Navigating the Global Market for Wafer Suppliers in the Semiconductor Industry
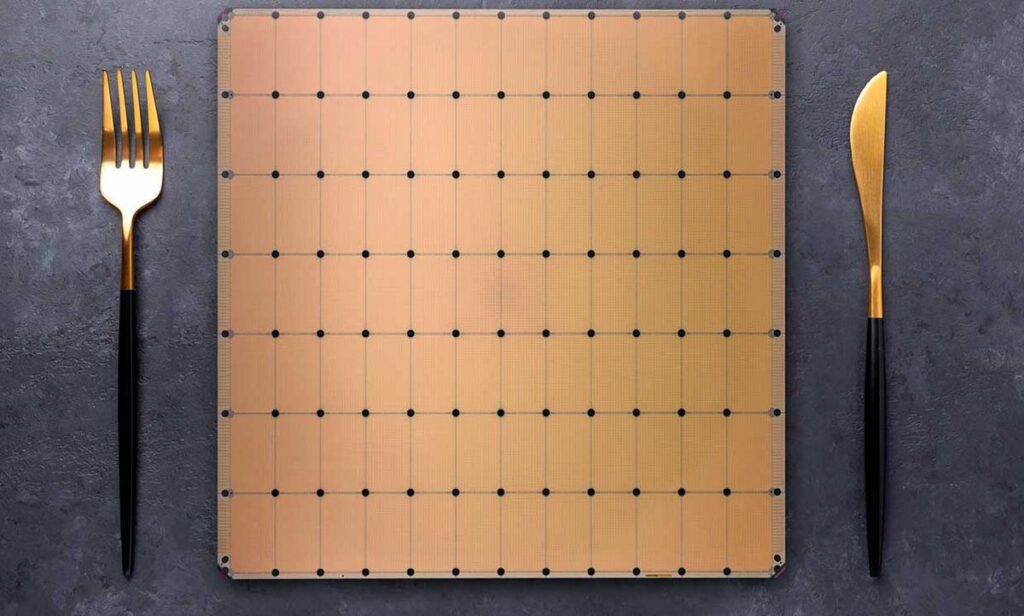
The semiconductor industry is a cornerstone of modern technology, with wafers being a critical component in the production of integrated circuits. As the demand for more advanced and efficient electronic devices grows, so does the need for high-quality wafers. This article delves into the complexities of the global market for wafer suppliers, exploring the dynamics of supply and demand, advancements in wafer-level packaging (WLP), the competitive landscape, and the regional market variations. We’ll also look at the challenges and opportunities presented by advanced semiconductor packaging and how they are shaping the industry.
Key Takeaways
- The global demand for wafers is projected to increase significantly, from 11 million units in 2019 to 33 million by 2030, especially in sub-11 nm markets.
- Advancements in wafer-level packaging (WLP) are revolutionizing the industry, with emerging trends focusing on better integration and efficiency in manufacturing processes.
- The competitive landscape is marked by key players such as Integrated Device Manufacturers (IDMs), Outsourced Semiconductor Assembly and Test (OSAT) companies, and wafer foundries, each playing a vital role.
- Challenges such as rising fabrication costs, which have been increasing over 10% per year since the early 2000s, and complexity barriers are prevalent, yet balanced by opportunities in system-in-package (SiP) and novel material use.
- Regional markets, including North America, Asia Pacific, and Europe, are influenced by factors like artificial intelligence (AI), machine learning (ML), data centers, and the automotive sector, driving growth and innovation in semiconductor packaging.
Understanding the Dynamics of Wafer Supply and Demand
Projected Growth in Wafer Demand
The semiconductor industry is poised for significant growth in wafer demand, with projections indicating a rise from approximately 11 million units in 2019 to an estimated 33 million by 2030. This surge is primarily driven by advancements in technology and an increasing need for more sophisticated components across various sectors. The global silicon wafer market, valued at $15.3 billion in 2022, is expected to reach $25.9 billion by 2032, showcasing a robust compound annual growth rate (CAGR).
