Advancements and Efficiency in Modern Wafer Production
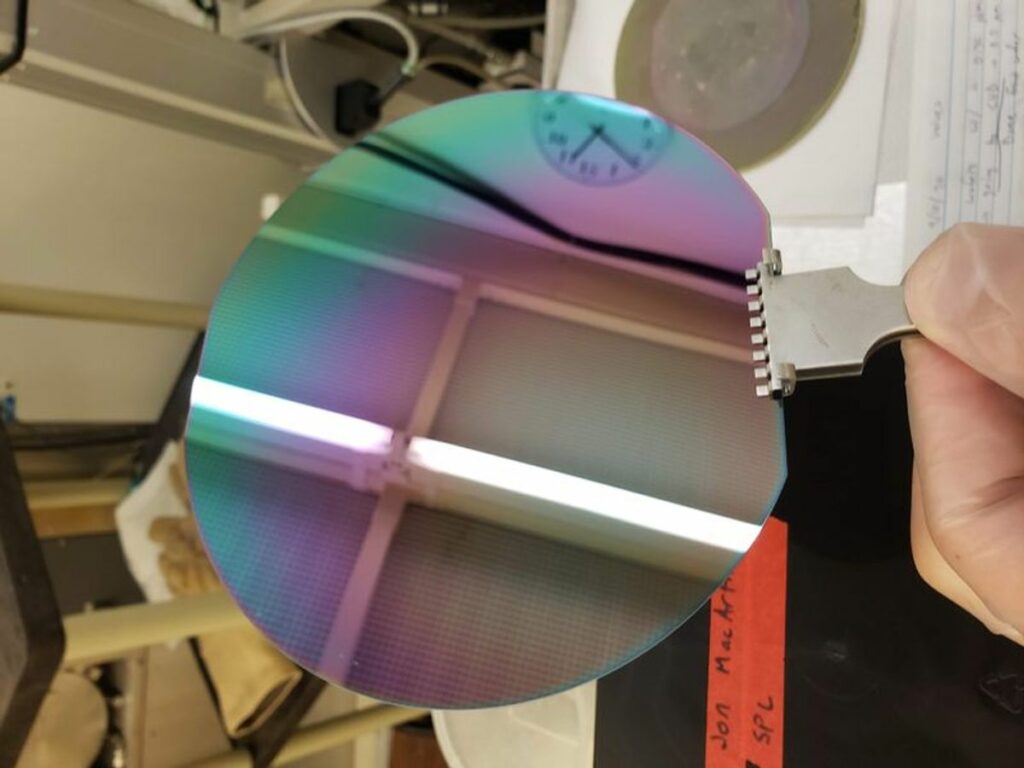
The semiconductor industry has witnessed remarkable advancements in wafer production, with innovations and efficiency playing pivotal roles in shaping the future of electronics. This article delves into the latest trends and developments in wafer fabrication, from cutting-edge manufacturing techniques to sustainable practices. We explore how these improvements not only enhance performance but also address the environmental impact of semiconductor production. Join us as we uncover the strides made in this critical field, which is at the heart of our increasingly digital world.
Key Takeaways
- 3D transistors and advanced lithography techniques are pushing the boundaries of silicon wafer fabrication, enabling more powerful and compact electronics.
- The integration of automation, robotics, and machine learning is revolutionizing wafer manufacturing, leading to higher precision and efficiency.
- Energy efficiency and sustainability are becoming central to wafer production, with efforts to reduce carbon footprints, recycle silicon, and adopt renewable energy.
- Quality control has seen significant enhancements through real-time monitoring and AI-based defect detection, optimizing yield and reducing waste.
- The future of wafer production is poised for transformative change with the exploration of new materials, nanotechnology, and the principles of Industry 4.0.
Innovations in Silicon Wafer Fabrication
Emergence of 3D Transistors
The relentless pursuit of Moore’s Law has led to a groundbreaking shift in transistor design. Integrating dimensions to enhance performance and reduce power consumption has become a pivotal strategy. 3D transistors represent a significant leap from their 2D counterparts, offering a new way to continue the trend of miniaturization and efficiency.
