Exploring the Intricacies of Wafer Semiconductor Process Technologies
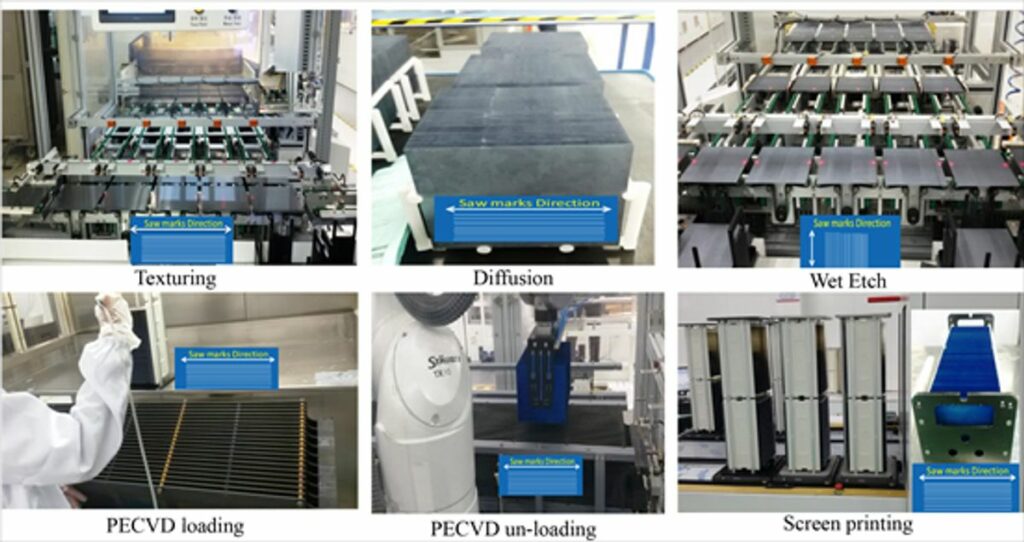
The semiconductor wafer process is a cornerstone of modern technology, enabling the creation of microprocessors and integrated circuits (ICs) that power our electronic devices. This complex and precise process has evolved significantly since the inception of the first semiconductor IC in 1958, with advancements in materials, techniques, and equipment. As we delve into the intricacies of wafer semiconductor process technologies, we uncover the evolution, challenges, and future trends that shape this fascinating field. From the doping of silicon to the latest nanotechnology applications, each step is critical to producing the efficient and powerful computing solutions that drive innovation across industries.
Key Takeaways
- Semiconductor wafer technologies have undergone significant evolution, from the use of silicon ingots to the precision of nanoscale fabrication, impacting the development of microprocessors and ICs.
- Fabrication techniques, such as doping, layering, and wafer dicing, play a crucial role in the performance and reliability of semiconductor devices, with ongoing advancements enhancing complexity and capability.
- Manufacturing microprocessors and ICs presents challenges including high costs, the need for extreme cleanliness and precision, and security vulnerabilities that must be continuously addressed.
- Emerging technologies like nanotechnology and System in Package (SiP) are shaping the future of semiconductor manufacturing, promising greater efficiency, performance, and reduced environmental impact.
- Practical applications of semiconductor process technologies are vast, with innovations leading to more efficient computing solutions and specialized functions in a wide range of electronic devices.
The Evolution of Semiconductor Wafer Technologies
From Silicon Ingots to Nanoscale Precision
The journey of a microprocessor from concept to reality begins with the transformation of sand into highly purified silicon. These silicon ingots are then meticulously sliced into thin wafers, which serve as the substrates for intricate electronic circuits. Silicon’s popularity in semiconductor manufacturing stems from its abundant useful properties, making it the material of choice for most microprocessors and integrated circuits (ICs).
The fabrication of these wafers involves a series of complex processes, each requiring precision and control. Photolithography, a technique used to transfer circuit patterns onto the wafer surface, is followed by doping, where specific areas of the silicon wafer are infused with impurities to alter electrical properties. Etching then removes unwanted material, and layering adds different materials to build the complex structures of a microprocessor.
As technology advances, the scale of these processes has shrunk dramatically, moving from micrometer to nanoscale precision. This evolution has been pivotal in increasing the performance and reducing the power consumption of electronic devices. The table below outlines the progression of feature sizes in semiconductor manufacturing over recent decades:
Year | Feature Size (nm) |
---|---|
1990 | 800 |
2000 | 180 |
2010 | 45 |
2020 | 7 |
2030 | Expected < 1 |
This relentless pursuit of miniaturization encapsulates the essence of semiconductor wafer technology’s evolution, driving the industry towards ever more powerful and energy-efficient components.