As the industry evolves, the demand for smaller node sizes is intensifying, particularly in the sub-11 nm market. This shift towards more advanced nodes is creating a supply imbalance, with most node sizes predicted to face an undersupply situation at current demand levels. The exception lies within the 25-45 nm range, which is currently aligned with market demand.
The cost implications of this growth are also noteworthy. Fabrication costs have been escalating, with the highest-value sectors, including semiconductor fabrication, experiencing steep rates of cost increase—over 10% per year since the early 2000s. As companies transition to larger wafer sizes, such as the popular 300 mm, they encounter a proportional rise in manufacturing costs, approximately 1.4 times with each increase in wafer size.
Supply Chain Considerations for Wafer Sourcing
In the semiconductor industry, establishing a robust silicon wafer supply chain is crucial for maintaining production without disruptions. This involves a multi-faceted approach that includes diversifying sources to mitigate risks associated with supplier dependency. Proactive risk management strategies are essential to anticipate and address potential supply chain bottlenecks.
Key considerations for a resilient wafer supply chain include:
- Assessing supplier reliability and quality assurance practices
- Evaluating geopolitical risks and trade policy impacts
- Implementing inventory management techniques such as safety stock or buffer inventory
- Establishing partnerships with multiple suppliers to ensure a steady supply
By taking these steps, manufacturers can navigate the complexities of wafer sourcing and build a supply chain that can withstand various market fluctuations and challenges.
Impact of Node Size on Supply Adequacy
The semiconductor industry’s pivot towards smaller node sizes has significant implications for wafer supply adequacy. Demand for wafers is expected to triple by 2030, with most investments targeting sub-11 nm technologies. This focus on smaller nodes is creating a supply gap in the larger 90 nm space, which is not keeping pace with the growing demand.
Despite the increasing production of 90 nm chips, the compound annual growth rate (CAGR) is projected to remain around 5% through 2026, insufficient to bridge the supply-demand mismatch. OEMs are hesitant to transition to smaller nodes due to the high costs associated with development, qualification, and the need for additional R&D resources.
The following table summarizes the expected undersupply situations by node size range, based on current demand levels:
Node Size Range (nm) | Supply Status |
---|---|
<25 | Undersupply |
25-45 | Adequate |
>45 | Undersupply |
As node scaling slows and the economic benefits of Moore’s Law diminish, the industry faces increased manufacturing and design costs with each node transition. Hetero-integration (HI) technologies offer a pathway to further industry advancement for specific products and applications, potentially mitigating some of the supply challenges associated with node size reductions.
Advancements in Wafer-Level Packaging (WLP) Technologies
Current WLP Manufacturing Processes
Wafer-level packaging (WLP) is a sophisticated method that encapsulates an integrated circuit at the wafer level, enhancing efficiency and reducing size. The WLP manufacturing process begins with wafer preparation, which involves cleaning and surface conditioning to ensure optimal adhesion for subsequent layers.
The next steps include RDL (Redistribution Layer) buildup, where conductive traces are formed to reroute the electrical connections from the die to the package. This is followed by bumping, a process of adding solder or copper pillars to the wafer’s pads to facilitate electrical connection with the package or the next level of interconnect.
Encapsulation provides protection to the die from environmental factors and mechanical stress. Integration of multiple dies can occur at this stage, depending on the design. Finally, the wafers undergo testing for quality assurance before singulation, where individual chips are cut from the wafer.
The evolution of WLP has led to various types such as eWLB (Embedded Wafer Level BGA) and chip-last FO-WLP (Fan-Out Wafer-Level Packaging), each with its own set of advantages and applications. As the demand for more powerful CPUs grows, these processes are continuously refined to increase production efficiency and meet the market’s needs.
