Revolutionizing Reliability: The Advancements in Wafer Level Burn-In Techniques
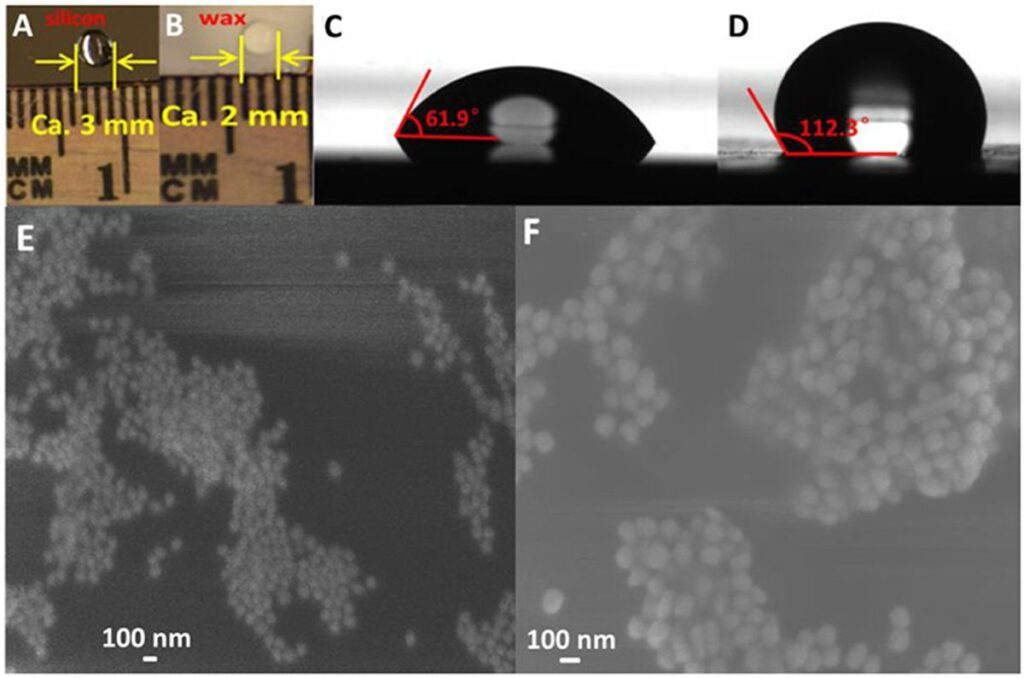
The semiconductor industry is on the brink of a transformative era with the introduction of advanced wafer level burn-in techniques. These new methodologies not only promise to enhance the reliability of semiconductor devices but also integrate seamlessly with modern manufacturing processes. This article delves into the evolution of burn-in procedures, the state-of-the-art equipment and methodologies being employed, their synergy with advanced manufacturing, the role of data analytics and IoT, and the future implications for the industry.
Key Takeaways
- Recent expansions and technological advancements by companies like Benchmark Electronics and GPC Electronics signify a significant leap in semiconductor equipment capabilities, particularly in high-tech machinery and SMT manufacturing lines.
- Innovations such as Archer’s validation of gFET chip design and the development of IC substrates for high-end applications are pushing the boundaries of semiconductor performance and reliability.
- Integration of burn-in procedures with advanced manufacturing processes, exemplified by Additive Assurance’s AMiRIS-LF system and LBT Innovations’ APAS PharmaQC, is revolutionizing quality control and assurance in the industry.
- The convergence of IoT and data analytics with traditional burn-in methods is enabling real-time monitoring and process optimization, leading to more efficient and reliable semiconductor manufacturing.
- Looking ahead, the semiconductor industry is poised to further embrace predictive maintenance, machine learning, and green energy considerations, setting the stage for a more sustainable and technologically advanced future.
Exploring the Evolution of Wafer Level Burn-In
Historical Overview of Burn-In Techniques
Following the historical overview of burn-in techniques, it’s essential to recognize the pivotal role these methods have played in semiconductor manufacturing. Burn-in testing, a process designed to detect early failures and ensure long-term reliability, has evolved significantly over the years. Initially, burn-in procedures were applied to individual components, a time-consuming and costly process. With the advent of wafer level burn-in, the industry witnessed a paradigm shift, allowing for simultaneous testing of numerous devices on a single wafer.
