Enhancing Efficiency: The Rise of Industrial Automation Systems
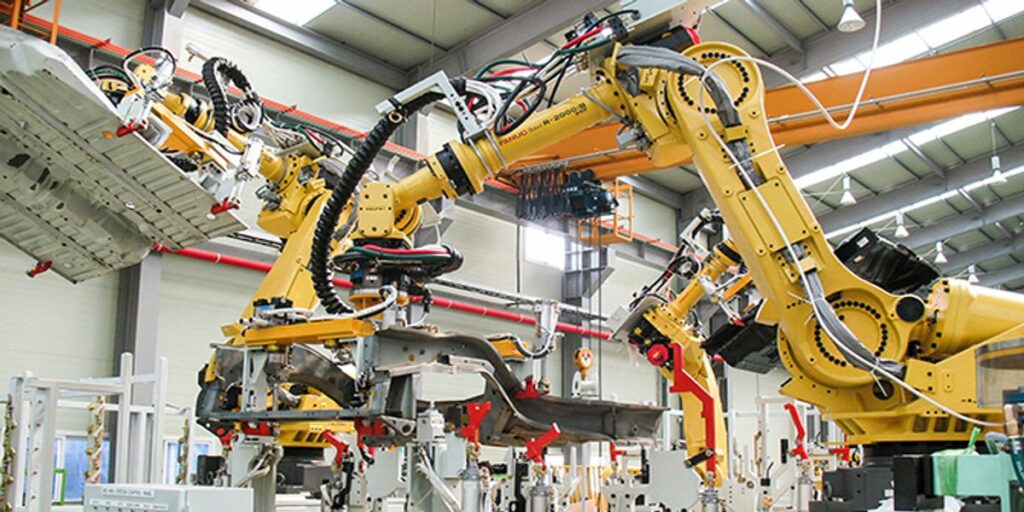
The article ‘Enhancing Efficiency: The Rise of Industrial Automation Systems’ delves into the transformative effects of automation in the industrial sector. It explores the progression from manual labor to the use of sophisticated robotics, the integration of network virtualization, and the advent of smart manufacturing. The narrative also sheds light on the myriad benefits of industrial automation, such as improved safety, efficiency, and decision-making, as well as the concept of hyperautomation and its influence on competitive dynamics. Furthermore, the article examines the varied impacts of automation across different industry sectors and discusses the challenges and opportunities it presents, including employment transformation and sustainability considerations.
Key Takeaways
- Industrial automation has evolved from manual labor to advanced robotics, highlighting a shift towards more sophisticated and intelligent manufacturing processes.
- Automation enhances safety with sensors that detect hazards, increases efficiency through automated processes, and boosts productivity with predictive maintenance and process control.
- Hyperautomation extends beyond traditional automation by integrating advanced technologies like AI, offering a competitive edge to industries that adopt it.
- The impact of automation varies across sectors, with significant benefits in productivity and efficiency, especially in agriculture and manufacturing.
- While automation presents opportunities for cost savings and environmental benefits, it also poses challenges in balancing human cognition and job transformation.
The Evolution of Industrial Automation
From Manual Labor to Advanced Robotics
The transition from manual labor to advanced robotics marks a significant milestone in the evolution of industrial automation. Robotic systems have become integral to manufacturing, enhancing output efficiency, reducing costs, and elevating product quality. These systems are designed to imitate human behaviors, perform intricate tasks with high precision, and adapt to critical situations with the aid of machine learning algorithms.
The adoption of robotic process automation (RPA), artificial intelligence (AI), and intelligent process automation (IPA) has transformed the manufacturing landscape. Here’s how these technologies have impacted the industry:
- RPA: Streamlines processes by automating repetitive tasks, freeing up human workers for more complex roles.
- AI: Enhances decision-making and predictive capabilities, leading to smarter and more efficient operations.
- IPA: Combines elements of RPA and AI to create systems that can learn and improve over time.
