Precision Meets Innovation: Wafer Electrical Test Methods and Their Impact on Semiconductor Excellence
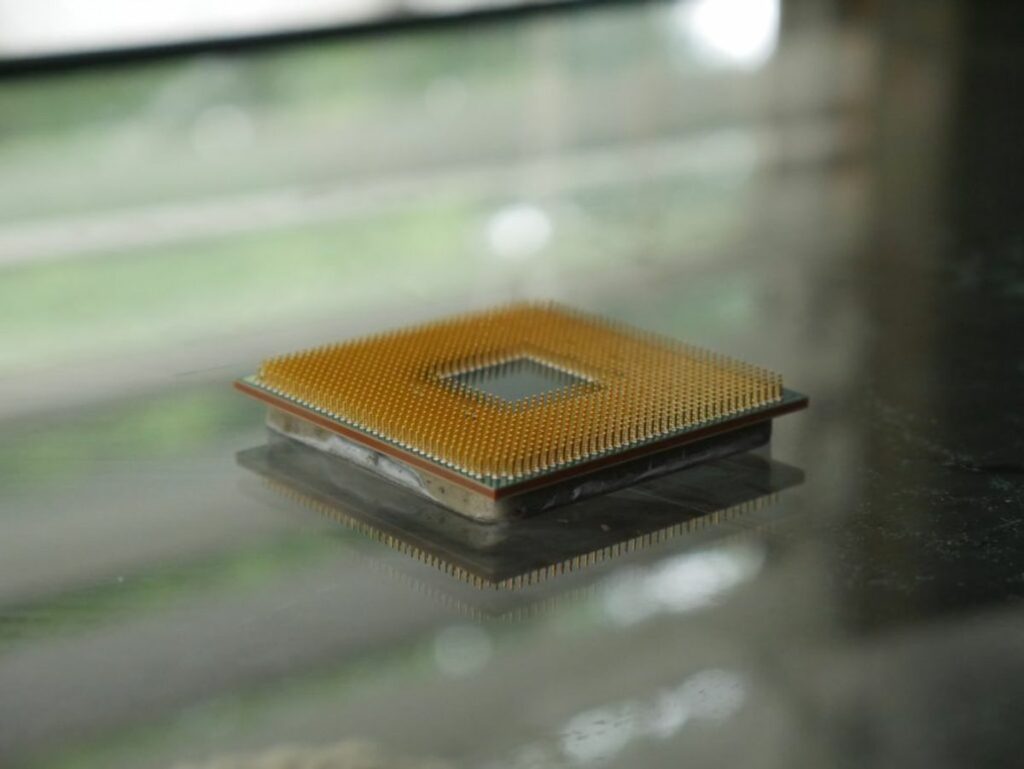
In the realm of semiconductor manufacturing, wafer electrical test methods serve as a critical juncture between design and mass production, ensuring that each chip meets the highest standards of performance and reliability. As the industry pushes the boundaries of miniaturization and complexity, these testing protocols have evolved from microfabrication techniques to advanced nanomanufacturing processes, integrating innovations such as MEMS and photolithography. This article delves into the evolution of these methods, their role in backend manufacturing, the integration of chiplets, and the strategic management of semiconductor resources.
Key Takeaways
- The evolution of wafer electrical test methods has transitioned from traditional microfabrication to sophisticated nanomanufacturing, enabling higher precision and integration at smaller scales.
- Backend semiconductor manufacturing faces challenges such as material transformations, adherence to SEMI standards, and the need for high product variety and velocity, which drive innovation in automation and process management.
- Chiplet integration testing is crucial for assessing risks in design, assembly, and testing, with current safeguards addressing industry challenges and emphasizing the importance of unit product traceability.
- Strategic coordination within the semiconductor sector is facilitated by access to resources such as silicon prototyping, advanced packaging services, EDA tools, and design IP.