Emerging Trends in Wafer-Level Packaging
The landscape of wafer-level packaging (WLP) is rapidly evolving, with new trends emerging that promise to reshape the industry. Fan-out wafer-level packaging (FOWLP) is gaining traction due to its enhanced performance and ability to accommodate more I/Os than traditional WLCSP (wafer-level chip scale packaging). This trend is indicative of the industry’s shift towards more sophisticated packaging solutions that can meet the demands of high-performance applications.
Another significant trend is the integration of heterogeneous components through System-in-Package (SiP) modules. This approach allows for the combination of different types of components, such as analog, digital, and RF, into a single package, optimizing performance and reducing footprint. The table below highlights some of the key factors driving the adoption of these advanced packaging techniques:
Factor | Impact on WLP Adoption |
---|---|
Increased I/O Density | Facilitates the integration of more functions into a single package |
Performance Optimization | Enables higher performance for demanding applications |
Form Factor Reduction | Allows for smaller and more compact device designs |
System Cost Efficiency | Reduces overall system costs through integration |
As the semiconductor industry continues to innovate, these trends are expected to proliferate, further influencing the design and manufacturing processes of WLP. The implications for supply chains and OEMs are significant, as they must adapt to these advancements to stay competitive in the global market.
Applications of WLP in Various Industries
Wafer-Level Packaging (WLP) has become a cornerstone technology in various sectors due to its compact size and enhanced performance characteristics. Mobile and consumer electronics have been the primary beneficiaries, with WLP enabling the production of thinner, lighter devices without compromising on functionality. The automotive industry is another significant adopter, where WLP’s reliability and robustness support the demanding requirements of automotive electronics.
The versatility of WLP is also evident in its application across different technology nodes, with each node size presenting unique advantages. For instance, the Embedded Wafer Level BGA (eWLB) offers a high level of integration, making it suitable for complex devices. On the other hand, the Chip-last Fan-Out WLP (FO-WLP) is gaining traction for its cost-effectiveness and flexibility in integrating heterogeneous components.
The following table summarizes the applications of WLP in key industries:
Industry | Application | WLP Type |
---|---|---|
Mobile & Consumer Electronics | Smartphones, Wearables | eWLB, FO-WLP |
Automotive | Sensors, Control Units | eWLB, FO-WLP |
Telecommunications | Network Hardware | Cu-Pillar Flip Chip |
Wireless | RF Modules | Wafer-on-Wafer (WoW) |
As the demand for advanced semiconductor devices continues to grow, driven by trends such as AI, ML, and data centers, WLP is poised to play an even more critical role in the industry. The ability to package chips at the wafer level not only reduces costs but also accelerates the time-to-market for new technologies.
Market Players and Competitive Landscape
Key Integrated Device Manufacturers (IDMs)
Integrated Device Manufacturers (IDMs) are pivotal in the semiconductor industry, providing not only the manufacturing of wafers but also the design and development of semiconductor devices. Intel Corporation, Samsung Electronics, and Taiwan Semiconductor Manufacturing Company (TSMC) are among the giants in this space, each playing a significant role in shaping the market dynamics.
The competitive landscape is marked by a mix of established players and emerging challengers. Below is a list of some key IDMs and their areas of expertise:
- Intel Corporation: Microprocessors and chipsets
- Samsung Electronics: Memory chips and system LSI
- TSMC: Foundry services and advanced node production
- SK hynix: Memory semiconductors
- Powertech: Packaging and testing services
These companies are at the forefront of technological advancements, driving innovation in areas such as heterogeneous integration, thermal solutions, and miniaturization. Their contributions are essential across various applications including AI, mobile, automotive, and high-performance computing.
Role of Outsourced Semiconductor Assembly and Test (OSAT) Companies
The semiconductor industry’s reliance on Outsourced Semiconductor Assembly and Test (OSAT) companies is becoming increasingly pronounced as these entities strengthen their collaborations with Integrated Device Manufacturers (IDMs) and foundries. OSATs are pivotal in bridging the gap between semiconductor manufacturing and market-ready products, often handling the final steps of packaging and testing. With the top six OSATs commanding 70 percent of the market share in 2022, their influence is undeniable.
