The Future of Electronics: Innovations in Wafer Production
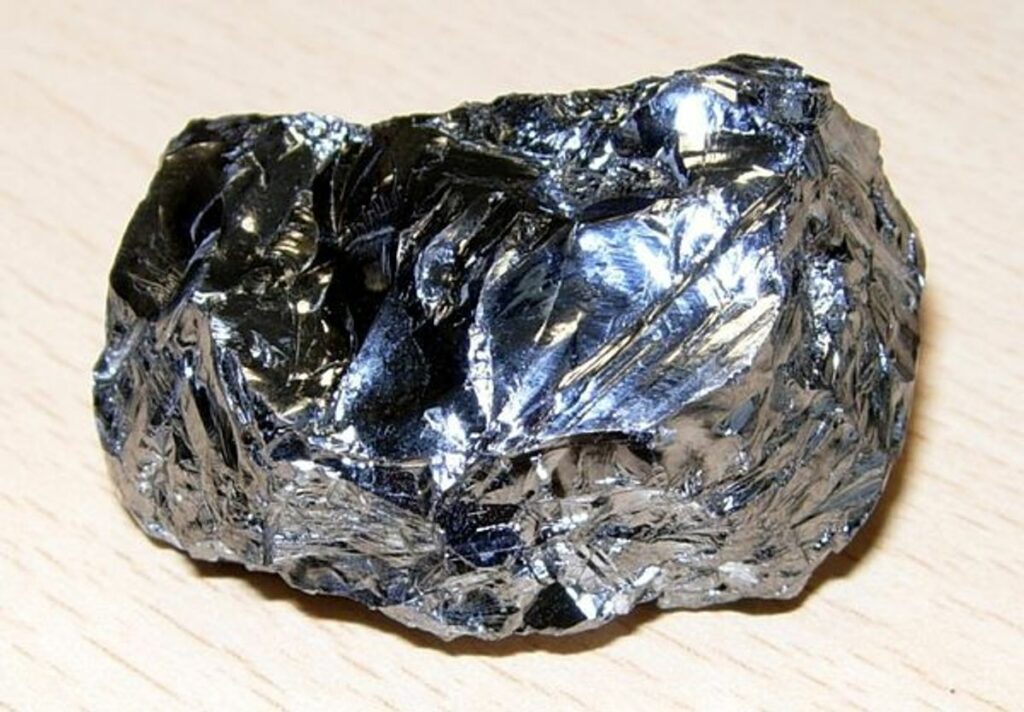
The electronics industry is on the cusp of a transformative era, with innovations in wafer production at the heart of this revolution. Wafers, the foundational substrate for semiconductor devices, are undergoing significant changes in size, efficiency, and type. These advances promise to reshape the landscape of electronics, enabling new applications and enhancing device performance. This article explores the future of electronics through the lens of wafer production, highlighting the latest advancements and their implications for the industry.
Key Takeaways
- The transition from 3-inch to 6-inch wafers marks a significant leap in semiconductor manufacturing, promising a quadrupling of device output per wafer and a substantial reduction in die cost.
- Innovative wafer types, such as polished and epitaxial wafers, are paving the way for highly integrated components and specialized technologies, offering pristine surfaces and superior structural foundations.
- Siltronic’s strategic shift away from small diameter wafer production reflects industry-wide trends towards larger, more efficient wafers that cater to the growing demands of advanced semiconductor applications.
- Microvia technology advancements are driving the miniaturization of electronics, enabling the creation of more compact, powerful devices and setting the stage for future innovations in electronic device capabilities.
- The evolution of wafer production technology, characterized by larger diameters and automation, is a testament to the industry’s relentless pursuit of efficiency and cost-effectiveness, impacting everything from consumer electronics to industrial systems.
Advancements in Wafer Size and Efficiency
Transition from 3-inch to 6-inch Wafers
The semiconductor industry is witnessing a significant shift in wafer production as companies like Coherent move towards larger 6-inch wafers. The transition from 3-inch to 6-inch wafers marks a pivotal change, promising substantial improvements in productivity and cost-efficiency. Dr. Beck Mason of Coherent highlights the advantages, stating that this shift will allow for the manufacturing of four times the number of devices per wafer and a reduction in die cost by over 60%.
The move to larger wafers is not just about scaling up; it’s about meeting the demands of a rapidly evolving market. With the transition, companies expect to fully leverage the benefits of higher yield and improved performance, which are essential for maintaining a competitive edge in communications and sensing markets.
Here’s a quick look at the expected benefits of transitioning to 6-inch wafers:
- Increased number of devices per wafer: Enhanced productivity.
- Significant cost reduction: Over 60% decrease in die cost.
- Higher yield and performance: Critical for competitive advantage.