- Recent conferences and industry discussions, like those organized by SEMI, USA, highlight the ongoing efforts to standardize and improve backend manufacturing processes in the global semiconductor industry.
The Evolution of Wafer Electrical Test Methods
From Microfabrication to Nanomanufacturing
The transition from microfabrication to nanomanufacturing marks a significant evolution in the realm of semiconductor device fabrication. This shift is characterized by the move towards creating devices with features on the nanometer scale, which has been made possible through the refinement of techniques such as photolithography and etching. These processes have been adapted from the micro-scale to enable the precise manipulation of materials at the nano-scale, leading to the production of semiconductor devices with enhanced performance and reduced size.
In the context of nanomanufacturing, various innovative methods have been developed to further push the boundaries of miniaturization and precision. For instance, the use of tri-layer resist templates has emerged as a simple yet universal pathway to produce multilayer synthetic nanoparticles. Similarly, the introduction of silicon nano-well arrays has facilitated uniform nanoscale pattern transfer, maintaining the integrity of lithographic resolution. Moreover, advancements in nanoimprint lithography, such as the implementation of gradual pressure release, have contributed to the reliability of the patterning process.
The following list highlights key developments in the transition to nanomanufacturing:
- Refinement of photolithography for nanoscale feature creation
- Adaptation of etching techniques for precise material manipulation
- Utilization of tri-layer resist templates for nanoparticle fabrication
- Development of silicon nano-well arrays for accurate pattern transfer
- Improvement of nanoimprint lithography for enhanced reliability
Advancements in Photolithography and Etching
The semiconductor industry has witnessed a significant transformation with the advent of advanced photolithography and etching techniques. These processes are vital for defining intricate circuit patterns on semiconductor wafers, and their evolution has been pivotal in enabling the miniaturization of electronic components.
One of the most notable advancements is the shift towards computational lithography, a method that leverages the power of accelerated computing and generative AI. This approach, spearheaded by collaborations between industry giants like Nvidia, TSMC, and Synopsys, has been instrumental in pushing the limits of physics for next-generation chips. Computational lithography not only enhances the precision of pattern creation but also accelerates the manufacturing process, making it a cornerstone of chip fabrication.
The table below summarizes the impact of computational lithography compared to traditional CPU-based methods:
Aspect | CPU-based Lithography | Computational Lithography |
---|---|---|
Precision | High | Very High |
Manufacturing Speed | Moderate | Fast |
Scalability | Limited | Extensive |
Cost Efficiency | Lower | Higher |
As we look forward, the semiconductor industry continues to explore novel materials and 3D integration techniques, promising to further revolutionize wafer electronics. These advancements are not just about scaling down; they’re about stepping into a future where the fabrication of chips and wafers becomes even more sophisticated and integral to technological progress.
The Role of MEMS in Precision Testing
Micro-Electro-Mechanical Systems (MEMS) have revolutionized precision testing in semiconductor manufacturing. MEMS technologies enable the creation of ultrathin sensing nodes with micrometer-level precision, which are essential for the miniaturization of electronic components. These sensors can be mounted on various surfaces, significantly expanding their application range.
The integration of MEMS with flexible polymer substrates has streamlined the sensor fabrication process, making it both time-efficient and cost-effective. This has opened up new possibilities for smart vehicle applications, particularly in the realm of unmanned aerial vehicles. The table below highlights the key attributes of MEMS sensors that contribute to their effectiveness in precision testing:
Attribute | Description |
---|---|
Size | Ultrathin nodes with less than 100 µm thickness |
Sensitivity | High sensitivity (~14 mV/V/bar) |
Linearity | Good linearity for accurate measurements |
Cost-Effectiveness | Integrated with flexible polymer substrates for economical production |
Furthermore, MEMS sensors have demonstrated their versatility in various fields, including nanomedicine, where they are used for early disease detection and other therapeutic applications. The coupling of MEMS sensors with advanced materials like piezoelectric-piezoresistive and magnetoresistive elements has led to the development of devices capable of measuring electric fields with broad bandwidth and large dynamic range. This adaptability and precision are crucial for maintaining the high standards of semiconductor excellence.