Investments in advanced packaging technologies are a strategic focus for these market leaders. As they allocate significant portions of their capital expenditures (capex) to this area, we are witnessing a shift in their revenue streams, with advanced packaging becoming a more substantial contributor. This trend is indicative of the OSATs’ potential to penetrate the high-end performance packaging segment, which has traditionally been dominated by IDMs and foundries.
OSAT Company | Market Share (%) | Advanced Packaging Investment Focus |
---|---|---|
Company A | 15 | High |
Company B | 12 | Medium |
Company C | 11 | High |
Company D | 10 | Low |
Company E | 9 | Medium |
Company F | 13 | High |
Note: The table represents a simplified view of the market share and investment focus of leading OSAT companies in advanced packaging technologies.
Foundries and Electronics OEMs: A Comparative Analysis
In the semiconductor industry, foundries and electronics original equipment manufacturers (OEMs) play distinct yet interrelated roles. Foundries are specialized in the mass production of chips, offering their manufacturing capabilities to various clients, while electronics OEMs typically integrate these chips into their own branded products. The relationship between the two is symbiotic, as OEMs rely on the technical prowess and capacity of foundries to meet their product demands.
The competitive landscape is shaped by several factors, including production capacity, technological advancements, and market strategies. A comparison of these entities reveals differences in their operational focus and strategic positioning. For instance, foundries prioritize scaling their output and advancing process technologies, whereas OEMs focus on product innovation and market penetration.
Aspect | Foundries | Electronics OEMs |
---|---|---|
Core Focus | Chip manufacturing | Product integration |
Market Strategy | Capacity scaling | Brand development |
Innovation | Process technologies | Product features |
Recent discussions on market structures and business practices, such as those highlighted in the American Economic Liberties Project’s paper, underscore the importance of a robust and competitive semiconductor ecosystem. The CHIPS Implementation is a pivotal move in this direction, aiming to bolster domestic production and mitigate supply chain vulnerabilities.
Challenges and Opportunities in Advanced Semiconductor Packaging
Cost and Complexity Barriers
The semiconductor industry is grappling with escalating costs and increasing complexity, which pose significant barriers to innovation and market entry. Costs have been rising at over 10% per year, with advanced technologies such as gate-all-around, EUV double patterning, and SiGe channels contributing to node-to-node mask and wafer cost increases that can exceed 30 percent. This upward trend in expenses is not only a hurdle for new entrants but also squeezes the margins of established players.
The complexity of semiconductor chips is another daunting challenge. As billions of transistors are integrated into smaller areas, the development of test programs becomes more intricate and time-consuming. Each product’s unique test requirements, dictated by its application, further complicate the process. For instance, consumer electronics and automotive systems have vastly different testing needs, necessitating tailored solutions that add to development time and cost.
To mitigate these issues, some manufacturers are adopting strategies such as bulk buying to guard against price hikes and leveraging automation design software tools. Despite these efforts, the rapid pace of technological advancement continues to present challenges for electronics manufacturers.
Innovations in System-in-Package (SiP) and Heterogeneous Integration
The semiconductor industry is witnessing a transformative phase with the adoption of silicon processing techniques in packaging, emphasizing system integration over traditional single-chip solutions. Heterogeneous integration (HI) is at the forefront of this evolution, integrating separately manufactured components such as chiplets, SiPs, and modules to enhance functionality and operating characteristics. This approach is becoming increasingly mainstream, particularly for high-performance computing (HPC) applications, through advanced packaging platforms.
Key factors driving the adoption of heterogeneous integration include improved performance, thermal management, and the ability to integrate different types of technology into a single package. The table below summarizes some of the primary drivers and trends influencing the adoption of SiP modules:
Driver | Description |
---|---|
Performance Enhancement | Integration of multiple chiplets or dies to achieve higher computational power. |
Thermal Management | Advanced materials and designs that effectively dissipate heat. |
Technology Convergence | Ability to combine various technologies (analog, digital, RF, etc.) in one package. |
Form Factor Reduction | Miniaturization of components leading to smaller, more compact devices. |
As the industry progresses, the future outlook on heterogeneous integration is optimistic, with expectations of lower power consumption, reduced latency, and higher bandwidths. The evolution of advanced semiconductor packaging is not only enhancing the performance of next-generation electronics but also shaping the landscape of SiP applications across various industries.