Milestones in Microprocessor Development
The journey of microprocessor development is marked by several key milestones that have revolutionized the technology landscape. In 1971, Intel introduced the 4004, the world’s first commercially available microprocessor. This 4-bit CPU was not just a technological breakthrough; it symbolized the dawn of the microprocessor era and the future of digital computing.
Subsequent decades witnessed exponential growth in microprocessor capabilities, closely adhering to Moore’s Law. The 1980s and 1990s, in particular, were a period of rapid advancements, with significant increases in speed and power. This era also saw the diversification of integrated circuits, expanding into microcontrollers, digital signal processors, and application-specific integrated circuits (ASICs).
Landmark products such as the Intel 8086 have had a lasting impact, laying the foundation for the x86 architecture still prevalent today. The emergence of multi-core processors and complex ICs, like the Qualcomm Snapdragon series, has continued to push the boundaries of what is possible, enabling the development of modern electronics, computing, and communication devices.
The Role of Photolithography and Etching
Photolithography and etching are pivotal steps in the fabrication of microprocessors and integrated circuits (ICs). Photolithography uses light to transfer intricate patterns onto a silicon wafer, which is then selectively removed through etching to create the desired circuitry. This process demands extreme precision, as the patterns define the transistors and connections that form the heart of the microprocessor.
The etching process can be wet or dry, with each method having its own advantages and applications. Wet etching uses chemical solutions to remove material, which is ideal for large-area processing. Dry etching, on the other hand, uses gases and is better suited for creating finer details. Both methods are essential in achieving the nanoscale precision required for modern electronics.
- Wet Etching
- Large-area processing
- Uses chemical solutions
- Dry Etching
- Finer details
- Uses gases
Fabrication Techniques and Their Impact
Doping Processes and Material Variability
The semiconductor doping process is a critical step in defining the electrical properties of microprocessors and integrated circuits (ICs). Doping involves the intentional introduction of impurities into the silicon substrate to alter its conductivity. The choice of dopant, its concentration, and the distribution within the silicon lattice are all factors that contribute to the performance and functionality of the final product.
Material variability is another significant aspect of semiconductor manufacturing. Different applications may require alternative materials to silicon, such as gallium arsenide, which offers superior electron mobility for high-speed devices. Below is a list of common materials and their typical applications in IC fabrication:
- Silicon: General-purpose microprocessors and ICs
- Gallium Arsenide: High-speed, high-frequency ICs
- Silicon Carbide: High-power, high-temperature applications
Each material brings its own set of challenges and benefits, influencing the complexity and cost of the manufacturing process. As the industry continues to innovate, the exploration of new materials and doping techniques remains a pivotal area of research and development.
Layering Strategies for Complex Circuits
The fabrication of complex integrated circuits (ICs) is a marvel of modern engineering, requiring precise layering strategies to accommodate the myriad of components necessary for their functionality. Each layer, from the substrate to the final protective coating, plays a critical role in the circuit’s performance and reliability.
To achieve the necessary precision, manufacturers employ a variety of techniques. One such technique is chemical vapor deposition (CVD), which allows for the creation of uniform layers of materials with atomic-level accuracy. Another is molecular beam epitaxy (MBE), which is used for creating high-quality semiconductor layers. These processes are essential for the development of high-speed, low-power consumption electronics that are the backbone of today’s digital world.
The table below outlines some of the common materials used in the layering process and their respective functions within an IC:
Material | Function |
---|---|
Silicon | Substrate |
Silicon Dioxide | Insulator |
Polysilicon | Gate Material |
Copper | Interconnect |
As the semiconductor manufacturing process evolves, so too do the layering strategies. Innovations in materials and techniques continue to push the boundaries of what is possible, enabling the creation of ever more complex and powerful circuits.
Advancements in Wafer Dicing Technologies
The semiconductor industry has witnessed significant advancements in wafer dicing technologies, which are crucial for the final step of IC fabrication. Wafer dicing is the process of cutting a completed wafer into individual die or chips, ready for packaging. With the growing adoption of advanced packaging technologies such as System-on-Chip (SoC), 3D packaging, and wafer-level packaging, the demand for precise and efficient dicing methods has surged.
