Navigating the Market: How Wafer Services are Shaping the Future of Chip Manufacturing
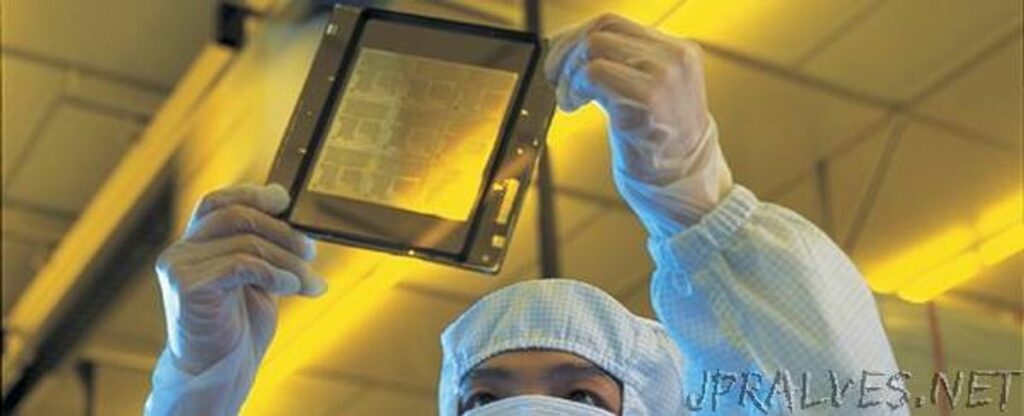
The semiconductor industry is at a crossroads as it grapples with the wafer supply dilemma, surging demand, international policies, the quest for self-sufficiency, and packaging innovations. This article delves into the complexities of chip manufacturing, highlighting how wafer services are playing a pivotal role in shaping the industry’s future.
Key Takeaways
- The wafer supply shortage, particularly for 300mm wafers, is expected to persist, impacting the semiconductor industry’s ability to meet rising demand.
- Cost control remains a significant challenge for the semiconductor industry, despite new markets and the demand for more complex chips driving growth.
- International collaboration and policies, such as the US’ FABS and CHIPS act, are becoming increasingly critical in the strategic planning of semiconductor manufacturing.
- Investments in domestic chip production are being prioritized globally, with significant financial implications for creating independent supply chains.
- Advanced semiconductor packaging faces challenges such as warpage and thermal mismatch, even as innovations like chiplets gain traction in applications like automotive.
The Wafer Supply Dilemma: Current State and Future Projections
Improving the 300mm Wafer Shortage
The semiconductor industry is witnessing a significant imbalance in the supply chain for 300mm wafers. With demand consistently outpacing the ability of suppliers to keep up, shortages are expected to persist for the foreseeable future. However, there are signs of improvement on the horizon. Key suppliers, such as Sumco Corp., have sold out their production capacity through 2026, indicating a robust pipeline that could eventually meet the growing needs of the industry.
Efforts to mitigate the shortage are multifaceted, involving the ramp-up of production and the introduction of new manufacturing projects. For instance, Chinese chip manufacturers are forecast to start operations of 18 projects in 2024, which could significantly increase China’s share in the global semiconductor production. This expansion is not without its challenges, as geopolitical tensions and legislation like the US’ FABS and CHIPS act influence the market dynamics.
The shortage has also spurred innovation in wafer fabrication, with a focus on enhancing the yield of ultra-thin wafers during back-end-of-line processing. This is crucial for the industry’s ability to supply complex chips for new end markets, which continue to drive demand. As the industry navigates these challenges, the hope is for a gradual return to normalcy, with some industry leaders like Bosch’s CEO optimistic about easing shortages by 2023.
Persistent Challenges with 200mm Wafers
Despite improvements in the supply of 300mm wafers, the industry continues to grapple with the persistent challenges associated with 200mm wafers. The demand for these wafers often outstrips supply, leading to a bottleneck that can affect the entire semiconductor manufacturing process. This imbalance is not expected to resolve in the near future, as suppliers struggle to keep pace with the industry’s needs.
The issues with 200mm wafers are multifaceted, involving both technical and logistical hurdles. Technical challenges include the warpage of wafers and packages, which is particularly problematic for high-integration (HI), 3D HI, and Chiplet-based architectures. These issues are exacerbated by thermal mismatches among different materials, potentially leading to interconnect misalignment, reduced bonding efficiency, and long-term reliability concerns. Logistical challenges, on the other hand, stem from the global supply chain dynamics, where geopolitical tensions and legislation such as the US’ FABS and CHIPS act influence market availability.