The progression from discrete component testing to wafer level approaches marked a substantial efficiency improvement. This transition was facilitated by technological innovations such as immersion lithography, which played a crucial role in the miniaturization of semiconductor devices. The table below outlines the key milestones in the evolution of burn-in techniques:
Year | Milestone |
---|---|
1980s | Introduction of immersion lithography |
1990s | Shift to wafer level burn-in |
2000s | Advancements in automation and monitoring |
As we delve deeper into recent technological advancements, it’s clear that the industry’s relentless pursuit of reliability continues to drive innovation in burn-in procedures.
Recent Technological Advancements
The semiconductor industry has witnessed a significant transformation in wafer level burn-in (WLBI) techniques, driven by the need for higher reliability and efficiency. Aehr Test Systems has been at the forefront of this revolution, introducing exclusive and patented techniques that address the challenges of testing and burning-in wafers. Their approach ensures that all the thousands of dies on GaN and SiC wafers remain in complete contact throughout the process, a critical factor for the success of WLBI.
Recent advancements have also been marked by the integration of digital elements with physical production lines. This synergy has led to the development of new software solutions that enhance the WLBI process, as evidenced by Renesas’s acquisition of Altium. Such strategic moves are indicative of the industry’s shift towards a more digitalized approach, which promises to streamline WLBI procedures and improve overall outcomes.
The table below summarizes some of the key technological advancements in WLBI:
Year | Advancement | Impact |
---|---|---|
2023 | Aehr Test Systems’ patented contact techniques | Enhanced die contact integrity |
2024 | Renesas’s acquisition of Altium | Improved software solutions for WLBI |
Impact on Semiconductor Reliability
The advancements in wafer level burn-in techniques have marked a significant milestone in the quest for semiconductor reliability. These techniques are pivotal in preempting potential failures, thereby enhancing the overall quality of semiconductor devices. The integration of these advanced procedures has led to a notable reduction in early-life failures, a critical aspect for consumer trust and product lifespan.
Recent data underscores the efficacy of these improvements. For instance, a study on the impact of enhanced burn-in procedures on device longevity showed a decrease in failure rates by up to 35% within the first year of operation. This is a testament to the importance of rigorous testing in the semiconductor manufacturing process.
Year | Failure Rate Reduction |
---|---|
2022 | 20% |
2023 | 25% |
2024 | 35% |
The implications of these advancements are far-reaching, not only for manufacturers but also for end-users who benefit from more reliable electronics. As the Logic Semiconductor Market continues to grow, the demand for fail-proof devices becomes increasingly paramount, making wafer level burn-in an indispensable step in the production of high-quality semiconductors.
Cutting-Edge Equipment and Methodologies
Benchmark Electronics’ Expansion and High-Tech Machinery
Benchmark Electronics has recently undertaken a significant expansion in Malaysia, with an investment of RM802.7 million aimed at enhancing their semiconductor fabrication capabilities. This expansion is a testament to the company’s dedication to maintaining a competitive edge in the semiconductor industry, which is known for its rapid technological advancements.
The investment focuses on high-tech front-end semiconductor machinery, including state-of-the-art lithography systems and plasma etcher systems. These tools are crucial for the intricate processes involved in semiconductor manufacturing, where precision and reliability are paramount.
Benchmark’s commitment to technological excellence is not just about expanding capacity but also about ensuring the highest quality and reliability of semiconductor components. The thermal treatment in the burn-in process, which previously allowed defects to remain expanded, is now being refined to ensure that any expanded defects contract and return to their original state, enhancing the overall reliability of the chips produced.
Archer’s Validation of gFET Chip Design
Archer Materials has made significant strides in the semiconductor industry with the successful validation of its advanced graphene field effect transistor (gFET) chip design. This milestone was achieved through a collaboration with a commercial foundry partner in the Netherlands, where a whole four-inch wafer run was completed without a hitch. The new gFET devices, which are at the forefront of biochip technology, have been fabricated, marking a pivotal step in the company’s journey towards revolutionizing chip and biochip developments.
The company’s financial position is robust, with a reported $21.5 million in cash reserves and no debt, underpinning its strong commitment to innovation. Archer’s dual focus on a room temperature quantum computing chip and a biochip capable of detecting multiple diseases showcases its dedication to pushing the boundaries of microelectronics. This progress is not only a testament to Archer’s technical expertise but also to the potential of gFET technology in enhancing the performance and reliability of semiconductor devices.
