Understanding Wafer Burn-In Processes: Best Practices and Techniques
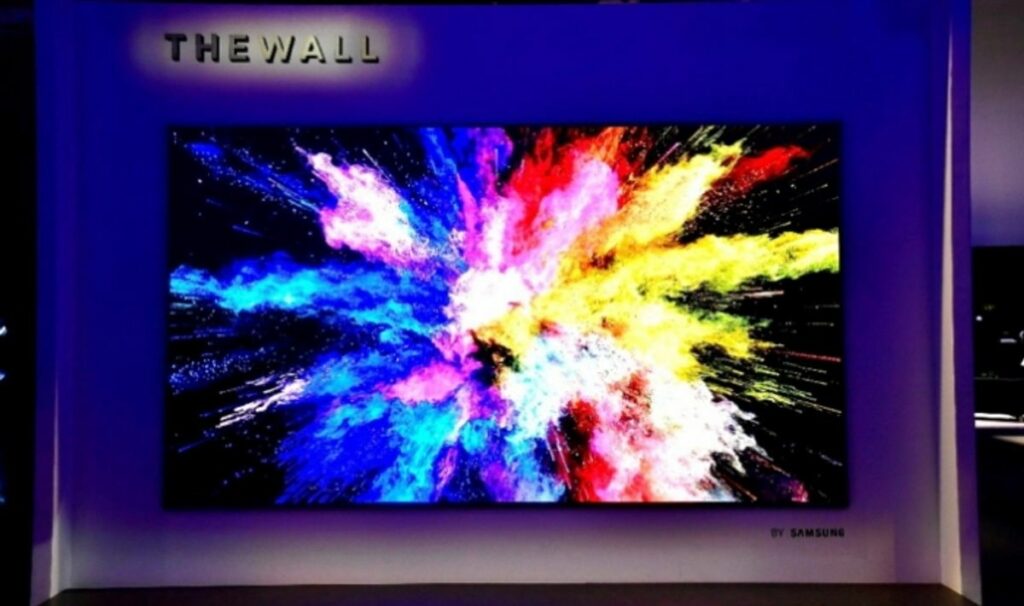
The wafer burn-in process is a critical step in semiconductor manufacturing, aiming to detect early failures and ensure the reliability of integrated circuits. This article dives into the best practices and techniques for an effective wafer burn-in process, exploring the fundamentals, advanced equipment, and the latest trends shaping the future of this vital procedure.
Key Takeaways
- Wafer burn-in is essential for identifying early-life failures and improving the reliability of semiconductor devices.
- Advanced burn-in techniques and automation are pivotal for enhancing the efficiency and accuracy of stress testing.
- Optimizing time and temperature parameters is crucial for effective burn-in without compromising wafer integrity.
- Emerging technologies such as AI and predictive modeling are revolutionizing the way burn-in processes are simulated and optimized.
- Custom burn-in strategies and innovations in equipment are addressing the challenges posed by high-power and high-density wafers.
Fundamentals of Wafer Burn-In Processes
Defining Wafer Burn-In and Its Objectives
Wafer burn-in is a critical procedure in the semiconductor industry, ensuring the reliability and quality of semiconductor devices. It involves subjecting semiconductor wafers to elevated temperatures and electrical stress to accelerate the failure of weak components before they are packaged and shipped. This process helps in identifying and eliminating early-life failures, thereby increasing the overall robustness of the final product.
The primary objectives of wafer burn-in include improving product reliability, reducing return rates, and enhancing customer satisfaction. By detecting defects early in the manufacturing cycle, companies can avoid costly recalls and maintain their reputation for quality. The process is especially crucial for high-performance and safety-critical applications where failure is not an option.