Despite the clear benefits, the uptake of automation technologies varies across sectors, with larger and more technologically advanced firms leading the way. The shift towards automation not only boosts productivity but also redefines the nature of employment, transitioning roles from manual to more strategic and analytical positions.
The Role of Network Virtualization and Machine Miniaturization
The advent of network virtualization and machine miniaturization has been a game-changer in the realm of industrial automation. These technologies have enabled the creation of more compact, efficient, and flexible manufacturing systems. Network virtualization allows for the seamless integration of various devices and systems, leading to improved communication and coordination across the manufacturing floor.
Machine miniaturization, on the other hand, has been propelled by advancements in nanotechnology, particularly through the development of silicon nanowires. These tiny yet powerful components are revolutionizing the design of integrated circuits and sensors, contributing to the creation of future-generation actuators and inertial sensors. The recent breakthroughs in monolithic fabrication of nanowires are particularly noteworthy, as they simplify the manufacturing process and reduce both the complexity and temperature requirements.
The table below outlines the impact of these innovations on the manufacturing process:
Innovation | Impact on Manufacturing Process |
---|---|
Network Virtualization | Enhanced communication and system integration |
Machine Miniaturization | Reduced size and increased functionality of devices |
As we continue to push the boundaries of what’s possible with industrial automation, these advancements are setting the stage for a new era of smart manufacturing, where efficiency and productivity reach unprecedented levels.
Industrial Intelligence: A New Era of Smart Manufacturing
The advent of industrial intelligence marks a transformative phase in manufacturing, where the convergence of advanced technologies is reshaping production landscapes. Automation technologies, including intelligent, integrated, and flexible systems, are now pivotal in mechanical manufacturing for enhancing industry competitiveness. These systems are not only revolutionizing product processing and assembly but also refining information systems and supply chain management.
The integration of Industry 4.0 technologies such as cloud technology, the Internet of Things (IoT), and Big Data is propelling manufacturing into a new era of efficiency and sustainability. ERP systems, now aligned with sustainability management, are reducing the need for extensive data collection from various sources for Life Cycle Assessment (LCA), thereby streamlining environmental impact assessments.
As we witness the rise of smart manufacturing, a recent New State of Smart Manufacturing Study underscores the significant impact of artificial intelligence in empowering the workforce and bolstering operational resilience. The study highlights the deployment of AI as a means to provide the workforce with ‘superpowers’, enabling them to perform tasks with unprecedented precision and efficiency.
Key Advantages of Industrial Automation
Enhanced Safety through Advanced Sensing Technologies
The integration of advanced sensing technologies in industrial automation has significantly elevated workplace safety. Sensors capable of detecting potential hazards provide real-time alerts, allowing for immediate response to prevent accidents. This proactive approach to safety is a cornerstone of modern automated systems.
Advanced sensors not only detect immediate threats but also contribute to a broader safety culture by monitoring environmental conditions and equipment performance. This continuous surveillance ensures that any deviation from the norm can be addressed swiftly, often before it poses a real danger.
Key benefits of advanced sensing technologies include:
- Real-time hazard detection and alerts
- Monitoring of environmental conditions
- Enhanced equipment performance tracking
- Support for predictive maintenance strategies
The development of new sensor fabrication techniques compatible with semiconductor manufacturing is crucial for further advancements. This will enable the creation of more sophisticated sensors, which can integrate multiple functionalities and further enhance safety measures in industrial settings.
Boosting Efficiency with Automated Processes
The integration of automation technologies in manufacturing has revolutionized the way industries operate, leading to a substantial increase in efficiency and productivity. Automation allows for the consistent execution of tasks with high precision, significantly reducing the likelihood of human error and the variability associated with manual processes.
In the realm of agriculture, for instance, the implementation of automation has been pivotal in enhancing technical efficiency, particularly on dairy farms. The use of automated technologies such as cluster removers and scrapers has shown to improve efficiency on smaller farms, while larger operations benefit from automated parlour feeders.
