The Evolving World of Semiconductor Electronics: Trends and Predictions
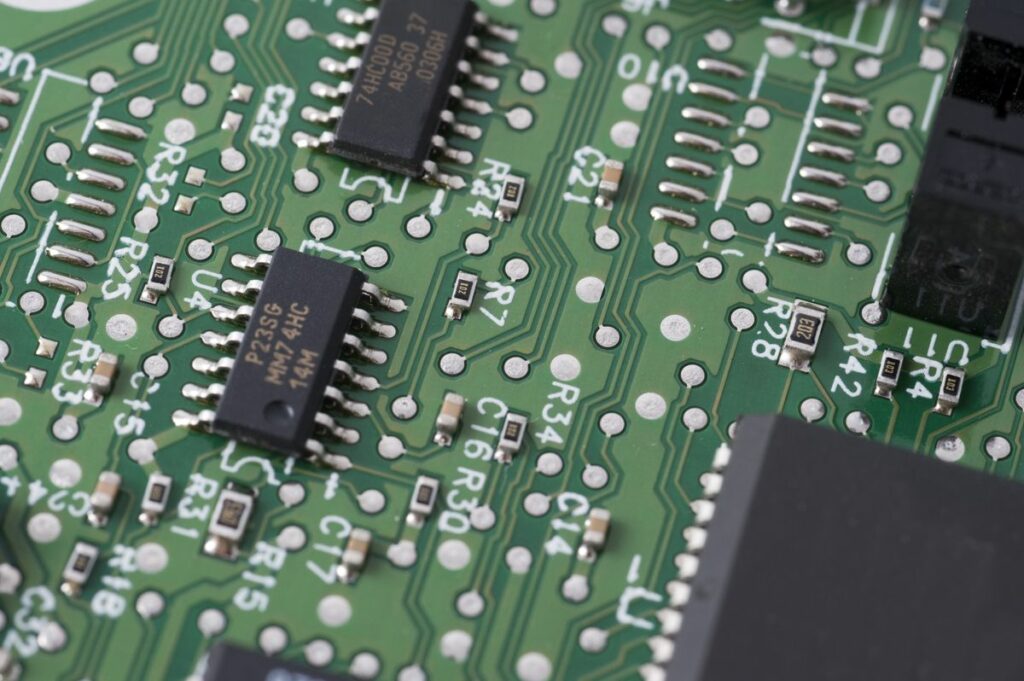
The semiconductor electronics landscape is rapidly evolving, driven by technological advancements, market dynamics, and global manufacturing trends. This article delves into the current state and future predictions of semiconductor electronics, exploring the shift towards localization in manufacturing, market growth opportunities, innovative trends, workforce and supply chain challenges, and the burgeoning markets for semiconductor plastics and wet chemicals. By understanding these elements, we can anticipate the directions in which the industry is headed and the implications for businesses and consumers alike.
Key Takeaways
- The semiconductor industry is experiencing a significant shift towards localization, with a focus on onshoring manufacturing facilities to enhance security and economic benefits.
- Silicon Carbide’s rise in the automotive sector and the increasing demand for electric vehicles are driving growth and innovation in semiconductor electronics.
- Advancements in lightweight and flexible electronics, as well as high-temperature performance materials like PPS, are setting new trends in the semiconductor landscape.
- The industry faces challenges such as a skilled labor shortage and supply chain disruptions, necessitating strategic workforce development and supply network redesign.
- The markets for semiconductor plastics and high-purity wet chemicals are expanding, with predictions of robust growth due to the rising demand for advanced electronics and smart technology.
Global Semiconductor Manufacturing: A Shift Towards Localization
The Onshoring Movement in High Tech Industries
The semiconductor industry is witnessing a significant shift with current investments in new or expanded fabrication plants (fabs), signaling a strong belief in the industry’s future. Onshoring and nearshoring are gaining traction as businesses and governments aim to diversify chip manufacturing locations to enhance supply chain resiliency. However, this move is not without its challenges, which include collaboration with various stakeholders, securing infrastructure and resources, and acquiring skilled semiconductor talent.
A key strategy for managing these challenges involves rethinking the supply network. A staggering 78% of supply chain and manufacturing executives express a preference for factories to be within four time zones of their customers. This proximity can lead to improved supply chain resilience and reduced risks. Additionally, the industry must address the growing talent gap and ensure that the onshoring of fabs does not exacerbate this issue.