To achieve these objectives, the burn-in process is carefully designed and monitored. Key parameters such as time and temperature are optimized to ensure that the stress conditions are sufficient to reveal potential defects without causing damage to the good dies. The following list outlines the core components of a typical burn-in process:
- Selection of appropriate stress conditions
- Application of electrical and thermal stress
- Monitoring of wafer performance
- Analysis of test results to identify failures
- Feedback loop for process improvement
Historical Evolution of Burn-In Techniques
The evolution of wafer burn-in techniques has been marked by significant advancements aimed at improving the reliability and performance of semiconductor devices. Early burn-in processes were relatively rudimentary, often involving manual testing and simple stress applications. Over time, the industry recognized the need for more sophisticated methods to address the increasing complexity of integrated circuits.
In the 1980s and 1990s, the focus shifted towards the development of automated burn-in systems, which allowed for more consistent and controlled stress application. This period also saw the introduction of temperature cycling and voltage stressing as standard practices. The table below highlights key milestones in the evolution of burn-in techniques:
Decade | Advancements |
---|---|
1970s | Manual testing and simple stress applications |
1980s | Introduction of automated burn-in systems |
1990s | Standardization of temperature cycling and voltage stressing |
2000s | Integration of software for monitoring and control |
2010s | Adoption of advanced thermal and voltage stress methods |
As semiconductor technology continued to advance into the 2000s, software integration became crucial for monitoring and controlling the burn-in process. This allowed for more precise adjustments and real-time data analysis, leading to improved outcomes. The last decade has seen the adoption of even more advanced thermal and voltage stress methods, tailored to the specific needs of modern high-density and high-power wafers.
The Science Behind Stress Testing in Burn-In
Stress testing during the wafer burn-in process is a critical step in ensuring the reliability and longevity of semiconductor devices. The goal is to accelerate the failure mechanisms that could occur under normal operating conditions, thereby identifying potential defects and weaknesses in the wafer. This is achieved by applying controlled thermal and electrical stresses that mimic or exceed the conditions the device will face in its working environment.
The process involves a series of rigorous tests that can be broken down into three main categories:
- Thermal Stress Testing: Exposing the wafer to high temperatures to identify heat-related failures.
- Electrical Stress Testing: Applying voltage and current levels beyond typical operating ranges to test electrical robustness.
- Mechanical Stress Testing: Subjecting the wafer to physical forces to assess structural integrity.
By analyzing the results of these tests, engineers can determine the thermal and mechanical stress distribution within the semiconductor package. This analysis is crucial for predicting the fatigue life of interconnect structures like solder bumps, which are often the most failure-prone areas. The interaction between temperature and thermal stress is particularly important, as it can lead to interconnect cracking and other defects. Advanced simulation techniques, such as finite element modeling (FEM), are frequently used to optimize material and structural designs, ensuring that the final product can withstand the rigors of its intended application.
Advanced Burn-In Techniques and Equipment
State-of-the-Art Burn-In Chambers and Systems
The evolution of wafer burn-in processes has led to the development of state-of-the-art burn-in chambers and systems that are crucial for ensuring the reliability of semiconductor devices. These advanced systems are designed to accommodate the increasing complexity of semiconductor wafers, including those made from silicon carbide (SiC), which are known for their high power and thermal conductivity.
Modern burn-in chambers are equipped with sophisticated features such as precise temperature control, uniform heat distribution, and advanced monitoring capabilities. These enhancements allow for more effective stress testing, which is essential for identifying potential failures in semiconductor devices before they reach the market. The table below outlines some of the key specifications and capabilities of contemporary burn-in systems:
Feature | Description |
---|---|
Temperature Range | Capable of reaching extreme temperatures required for thorough stress testing. |
Heat Distribution | Engineered for uniform temperature application across the entire wafer surface. |
Monitoring Systems | Integrated sensors and software for real-time data analysis and adjustments. |
Customization Options | Configurable settings to cater to specific wafer materials and sizes. |
As the demand for high-quality SiC crystals grows, manufacturers are scaling up their production capabilities. However, the complexity of growing quality SiC crystals means that there is a pressing need for more advanced burn-in systems that can meet global production targets. This challenge underscores the importance of continuous innovation in burn-in technology to support the semiconductor industry’s escalating demands.