The following table illustrates the impact of automation on productivity and cost-effectiveness across different sectors:
Sector | Productivity Increase | Cost-effectiveness |
---|---|---|
Agriculture | High | Moderate |
Manufacturing | Very High | High |
Automation not only accelerates production processes and reduces labor-intensive tasks but also plays a critical role in the strategic application of machinery. This leads to a streamlined production process, ultimately enhancing the overall competitiveness of businesses.
Productivity Gains from Predictive Maintenance and Process Control
The integration of predictive maintenance and process control within industrial automation systems has led to significant productivity gains. By anticipating equipment failures before they occur, businesses can schedule maintenance activities during non-peak hours, minimizing downtime and maintaining a steady flow of operations.
Predictive maintenance leverages data analytics to monitor the condition of equipment and predict when maintenance should be performed. This approach not only extends the lifespan of machinery but also optimizes the use of resources. Here’s how predictive maintenance contributes to productivity:
- Maximizes equipment uptime: Ensures machinery is operational when needed.
- Improves operational efficiency: Streamlines processes by reducing unexpected breakdowns.
- Reduces maintenance expenses: Prevents costly repairs and extends equipment life.
- Facilitates informed decision-making: Data analysis allows for better planning and resource allocation.
Process control further enhances these benefits by ensuring that manufacturing processes remain within specified parameters, leading to consistent quality and reduced waste. Together, these technologies form a powerful duo that revolutionizes industrial operations, providing safety, efficiency, and cost savings.
Cost Reduction and Energy Management
Industrial automation systems are pivotal in achieving significant cost savings and enhancing energy efficiency. By integrating technologies such as predictive maintenance and process control, industries can minimize energy consumption and reduce operational costs, making these systems more efficient and cost-effective than traditional methods. The synergy between automation and energy management not only lowers expenses but also supports sustainability goals.
The implementation of Enterprise Resource Planning (ERP) systems during Industry 4.0 has further streamlined cost reduction and energy management. These systems, when aligned with sustainability management, can significantly impact environmental and social outcomes. For instance, ERP systems facilitate the collection and analysis of data for Life Cycle Assessment (LCA), which is crucial for improving operational efficiency and achieving sustainability targets.
Here is a brief overview of the impact of automation on cost and energy management:
- Reduction in Wastage: Automation leads to more precise control and less material waste.
- Labor Cost Savings: Automated processes reduce the need for manual labor, cutting labor costs.
- Energy Efficiency: Smart systems optimize energy use, leading to lower utility bills.
- Real-time Data Analysis: Enables informed decision-making for cost and energy savings.
- Sustainability: Aligns with corporate sustainability goals through efficient resource utilization.
Data-Driven Decision Making and Real-Time Analysis
The integration of real-time analysis and data-driven decision making into industrial automation systems marks a significant leap forward in operational efficiency. By leveraging the power of real-time data, companies can make informed decisions swiftly, ensuring that production processes are optimized and potential issues are addressed before they escalate.
Key components of this approach include the MAPE-K (Monitor, Analyze, Plan, Execute over a shared Knowledge) framework, which is instrumental in enhancing the autonomy of Cyber-Physical Systems. This framework is particularly effective when combined with Digital Twins, enabling a reflective middleware architecture that supports fault diagnosis and process adjustments on the fly.
The benefits of such systems are manifold, as outlined below:
- Enhanced safety by predicting potential dangers and allowing workers to focus on more complex tasks.
- Increased efficiency through the automation of key processes such as predictive maintenance and process control.
- Cost savings by reducing energy consumption and streamlining the chemical risk assessment process.
- Harmonization of processes through the development of automated software tools, expediting safety assessments.
Hyperautomation: Beyond Traditional Automation
The Concept and Drivers of Hyperautomation
Hyperautomation represents the next leap in the evolution of automation, where advanced technologies such as artificial intelligence (AI), machine learning (ML), robotic process automation (RPA), and intelligent process automation (IPA) converge to automate complex business processes. This approach extends beyond traditional automation by not only performing predefined tasks but also by learning and adapting to new scenarios without human intervention.