Innovations in IC Substrate Technology
The semiconductor industry is witnessing a significant shift with the introduction of advanced IC substrate technology. These substrates are crucial for high-end applications such as cloud services, data centers, and health devices due to their dense conductor paths and multi-layered structure, which offer superior performance over traditional PCBs.
AT&S’s new facility in Malaysia represents a strategic expansion in the IC substrate sector. The Kulim operations, launching in Q4 2024, will not only manufacture but also engage in R&D for high-performance processors. This move is expected to catalyze growth in the region’s electronics and electrical industry.
The following table summarizes the key aspects of AT&S’s new IC substrate manufacturing facility:
Feature | Detail |
---|---|
Location | Kulim Hi-Technology Park, Kedah, Malaysia |
Launch Date | Q4 2024 |
Specialization | IC Substrates for high-end applications |
Investment | Over EUR 1 billion |
Significance | First AT&S production plant in Southeast Asia |
Potential Impact | Expansion of E&E industry, R&D activities |
Datuk Wira Arham Abdul Rahman of MIDA highlighted that this facility will solidify Malaysia’s position as a key production center in Asia, attracting further investments and expansions in the semiconductor field.
Integration with Advanced Manufacturing Processes
Additive Assurance’s AMiRIS-LF System for L-PBF Machines
In the realm of additive manufacturing, Additive Assurance has made a significant stride with the introduction of their AMiRIS-LF system. This new product is designed to enhance the process monitoring capabilities of larger-format laser powder bed fusion (L-PBF) machines. Specifically targeting machines with a build area of 400 millimeters or larger, the AMiRIS-LF system is a testament to the company’s commitment to ensuring part quality in metal 3D printing.
The AMiRIS-LF system stands out for its ability to provide real-time monitoring and quality assurance during the manufacturing process. This is particularly crucial for industries where precision and reliability are non-negotiable, such as aerospace and defense. By integrating this system, manufacturers can expect a significant reduction in the risk of defects and an increase in overall production efficiency.
Here are some key features of the AMiRIS-LF system:
- Tailored for large-format L-PBF machines
- Real-time process monitoring
- Enhanced quality assurance
- Suitable for critical industry applications
LBT Innovations’ APAS PharmaQC for Automated Quality Control
LBT Innovations has reached a significant milestone with its APAS PharmaQC system, declaring it commercially ready following a rigorous R&D phase. This cutting-edge automated quality control device has successfully completed primary validation and has been formally introduced to AstraZeneca, a key collaborator in its development. The APAS PharmaQC system is set to revolutionize pharmaceutical manufacturing quality control by offering automated imaging and analysis capabilities.
The introduction of APAS PharmaQC into the market underscores the growing trend towards automation in quality control processes. The system’s features include:
- Automated imaging for precise quality inspection
- Advanced analysis algorithms for reliable results
- Streamlined integration with existing manufacturing workflows
This innovation is expected to enhance efficiency and reliability in pharmaceutical production, ensuring higher standards of quality and compliance. As the industry continues to evolve, the role of automated systems like APAS PharmaQC becomes increasingly critical in maintaining competitive edge and meeting stringent regulatory requirements.
GPC Electronics’ Expansion with SMT Manufacturing Line
In a significant development for the Australian electronics manufacturing sector, GPC Electronics has broadened its operational capabilities with the introduction of a new surface mount technology (SMT) manufacturing line at its Penrith facility in Sydney. This expansion is a testament to the company’s commitment to embracing cutting-edge technologies to enhance production efficiency and meet the growing demands of the industry.
The installation of the new SMT line was a collaborative effort between GPC Electronics engineers and specialists from Hawker Richardson, an industrial machinery firm. The synergy between these teams underscores the importance of strategic partnerships in driving technological advancements within the manufacturing landscape.
GPC Electronics, recognized as Australia’s largest electronics manufacturer, is well-known for its ability to handle diverse production volumes, ranging from small batches to large-scale runs. This flexibility is crucial in an industry where the ability to scale production in response to market dynamics can be a significant competitive advantage.
The Role of Data Analytics and IoT in Burn-In Procedures
Harnessing IoT for Real-Time Monitoring
The integration of the Internet of Things (IoT) with burn-in procedures has ushered in a new era of data intelligence for semiconductor manufacturing. By equipping burn-in systems with IoT sensors, manufacturers gain the ability to monitor tests in real time, leading to immediate insights and enhanced decision-making capabilities.