Automation and Control in Burn-In Procedures
The integration of automation and control systems in wafer burn-in procedures has revolutionized the semiconductor manufacturing industry. Automated systems are now capable of handling complex tasks with precision and repeatability, reducing the potential for human error and increasing throughput. These systems often include features such as auto laser wafer marking and dual-arm robotic mechanisms, which support real-time monitoring and control of critical parameters like voltage and power.
To illustrate the capabilities of modern burn-in testers, consider the example of the FitTech Co., Ltd. Burn In Tester, which is integrated with a robot system for enhanced efficiency. The table below summarizes some of the key features of this advanced equipment:
Feature | Description |
---|---|
Auto Laser Marking | Enables precise identification and tracking of wafers. |
Dual-Arm Robotics | Facilitates automated handling and transport of wafers. |
Real-Time Monitoring | Allows for continuous observation of voltage and power levels. |
Automated Control | Ensures consistent application of stress tests across all wafers. |
Adopting such sophisticated equipment is essential for maintaining a competitive edge in the industry. It not only streamlines the burn-in process but also provides a platform for further innovations in semiconductor testing and quality assurance.
Innovations in Thermal and Voltage Stress Methods
The relentless pursuit of semiconductor efficiency and reliability has led to significant innovations in thermal and voltage stress methods. Aehr Test Systems has been at the forefront, advancing GaN technologies with their FOX systems that integrate thermal control and electrical stress conditions for wafer-level burn-in testing. This approach not only enhances the detection of early-life failures but also contributes to the overall yield improvement of semiconductor devices.
Recent studies have explored the intricate relationship between thermal stress and device integrity. For instance, Wang’s research using a hybrid finite element method revealed the impact of silicon oxide isolation thickness on the transient electro-thermal-mechanical response of multilayer TSVs. Similarly, Ni’s work on the reliability of TSVs filled with carbon nanotubes under electro-thermal coupling fields has validated their high resilience, offering insights into material and structural design optimizations.
The table below summarizes key findings from recent research on thermal and voltage stress methods:
Study | Focus | Key Findings |
---|---|---|
Wang | TSVs Electro-Thermal Response | Sensitivity to isolation thickness |
Ni | TSVs with CNTs Reliability | High resilience under thermal stress |
These advancements underscore the importance of continuous innovation in burn-in processes, ensuring that the semiconductor industry can meet the demands of increasingly complex and power-intensive devices.
Best Practices for Effective Burn-In
Optimizing Time and Temperature Parameters
The optimization of time and temperature parameters is a critical aspect of the wafer burn-in process. Proper calibration of these parameters can significantly enhance the reliability and performance of semiconductor devices. It is essential to consider the environmental conditions in which the device will operate, as different temperature ranges can affect power supply performance and efficiency. For instance, high-temperature industrial applications may require different settings compared to devices used in outdoor environments with fluctuating temperatures.
Managing internal temperatures is equally important. Temperature control systems are vital in preventing degradation and energy loss in both high heat and extreme low conditions. The table below outlines the recommended temperature ranges for various environmental conditions and their corresponding time settings for an effective burn-in process:
| Environment Type | Temperature Range (
) | Time Duration |
|——————|———————-|—————|
| Industrial High-Temperature | 85-125 | 48-72 hours |
| Outdoor Variable | -40 to 85 | 72-96 hours |
| Standard | 55-85 | 24-48 hours |
By adhering to these guidelines and continuously monitoring the burn-in results, manufacturers can ensure uniformity and reliability across all wafers.
Ensuring Uniformity and Reliability Across Wafers
Uniformity and reliability are critical to the success of wafer burn-in processes. Ensuring that each wafer undergoes the same level of stress testing is essential for maintaining high yield rates and the overall quality of semiconductor devices. Variations in temperature or voltage can lead to inconsistent results, which in turn can affect the performance and longevity of the final product.