The industry’s trajectory is clear as it steers away from smaller wafers, with Siltronic’s strategic move away from small diameters underscoring the trend. The focus on larger wafers is a response to the technological advancements and market pressures that demand more efficient and cost-effective production methods.
Implications for Productivity and Cost
The transition to larger wafer diameters has been driven by noteworthy trends in the industry, particularly the shift to smaller nanometer process technologies. This change is not merely a matter of scale; it directly influences the productivity and efficiency of chip manufacturing. Larger wafers allow for more chips to be produced per cycle, reducing the cost per chip and significantly impacting the economics of semiconductor production.
However, this shift also brings about a set of challenges and considerations. The technical precision required for larger wafers necessitates advanced equipment and processes, which can drive up initial costs. Additionally, there are environmental concerns to consider, as the production of larger wafers may have a greater ecological footprint. Despite these challenges, the industry is actively seeking innovative solutions to mitigate these issues and enhance the overall sustainability of wafer production.
The implications for productivity and cost are multifaceted:
- Increased chip yield per wafer enhances overall production efficiency.
- Higher initial investment in equipment and technology may be offset by long-term cost savings.
- Environmental considerations are becoming an integral part of production planning, with a focus on socially responsible solutions.
The Role of Automation in Wafer Fabrication
The integration of automation in wafer fabrication is a pivotal development in semiconductor manufacturing. Automation’s primary role is to reduce human intervention, particularly in the intricate processes of wafer fabrication. This shift not only enhances precision but also significantly boosts throughput and consistency across production batches.
Automation technologies encompass a range of equipment and software that work in unison to perform tasks such as Photolithography, Chemical Vapor Deposition, and Etching. These processes are critical for imprinting complex circuit patterns onto wafers, and automation ensures they are executed with exacting standards. The table below illustrates the impact of automation on key fabrication metrics:
Metric | Before Automation | After Automation |
---|---|---|
Throughput | Low | High |
Precision | Variable | Consistent |
Human Involvement | High | Minimal |
As companies like Siltronic lead the charge in wafer production, the move towards larger wafers and automated processes is a strategic one. It allows for the production of more chips per wafer and a significant reduction in die cost, aligning with the industry’s goal to fabricate smaller and more efficient designs. The transition to automation is not just a trend; it is a necessary evolution to meet the burgeoning demand for semiconductor devices in a multitude of applications.
Innovative Wafer Types and Their Applications
Polished Wafers: Achieving Perfect Surfaces
In the realm of semiconductor manufacturing, the quest for perfection is relentless. Polished wafers stand at the forefront of this pursuit, providing the immaculate surfaces necessary for intricate circuitry. Following the cleaning process, the wafers are subjected to a meticulous polishing routine. This routine employs a specialized polishing slurry designed to eliminate microscopic irregularities, ensuring a mirror-like finish that is essential for high-performance applications.
The significance of polished wafers cannot be overstated. They serve as the foundation for a multitude of semiconductor devices, underpinning the functionality of everything from smartphones to advanced computing systems. The table below outlines the key attributes that polished wafers bring to the electronics industry:
Attribute | Description |
---|---|
Surface Quality | Enables the creation of complex and precise electronic circuits. |
Material Purity | Ensures the reliability and longevity of semiconductor components. |
Versatility | Accommodates a wide range of applications across various industries. |
As the electronics industry continues to evolve, the role of polished wafers remains pivotal. Their production, properties, and application are a testament to the power of silicon wafers, driving innovation and efficiency in wafer production.
Epitaxial Wafers: The Foundation for Integration
Epitaxial wafers serve as a superior basis for highly integrated components in the electronics industry. These wafers are created by adding one or more layers of single-crystal silicon on top of a polished wafer substrate. This process enhances the electrical properties and allows for the development of advanced circuit designs.
The epitaxial layer is fundamental in the manufacturing of semiconductor devices. It provides a pristine, defect-free surface which is crucial for the performance and reliability of integrated circuits. The use of epitaxial wafers is widespread in applications requiring high-speed, high-power, and optoelectronic components.
Here is a brief overview of the epitaxial wafer’s role in semiconductor fabrication:
- Layer Deposition: The epitaxial layer is deposited using techniques such as Chemical Vapor Deposition (CVD).
- Surface Perfection: Ensures a defect-free surface for subsequent semiconductor processing.
- Device Performance: Enhances electrical properties for better device functionality.
The transition to larger wafer sizes, such as the move to 6-inch wafers, has significant implications for epitaxial wafer production. Larger wafers offer the potential for increased productivity and cost savings, as more devices can be produced per wafer. This scalability is essential for meeting the growing demand for semiconductor devices in various markets.