The drivers of hyperautomation are multifaceted, encompassing the need for greater efficiency, innovation, and growth within industries. Businesses are increasingly seeking to automate every imaginable function to enhance productivity, reduce labor-intensive tasks, and optimize manufacturing processes. The table below summarizes the core components of hyperautomation and their respective roles:
Component | Role in Hyperautomation |
---|---|
AI & ML | Enable systems to learn, adapt, and make decisions. |
RPA | Automate repetitive tasks and streamline workflows. |
IPA | Integrate AI capabilities to enhance RPA functionalities. |
As industries strive to remain competitive, the adoption of hyperautomation technologies is becoming a strategic imperative. These technologies not only improve the accuracy of business activities but also drive transformation by imitating human behaviors and executing a wide array of tasks with precision.
Transforming Manufacturing with Intelligent Automation
The integration of artificial intelligence in manufacturing is not just an incremental improvement; it’s a complete transformation. Employing algorithms to process data from sensors and human inputs, AI enables machines to make decisions and optimize processes in real-time. This shift towards intelligent automation is redefining the landscape of manufacturing, leading to unprecedented levels of productivity and efficiency.
Intelligent automation combines various technologies such as robotic process automation (RPA), intelligent process automation (IPA), and AI to imitate human behaviors and enhance industry competitiveness. These technologies are crucial for tasks that were once manual, now allowing for higher productivity and yield enhancement. The table below illustrates the impact of intelligent automation on key manufacturing metrics:
Metric | Before Automation | After Automation |
---|---|---|
Production Output | Low | High |
Operational Efficiency | Moderate | Significantly Improved |
Cost of Production | High | Reduced |
Employee Role Transformation | Repetitive Tasks | Top-tier Employment |
As intelligent automation becomes a cornerstone in modern manufacturing, companies that adopt these technologies not only streamline their processes but also gain a significant competitive edge. The result is a dynamic industry where automation solutions continuously evolve, pushing the boundaries of what’s possible in manufacturing.
The Competitive Edge: Hyperautomation in Industry
Hyperautomation represents the pinnacle of automation technology, integrating advanced tools like AI, machine learning, and robotics to transform the manufacturing landscape. Businesses that embrace hyperautomation gain a significant competitive edge, leveraging its potential to enhance efficiency, productivity, and precision.
In the realm of manufacturing, hyperautomation goes beyond traditional automation by not only imitating human actions but also making intelligent decisions. This shift is evident in the way hyperautomation is applied across various processes, from supply chain management to assembly lines. The table below showcases some of the top benefits of hyperautomation in the manufacturing industry:
Benefit | Description |
---|---|
Enhanced Efficiency | Streamlines processes and reduces time-consuming tasks. |
Improved Productivity | Increases output and accelerates production cycles. |
Cost Reduction | Minimizes expenses by optimizing resource utilization. |
Process Accuracy | Improves precision and reduces error rates. |
As industries strive to support market competition effectively, the role of hyperautomation becomes increasingly crucial. It not only reduces human workload but also augments human performance, leading to innovative automated services that can adapt to changing market demands.
Automation’s Impact on Industry Sectors
Revolutionizing Productivity and Efficiency Across Industries
The integration of industrial automation has been a game-changer for numerous sectors, dramatically enhancing productivity and efficiency. This transformation is evident in the way businesses now operate, with automation becoming a cornerstone for competitiveness in the digital economy.
In particular, the agriculture sector has seen remarkable improvements. Automation’s role in this industry is underscored by its ability to increase technical efficiency, especially on dairy farms where larger, more intensive operations have benefited significantly.