Researchers, including teams from Penn State, have been at the forefront of this innovation. They have successfully demonstrated the 3D integration of semiconductors on a massive scale, characterizing tens of thousands of devices. This advancement is not just a technical feat; it’s a reinvention of the building blocks of modern electronics.
The benefits of 3D transistors are numerous:
- Enhanced electrical performance
- Lower power consumption
- Increased packing density
These improvements are essential for the next generation of electronic devices, which demand ever-greater computational power and energy efficiency.
Advances in Lithography Techniques
The relentless pursuit of miniaturization in semiconductor devices has led to significant advances in lithography techniques. These techniques are crucial for defining the intricate patterns that form the circuits on a chip. As feature sizes on chips continue to shrink, the challenges in lithography grow exponentially.
Chip manufacturers, including industry giants like Intel and Samsung, are at the forefront of tackling these challenges. They are exploring new ways to push the boundaries of what’s possible with lithography, patterning, and semiconductor fabrication. The dialogue between these companies often revolves around overcoming the physical limitations that come with advanced lithography.
One of the key areas of focus is the transition to extreme ultraviolet (EUV) lithography. This technology allows for smaller feature sizes and more complex circuitry on silicon wafers. The table below summarizes the progression from traditional lithography to EUV:
Generation | Light Source | Wavelength (nm) | Feature Size (nm) |
---|---|---|---|
Traditional | Deep Ultraviolet (DUV) | 193 | >45 |
Advanced | Extreme Ultraviolet (EUV) | 13.5 | <7 |
The adoption of EUV lithography is a testament to the industry’s commitment to innovation and efficiency. As these techniques evolve, they will continue to shape the future of wafer production and the capabilities of electronic devices.
High-Purity Silicon: Achieving New Standards
The quest for high-purity silicon is a critical aspect of modern wafer production, as it directly impacts the performance and reliability of semiconductor devices. Manufacturers are constantly pushing the boundaries to achieve silicon of the highest purity, which is essential for the fabrication of advanced electronic components.
Quality standards and testing play a pivotal role in this process. The International Electrotechnical Commission (IEC) is instrumental in specifying the size, materials, and quality parameters for silicon wafers. These standards ensure that wafers meet a consistent level of quality, fostering interoperability and reliability across the semiconductor industry.
IEC Standard | Description |
---|---|
IEC 62258-1 | Specifies dimensions and other parameters for silicon wafers |
IEC 62258-2 | Defines the standard for silicon wafer materials |
IEC 62258-3 | Outlines the quality requirements for silicon wafers |
By adhering to these stringent standards, manufacturers are able to deliver products that meet the ever-increasing demands of the technology sector. The integration of sophisticated testing methods further ensures that each wafer batch achieves the new benchmarks of purity required for today’s high-performance electronics.
Automation and Robotics in Wafer Manufacturing
Robotic Process Automation (RPA)
The integration of Robotic Process Automation (RPA) in wafer manufacturing marks a significant leap towards greater efficiency and precision. By automating repetitive and high-volume tasks, RPA not only streamlines operations but also minimizes human error, leading to more consistent quality in wafer production.
Key benefits of RPA include:
- Reduction in production time
- Consistent execution of processes
- Lower operational costs
- Improved safety by reducing human intervention
As the semiconductor industry continues to evolve, the role of automation becomes increasingly critical. The adoption of RPA is a testament to the industry’s commitment to innovation and its pursuit of the next level of manufacturing excellence. With AI and robotics shaping its future, the potential for further advancements in precision and efficiency is vast.
Machine Learning for Predictive Maintenance
The integration of machine learning for predictive maintenance is revolutionizing wafer manufacturing. Predictive analytics enable early detection of potential equipment failures, reducing downtime and maintenance costs. By analyzing vast amounts of operational data, machine learning algorithms can identify patterns that precede equipment issues.
Key benefits of machine learning in predictive maintenance include:
- Increased equipment uptime: By anticipating failures, manufacturers can schedule maintenance proactively.
- Extended equipment lifespan: Timely maintenance can prevent severe damage and extend the life of machinery.