Modern dicing techniques have evolved to address the challenges of cutting thinner wafers and more complex IC designs. These include stealth dicing, which uses a laser to create a modified layer within the wafer, and plasma dicing, which etches the wafer apart using plasma. Both methods offer cleaner cuts and higher throughput compared to traditional blade dicing.
The table below summarizes the key differences between traditional blade dicing and the newer stealth and plasma dicing technologies:
Dicing Technology | Cut Quality | Throughput | Wafer Thickness Compatibility |
---|---|---|---|
Blade Dicing | Good | Moderate | Thick Wafers |
Stealth Dicing | Excellent | High | Thin to Medium Wafers |
Plasma Dicing | Excellent | High | Very Thin Wafers |
As the industry moves towards more sophisticated ICs, the role of dicing technologies becomes even more pivotal. Manufacturers must continue to innovate to ensure that dicing processes keep pace with the ever-decreasing sizes and increasing complexities of semiconductor devices.
Challenges in Microprocessor and IC Manufacturing
Cost and Complexity Considerations
The semiconductor industry faces a delicate balance between cost efficiency and manufacturing complexity. As microprocessors and integrated circuits (ICs) become more advanced, the intricacies of their design and production escalate. This complexity not only impacts the direct costs of materials and labor but also introduces hidden costs and tradeoffs in ensuring IC quality.
For instance, the pursuit of higher performance and lower power consumption often necessitates the use of more sophisticated and expensive fabrication techniques. The table below outlines some of the key factors that influence the cost and complexity in semiconductor manufacturing:
Factor | Impact on Cost | Impact on Complexity |
---|---|---|
Performance Requirements | High | High |
Power Consumption | Moderate | High |
Size Constraints | Moderate | Moderate |
Design and Manufacturing Process | High | Very High |
Balancing reliability against cost is becoming more difficult for semiconductor test engineers. As devices become more domain-specific and chip complexity increases, the tradeoffs become more pronounced. It is essential to consider all these factors to maintain a competitive edge while ensuring the quality and reliability of the final product.
Cleanliness and Precision in Fabrication
The fabrication of microprocessors is a testament to the marvels of modern engineering, demanding not only complex precision but also an unparalleled level of cleanliness. Each step, from photolithography to etching, must be conducted in a contaminant-free environment to avoid defects that could compromise the performance of the final product.
To maintain this stringent standard, manufacturers employ various cleaning techniques. Among these, Batch Spray Cleaning Systems have garnered attention for their efficiency and are projected to capture a significant market share. This underscores the importance of cleaning equipment in the semiconductor manufacturing process.
The pursuit of perfection in semiconductor fabrication also involves secure manufacturing processes. It is crucial to prevent tampering and ensure the integrity of microprocessors and ICs throughout the supply chain. This aspect of fabrication not only safeguards the functionality of the devices but also protects against potential security vulnerabilities.
Security Vulnerabilities and Mitigation Strategies
The security vulnerabilities inherent in microprocessors and integrated circuits (ICs) pose significant risks to data privacy and system integrity. These vulnerabilities can arise from various sources, including electronic design flaws, manufacturing defects, and the potential for malicious hardware modifications during the production process. One notable example is the discovery of hardware-based vulnerabilities such as Spectre and Meltdown, which exploit critical vulnerabilities in modern microprocessors to allow unauthorized access to sensitive information.
To mitigate these risks, the industry has been taking proactive measures. These include the development of more secure hardware designs that are resistant to tampering and exploitation, and the implementation of robust security protocols at the software level. Manufacturers are also adopting secure manufacturing processes to prevent tampering and ensure the integrity of microprocessors and ICs throughout the supply chain.
In addition to technical measures, there is also a growing emphasis on transparency and responsible disclosure. Companies are increasingly working with security researchers to identify and address vulnerabilities before malicious actors can exploit them. When vulnerabilities are discovered, prompt and transparent communication with users and the implementation of software patches or hardware fixes are crucial for maintaining trust and ensuring the security of devices.
Recommended Reading:
- Integrated Circuit Lifecycles and Impact on Security
Emerging Technologies and Future Trends
Nanotechnology in IC Fabrication
The advent of nanotechnology has been a game-changer in the realm of semiconductor fabrication. By manipulating materials at an atomic or molecular scale, it has enabled the creation of microprocessors and integrated circuits (ICs) that are not only smaller but also more powerful and energy-efficient. This has opened up new avenues for innovation in digital fabrication, including the development of flexible electronics and microcontrollers.