Challenges and Innovations in Backend Semiconductor Manufacturing
Material Transformations and Flow Shop Operations
The backend phase of semiconductor manufacturing presents unique challenges, distinct from those encountered during wafer fabrication. Material transformations and flow shop operations are central to this phase, requiring meticulous coordination and precision. The process involves multiple stages of transformation, where raw materials are systematically converted into finished semiconductor products.
Automation hurdles are significant due to the high product variety and velocity, which demand flexible yet precise handling systems. Alan Weber from Cimetrix highlights the complexity of these operations, including the need for significant manual intervention and the management of a wide range of equipment costs within a typically low automation budget. Moreover, the industry’s gradual shift towards digital transformation promises to revolutionize these processes, leveraging advanced technologies to reduce turnaround time by orders of magnitude.
Adherence to SEMI standards is crucial for ensuring consistency and quality across the board. However, suppliers’ unfamiliarity with these standards can pose a barrier to seamless operations. Additionally, the backend phase must contend with handling multiple data source types and protocols, further complicating the integration of automation systems.
Automation Hurdles and SEMI Standards
The backend of semiconductor manufacturing presents a unique set of automation challenges that differ significantly from wafer fabrication. Complex unit product traceability and the need for significant manual intervention are just the tip of the iceberg. Backend processes involve multiple material transformations and flow shop operations, which are further complicated by the high product variety and velocity.
Adherence to SEMI standards is crucial for ensuring consistency and quality across the industry. However, suppliers’ unfamiliarity with these standards can lead to inefficiencies and increased costs. The recent SEMI conference highlighted the importance of standardization, with experts like Alan Weber and Brian Rubow leading discussions on overcoming these hurdles.
The table below summarizes the key automation challenges identified by industry leaders:
Challenge | Description |
---|---|
Material Transformations | Multiple stages of material changes |
Flow Shop Operations | Sequential process steps |
Product Variety & Velocity | High diversity and production speed |
Manual Intervention | Need for skilled labor |
SEMI Standards | Ensuring industry-wide compliance |
As the industry moves forward, addressing these challenges will be essential for maintaining the pace of innovation and meeting the growing demand for semiconductors.
Strategies for High Product Variety and Velocity
In the semiconductor industry, the ability to manage a high product variety and maintain production velocity is crucial. Diversification in the product portfolio is a strategic approach to mitigate risks and seize new opportunities. Innovation is equally important, as it provides a competitive edge through the adoption of new technologies and investment in research and development.
Collaboration is another key strategy, where forming strategic alliances or partnerships can significantly enhance capabilities and resource access. Alan Weber of Cimetrix highlights the contrast in backend automation challenges compared to wafer fabrication, such as the need for handling a wide range of equipment costs and the complexity of unit product traceability.
To address these challenges, the industry must scale out, increasing the areal density of chips on a package to accommodate more heterogeneous dies. This requires addressing power delivery, thermal dissipation, and external connection challenges, as well as developing standards and protocols for a diverse set of chips. Sustainable manufacturing practices and the translation of domestic materials and substrate innovation into US manufacturing are also vital steps for the industry’s advancement.
Enhancing Chiplet Integration Through Testing
Assessing Risks in Design, Assembly, and Testing
In the intricate process of semiconductor manufacturing, the integration of chiplets presents a complex array of risks at various stages, particularly in design, assembly, and testing. Ensuring the integrity of these components is paramount, as any compromise can lead to significant setbacks in both performance and security. Industry experts like Bob Smith from ESD Alliance emphasize the importance of current safeguards and the need to address ongoing challenges collaboratively between industry and academia.
John Hallman of Siemens EDA highlights the critical aspects of trust and verification within the chip. The transition from System on Chip (SoC) to chiplet security necessitates a robust approach to prevent the insertion of malicious circuitry during the early design phase. This approach must be complemented by stringent measures for integration, verification, and the protection of intellectual property (IP) against reverse engineering.