To achieve uniformity, manufacturers must meticulously calibrate and monitor their burn-in equipment. This includes regular checks and maintenance to prevent any deviations that could compromise the burn-in process. Additionally, the use of advanced sensors and feedback systems can help in maintaining a consistent environment for all wafers.
Key factors influencing yield and quality include surface smoothness, purity of the silicon, and the uniformity of the dopant distribution. A bulleted list of best practices for ensuring uniformity and reliability might include:
- Regular calibration of burn-in chambers
- Implementation of real-time monitoring systems
- Strict adherence to predefined stress test parameters
- Comprehensive data analysis to identify and rectify any irregularities
Monitoring and Analysis of Burn-In Results
The monitoring and analysis phase is critical in the wafer burn-in process, as it ensures that the stress tests have been effective and that the wafers meet the required reliability standards. Real-time monitoring is essential for detecting any immediate failures and allows for adjustments to be made on-the-fly to optimize the burn-in conditions.
Analysis of the results post-burn-in involves a detailed examination of the wafers to identify any latent defects that could lead to future failures. This is where advanced sensors, such as the newly developed wafer-type plasma monitoring sensor, come into play, providing precise measurements and enhancing the overall efficiency of the burn-in process.
To illustrate the importance of systematic analysis, consider the following table which summarizes key metrics evaluated during the burn-in analysis phase:
Metric | Description | Importance |
---|---|---|
Defect Density | Number of defects per unit area | High |
Failure Rate | Frequency of failures over time | Critical |
Parametric Shifts | Changes in electrical parameters | Moderate |
By closely monitoring these metrics, engineers can ensure that the burn-in process yields wafers with the highest possible quality and longevity.
Challenges and Solutions in Wafer Burn-In
Dealing with High-Power and High-Density Wafers
As semiconductor devices continue to shrink in size, the challenge of effectively burn-in testing high-power and high-density wafers becomes more pronounced. The miniaturization trend demands advanced chuck designs that can manage smaller wafers with improved heat dissipation and particle control.
The transition from the standard 300mm wafers to those measuring 200mm or less has necessitated the development of innovative layouts for these compact systems. These designs are crucial for maintaining the integrity of the wafer during the burn-in process, which subjects the wafer to extreme conditions to ensure reliability.
Advanced packaging technologies like Flip Chip (FC), Wafer-Level Packaging (WLP), and 3D packaging have compounded the complexity of burn-in testing. The reduced thermal space and increased power density create intricate physical fields that must be carefully managed:
- Electricity: Ensuring consistent electrical performance under stress.
- Heat: Effective dissipation to prevent damage.
- Stress: Minimizing mechanical stress to avoid structural defects.
Addressing these challenges requires a multifaceted approach that includes both innovative equipment design and precise control of burn-in parameters.
Overcoming Limitations of Traditional Burn-In Methods
As semiconductor technology advances, the limitations of traditional burn-in methods become more apparent. Traditional techniques often struggle to keep pace with the increasing complexity of wafers, particularly when it comes to high-power and high-density devices. To address these challenges, the industry has been exploring new approaches that can more effectively induce and monitor stress in semiconductor wafers.
One such approach involves the refinement of biasing techniques. The scaled, multi-frequency approach to bias has shown its limits in effectively controlling critical wafer-level reactions. This has led to the development of alternative strategies that aim to enhance the precision and effectiveness of burn-in processes. For instance, the implementation of adaptive biasing methods allows for dynamic adjustments during the burn-in procedure, ensuring better control over the stress applied to the wafers.
Another key area of improvement is the integration of advanced monitoring systems. These systems are designed to provide real-time data on the wafer’s response to stress, enabling immediate adjustments and more accurate end-results. The table below summarizes some of the emerging techniques and their benefits:
Technique | Benefit |
---|---|
Adaptive Biasing | Dynamic stress control |
Real-time Monitoring | Immediate feedback |
Enhanced Thermal Methods | Improved heat distribution |
By adopting these and other innovative methods, manufacturers can overcome the limitations of traditional burn-in processes, leading to more reliable and efficient production of semiconductor devices.