Specialized Wafers: Pioneering New Technologies
Specialized wafers are at the forefront of innovation, enabling the development of new technologies that push the boundaries of what’s possible in electronics. These wafers are tailored to meet the unique needs of advanced applications, often requiring custom designs and material properties.
The versatility of specialized wafers is evident in their wide range of applications. From power electronics that demand robust performance to sensors that require precise and reliable detection capabilities, these wafers are integral to the success of cutting-edge devices.
Here’s a glimpse into the diverse applications of specialized wafers:
- Power electronics for renewable energy systems
- High-frequency devices for telecommunications
- Sensors for medical and environmental monitoring
- Optoelectronic components for lighting and displays
As the demand for sophisticated electronics grows, the role of specialized wafers becomes increasingly critical. Manufacturers like Siltronic are continuously refining their processes to produce wafers that not only meet but exceed the stringent requirements of these emerging technologies.
The Evolution of Wafer Production Technology
Historical Shifts in Wafer Diameter Preferences
The semiconductor industry has witnessed a dramatic shift in wafer diameter preferences over the past quarter-century. The market for wafers up to 150 mm in diameter has shrunk from over fifty percent to less than five percent, reflecting the industry’s rapid technological evolution and the competitive pressures, especially from regions like China.
Siltronic, a key player in the wafer production arena, has mirrored this trend by focusing on larger diameter wafers. The company’s portfolio now predominantly features 300 mm and 200 mm wafers, with smaller diameters being a relic of technology developed mainly in the 1990s. The larger wafers not only represent the forefront of technological advancements but are also expected to see an average volume growth of 6 percent annually.
Here’s a snapshot of the historical wafer diameter preferences:
Year | Up to 150 mm Market Share | Notable Technological Developments |
---|---|---|
25 years ago | >50% | SD wafer technology inception |
Present | <5% | Dominance of 300 mm and 200 mm wafers |
The transition to larger diameters is not just about size; it’s about efficiency and productivity. As Dr. Beck Mason of Telecommunications highlights, moving to 6-inch wafers can quadruple the number of devices per wafer and slash die costs by over 60%, all while transitioning to more efficient automated processes. This strategic shift is crucial for maintaining a competitive edge in the fast-paced markets of communications and sensing.
Technological Breakthroughs in Large Diameter Wafers
The semiconductor industry has witnessed a significant shift towards larger wafer diameters, with 300 mm wafers now representing the forefront of technological advancement and market growth. Siltronic’s production of these wafers has been a response to the increasing demand for higher efficiency and productivity in semiconductor manufacturing.
Historically, wafers up to 150 mm in diameter dominated the market. However, the landscape has changed dramatically, with these smaller wafers now constituting a mere fraction of the market. This evolution is a testament to the industry’s relentless pursuit of cost reduction and performance enhancement.
The transition to larger wafers has been marked by several key benefits:
- Enhanced yield and device performance
- Significant cost savings per device
- Adaptation to automated manufacturing processes
As companies like Siltronic phase out smaller diameters, the focus on large diameter wafers is expected to continue, driven by the promise of improved reliability and the ability to meet the burgeoning demands of advanced electronics.
Siltronic’s Strategic Move Away from Small Diameters
In a decisive shift, Siltronic AG has announced its intention to discontinue the production of small diameter wafers. This move aligns with the industry’s trend towards larger wafer sizes, which offer greater efficiency and potential for technological advancements. The company’s focus will now be on wafers with diameters of 200 mm and above, particularly the 300 mm wafers that are expected to see an average volume growth of 6 percent annually.
The transition away from small diameters, primarily developed in the 1990s, is a response to the declining volumes and negative impact on earnings observed in recent years. Dr. Michael Heckmeier, CEO of Siltronic AG, cited the end of the life cycle for these products as a key reason for the strategic shift. The cessation of small diameter wafer production at the Burghausen site is planned to be completed by 2025, marking the end of an era for Siltronic’s product portfolio.
Wafer Diameter | Status | Expected Completion |
---|---|---|
Up to 150 mm | Ceasing | 2025 |
200 mm | Active | – |
300 mm | Active | – |
Siltronic’s decision is a clear indicator of the changing landscape in wafer production, where larger diameters are not only a preference but a necessity for innovation and growth in the semiconductor industry.
Microvia Technology: Enabling Compact Electronics
Advances in Microvia Fabrication
The relentless pursuit of miniaturization in electronics has led to significant advancements in microvia fabrication. These tiny interconnects are essential for the high-density circuitry found in modern devices. Fabricating microvias involves advanced materials and processes, such as laser drilling, ensuring precise creation. Materials like copper are chosen for their superior electrical and thermal properties, critical for managing current loads and heat dissipation.