To address these challenges, the industry must adopt a multidisciplinary approach, focusing on both the refinement of manufacturing processes and the stabilization of supply chains. The table below summarizes the key challenges and potential solutions for 200mm wafer manufacturing:
Challenge | Potential Solution |
---|---|
Wafer and package warpage | Enhanced material selection and process optimization |
Thermal mismatch | Advanced thermal management techniques |
Supply chain imbalance | Diversification of suppliers and strategic stockpiling |
As the semiconductor industry evolves, it is crucial to not only innovate but also to ensure the robustness and reliability of foundational components like 200mm wafers.
Global Supply Chain Dynamics and Impacts
The global supply chain is facing a period of significant upheaval. Recent events have highlighted the fragility of the current system, with the Covid-19 pandemic, geopolitical tensions, and trade disputes leading to widespread disruptions. These challenges have underscored the need for a more resilient supply chain, capable of withstanding a variety of shocks.
Key factors impacting the supply chain include:
- Geopolitical risks in Asia and trade frictions, particularly involving China, have led to a reevaluation of dependency on single-source regions.
- The pandemic has transformed the workforce, leading to labor shortages and a shift in the logistics landscape.
- New policies and regulations are altering the playing field for international trade, with countries like the US, Japan, and the Netherlands implementing chip controls on China.
The semiconductor supply chain update provides an overview on how geopolitics, national security, and government incentives are impacting the market. This has resulted in a push for onshoring key supply links and a reconsideration of global dependencies. As the situation evolves, it is clear that the supply chain crisis is not only persisting but in some aspects, intensifying.
Demand Surge and Cost Control: The Semiconductor Industry’s Balancing Act
New Markets Fueling Demand for Advanced Chips
The semiconductor industry is witnessing a significant surge in demand, driven by new markets that require advanced chip technologies. The global market for semiconductors is projected to reach $1 trillion by 2030, up from $600 billion in 2021, indicating a thriving market that encourages expansion. This growth is not only fueled by traditional computing and mobile devices but also by emerging sectors such as electric vehicles (EVs), Internet of Things (IoT) devices, and artificial intelligence (AI) applications.
Investments in semiconductor infrastructure are booming as countries and companies vie for supply chain security and technology leadership. The push for innovation is leading to collaboration among big chip companies, recognizing the need for earlier cooperation as complexity rises for advanced nodes and packages. Here’s a snapshot of the recent investment trends:
- Americas: Sales increased by 43.2% year-to-year in February.
- China: Chinese EV makers are venturing into semiconductor and battery production.
- Global: Governments are accelerating chip investments for economic competitiveness.
These developments underscore the critical role of semiconductors as the new oil, with nations spending billions to safeguard their supply. As the industry grapples with the rising price of power in chips and the challenges of cost control, the future landscape of chip manufacturing will undoubtedly be shaped by these new market demands.
The Struggle to Keep Semiconductor Costs Down
As the semiconductor industry experiences a boom, with projections of reaching $1 trillion in yearly revenues by 2030, the pressure to expand manufacturing capabilities while controlling costs is immense. Building new facilities is a costly endeavor, particularly in the United States where it can be 25 to 50 percent more expensive than in other countries, due to a lack of manufacturing incentives. This cost disparity is driving a global competition for the establishment of semiconductor fabs, with nations like the UK stepping in to subsidize domestic chip production.
To address these challenges, the industry is exploring various strategies for cost reduction. Process optimization and waste reduction are key areas where digital transformation can lead to significant cost savings. Additionally, advancements in technology, such as the development of thinner semiconductor channels and more cost-effective electron sources, are contributing to the reduction of manufacturing expenses. However, these innovations must be balanced against the need for quality and performance, ensuring that cost-cutting measures do not compromise the integrity of the final product.
Here are some key areas of focus for cost control in semiconductor manufacturing:
- Process Optimization: Implementing lean manufacturing principles to reduce waste and improve efficiency.
- Advanced Materials: Exploring new materials like 2D semiconductors that offer better performance at reduced thicknesses.
- Government Subsidies: Leveraging state-backed initiatives to offset the high costs of building and operating fabs.
- Technology Innovation: Investing in research to discover breakthroughs that can lower the costs of critical components.
The Role of Industry 4.0 in Streamlining Chip Manufacturing
The semiconductor industry is undergoing a transformative phase with the integration of Industry 4.0 technologies. These advancements are not only enhancing productivity but also enabling manufacturers to achieve higher precision and lower operating costs. The adoption of smart manufacturing practices, such as ‘lights out’ manufacturing, is a testament to the industry’s commitment to innovation and sustainability.