Custom Burn-In Strategies for Advanced Semiconductor Materials
As semiconductor materials evolve, custom burn-in strategies become essential to address the unique challenges they present. Advanced materials such as Silicon/Graphite composites require tailored approaches to ensure that the burn-in process effectively induces stress without damaging the intricate structures of the wafer.
The integration of Through-Silicon Vias (TSVs) and micro pin fins, for instance, has necessitated the development of specialized heat transfer performance assessments during burn-in. Researchers like He et al. have investigated the heat transfer performance for TSVs embedded in micro pin fins, highlighting the need for precision in thermal management.
To cater to the miniaturization trend in electronics, burn-in strategies must also adapt to smaller wafer sizes. The shift towards 200mm and smaller wafers demands chucks and systems that can handle reduced footprints while maintaining enhanced heat dissipation and particle management. Below is a list of key considerations for custom burn-in strategies:
- Tailoring thermal processes to the material properties of advanced semiconductors.
- Ensuring accurate simulation of warping effects, especially for stacked-chip wafers with complex Redistribution Layer (RDL) structures.
- Developing dynamic electrothermal macromodels to maintain signal integrity in highly integrated systems.
- Adapting equipment layouts to accommodate the miniaturization of electronic components.
Future Trends and Research Directions
Predictive Modelling and Simulation of Burn-In Processes
The integration of predictive modelling and simulation into burn-in processes represents a significant advancement in the semiconductor industry. Predictive process monitoring has emerged as a powerful tool for forecasting the remaining cycle time in automated manufacturing, enhancing the efficiency and precision of burn-in procedures. By leveraging data-driven temperature estimation and adaptive test ramps, manufacturers can tailor the burn-in process to the specific needs of each wafer, ensuring optimal stress application and defect identification.
Recent studies have demonstrated the efficacy of data-driven approaches in temperature estimation for multi-stage processes, which is crucial for the burn-in of semiconductor wafers. These methods enable the prediction of thermal behaviors and the adjustment of parameters in real-time, reducing the risk of damage due to overheating or insufficient stress. Adaptive testing, as highlighted in the literature, is particularly relevant in the data intelligence era, where wafer-level adaptive testing is the most leveraged and simplest to deploy in the context of post-processing.
The table below summarizes key publications that have contributed to the field of predictive modelling and simulation in burn-in processes:
Author(s) | Year | Title | Reference |
---|---|---|---|
J. Wallace et al. | 2023 | Computer-Human Interaction in Play | ACM doi:10.1145/3573382.3616076 |
J. Friederich et al. | 2023 | Predictive Process Monitoring for Prediction of Remaining Cycle Time in Automated Manufacturing | IEEE doi:10.1109/ETFA54631.2023.10275361 |
M. Wrobel et al. | 2023 | Data-driven Temperature Estimation for a Multi-Stage Press Hardening Process | IFAC-PapersOnLine doi:10.1016/j.ifacol.2023.10.1785 |
These advancements pave the way for more sophisticated burn-in processes, where predictive analytics and simulations play a crucial role in ensuring the quality and reliability of semiconductor devices.
Integration of AI and Machine Learning for Process Optimization
The integration of AI and machine learning into wafer burn-in processes marks a significant leap towards optimizing semiconductor test costs. These intelligent systems can analyze vast amounts of data to identify patterns and predict outcomes, leading to more efficient and cost-effective testing strategies. For instance, AI-driven test optimization can significantly reduce the cost of production testing at various stages, including wafer-sort test, burn-in test, and system level test.
Machine learning algorithms, particularly those involving active learning, can adapt and improve over time. This adaptability ensures that the burn-in process remains at the cutting edge of technology, continuously evolving with the semiconductor industry’s advancements. The table below illustrates the potential improvements in key performance indicators (KPIs) when AI and machine learning are applied to the burn-in process:
KPI | Before AI Integration | After AI Integration |
---|---|---|
Test Time Reduction | 10% | 30% |
Cost Savings | 15% | 40% |
Yield Improvement | 5% | 20% |
By leveraging these technologies, manufacturers can expect not only to enhance the reliability of their products but also to gain a competitive edge in the market.