Nanotechnology advancements in IC fabrication have been pivotal in driving the miniaturization revolution. The field of nanotechnology has played a crucial role in this miniaturization revolution, particularly in the Integrated Circuit Chip Handling (ICCH) industry. As a result, we are witnessing a significant shift towards more compact devices that do not compromise on performance or power consumption.
The manufacturing process for microprocessors and ICs is intricate and requires a high degree of precision. It involves a series of complex steps such as photolithography, doping, etching, and layering. These processes are essential for creating the detailed patterns of transistors and connections that define the chip’s capabilities. Despite the complexity and cost associated with these processes, the benefits of nanotechnology in enhancing the efficiency and reliability of these components are undeniable.
System in Package (SiP) Technology
System in Package (SiP) technology represents a significant leap in the miniaturization and integration of electronic circuits. Unlike traditional System on Chip (SoC) designs, SiP allows for the combination of multiple chips into a single package, often including heterogeneous components that would not be feasible to fabricate on a single silicon die. This approach enables greater flexibility in design and functionality, while also reducing the overall footprint of electronic devices.
The benefits of SiP technology are manifold, particularly in the realm of mobile devices. By integrating components such as processors, memory, and connectivity modules into a compact package, manufacturers can produce thinner, lighter, and more power-efficient devices. The table below summarizes the key advantages of SiP over conventional SoC designs:
Feature | SoC | SiP |
---|---|---|
Integration Level | High | Very High |
Component Diversity | Limited | Extensive |
Design Flexibility | Moderate | High |
Power Efficiency | Good | Better |
Physical Footprint | Small | Smaller |
As the demand for more sophisticated and compact electronics continues to grow, SiP technology is poised to play a pivotal role. It not only caters to the current market needs but also paves the way for future innovations in wearable technology, Internet of Things (IoT) devices, and even medical implants, where space is at a premium and functionality cannot be compromised.
Environmental Impact and E-Waste Management
The manufacturing and disposal of microprocessors and integrated circuits (ICs) are fraught with environmental challenges. The production process is not only resource-intensive, requiring significant amounts of water, energy, and raw materials, but also generates hazardous waste that can harm the environment if not managed properly.
Efforts to mitigate these impacts are underway, with the electronics industry striving for more sustainable manufacturing practices. This includes reducing hazardous materials, improving energy efficiency, and enhancing the recyclability of components. Notably, some companies have implemented closed-loop recycling systems, which recover materials from discarded devices to produce new ones.
The disposal of electronic devices contributes to the growing concern of e-waste. Toxic substances such as lead and mercury in microprocessors and ICs pose health risks when they leach into soil and water. The rapid technological advancement and shortened device lifespans exacerbate the volume of e-waste, underscoring the need for effective management strategies. In response, there is an emphasis on designing products for longevity and repairability, supported by regulations in some regions that mandate responsible e-waste disposal and recycling.
Addressing the environmental impact of these technologies is a multifaceted challenge, requiring collaboration among manufacturers, consumers, and policymakers. Through innovation and sustainable practices, the industry can reduce its environmental footprint and contribute to a more sustainable future.
Practical Applications and Innovations
Microprocessors in Computing Devices
At the heart of computing devices, microprocessors are pivotal in executing software instructions and performing essential calculations. These central processing units (CPUs) collaborate with various integrated circuits (ICs), such as memory chips and graphics processors, to provide a full spectrum of computing functions. The synergy between microprocessors and ICs is what enables our personal computers, servers, and mobile devices to operate efficiently and effectively.
The capabilities of microprocessors are a testament to their design, which is focused on processing power and speed. As the primary engines of computing devices, they are responsible for complex calculations and data processing. This is in contrast to other ICs, which may serve more specialized roles within the device. The following table illustrates the differences in roles and performance characteristics between microprocessors and other ICs:
Component | Role in Device | Performance Characteristic |
---|---|---|
Microprocessor | Execute instructions | Optimized for speed |
Memory Chip (RAM) | Store data temporarily | Optimized for access speed |
GPU | Render graphics | Optimized for image processing |
Microprocessors and ICs not only define the performance of computing devices but also their energy efficiency. In an era where mobile device battery life is paramount, advancements in these components have led to architectures that consume less power and generate less heat, thereby enhancing battery life and contributing to the sustainability of technology.