Manufacturing industries, too, have embraced various forms of automation, including Robotic Process Automation (RPA), Artificial Intelligence (AI), Intelligent Process Automation (IPA), and Hyperautomation. These technologies have been instrumental in reducing costs, streamlining processes, and imitating human behaviors to achieve superior outcomes.
The Crucial Role of Automation in Agriculture
In the realm of agriculture, automation has become a transformative force, enhancing the efficiency and productivity of farms. Automation augments the role of the farm worker, making daily tasks quicker to complete and far less labor-intensive. This shift not only streamlines operations but also allows for the optimization of resources such as water and soil nutrients.
The integration of AI, robotics, drones, and machine learning has given rise to precision agriculture. This approach utilizes data analytics and smart technologies to optimize crop yields and manage soil conditions effectively. For instance, automated irrigation systems are designed to optimize water usage, preventing excessive irrigation and thereby increasing plant productivity.
Here’s a glimpse of how automation impacts various aspects of agriculture:
- Precision in crop management: Predicting and implementing effective crop strategies.
- Efficiency in resource utilization: Smart farming with sensors and automated systems.
- Labor and cost reduction: Minimizing human intervention and optimizing production costs.
The potential for further automation looms on the horizon, promising even greater advancements in the agricultural sector.
Differential Adoption Rates: Factors Influencing Automation Uptake
The landscape of industrial automation is not uniform across sectors or even within them. Factors such as company size, age, and sector specificity play pivotal roles in the adoption of automation technologies. Larger and younger firms are often at the forefront, leveraging automation to enhance productivity and reshape workforce skill requirements. In contrast, smaller and more traditional businesses may lag, facing barriers to entry that include cost, complexity, and a lack of expertise.
In the realm of manufacturing, for instance, China has seen a surge in the use of intelligent technology and flexible automation to bolster the competitiveness of its mechanical manufacturing industry. Similarly, in agriculture, automation has been instrumental in improving technical efficiency, particularly on larger and more intensive farms.
The following table summarizes the influence of key factors on automation adoption rates:
Factor | Influence on Adoption |
---|---|
Company Size | Larger companies adopt more readily |
Company Age | Younger companies are quicker to adopt |
Sector | Manufacturing and agriculture show significant uptake |
Economic Factors | Cost-effectiveness and competitiveness drive adoption |
Technological Advancements | Availability of advanced technologies spurs adoption |
Understanding these factors is crucial for businesses aiming to stay competitive in an increasingly automated world. Tailoring automation strategies to the specific needs and capabilities of a company can help overcome adoption barriers and unlock the full potential of these transformative technologies.
Challenges and Opportunities in Industrial Automation
Balancing Automation with Human Cognition and Performance
The integration of automation in industries has been a double-edged sword. On one hand, it has reduced human workload and improved performance; on the other, it has introduced complexities in cognitive activities that can lead to errors. To harness the full potential of automation while maintaining human cognitive strengths, a delicate balance must be struck. This involves understanding the nuances of human cognition and designing systems that complement rather than replace human capabilities.
Experience from various industries has shown that automation can lead to human complacency and over-reliance on automated systems. To counteract this, knowledge on human cognition should be leveraged to design human-AI systems that require continuous human engagement and decision-making. This approach ensures that the human workforce remains an integral part of the automated environment, fostering a symbiotic relationship between humans and machines.
The table below illustrates the impact of automation on team dynamics and individual performance:
Factor | Impact of Automation |
---|---|
Team Performance | Decrease in overall performance, coordination failures |
Team Trust | Reduction in trust levels |
Individual Effort | Lower effort provision |
Worker Well-being | Mixed or negative impacts |
It is clear that while automation brings numerous benefits, it also poses challenges that need to be addressed. By designing systems that are aware of human cognitive limits and strengths, we can create a future where automation supports and enhances human work rather than undermining it.