Emerging Technologies Influencing Burn-In Protocols
The semiconductor industry is witnessing a transformative phase with the advent of emerging technologies that are reshaping wafer burn-in protocols. These technologies aim to enhance the efficiency and effectiveness of the burn-in process, which is critical for ensuring the reliability of next-generation chips.
One such advancement is the integration of wafer-level test and burn-in procedures, which are now being adopted to improve Wide Bandgap (WBG) semiconductor reliability. This integration is crucial for power electronics, where GaN and SiC materials are becoming increasingly prevalent. The ability to test and stress these materials at the wafer level is a significant step forward in the burn-in process.
Moreover, the industry is exploring the use of predictive modelling and simulation to anticipate potential failure modes and optimize burn-in parameters. This approach, coupled with the application of AI and machine learning, can lead to more intelligent and adaptive burn-in strategies. These strategies are not only more efficient but also reduce the time-to-market for semiconductor devices.
The table below highlights the impact of these technologies on key aspects of the burn-in process:
Technology | Impact on Burn-In Process |
---|---|
Wafer-Level Test and Burn-In | Enhances WBG semiconductor reliability |
Predictive Modelling | Optimizes burn-in parameters |
AI and Machine Learning | Enables adaptive burn-in strategies |
As the industry continues to evolve, it is clear that these emerging technologies will play a pivotal role in the future of semiconductor testing and burn-in protocols.
Conclusion
In conclusion, the wafer burn-in process is a critical step in ensuring the reliability and performance of semiconductor devices. Throughout this article, we have explored various best practices and techniques that contribute to an effective burn-in process. From understanding the fundamental principles to implementing advanced simulation models and integrating the latest research findings, such as those from Schüßler et al. (2023) on process simulation and Fischmann et al. (2023) on tooth root burnishing, we have seen how meticulous attention to detail can significantly impact the final product quality. It is evident that continuous innovation and research, as demonstrated by the works of Meyer and Pfleging (2023) on laser structuring of electrodes and Böttger et al. (2024) on soft sensors for quality control, are essential in refining these processes. As technology advances, adopting these best practices and staying abreast of new techniques will be paramount for industry professionals to maintain high standards in wafer production and meet the ever-increasing demands of the electronics market.
Frequently Asked Questions
What is wafer burn-in and why is it important?
Wafer burn-in is a process where semiconductor wafers are subjected to thermal and electrical stress to identify and eliminate early-life failures. This ensures that only reliable devices reach the market, reducing warranty costs and maintaining brand reputation.
How has wafer burn-in evolved over time?
The wafer burn-in process has evolved from simple, manual operations to sophisticated, automated systems that can apply precise stress conditions. Improvements in technology have led to more efficient and effective burn-in processes that can handle complex semiconductor devices.
What are the latest advancements in burn-in equipment?
State-of-the-art burn-in chambers and systems now feature advanced temperature control, high-precision voltage stress application, and automation for consistent and repeatable stress application. These advancements enable more accurate and faster burn-in cycles.
What are some best practices for conducting an effective burn-in process?
Best practices include optimizing time and temperature parameters for the specific devices being tested, ensuring uniform stress application across all wafers, and conducting thorough analysis of burn-in results to improve yield and reliability.
What challenges are associated with burn-in of high-power and high-density wafers?
High-power and high-density wafers can generate significant heat, which can lead to non-uniform temperature distribution and stress application. Solutions include advanced cooling systems and custom burn-in strategies tailored to these types of wafers.
How might AI and machine learning impact the future of wafer burn-in processes?
AI and machine learning can be used to analyze burn-in data to predict failures, optimize burn-in parameters, and improve overall process efficiency. This can result in reduced testing times, lower costs, and higher quality semiconductor devices.