Steve Carlson from Cadence Design Systems points out the necessity of maintaining confidentiality and safeguarding against unauthorized access. The collaboration across hardware and software teams is essential to fortify the security measures and ensure the traceability of the supply chain. The collective effort is a testament to the industry’s commitment to upholding the highest standards of semiconductor excellence.
Current Safeguards and Open Industry Challenges
In the realm of semiconductor manufacturing, wafer testing is a key step in ensuring the quality and precision required for today’s advanced technology. This process is critical for verifying the high standards expected in the industry. Current safeguards involve a multi-layered approach to security, addressing supply chain risks, side channel attacks, and the threat of reverse engineering. Chiplets, for instance, are designed with onboard protections against such vulnerabilities.
Despite these measures, the industry faces ongoing challenges. The integration of chiplets from multiple foundries necessitates a robust framework for provenance, traceability, and security. As technologies advance towards sub-3nm designs, the complexity of these challenges increases, often requiring government intervention and funding to support further innovation. The need for a comprehensive security architecture across heterogeneous integration (HI) is paramount, ensuring that all layers of the chiplet structure are safeguarded.
The table below outlines some of the key areas of focus for current safeguards and the challenges that remain open within the industry:
Area of Focus | Current Safeguards | Open Challenges |
---|---|---|
Supply Chain | Onboard protections | Ensuring traceability |
Side Channel Attacks | Security architecture | Advanced threat modeling |
Reverse Engineering | Protection layers | Intellectual property risks |
Integration | Government support | Sub-3nm technology development |
The Importance of Unit Product Traceability
In the semiconductor industry, unit product traceability is crucial for maintaining high standards of quality and security. It involves probing individual semiconductor devices on a wafer to identify defects and confirm functionality before further manufacturing. This process not only ensures that each chip meets the required specifications but also provides a means to track and address potential issues throughout the product’s lifecycle.
John Hallman emphasizes the need for additional security verification at the integration level, highlighting that traceability serves as evidence to support security claims. As we scale up the complexity of semiconductor devices, the ability to verify these claims becomes increasingly important. Integrators face the challenge of building up security claims, which requires an objective assessment and, ideally, government support.
To effectively manage unit product traceability, several best practices can be adopted:
- Conduct regular risk assessments
- Establish robust tracking systems
- Foster strong relationships with logistics providers
These practices help ensure the integrity of the supply chain and support the overall security and quality of semiconductor products.
Strategic Coordination and Access to Semiconductor Resources
Silicon Prototyping and Low Volume Piloting
Silicon prototyping and low volume piloting are critical early stages in the semiconductor manufacturing process. They allow for the validation of design concepts and the refinement of manufacturing techniques before full-scale production commences. Prototyping serves as a litmus test for design viability, offering insights into potential performance issues and fabrication challenges.
The process typically involves the creation of small batches of wafers, enabling engineers to conduct thorough testing and make necessary adjustments. This iterative approach is essential for ensuring the quality and reliability of semiconductor devices. The table below outlines the key aspects of silicon prototyping and their respective objectives:
Aspect | Objective |
---|---|
Design Validation | Confirming the functionality of the semiconductor design |
Process Refinement | Optimizing manufacturing processes for efficiency and yield |
Performance Testing | Assessing the device’s operational capabilities |
Reliability Assurance | Ensuring long-term device stability and durability |
As the semiconductor sector strives for innovation, the role of prototyping and piloting becomes even more significant. It not only accelerates the development cycle but also contributes to supply chain resilience by identifying potential issues early on.
Advanced Packaging and Foundry Services
The semiconductor industry is witnessing a significant shift with the introduction of advanced packaging technologies. These innovations are crucial for the miniaturization of devices and the enhancement of performance through better electrical interconnects. The National Advanced Packaging Piloting Facility (NAPPF) plays a pivotal role in this transformation, supporting high-volume manufacturing and the critical stages of piloting and prototyping.