Key benefits of Industry 4.0 in chip manufacturing include:
- Increased efficiency through automation and data analytics
- Improved yield and quality control with advanced monitoring systems
- Reduction in environmental impact due to optimized resource usage
The amalgamation of Fab Automation and Industry 4.0 is reshaping semiconductor manufacturing, fostering unprecedented levels of efficiency and precision. As the industry grapples with complex processes and the demand for more powerful semiconductors, leveraging data effectively has become crucial. This data-driven approach not only improves the productivity of design teams but also enhances the reliability of systems in the field.
International Policies and Collaborations in Chip Manufacturing
US and Allies Developing Joint Semiconductor Strategies
In response to the ever-growing importance of semiconductors in the global economy, the United States is spearheading efforts to form strategic alliances with key allies. This initiative, often compared to an OPEC-style cartel for the digital age, aims to consolidate various aspects of the semiconductor industry, from research and development to sales. The proposed ‘Chip 4 Alliance‘ is a testament to this strategy, seeking to internalize the entire semiconductor business within the coalition.
The significance of such collaborations is underscored by the U.S. semiconductor industry’s reliance on overseas markets, which account for over 80% of its sales. These revenues are crucial for funding the research and development necessary to maintain a competitive edge. Moreover, the U.S. has been actively working with international partners to develop cohesive semiconductor policies, further emphasizing the need for a unified approach in this sector.
Here is a snapshot of the recent investments and collaborations in the semiconductor industry:
- U.S. Investments in Chips: Triggering an investment boom with over 40 projects and close to $200 billion in total investments.
- EU’s Chip Subsidy Plan: A 43 billion euro initiative to bolster its semiconductor industry and compete globally.
- China’s Expansion: Guangdong province announces 40 new semiconductor projects valued at US$74 billion.
China’s Stance on Global Semiconductor Legislation
China’s position on global semiconductor legislation is intricately linked to its strategic interests in maintaining and expanding its role in the semiconductor industry. The Chinese government has expressed opposition to bills aimed at bolstering U.S. semiconductor manufacturing, viewing them as a threat to its competitive edge. The U.S. Commerce Secretary Gina Raimondo highlighted that such legislation would enhance the U.S.’s competitive position, a sentiment echoed by industry experts who note the decline of U.S. global semiconductor production from 37% to 12% over the past decades.
The Semiconductor Industry Association (SIA) has pointed out the importance of the Chinese market, which is the largest for semiconductors globally. Access to this market is deemed crucial for any globally competitive chip firm. However, the ongoing escalation of controls and the push for tech self-sufficiency in China pose significant risks to the global competitiveness of the U.S. semiconductor industry.
Country | % Global Semiconductor Production (1990) | % Global Semiconductor Production (Now) |
---|---|---|
U.S. | 37% | 12% |
As international policies evolve, the semiconductor landscape continues to be shaped by these geopolitical tensions and the strategic moves of major players.
The Importance of Early Vendor Cooperation in Advanced Manufacturing
In the rapidly evolving landscape of chip manufacturing, early vendor cooperation has emerged as a critical factor for success. Strategic partnerships, like the one between TSMC and ADI, underscore the growing necessity for alliances in addressing the complexities of advanced manufacturing. These collaborations not only tackle the immediate challenges of rising demand and technological intricacies but also build a resilient framework to withstand supply chain disruptions.
The benefits of such cooperation extend beyond mere risk mitigation. By sharing data and resources, companies can predict and avoid potential failures, especially in high-stakes sectors like automotive chips. Moreover, the integration of Industry 4.0 solutions within OSAT and wafer fabs, facilitated by these partnerships, paves the way for smarter manufacturing processes. This not only enhances efficiency but also contributes to a more robust global supply chain, as evidenced by the concerted efforts of the US and its allies in developing semiconductor policies.
To illustrate the impact of early vendor cooperation, consider the following table highlighting key aspects of strategic partnerships in the semiconductor industry:
Aspect | Benefit |
---|---|
Risk Mitigation | Enhanced resilience against disruptions |
Technological Advancement | Shared expertise for complex node development |
Efficiency | Streamlined processes through Industry 4.0 integration |
Policy Alignment | Coordinated efforts in international legislation |
As the industry continues to navigate the market’s complexities, the role of early vendor cooperation will only grow in significance, shaping the future of chip manufacturing.