To successfully onshore manufacturing operations, companies are advised to follow a four-step approach that includes engaging in partnerships, rethinking talent strategies, enabling security and technologies, and reassessing ROI expectations. With 60 new high-tech manufacturing sites projected to be upgraded or created in the US by 2024, the semiconductor industry is poised to undergo a transformative change, reshaping local talent pools and the global supply chain.
Challenges and Strategies for Localized Production
The push towards localizing semiconductor production is driven by the need for supply chain resiliency and risk reduction. According to industry insights, 78% of supply chain and manufacturing executives desire factories within four time zones of their customers. This shift is not without its challenges, such as the need for collaboration with public and private entities, securing infrastructure, and most notably, addressing the semiconductor worker shortage.
To overcome these obstacles, companies are rethinking their manufacturing capabilities. The integration of automation, machine learning, and scalable robotics is essential for modernizing production. Additionally, the use of digital twins and other emerging technologies can reimagine the fab floor, providing greater visibility and efficiency.
Strategic partnerships and investments are crucial for success in localized semiconductor manufacturing. The industry is expected to see 60 new or upgraded high-tech manufacturing sites in the US by 2024. This expansion will impact not only local talent but also the global supply chain, necessitating a redesign of the supply network to meet the evolving demands.
Rethinking ROI in the Context of Global Manufacturing
In the semiconductor industry, the traditional metrics for calculating return on investment (ROI) are being challenged by the new dynamics of global manufacturing. The shift towards localization is not just a response to geopolitical tensions and trade uncertainties; it’s a strategic move to bring production closer to end markets. This approach can lead to significant benefits, such as improved supply chain resilience and reduced transportation costs.
However, rethinking ROI involves considering a broader set of factors beyond immediate financial returns. For instance, the construction of new semiconductor manufacturing facilities, as reported by Sourcengine in March 2024, indicates a response to the previous year’s low consumer demand. Companies are now evaluating the long-term value of manufacturing flexibility, the ability to quickly adapt to market changes, and the importance of securing a stable supply chain.
To illustrate the evolving considerations for ROI in semiconductor manufacturing, here’s a snapshot of industry sentiments:
- 78% of supply chain and manufacturing executives prefer factories within 4 time zones of the customer.
- 60 new high-tech manufacturing sites are expected to be upgraded or created in the US by 2024.
These figures underscore the importance of proximity and the growing emphasis on local talent and supply chain implications. As the industry continues to adapt, ROI calculations will increasingly factor in these strategic elements to ensure long-term success and sustainability.
Market Dynamics and Growth Opportunities in Semiconductors
Silicon Carbide’s Rise in the Automotive Sector
The auto industry sees silicon carbide chips as key for EV push, recognizing their superior efficiency and heat resistance, which are critical for electric vehicles (EVs). An October 2023 report by McKinsey and Co. forecasts that global demand for silicon carbide across industries will grow to between $11 billion and $14 billion, highlighting the material’s importance in the automotive sector.
Silicon carbide’s adoption is driven by the need for advanced semiconductor components in EVs, which require sophisticated battery management and power electronics. The Asia-Pacific region, particularly China, is leading the charge with a compound annual growth rate (CAGR) of around 12%, fueled by economic growth and significant investments in electric and autonomous vehicle technologies.
However, the industry faces challenges such as a lack of skilled labor and a general shortage of semiconductors, which could hinder growth. Despite these restraints, key companies like Continental, DENSO CORPORATION, and Infineon Technologies are at the forefront of addressing these issues and pushing the boundaries of automotive semiconductor technology.
The Impact of Electric Vehicles on Semiconductor Demand
The surge in electric vehicle (EV) production is a major catalyst for the semiconductor industry’s expansion. As EVs gain traction, they necessitate a broad array of semiconductor components for functions such as battery management, power electronics, and motor control. These components are critical for the vehicles’ performance, energy efficiency, and overall user experience.