A comprehensive chiplet and design ecosystem is essential for the successful implementation of advanced packaging. This includes the development of methodologies for chiplet discovery, dis-aggregation, and re-aggregation, as well as the establishment of protocols and standards. Furthermore, the design for test, repair, and reliability, alongside holistic design tools and methodologies, are integral to the advanced packaging process.
To ensure the sustainability of these advancements, there is a concerted effort to establish a robust domestic capacity for R&D, prototyping, commercialization, and manufacturing of advanced packaging materials and substrates. Additionally, fostering a skilled and diverse workforce is paramount for maintaining a sustainable domestic substrate manufacturing sector.
Leveraging EDA Tools and Design IP
The integration of Electronic Design Automation (EDA) tools and Design Intellectual Property (IP) is a cornerstone in modern semiconductor manufacturing. The adoption of EDA tools is accelerating, as evidenced by their inclusion in fab purchase specifications and discussions at smart manufacturing conferences. EDA, also known as Interface A, comprises a suite of SEMI standards that facilitate high-speed data exchange between equipment and data consumers via web services.
EDA tools offer several advantages:
- They provide dedicated channels for data transmission, ensuring that control messages do not interfere with data flow.
- The tools support strategic coordination within the semiconductor sector, enhancing both silicon prototyping and advanced packaging processes.
- Access to design IP through EDA tools streamlines the integration of complex systems, allowing for more efficient low volume piloting and prototyping.
As the industry moves towards more sophisticated manufacturing techniques, the role of EDA tools and access to design IP becomes increasingly critical. These resources not only improve the efficiency of semiconductor production but also enable the rapid iteration and innovation necessary to meet the demands of a highly competitive market.
Conclusion
As we have explored throughout this article, the precision and innovation in wafer electrical test methods are pivotal for the advancement of semiconductor excellence. From the meticulous fabrication of probes using micro- and nanomanufacturing techniques to the integration of MEMS for enhanced performance, the semiconductor industry continues to push the boundaries of what is possible. The discussions at the SEMI conference and insights from industry experts like Alan Weber highlight the ongoing challenges in backend automation and the critical need for standardization. Moreover, the potential threats identified at various stages of chiplet production underscore the importance of robust safeguards and collaboration between industry and academia. As we look to the future, the strategic coordination provided by institutional frameworks, access to advanced EDA tools, and the adoption of SEMI standards will be instrumental in taming the ‘Wild West’ of semiconductor backend manufacturing, ensuring that the global semiconductor market remains at the forefront of technological innovation.
Frequently Asked Questions
What recent advancements have been made in wafer electrical test methods?
Recent advancements include the use of micro- and nanomanufacturing techniques for probe fabrication, improvements in photolithography and etching processes, and the incorporation of MEMS for higher precision testing.
How is the backend semiconductor manufacturing process being standardized?
SEMI, USA has organized conferences to address standardization in the backend semiconductor manufacturing process, focusing on automation challenges, material transformations, and SEMI standards.
What are the challenges in chiplet integration during the testing phase?
Challenges in chiplet integration include assessing risks in design, assembly, and testing stages, as well as ensuring current safeguards are effective and addressing open industry challenges.
What resources are available for silicon prototyping and low volume piloting?
Resources for silicon prototyping and low volume piloting include access to advanced packaging services, compound semiconductor open-access foundries, EDA tools, and design IP.
How does the semiconductor industry handle unit product traceability?
The industry faces challenges in maintaining complex unit product traceability due to high product variety, velocity, and significant manual intervention. Strategic coordination and leveraging institutional frameworks are key to managing traceability.
What role does EDA play in the semiconductor manufacturing process?
Electronic Design Automation (EDA) tools are critical in the semiconductor manufacturing process as they facilitate the design and development of semiconductor devices, ensuring precision and innovation in the final products.