- Optimized maintenance schedules: Machine learning helps in planning maintenance activities during non-peak hours, minimizing production disruption.
The table below illustrates the impact of machine learning on maintenance efficiency:
Metric | Before ML | After ML Implementation |
---|---|---|
Downtime Reduction (%) | 25 | 45 |
Maintenance Cost Savings (%) | 20 | 35 |
Equipment Lifespan Increase (%) | 15 | 30 |
This data-driven approach not only enhances the efficiency of the maintenance process but also contributes to overall production optimization.
Enhanced Precision with Industrial Robots
The integration of industrial robots into wafer production lines has been a game-changer for the semiconductor industry. These robots are equipped with advanced sensors and machine vision systems, which allow for unparalleled precision and accuracy in handling delicate wafers. The benefits of robotic intervention are numerous, including reduced human error, consistent product quality, and the ability to operate in environments that are hazardous or unsuitable for human workers.
Robotic systems are not only precise but also highly adaptable. They can be reprogrammed for different tasks, making them a versatile asset in the production process. This adaptability is crucial as it enables quick shifts in production in response to market demands or technological advancements. The table below summarizes the key advantages of using industrial robots in wafer fabrication:
Advantage | Description |
---|---|
Precision | Robots maintain exacting standards, reducing deviations and scrap. |
Efficiency | Continuous operation without fatigue increases throughput. |
Flexibility | Easy reprogramming allows for rapid changes in production. |
Safety | Robots can work in hazardous conditions, protecting human workers. |
As the demand for smaller, more powerful electronic devices continues to grow, the role of robotics in ensuring the efficiency and precision of wafer production will only become more critical.
Energy Efficiency and Sustainability
Reducing Carbon Footprint in Production
The semiconductor industry is increasingly focusing on sustainable manufacturing practices to meet climate goals. By reducing the carbon footprint of wafer production, companies not only adhere to environmental regulations but also contribute to a greener future.
Key initiatives include optimizing energy consumption, transitioning to low-carbon energy sources, and implementing more efficient manufacturing processes. These efforts are crucial as the demand for electronic devices continues to surge, necessitating a responsible approach to production.
- Optimizing energy consumption: By refining production techniques, manufacturers can significantly lower energy usage.
- Transitioning to low-carbon energy sources: Shifting from fossil fuels to renewable energy is essential for a sustainable operation.
- Efficient manufacturing processes: Innovations in production technology can reduce waste and emissions.
Embracing these strategies not only benefits the environment but also enhances the industry’s reputation and long-term viability.
Recycling and Reclaiming Silicon
The silicon wafer industry is increasingly focusing on sustainability, with recycling and reclaiming used silicon becoming a pivotal process. The top recycling treatment is employed to recover high-quality silicon wafers, glass, and valuable materials such as silver, aluminium, and copper. This not only reduces waste but also conserves resources by extracting valuable elements that can be reused in the production cycle.
The benefits of silicon recycling are manifold, impacting both economic and environmental aspects. Here’s a brief overview of the advantages:
- Economic savings: By reclaiming materials, manufacturers can reduce the costs associated with raw material procurement.
- Environmental conservation: Recycling mitigates the environmental impact by decreasing the need for new silicon extraction and reducing landfill waste.
- Resource efficiency: Recovered materials can be reintegrated into the manufacturing process, promoting a circular economy.
Despite these benefits, challenges remain in optimizing the recycling process to ensure maximum efficiency and minimal environmental footprint. Ongoing research and technological advancements are crucial to overcoming these hurdles and achieving a more sustainable wafer production industry.
Adoption of Renewable Energy Sources
The semiconductor industry is increasingly turning to renewable energy sources to power wafer production facilities. This shift not only aligns with global sustainability goals but also offers long-term cost savings and energy security. Solar and wind energy are the most commonly adopted renewables in the sector, providing a clean and consistent power supply.
To illustrate the impact, consider the following data from a recent industry report:
Year | Percentage of Renewable Energy Usage |
---|---|
2019 | 12% |
2020 | 17% |
2021 | 23% |
2022 | 29% |
These figures show a steady increase in the adoption of renewable energy, reflecting a commitment to environmental responsibility and operational efficiency. Companies are also exploring the use of on-site renewable energy generation, such as solar panels and wind turbines, to further reduce their reliance on non-renewable sources.