Recent innovations have introduced conductive inks and pastes as alternatives to traditional copper plating. This development not only enhances electrical performance but also simplifies the processing of very small microvias. Moreover, the use of high-performance thermoplastics as substrate materials has improved thermal management and reliability in densely packed PCBs.
Addressing the challenges of microvia fabrication, particularly in quality and reliability, is paramount. As vias shrink, issues like incomplete drilling and poor adhesion can compromise PCB integrity. Solutions involve optimizing drilling parameters, employing advanced materials for adhesion, and implementing stringent quality control measures. The future of microvia technology holds the promise of even smaller vias, novel materials, and more efficient manufacturing techniques, potentially integrating with flexible and 3D-printed PCBs.
The Impact on Electronic Device Capabilities
The advent of microvia technology has had a profound impact on the capabilities of electronic devices. Microvias enable the creation of high-density interconnect (HDI) PCBs, which are essential for the miniaturization of electronics. This has allowed for more components to be packed into smaller spaces, enhancing the functionality and efficiency of devices such as smartphones, laptops, and medical equipment.
Microvias have become indispensable in the manufacturing of a wide array of electronic devices, supporting advanced functionalities within extremely compact spaces. For instance, in consumer electronics like smartphones and tablets, microvias are crucial for achieving the high-density circuitry required for their multifunctional capabilities. Similarly, laptops and wearable technology benefit from the integration of more features into slender and lightweight designs.
The significance of microvias extends beyond just compactness; they are pivotal in the ongoing evolution of electronic products. They push the boundaries of PCB design and functionality, facilitating the development of devices that were once thought impossible. As the technology continues to advance, it will be critical in shaping the future landscape of electronics and the capabilities of the devices that have become integral to modern life.
Future Prospects for Microvia Innovations
The future landscape of electronics heavily relies on continuous advancements in microvia technology. As consumer demands for smaller, more integrated devices grow, microvias stand at the forefront of meeting these complex requirements. The potential for innovation in this area is vast, with several key developments on the horizon.
Potential innovations include:
- Development of new materials with superior electrical and thermal properties
- Improved fabrication techniques to reduce costs and increase production speeds
- Advancements in 3D printing and additive manufacturing for direct microvia writing
These advancements promise to revolutionize the design and functionality of electronic devices. As we look ahead, the integration of microvias with flexible and 3D-printed PCBs is particularly exciting, suggesting a future where electronics are not only more powerful but also more adaptable to a variety of applications. The ongoing research and development in microvia technology will be pivotal in shaping the capabilities of devices that are integral to our daily lives.
Conclusion
The evolution of wafer production is a testament to the relentless pursuit of efficiency and innovation in the electronics industry. As we’ve seen, the transition to larger wafer sizes, such as the shift from 3-inch to 6-inch wafers, promises significant advancements in productivity, cost reduction, and performance. Companies like Siltronic are adapting to these changes, phasing out smaller diameter wafers to focus on the more technologically advanced and economically viable larger wafers. The cessation of small diameter wafer production at Siltronic’s Burghausen site by 2025 underscores the industry’s commitment to progress and the need to meet the ever-growing demand for sophisticated electronic components. With potential innovations in microvia capabilities and new fabrication techniques on the horizon, the future of electronics looks bright, promising more powerful, efficient, and compact devices that will continue to revolutionize our world.
Frequently Asked Questions
What are the benefits of transitioning from 3-inch to 6-inch wafers?
Moving to 6-inch wafers allows for the manufacturing of 4 times the number of devices per wafer, a greater than 60% reduction in die cost, and the transition to higher-capacity, more efficient automated process tools. This results in massive productivity improvements and the ability to meet growing demand for indium phosphide products.
How do polished wafers contribute to the semiconductor industry?
Polished wafers provide perfect surfaces that are essential for versatile applications in the semiconductor industry. They are used to create high-quality, reliable electronic components.
What are epitaxial wafers and why are they important?
Epitaxial wafers are used as a superior basis for highly integrated components. They allow for the development of advanced devices with more complex and intricate circuitry.
How has the wafer diameter preference changed historically?
Just 25 years ago, wafers with a diameter of up to 150 mm made up over half of the market. Today, they account for less than five percent. This shift is due to technological advancements and the need for larger wafers that can produce more chips.
What is the significance of microvia technology in electronics?
Microvia technology is crucial for creating more powerful, efficient, and compact electronic devices. It allows for the fabrication of smaller and tighter designs, which is essential for the miniaturization of electronics.
What is Siltronic’s strategic move regarding wafer production?
Siltronic AG plans to gradually cease production of polished and epitaxial small diameter wafers, focusing on larger diameter wafers which show higher growth potential and have been the subject of significant technological breakthroughs.