Future Outlook on Monolithic 3D ICs and Novel Material Use
The semiconductor industry is on the cusp of a transformative era with the advent of monolithic 3D integrated circuits (M3D ICs). These circuits promise to revolutionize chip architecture by stacking layers of transistors within a single chip, offering significant improvements in interconnect density and overall performance. The transition from traditional 2D systems to M3D is motivated by the need for higher efficiency and the limitations of current silicon-based technologies.
Alternative materials such as graphene and transition metal dichalcogenides are being explored for their superior electrical properties. These novel 2D materials could be pivotal in overcoming the challenges faced by silicon, potentially leading to more efficient transistors and a new generation of semiconductor devices.
However, the shift to M3D ICs and the integration of new materials are not without challenges. The complexity of design and manufacturing processes, along with the high costs associated with development, pose significant barriers. The industry is exploring various strategies, including chiplets and heterogeneous design, to balance power, performance, area, and cost considerations, along with reduced time-to-market.
Looking ahead, the global market for advanced semiconductor packaging is expected to grow substantially. The table below provides a snapshot of the projected market from 2020 to 2035, by packaging type, in billions USD:
Year | Packaging Type | Market Value (USD Billions) |
---|---|---|
2020 | Traditional | 50 |
2025 | 2.5D/3D | 75 |
2030 | Fan-out | 100 |
2035 | Monolithic 3D | 150 |
Note: The above figures are illustrative and not actual market data.
Regional Market Analysis and Growth Drivers
Breakdown of Semiconductor Packaging Markets by Region
The semiconductor packaging market is a dynamic and geographically diverse sector, with significant variations in market size and growth drivers across different regions. Asia Pacific currently leads the global market, driven by the presence of major semiconductor manufacturing hubs in countries like China, South Korea, and Taiwan. This region is followed by North America and Europe, which also hold substantial market shares.
The following table provides a snapshot of the semiconductor packaging market size by region, reflecting the distribution of market dominance and potential for growth:
Region | Market Size (USD billion) | Projected Growth (2020-2035) |
---|---|---|
Asia Pacific | 64.22 | High |
North America | – | Moderate |
Europe | – | Moderate |
China | – | High |
Japan | – | Stable |
Rest of World | – | Variable |
It is important to note that the market is not static, and shifts in geopolitical, economic, and technological factors can rapidly alter the landscape. For instance, advancements in AI, ML, and data centers are expected to be significant growth drivers, particularly in regions with strong technology sectors.
Influence of AI, ML, and Data Centers on Market Growth
The semiconductor industry is witnessing a transformative era with the advent of artificial intelligence (AI) and machine learning (ML). The development of AI Centers will likely lead to increased investment in terms of capital and research, fostering a new wave of technological advancements. Collaborations between tech giants and semiconductor firms are becoming more common, as the demand for high-performance computing power surges.
The data center market, traditionally driven by cloud-based applications, is now experiencing significant growth due to AI and ML applications. These technologies require substantial computational resources, leading to a super-exponential growth in data volumes and modeling parameters. The market share of AI-purposed servers is expected to experience a meteoric rise, with projections indicating a jump from a negligible footprint in 2022 to 50% of the overall market revenue by 2027.
This growth is not confined to a single sector; it spans across robotics, automated design, advanced augmented/virtual reality, medicine, chemistry, finance, and many others. The cumulative effect of these applications is pushing the high-performance computing and data center segments into a new techno-economic paradigm, presenting both challenges and opportunities for wafer suppliers and semiconductor manufacturers.