Quality Control and Yield Optimization
Real-Time Monitoring Systems
The implementation of real-time monitoring systems in wafer production has revolutionized the way manufacturers approach quality control. By integrating these systems, deviations from desired specifications can be identified promptly during various stages of the manufacturing process. This proactive approach to monitoring ensures that any potential issues are addressed before they escalate into costly defects.
Real-time data collection and analysis are critical for maintaining the high standards required in wafer production. The table below illustrates the impact of real-time monitoring on key production metrics:
Metric | Before Real-Time Monitoring | After Real-Time Monitoring |
---|---|---|
Defect Rate | 5% | 2% |
Production Yield | 85% | 92% |
Downtime | 10% | 5% |
The benefits of such systems extend beyond immediate corrections. They also contribute to a deeper understanding of the production process, which can lead to continuous improvement and innovation. As a result, manufacturers are able to maintain a competitive edge in the fast-paced semiconductor industry.
Defect Detection Using AI
The integration of AI-powered automated inspection systems has marked a significant milestone in semiconductor manufacturing. These systems are equipped with advanced algorithms capable of identifying defects with a precision that was previously unattainable. The result is a substantial increase in the reliability and accuracy of defect detection, which is critical for maintaining high-quality standards in wafer production.
AI-driven defect detection not only enhances the quality but also contributes to efficiency. By rapidly scanning wafers and analyzing vast amounts of data, AI reduces the time required for inspection. This acceleration in the process allows for quicker feedback and adjustments in the manufacturing line, leading to a more streamlined production flow. The table below illustrates the impact of AI on defect detection rates compared to traditional methods:
Method | Detection Rate | Speed | Accuracy |
---|---|---|---|
Traditional | 85% | Moderate | High |
AI-powered | 98% | Fast | Very High |
The adoption of AI in defect detection is a testament to the industry’s commitment to embracing innovative technologies to drive progress. As AI systems continue to evolve, we can expect even greater advancements in the capabilities of these inspection tools, further pushing the boundaries of what is possible in wafer production.
Yield Management Strategies
Yield management in wafer production is a critical aspect that directly impacts the cost-effectiveness and overall success of semiconductor manufacturing. Effective yield management strategies are essential for maximizing the number of functional chips per wafer. One such strategy is the implementation of the Wafer Lot Disposition Control tool, which streamlines the process of wafer lot releases, retests, and holds. This tool enhances automated decision-making, reducing human error and improving throughput.
The table below outlines key metrics that are monitored and optimized through yield management systems:
Metric | Description | Impact |
---|---|---|
Defect Density | Number of defects per unit area | Directly affects chip quality |
Throughput Rate | Wafers processed per unit time | Influences production efficiency |
Retest Rate | Frequency of retesting wafers | Affects cycle time and costs |
By closely monitoring these metrics, manufacturers can identify trends and anomalies that may indicate process deviations or potential improvements. Continuous improvement in these areas leads to higher yields, which in turn, translates to greater profitability and competitive advantage in the market.
The Future of Wafer Production Technologies
Next-Generation Materials Beyond Silicon
The relentless pursuit of efficiency and performance in semiconductors has led to the exploration of next-generation materials that promise to revolutionize wafer production. Two prominent wide-bandgap semiconductor materials that have emerged are gallium nitride (GaN) and silicon carbide (SiC). These materials offer superior properties over traditional silicon, including higher thermal conductivity, greater electron mobility, and the ability to operate at higher temperatures and voltages.
The transition to these materials is not without its challenges, however. The table below outlines some of the key differences and considerations when comparing GaN and SiC with silicon:
Material | Bandgap (eV) | Thermal Conductivity (W/mK) | Electron Mobility (cm^2/Vs) |
---|---|---|---|
Silicon (Si) | 1.12 | 150 | 1400 |
GaN | 3.4 | 130 | 2000 |
SiC | 3.26 | 490 | 900 |
Adopting these materials could lead to significant advancements in power electronics, telecommunications, and even electric vehicles, where efficiency and high-power density are crucial. As the industry continues to innovate, the role of these alternative materials will likely become more prominent, shaping the future of technology.