Investing in Semiconductor Self-Sufficiency: A Global Perspective
The Drive for Domestic Chip Production in the US and UK
The push for domestic chip production in the US and UK is gaining momentum as both nations seek to reclaim a larger share of the semiconductor manufacturing market. The decline from a 37% global production share in the 1990s to a current 12% in the US has sounded alarms, with projections suggesting a further slip to 10% without intervention. This trend underscores the urgency for domestic revitalization efforts.
Subsidies have emerged as a critical tool in this endeavor. The Biden administration’s pledge of $1.5 billion in grants to GlobalFoundries is a testament to the government’s commitment to bolstering the semiconductor industry. However, significant hurdles remain, including the high costs of establishing new fabs and ensuring global competitiveness.
The UK, mirroring the US’s concerns, is also exploring avenues to enhance its semiconductor capabilities. Both countries recognize the strategic importance of semiconductors in economic strength, job creation, national security, and critical infrastructure. As such, the drive for self-sufficiency is not just an economic imperative but a strategic one.
Analyzing the Costs of Creating Independent Supply Chains
The quest for semiconductor self-sufficiency is marked by the staggering costs associated with establishing independent supply chains. Industry officials highlight that the price tag for leading-edge fabrication plants (fabs) can soar above $30 billion, a figure comparable to the cost of multiple aircraft carriers. This financial burden is a significant factor for nations considering the decoupling of their supply chains from global dependencies, particularly those linked to China.
The economic implications of such a strategic shift are multifaceted. On one hand, the investment in domestic chip production is seen as a necessary step towards ensuring national security and technological sovereignty. On the other hand, the sheer scale of the investment required raises questions about the viability and sustainability of these initiatives. The table below outlines the estimated costs and considerations for establishing a semiconductor fab:
Factor | Cost Estimate | Consideration |
---|---|---|
Construction | $5B – $20B | Facility complexity and location |
Equipment | Up to $10B | Advanced machinery and technology |
R&D | Several billion | Continuous innovation and development |
Workforce | Significant | Skilled labor and training |
As nations grapple with these challenges, the global effort to create independent supply chains continues to gain momentum, driven by the recognition of the incredible cost of chip manufacturing facilities and the strategic importance of the semiconductor industry.
State-Backed Initiatives and the Pivot to Mature Chip Nodes
In the quest for semiconductor self-sufficiency, massive state support has become a cornerstone of national strategies. Governments are funneling resources into the sector, recognizing the strategic importance of having a robust domestic chip industry. This support often manifests in the form of export controls, research funding, and incentives for local manufacturing.
The pivot to mature chip nodes is a strategic move to alleviate some of the pressures from the cutting-edge semiconductor market. By focusing on established technologies, countries can more quickly ramp up production and meet immediate demands. This approach also serves to balance the ledger, ensuring that investments in advanced nodes do not overshadow the need for a stable supply of more traditional chip technologies.
The following table outlines some of the key state-backed initiatives aimed at bolstering domestic chip production:
Country | Initiative | Focus Area |
---|---|---|
USA | Infrastructure Plan | Advanced Packaging |
UK | Research Funding | Chiplet IP Standards |
These initiatives are part of a broader trend where the National Integrated Circuit and other entities are playing a pivotal role in shaping the future of the semiconductor industry.
Innovations and Challenges in Advanced Semiconductor Packaging
Emerging Technologies in OSAT and Wafer Fabrication
The landscape of Outsourced Semiconductor Assembly and Test services (OSAT) is rapidly evolving to meet the demands of a dynamic semiconductor industry. OSAT suppliers are pivotal in conducting assembly and testing for semiconductor businesses, offering cost savings and expedited delivery. This collaboration is increasingly important as companies seek specialized OSAT capabilities to navigate the complexities of advanced packaging.
In the realm of wafer fabrication, the adoption of Industry 4.0 technologies is gaining traction. Wafer fabs are investing in smart manufacturing solutions to enhance efficiency and reduce operational costs. The integration of these technologies is not without its challenges, as it requires a strategic approach to evaluate various options and align them with long-term goals.
One of the notable advancements in wafer fabrication is the development of ultra-thin wafers, which are crucial during the back-end-of-line processing. These wafers contribute to increased final device yield, marking a significant step forward in semiconductor manufacturing efficiency.
Addressing Advanced Packaging Issues: Warpage and Thermal Mismatch
The integration of heterogeneous materials in advanced semiconductor packaging often leads to warpage and thermal mismatch, which are critical issues that can affect the performance and reliability of the final product. These challenges are particularly pronounced in high-integration architectures such as HI, 3D HI, and Chiplet-based systems. The mismatch in coefficients of thermal expansion (CTE) among different materials can cause significant stress during thermal cycling, leading to misalignment and reduced bonding efficiency.