Assessing the Impact of Electric Vehicles and Advanced Driver-Assistance Systems (EV/ADAS)
The semiconductor market is witnessing a significant transformation, driven by the proliferation of electric vehicles (EVs) and advanced driver-assistance systems (ADAS). These technologies are not just reshaping the automotive industry but are also creating a ripple effect across the semiconductor supply chain. The demand for high-performance semiconductors in EVs and ADAS is fueling the need for advanced packaging solutions that can handle the increased power and thermal management requirements.
The integration of EVs as dynamic data hubs, with the advent of 5G and V2X communication standards, is turning vehicles into mobile data centers. This evolution necessitates sophisticated semiconductor packaging to support the high-speed communication and complex data processing involved. Moreover, the rise of fleet telematics is contributing to the growth of the semiconductor market, as highlighted in recent industry reports.
Application Area | Packaging Requirement |
---|---|
ADAS & Autonomous Driving | Radar packaging |
EV Power Electronics | High-voltage environment management |
Infotainment & Telematics | Advanced connectivity solutions |
Sensors & Actuators | Precision and reliability |
The future trends indicate a continued expansion of the semiconductor market, with EV and ADAS applications playing a pivotal role. As the industry moves towards more connected and autonomous vehicles, the demand for semiconductors that can deliver on these complex requirements is expected to surge, presenting both challenges and opportunities for wafer suppliers and packaging specialists.
Conclusion
As we navigate the intricate landscape of the global market for wafer suppliers in the semiconductor industry, it is evident that the sector is poised for significant growth, driven by escalating demand across diverse applications. The surge in fabrication costs, the strategic expansions by companies in burgeoning markets like Malaysia, and the critical undersupply in certain node sizes underscore the complex dynamics at play. With the industry’s pivot towards advanced packaging technologies such as wafer-level packaging, chiplets, and 3D integration, stakeholders must adapt to the evolving value chain, from design to assembly and testing. The market’s trajectory, shaped by regional trends and technological advancements, presents both challenges and opportunities. Companies that can innovate and scale effectively in this competitive environment will likely emerge as leaders in meeting the burgeoning global demand for semiconductor wafers.
Frequently Asked Questions
What are the projected growth rates for wafer demand in the semiconductor industry?
The semiconductor industry anticipates a significant increase in wafer demand, with projections estimating the need for wafers to rise from about 11 million units in 2019 to 33 million by 2030. This growth is driven by advancements in technology and the increasing complexity of semiconductor devices.
How is the wafer supply chain affected by node size variations?
Node size has a substantial impact on wafer supply adequacy. Most wafer investments are targeting sub-11 nm markets, leading to potential undersupply in almost all node sizes except for the 25-45 nm range, which is currently aligned with demand. The smaller the node size, the more complex and costly the fabrication process becomes.
What are some recent advancements in Wafer-Level Packaging (WLP) technologies?
Recent advancements in WLP technologies include improvements in wafer preparation, Redistribution Layer (RDL) buildup, bumping, encapsulation, integration, and testing processes. These advancements contribute to the miniaturization and enhanced performance of semiconductor packages.
Who are the key players in the global market for wafer suppliers?
The key players in the global wafer supplier market include Integrated Device Manufacturers (IDMs), Outsourced Semiconductor Assembly and Test (OSAT) companies, foundries, and Electronics Original Equipment Manufacturers (OEMs). Each plays a distinct role in the supply chain, from design to manufacturing and testing.
What challenges does advanced semiconductor packaging currently face?
Advanced semiconductor packaging faces challenges such as escalating costs, increasing complexity, and the need for reliability in new packaging approaches like System-in-Package (SiP) and heterogeneous integration. The industry is also grappling with the introduction of novel materials and the transition to monolithic 3D ICs.
How is the semiconductor packaging market influenced by regional factors?
The semiconductor packaging market is influenced by regional factors such as the presence of key industry players, local market demands, and government policies. Regions like North America, Asia Pacific, and Europe have their own growth drivers, with AI, ML, data centers, EV/ADAS, and other technologies playing a significant role in market expansion.