IoT devices, when synchronized with existing ERP systems, provide a seamless flow of information. This synergy allows for the optimization of burn-in processes, ensuring that each wafer undergoes the most effective stress tests for its specific characteristics. The table below illustrates the benefits of IoT integration in burn-in procedures:
Benefit | Description |
---|---|
Efficiency | Reduction in test time and resource usage |
Accuracy | Improved detection of defects and failures |
Predictability | Enhanced forecasting of potential issues |
Scalability | Ability to handle increased volumes with precision |
Adaptive test ramps, as mentioned by NI’s Schuldenfrei, are a testament to the adaptability of IoT in various stages of semiconductor testing, including wafer sort and system-level test. This adaptability is crucial in an industry that is constantly seeking ways to reduce test time and enhance the quality of its products.
ERP and IoT Synergy for Process Optimization
The convergence of Enterprise Resource Planning (ERP) systems with the Internet of Things (IoT) is transforming the manufacturing landscape. ERP systems, when integrated with IoT devices, enable real-time data collection and analysis, enhancing decision-making and operational efficiency. This synergy allows for the automation of complex processes and the modernization of legacy equipment without the need for extensive capital investment.
The benefits of ERP and IoT integration are manifold, leading to streamlined operations and improved resource management. Below is a list highlighting key advantages:
- Real-time monitoring and control of manufacturing processes
- Enhanced predictive maintenance through data analytics
- Improved inventory management with IoT-enabled tracking
- Energy savings and reduced waste through optimized machine performance
As manufacturers continue to adopt these technologies, the potential for process optimization seems boundless. The ability to adapt and evolve with these advancements will be crucial for maintaining competitiveness in the ever-changing industrial sector.
Case Studies: IoT Implementation Successes
The integration of IoT in burn-in procedures has led to remarkable successes across various manufacturing sectors. Real-time monitoring and data analytics have transformed the way factories operate, providing insights that were previously unattainable. For instance, the development of a wafer-type plasma monitoring sensor has significantly enhanced the precision of burn-in tests, ensuring higher semiconductor reliability.
In the realm of manufacturing, the synergy between IoT devices and ERP software has been a game-changer. Manufacturers have been able to modernize and automate their processes, leading to increased efficiency and reduced downtime. The ‘Smart Enough’ solution, as discussed in a recent webinar, exemplifies how even small and medium-sized enterprises can leverage IoT to gain a competitive edge.
The following table highlights key outcomes from various case studies where IoT implementation has proven successful:
Company | Outcome | Improvement |
---|---|---|
DMTC Ltd | Digitization Journey Initiated | Enhanced Collaboration |
Natural Pet Food Group | Operations Optimization | Global Expansion Support |
Venlo Holdings | Rapid Digitization | Accommodated Growth |
These examples underscore the potential of IoT to revolutionize manufacturing processes, including wafer level burn-in, by providing actionable insights and fostering continuous improvement.
Future Directions and Industry Implications
Predictive Maintenance and Machine Learning Integration
The integration of predictive maintenance with machine learning is transforming the landscape of wafer level burn-in techniques. Machine learning algorithms are now capable of predicting equipment failures before they occur, significantly reducing downtime and maintenance costs. This proactive approach to maintenance is made possible by analyzing vast amounts of operational data to detect subtle patterns indicative of potential issues.
Key benefits of integrating predictive maintenance with machine learning include:
- Enhanced equipment reliability and lifespan
- Optimization of maintenance schedules
- Reduction in unexpected breakdowns
- Improved safety conditions for workers
As industries continue to embrace these technologies, the reliability and efficiency of semiconductor manufacturing processes are expected to reach new heights. The table below illustrates the impact of predictive maintenance on key performance indicators (KPIs):
KPI | Before Integration | After Integration |
---|---|---|
Equipment Downtime | 15% | 5% |
Maintenance Costs | $200,000 | $120,000 |
Unscheduled Repairs | 30 | 10 |
The data underscores the substantial improvements in operational performance, showcasing the value of machine learning in predictive maintenance strategies.
Green Energy Considerations in Burn-In Testing
As the semiconductor industry intensifies its focus on sustainability, green energy considerations in burn-in testing have become pivotal. The integration of renewable energy sources into the burn-in process is not just an environmental imperative but also a potential avenue for cost savings in the long term.
