, and fragile.
The integration of these technologies presents significant challenges in terms of yield, throughput, and cost. Manufacturers must adopt new approaches to handle the delicate nature of these advanced semiconductors without compromising on efficiency. The industry is witnessing a surge in demand for GPUs and ACUs, particularly for server applications in data centers, as highlighted by the popularity of NVIDIA’s Hopper chips. This trend underscores the need for semiconductor assembly equipment that can adapt to the intricate requirements of cutting-edge AI models and data processing tasks.
To stay competitive and meet these evolving needs, industry players must keep abreast of the latest trends and challenges. A comprehensive understanding of the market, including the advancements made by key players and the forecasted trends, is essential for navigating the dynamic landscape of semiconductor packaging.
Strategies for Competing in a Tight Market
In the fiercely competitive semiconductor assembly equipment market, companies are adopting multifaceted strategies to maintain and enhance their market positions. Key strategies include investment in research and development to innovate and expand product lines, which is crucial for staying ahead in technology and meeting the evolving demands of the industry.
To effectively compete, companies must also analyze the regional penetration of their products and services. Understanding the competitive landscape is essential, with a focus on the market ranking of major players and their recent strategic activities such as mergers, acquisitions, and partnerships. The table below summarizes recent strategic activities by leading market players:
Year | Company | Activity | Outcome |
---|---|---|---|
2024 | Company A | Merger | Expanded market share |
2023 | Company B | New product launch | Technological edge |
2022 | Company C | Acquisition | Increased global footprint |
Finally, companies are advised to heed recommendations from industry analyses and market outlooks, which often highlight the importance of micro architecture planning and system level design. These components are vital for the semiconductor equipment industry to adapt and thrive in a market that is constantly being reshaped by new technological advancements and consumer demands.
Conclusion
The relentless march of progress in semiconductor manufacturing machines underscores a pivotal era for the industry. As we’ve explored, advancements in precision, efficiency, and integration are not just desirable but essential to meet the burgeoning demands of modern electronics. The HITACHI M-511AE exemplifies the pinnacle of current technology, yet its full potential is unlocked only through harmonious synergy with protocols like SECS/GEM and innovations such as EIGEMBox. The challenges of miniaturization, fragile new materials, and complex assembly requirements are being met head-on by equipment manufacturers and their visionary subsystem suppliers. With the stakes raised by fierce competition and the push towards sub-5nm scales, the industry’s future hinges on its ability to innovate and adapt. As we stand on the cusp of breakthroughs that will power the next generation of technology, it is clear that the evolution of semiconductor manufacturing machines is not just a testament to human ingenuity but a foundation for the future of technology itself.
Frequently Asked Questions
How are digital twins being used to improve semiconductor manufacturing?
Digital twins are used to create virtual replicas of semiconductor manufacturing equipment, allowing for rapid experimentation, data-rich analysis, and reduced material waste. This accelerates development and helps manufacturers achieve mature yields more quickly and economically.
What makes the HITACHI M-511AE significant in wafer processing?
The HITACHI M-511AE is known for its precision and reliability, playing a vital role in semiconductor wafer processing. Its advanced features require seamless integration with communication protocols like SECS/GEM to fully realize its potential, leading to improved productivity.
Why is SECS/GEM important for semiconductor equipment efficiency?
SECS/GEM is crucial for efficient data exchange between semiconductor manufacturing equipment and host systems. It standardizes communication, enabling better control and monitoring of equipment, thus enhancing efficiency and productivity.
What challenges arise from the miniaturization of semiconductors?
Miniaturization leads to smaller components and higher density, requiring more sophisticated assembly equipment for precision and accuracy. It also presents challenges with the fragility of new semiconductor materials and the integration of diverse technologies in compact devices.
How are subsystem suppliers contributing to semiconductor innovation?
Subsystems suppliers are developing pioneering solutions for next-generation chip manufacturing, addressing the intricate challenges of creating highly advanced semiconductors, especially as the industry moves towards sub-5nm scales.
What market dynamics are affecting the semiconductor assembly equipment industry?
The industry is influenced by trends such as AI, HPC, IoT, and the need for advanced packaging techniques like 3D stacking. Government investments and competitive pressures also play a significant role in shaping the market.