The automotive industry’s pivot towards electrification is not just a trend but a transformative movement. This shift is marked by a growing demand for advanced semiconductor technology to support features like autonomous driving, connectivity, and infotainment systems. The table below outlines some of the key semiconductor components and their applications in modern electric vehicles:
Component | Application in EVs |
---|---|
Power semiconductors | Motor drives, battery management |
Sensors | Monitoring vehicle status, safety features |
Microcontrollers | Powertrain control, energy management |
Connectivity modules | Telematics, vehicle-to-everything (V2X) communication |
However, this increased demand also presents challenges, such as the current global semiconductor shortage and the need for a skilled workforce to sustain growth. The industry must navigate these obstacles to meet the rising semiconductor requirements of the burgeoning EV market.
System-On-Chip (SoC) Usage and Market Expansion
The System-On-Chip (SoC) market is experiencing a significant surge, primarily driven by the growing demand for advanced electronic devices. SoCs, which integrate all components of a computer or other electronic system into a single chip, are becoming increasingly prevalent due to their efficiency and compact size.
Market opportunities are abundant, with trends indicating a strong adoption of SoCs across various sectors. Particularly, the automotive industry’s shift towards electric vehicles (EVs) and the development of autonomous vehicles are notable factors contributing to market growth. The integration of artificial intelligence (AI), machine learning (ML), and the Internet of Things (IoT) within automotive semiconductors further underscores the importance of advanced SoCs.
Despite the optimistic outlook, the market faces challenges such as a skilled labor shortage and a general semiconductor shortage, which could impede growth. However, the industry’s drive towards automation and AI in manufacturing processes is poised to counteract these restraints and propel the market forward.
According to a recent analysis, the SoC market is projected to reach a valuation of US$ 326.1 Billion by 2032, growing at a CAGR of 6.84% from 2024 to 2032. This growth trajectory highlights the expanding role of SoCs in the future of semiconductor electronics.
Innovations and Trends Shaping the Semiconductor Landscape
Lightweight and Flexible Electronics: The Next Frontier
The semiconductor industry is witnessing a significant transformation with the advent of lightweight and flexible electronics. This shift is not just a trend but a strategic move towards more versatile and adaptable technologies. The flexible electronics market is rapidly expanding, with projections indicating a growth from $29.40 billion in 2024 to $70.97 billion by 2032, marking a compound annual growth rate (CAGR) of 11.6%. This growth is fueled by the demand for thinner, lighter, and more bendable devices that can be integrated into a variety of applications, from wearables to medical devices.
In response to these market demands, semiconductor plastics are emerging as a key material, offering high temperature stability and the ability to conform to different shapes and structures. The role of polyphenylene sulfide (PPS) is particularly noteworthy, as it demonstrates the capacity to withstand high temperatures, making it a prime candidate for the highest growth within the semiconductor market. As the industry evolves, the competitive landscape is also shifting, with companies racing to develop materials that can support the next generation of flexible electronics.
The table below summarizes the projected market size and growth rate for flexible electronics:
Year | Market Size ($Billion) | CAGR (%) |
---|---|---|
2024 | 29.40 | |
2032 | 70.97 | 11.6 |
These developments are not only reshaping the way we think about electronics but also how we measure return on investment (ROI) in the context of global manufacturing. The push towards lightweight and flexible electronics is setting a new frontier for innovation, with significant implications for the semiconductor industry’s future.
Polyphenylene Sulfide (PPS) and High-Temperature Performance
Polyphenylene Sulfide (PPS) is increasingly recognized for its critical role in the semiconductor industry, particularly for its high-temperature performance and chemical resistance. As the demand for lightweight and flexible electronics grows, PPS stands out as a material capable of meeting these advanced requirements due to its exceptional dimensional stability.
The market for semiconductor plastics like PPS is segmented by types and applications, with PPS forecasted to experience significant growth. Applications in CMP (Chemical Mechanical Planarization), semiconductor processes, and back-end processes are areas where PPS’s properties are particularly advantageous.
A comprehensive analysis of semiconductor plastic shipments from 2018 to 2030 highlights the market’s expansion by type, application, and region. The following table summarizes the projected growth of PPS in the semiconductor market:
Year | Shipment Value (USD) |
---|---|
2018 | $X million |
2023 | $Y million |
2030 | $Z million |
Companies like Ensinger, Boedeker Plastics, and Victrex are among the key players in the PPS market, indicating a competitive landscape that is both dynamic and strategically significant for the future of technology and sustainability.