The Role of Nanotechnology
Nanotechnology is poised to revolutionize wafer production by enabling the creation of features at an atomic scale. The integration of nanofabrication equipment is a critical step towards the miniaturization of electronic components, allowing for more complex and powerful devices. For instance, the recent addition of new nanofabrication equipment at MIT.nano, provided by Applied Materials, is set to accelerate innovation in semiconductor technology.
The potential of nanotechnology in wafer production is not limited to just scaling down sizes; it also opens up possibilities for novel materials and architectures. These advancements could lead to significant improvements in performance, energy efficiency, and even the development of entirely new types of electronic devices.
- Enhanced feature resolution
- Novel material properties
- Innovative device architectures
- Improved performance and energy efficiency
Anticipating Industry 4.0 in Wafer Fabrication
As the semiconductor industry approaches the era of Industry 4.0, the integration of smart technologies is set to redefine wafer production. The adoption of Industry 4.0 principles promises to bring about a crystal-clear future in manufacturing efficiency and quality. Innovations such as EquipmentCloud are at the forefront, revolutionizing the sector with cutting-edge solutions.
The impact of Industry 4.0 on wafer fabrication can be summarized in several key areas:
- Enhanced efficiency: By leveraging the power of smart factories, wafer production can achieve unprecedented levels of efficiency.
- Improved quality standards: Advanced monitoring and control systems ensure that the highest quality standards are consistently met.
- Agility and flexibility: Industry 4.0 enables manufacturers to quickly adapt to changing market demands and technology advancements.
In conclusion, the transition to Industry 4.0 technologies is not just an upgrade; it’s a transformative shift that will enable wafer producers to meet the challenges of the future head-on. With solutions like EquipmentCloud paving the way, the industry is well-positioned to embrace these changes and set new benchmarks for production excellence.
Conclusion
In summary, the advancements in modern wafer production have led to remarkable improvements in efficiency and output quality. The integration of cutting-edge technologies and innovative manufacturing processes has not only accelerated production times but also enhanced the precision and consistency of semiconductor wafers. As the demand for smaller, more powerful electronic devices continues to grow, the semiconductor industry’s commitment to continuous improvement and investment in research and development is critical. The future of wafer production looks promising, with ongoing efforts to minimize defects, reduce costs, and improve the sustainability of manufacturing practices. The strides made in this field are a testament to the relentless pursuit of excellence and the pivotal role of semiconductors in shaping the technological landscape.
Frequently Asked Questions
What are 3D transistors, and how do they improve wafer production?
3D transistors, also known as FinFETs, are transistors that extend vertically from the plane of the wafer, allowing for more transistors to be placed on a chip. This design enhances performance and energy efficiency, leading to advancements in wafer production technology.
How have lithography techniques evolved in modern wafer production?
Advances in lithography, such as extreme ultraviolet (EUV) lithography, have allowed for the creation of smaller and more complex circuits on wafers. This has resulted in increased circuit density and improved performance of semiconductor devices.
What role does high-purity silicon play in wafer manufacturing?
High-purity silicon is crucial for the production of quality wafers as it ensures fewer defects and higher performance in semiconductor devices. Achieving new standards of purity has been a significant focus in modern wafer production.
In what ways has automation impacted the efficiency of wafer production?
Automation and robotics have greatly increased the efficiency and consistency of wafer production processes. Through the use of Robotic Process Automation (RPA) and industrial robots, manufacturers can achieve enhanced precision and reduced human error.
How is the wafer production industry addressing sustainability concerns?
The industry is focusing on reducing its carbon footprint by adopting renewable energy sources, recycling and reclaiming silicon materials, and implementing energy-efficient production technologies to minimize environmental impact.
What future technologies are anticipated to revolutionize wafer production?
Technologies such as nanotechnology, advanced materials beyond silicon, and the principles of Industry 4.0 are expected to bring about significant changes in wafer production, leading to further improvements in efficiency and performance.