The architecture of a microprocessor itself is a marvel, comprising a control unit, an Arithmetic Logic Unit (ALU), and registers. Each plays a crucial role: the control unit orchestrates processor operations, the ALU performs arithmetic and logic tasks, and registers provide rapid access to data and instructions for the ALU.
Custom ICs and Their Specialized Functions
Custom Integrated Circuits (ICs) are tailored to perform specific functions, optimizing the performance of electronic devices for their intended applications. Unlike general-purpose ICs, these specialized chips are designed with a particular task in mind, such as signal processing or power management. The design and optimization of custom ICs are pivotal in enhancing device efficiency and functionality.
The process of creating custom ICs involves the use of sophisticated software and hardware description languages (HDLs) to draft a detailed blueprint of the circuit’s layout. This blueprint is crucial as it dictates the placement and interconnection of various electronic components on the chip. The performance of these ICs is measured by their ability to execute their designated functions effectively, rather than by general processing speed.
Custom ICs can be categorized into three main types:
- Analog ICs: Handle continuously variable signals, crucial for devices like radios and audio equipment.
- Digital ICs: Work with binary data, powering logic and memory functions in computers and digital devices.
- Mixed-Signal ICs: Integrate both analog and digital functions on a single chip, offering a versatile solution for complex electronic systems.
The Quest for More Efficient Computing Solutions
The relentless pursuit of efficiency in computing solutions has led to significant innovations in microprocessor and integrated circuit (IC) technology. Energy efficiency has become a paramount concern, as it directly influences device longevity, performance, and sustainability. The introduction of quantum computing chips, for instance, represents a quantum leap in processing capabilities, enabling unprecedented speeds for complex calculations in cryptography and other fields.
Advances in microprocessor design have also resulted in architectures that consume less power and generate less heat. This is particularly beneficial for mobile devices, where battery life is a critical factor. The following table summarizes the impact of recent technological advancements on energy efficiency in computing devices:
Technology | Power Consumption Reduction | Heat Generation Reduction |
---|---|---|
Quantum Chips | Significant | Moderate |
Advanced Microprocessors | Moderate | Significant |
These developments not only enhance the user experience by extending battery life but also contribute to the broader goal of environmental sustainability. As the industry continues to innovate, the quest for more efficient computing solutions remains a driving force behind new technologies and design strategies.
Conclusion
As we have journeyed through the complexities of wafer semiconductor process technologies, it is evident that the field is marked by a relentless pursuit of innovation and precision. From the intricate steps of photolithography to the challenges of etching and doping, each phase of the semiconductor fabrication process underscores the remarkable engineering feats achieved since the first integrated circuit in 1958. The evolution of microprocessors and ICs not only reflects the technical advancements but also the industry’s response to the growing demands for more powerful, efficient, and secure computing devices. As we look towards the future, with nanotechnology and other emerging trends poised to redefine the landscape, the semiconductor industry continues to stand at the forefront of technological progress, shaping the capabilities of modern electronics and the potential for future breakthroughs.
Frequently Asked Questions
What are the key steps involved in the semiconductor wafer process?
The semiconductor wafer process involves several key steps, including photolithography, doping, etching, and layering, to create intricate patterns of transistors and connections on a chip. [3]
How do integrated circuits (ICs) differ from microprocessors in terms of manufacturing?
While both ICs and microprocessors share similar manufacturing processes, the complexity and cost can vary. Microprocessors require highly advanced and precise fabrication, whereas simple ICs may be cheaper and less complex to manufacture. [2][4]
What is the significance of nanotechnology in semiconductor fabrication?
Nanotechnology involves manipulating materials on an atomic or molecular scale, which can significantly reduce the size of electronic components while increasing performance and reducing power consumption, leading to more powerful and efficient devices. [7]
What are the challenges in ensuring the security of microprocessors and ICs?
Security challenges in microprocessors and ICs involve protecting against vulnerabilities like Spectre and Meltdown. A multifaceted approach is necessary, combining advanced technology, industry collaboration, and stringent security practices. [7]
How does the environmental impact of e-waste management relate to semiconductor technology?
Semiconductor technology contributes to e-waste, which has environmental impacts. Proper e-waste management involves recycling and reducing waste to minimize ecological damage. [6]
What are the practical applications of microprocessors in computing devices?
Microprocessors are the central processing units in computing devices, handling computations and controlling other components. They are essential for the functionality of smartphones, computers, and many other digital devices. [5]