The Future of Employment: Automation and Job Transformation
The rise of automation has been a double-edged sword for the employment market. On one hand, it has led to significant job growth and higher employment in certain sectors, particularly where automation complements human skills. However, it has also resulted in the displacement of workers, especially in roles characterized by routine and repetitive tasks. This shift has contributed to a decline in middle-skill jobs, pushing workers towards lower-skilled positions and increasing part-time employment, often involuntarily.
The impact of automation and AI on the labor market is multifaceted, affecting socioeconomic dynamics across various industries. While AI and automation have disrupted sectors by replacing human labor in some areas, they are still unable to replicate human qualities such as intuition and empathy. This leaves room for human advantage in the workforce. Nevertheless, the changing landscape requires workers to adapt and acquire new skills to stay relevant.
The table below illustrates the differential impact of automation on employment across various sectors:
Sector | Positive Impact | Negative Impact |
---|---|---|
Data Analysis | Increased demand for skilled labor | Displacement of routine jobs |
Robotics | Creation of specialized jobs | Reduction in manual labor roles |
Service Sector | Growth in local labor markets | Shift towards part-time employment |
Governments, companies, and individuals must work together to navigate these changes. Adaptation strategies include retraining programs, education reforms, and policies that support the transition into new roles within the evolving job market.
Sustainability and Environmental Benefits of Automation
The integration of industrial automation systems has proven to be a game-changer in achieving sustainability and environmental stewardship. By leveraging automation, industries can significantly reduce their carbon footprint, thanks to the efficient utilization of resources and lower emissions. This is not only beneficial for the environment but also aligns with the growing demand for eco-friendly practices in manufacturing.
Key environmental benefits include:
- Precision in resource management, leading to less waste
- Enhanced process safety and reduced risk of environmental hazards
- Improved energy efficiency, resulting in lower operational costs and conserving energy
As companies like Schneider Electric demonstrate, embracing innovative digital technologies is essential for industrial enterprises aiming to meet market needs while prioritizing sustainability. The move towards automation is a strategic response to the dual challenge of maintaining competitiveness and addressing ecological concerns.
Conclusion
The ascent of industrial automation systems marks a transformative era in manufacturing and various other industries. By integrating advanced technologies such as robotic systems, artificial intelligence, and process automation, businesses are achieving unprecedented levels of safety, efficiency, and productivity. The shift from manual labor to network virtualization, machine miniaturization, and industrial intelligence not only enhances competitiveness but also fosters a more sustainable approach through reduced energy consumption and emissions. As we have seen, the benefits of automation extend beyond mere cost savings to include improved process control, predictive maintenance, and data-driven decision-making. While the adoption rates vary across sectors and firm sizes, the trajectory is clear: industrial automation is revolutionizing operations and setting new benchmarks for performance. As industries continue to embrace these innovations, we can anticipate a future where automation is synonymous with advancement and where human roles evolve to meet the challenges of a hyper-automated world.
Frequently Asked Questions
What is the role of industrial automation in enhancing safety?
Industrial automation enhances safety by using advanced sensors to detect potential hazards and send real-time alerts, reducing the risk of accidents and injuries in the workplace.
How does industrial automation improve efficiency?
Automation improves efficiency by streamlining processes, allowing for quick responses to potential issues, and reducing the need for manual intervention, which speeds up production cycles.
In what ways does industrial automation contribute to productivity gains?
Productivity gains from industrial automation are achieved through predictive maintenance, process control, and efficient energy management, which ensure continuous and optimized production.
How does industrial automation affect energy consumption and costs?
Industrial automation reduces energy consumption and operational costs by optimizing processes and equipment usage, making it more efficient and cost-effective than traditional methods.
What is hyperautomation, and how is it transforming manufacturing?
Hyperautomation is the application of advanced technologies like AI and machine learning to further automate processes beyond traditional automation, transforming manufacturing with intelligent, integrated, and flexible systems.
What are the challenges and opportunities associated with industrial automation?
Challenges include balancing automation with human cognition and job transformation, while opportunities involve improving process safety, resource efficiency, and contributing to sustainability by lowering emissions.