To combat these issues, industry leaders are turning to innovative metrology systems like the Wave3000 developed by ERS Electronic GmbH. This system utilizes advanced optical sensors to measure wafer warpage with high precision. By integrating such systems into the manufacturing line, continuous monitoring can be achieved, allowing for dynamic adjustments to process parameters. This proactive approach helps to mitigate the risk of warpage and ensures that only wafers meeting strict flatness criteria proceed to subsequent processing steps, thus safeguarding the integrity of the chips.
The table below summarizes the impact of warpage on different aspects of semiconductor packaging:
Aspect | Impact of Warpage |
---|---|
Interconnect Alignment | Potential misalignment leading to signal integrity issues |
Bonding Efficiency | Reduced efficiency and long-term reliability concerns |
Performance | Degraded performance due to structural stress |
Addressing the thermal challenge in heterogeneous integration requires a multidisciplinary approach, involving material scientists and engineers to select materials with compatible CTEs and develop processes that minimize thermal stress.
The Evolution of Chiplets and Their Role in Automotive Applications
The automotive industry is on the cusp of a significant transformation, with chiplets emerging as a pivotal technology. These modular components are revolutionizing how semiconductors are designed and integrated, offering a versatile and cost-effective alternative to traditional monolithic chips. As vehicles become more reliant on advanced electronics for features like autonomous driving and connectivity, the adoption of chiplets allows for greater flexibility and scalability in automotive systems.
Despite the promise of chiplets, their journey to mainstream adoption is not without obstacles. Industry standards for data and protocol interoperability are still in development, which is crucial for ensuring seamless integration of chiplets from different vendors. Moreover, the automotive sector’s stringent requirements for reliability and durability necessitate customized chiplets, especially for AI applications, adding another layer of complexity to their deployment.
The table below outlines the current state of chiplet integration in the automotive industry, highlighting the benefits and challenges faced:
Aspect | Benefits | Challenges |
---|---|---|
Design Flexibility | Modular, scalable architectures | Need for industry-wide standards |
Cost Efficiency | Reduced development costs | Customization for specific needs |
Performance | Enhanced computational power | Ensuring long-term reliability |
Integration | Easier system upgrades | Compatibility with existing systems |
As the industry navigates these challenges, the role of chiplets in automotive applications is poised to grow, driving innovation and efficiency in chip manufacturing.
Conclusion
As we navigate the complexities of the semiconductor market, it’s evident that wafer services are playing a pivotal role in shaping the future of chip manufacturing. The industry faces significant challenges, including a persistent wafer shortage, particularly for 200mm wafers, and the escalating demand for more complex chips. Despite these hurdles, advancements in Industry 4.0, strategic collaborations, and substantial investments in semiconductor fabs signal a transformative era for chip production. The global landscape is shifting, with countries like the United States taking decisive action to reclaim a larger share of chip manufacturing and secure supply chains. While the road ahead is fraught with both obstacles and opportunities, the concerted efforts of industry leaders, policymakers, and innovators suggest a resilient and dynamic future for semiconductor manufacturing.
Frequently Asked Questions
What is causing the current wafer shortage, particularly for 300mm and 200mm sizes?
The wafer shortage is primarily due to demand outpacing the wafer suppliers’ ability to produce, with the 300mm size seeing some improvement in sight, but the 200mm shortage expected to last for years.
How are new markets impacting the demand for advanced semiconductor chips?
New markets are significantly increasing the demand for complex chips, which contributes to the growth outlook for integrated circuits (ICs) and challenges in controlling manufacturing costs.
What is the significance of the US’ FABS and CHIPS Act and why does China oppose it?
The FABS and CHIPS Act is aimed at bolstering the semiconductor industry in the US, which China opposes due to concerns over global semiconductor legislation and its impact on their market.
How is Industry 4.0 technology influencing semiconductor manufacturing efficiency?
Industry 4.0 technology is being adopted by OSAT and wafer fabs to improve efficiency and reduce operating costs, though it requires careful planning to evaluate various options and goals.
What are some of the challenges faced in advanced semiconductor packaging?
Advanced semiconductor packaging faces challenges such as warpage, thermal mismatch, heterogeneous integration, and the need for thinner lines and spaces.
Why is there a push for domestic chip production in countries like the US and UK?
There’s a push for domestic chip production to ensure semiconductor self-sufficiency and to safeguard against supply chain disruptions, as evidenced by significant investments from these governments.