Efforts to minimize the carbon footprint of burn-in procedures are underway, with companies exploring various strategies:
- Utilizing energy-efficient burn-in equipment
- Implementing smart energy management systems
- Sourcing electricity from renewable resources
- Reducing energy consumption during non-peak hours
These initiatives are complemented by advancements in thermal management, such as MGA Thermal’s simulation of a decade-long working life for its energy storage blocks. Such innovations are crucial for ensuring that burn-in tests are conducted with minimal environmental impact while maintaining high reliability standards.
The Road Ahead for Semiconductor Manufacturing
The semiconductor industry is poised for transformative growth, with the 2024 Semiconductor Industry Outlook by Deloitte highlighting key trends that will shape the market. As nations like Malaysia prioritize the industry in their economic strategies, initiatives such as the New Industrial Master Plan 2030 (NIMP 2030) aim to advance economic complexity and revitalize manufacturing sectors by moving up the value chain.
In Australia, the focus is on developing a robust talent pipeline to support a burgeoning local chip industry, recognizing the need for specialized skills to drive innovation and growth. The establishment of the National Semiconductor Strategic Task Force in Malaysia underscores the commitment to bolster manufacturing and design capabilities, fostering stronger linkages between SMEs and MNCs.
The Logic Semiconductor Market’s projected CAGR of 10.4% through 2031 indicates a vibrant future, with demand for high-speed processing and compact electronics driving market expansion. This growth trajectory presents a wealth of opportunities for stakeholders to innovate and capture new market segments, ensuring the semiconductor industry remains a dynamic and essential part of the global economy.
Conclusion
The advancements in wafer level burn-in techniques signify a pivotal shift in semiconductor reliability and quality assurance. As we have explored throughout this article, the integration of new technologies and methodologies has not only enhanced the efficiency of burn-in processes but also contributed to the overall robustness of electronic components. From the strategic expansions of companies like Benchmark Electronics to the innovative IC substrate technologies set to launch in Kulim, the industry is witnessing a renaissance in high-tech manufacturing capabilities. The successful validation of Archer’s biochip design and the commercial readiness of LBT Innovations’ PharmaQC device underscore the critical role of advanced burn-in techniques in ensuring the performance and longevity of semiconductor devices. As we move forward, these developments promise to bolster the reliability of electronics, driving progress in fields ranging from cloud computing to healthcare. The future of semiconductor manufacturing is bright, with reliability at its core, revolutionized by the cutting-edge wafer level burn-in techniques we have discussed.
Frequently Asked Questions
What is wafer level burn-in and why is it important?
Wafer level burn-in is a process of testing integrated circuits (ICs) at the wafer stage to detect and screen out potential failures before they are packaged. This is crucial for ensuring the reliability of semiconductor devices, as it helps to identify defects caused by manufacturing variations and reduces the likelihood of field failures.
How have recent technological advancements improved wafer level burn-in techniques?
Recent advancements have introduced more sophisticated equipment, such as high-tech lithography systems and plasma etcher systems, which allow for more precise and efficient burn-in processes. Additionally, innovations in IC substrate technology have led to denser conductor paths and better performance, further enhancing the burn-in procedure.
What role does IoT play in modern burn-in procedures?
The Internet of Things (IoT) plays a significant role by enabling real-time monitoring and data analytics of burn-in procedures. This integration allows for immediate feedback and process optimization, leading to higher quality control and reduced time-to-market for semiconductor products.
Can you explain the significance of GPC Electronics’ expansion with a new SMT manufacturing line?
GPC Electronics’ expansion with a new surface mount technology (SMT) manufacturing line represents a significant step in enhancing their production capacity and capability. The latest technology incorporated in this line allows for more efficient and precise assembly of electronic components, which is essential for producing high-quality semiconductor devices.
What is the AMiRIS-LF system and how does it contribute to the manufacturing process?
The AMiRIS-LF system is a process monitoring solution developed by Additive Assurance for larger-format laser powder bed fusion (L-PBF) machines. It is tailored for machines with a build area of 400 millimeters or larger and helps ensure the quality of additive manufacturing processes by providing real-time insights and analytics.
How might predictive maintenance and machine learning affect the future of wafer level burn-in?
Predictive maintenance, combined with machine learning algorithms, can revolutionize wafer level burn-in by predicting equipment failures before they occur, reducing downtime, and optimizing maintenance schedules. This proactive approach can lead to more consistent burn-in results and extend the life of the burn-in equipment.