The Role of Semiconductors in Electrification and Energy Efficiency
The integration of semiconductors into electric vehicles (EVs) is a testament to their pivotal role in the electrification and energy efficiency of modern transportation. Semiconductors are indispensable for managing power flows, optimizing charging, and enhancing the performance of EVs. They enable precise motor control for optimized efficiency and smooth acceleration, which is essential for the user experience and environmental benefits of electric mobility.
Advanced power electronics, which are the backbone of EVs, depend on semiconductor components such as insulated gate bipolar transistors (IGBTs) and silicon carbide (SiC) devices. These components are crucial for efficient power conversion and energy management. The battery management systems (BMS) in EVs also rely on semiconductors for critical functions like voltage and current sensing, temperature monitoring, and cell balancing, ensuring the battery pack’s performance, health, and safety.
The following table highlights the key semiconductor components used in EVs and their functions:
Component | Function |
---|---|
IGBTs | Power conversion |
SiC Devices | Energy management |
BMS | Battery performance monitoring |
As the automotive industry continues to evolve towards electrification, the demand for sophisticated semiconductor components is expected to rise, driving innovation and growth in the semiconductor sector.
The Semiconductor Workforce and Supply Chain Challenges
Addressing the Skilled Labor Shortage in the Industry
The semiconductor industry is facing a critical challenge: a growing talent gap. By 2030, the US alone is projected to have 460,000 semiconductor jobs, with an estimated 67,000 at risk of remaining unfilled. This shortage is not just a national issue but a global one, with a forecast of 1 million semiconductor positions worldwide demanding urgent attention.
To address this issue, industry leaders are advocating for three key actions:
- Growing the talent pipeline through educational partnerships and outreach.
- Creating reskilling programs to help current employees adapt to new technologies.
- Leveraging AI and automation to augment the workforce and improve efficiencies.
These steps are crucial for maintaining the industry’s growth and ensuring that semiconductor companies can meet the increasing demand. As new semiconductor fabrication plants come online, the need for skilled labor will only intensify, making the implementation of these strategies an immediate priority.
Navigating the Global Semiconductor Shortage
The shortage of semiconductors has become a pivotal issue for industries worldwide, particularly in the automotive sector. This scarcity has led to production delays and has necessitated a strategic allocation of available chips to essential components and products. To mitigate the impact, companies are advised to conduct a thorough analysis to identify their critical semiconductor needs.
In response to these challenges, semiconductor leaders are stepping up efforts to ensure they meet industry demands. The construction of new onshore fabrication plants is one such measure being taken to prevent future shortages. These fabs are expected to address the sharp demand rebound and avoid the pitfalls experienced during the pandemic-induced chip scarcity.
The situation also underscores the need for a redesign of supply chains. The current pressures demand a reconfiguration that can support the growing demands of the semiconductor industry. Collaborative efforts among stakeholders and a focus on talent development are crucial for overcoming the talent gap and ensuring a resilient supply network.
Supply Network Redesign for Resilient Semiconductor Production
The semiconductor industry has recognized the need for a redesign of the supply network to enhance resilience and adaptability. The recent supply chain crisis highlighted the importance of bringing supply closer to demand, prompting a shift towards onshoring and nearshoring of manufacturing facilities. This strategic move is not only about risk mitigation but also about aligning production with the evolving needs of the market.
Key initiatives include the integration of industrial automation and the adoption of digital technologies such as machine learning, scalable robotics, and sensors. These advancements are crucial for creating a robust digital core that can withstand future disruptions. Moreover, the construction of new semiconductor fabrication plants is underway, with a significant number of sites expected to be operational by 2024. This expansion is a direct response to the lessons learned from past shortages and a proactive step towards securing a stable supply chain.
The table below illustrates the commitment of executives to localize manufacturing:
Percentage | Goal |
---|---|
78% | Factories within 4 time zones of the customer |
As the industry moves forward, it is imperative to address the growing talent gap. With an estimated 1 million semiconductor positions to be filled globally by 2030, there is an urgent need to develop programs that cultivate the necessary skills and attract new talent to the field. The future of semiconductor production hinges on the ability to balance technological innovation with human expertise.
The Future of Semiconductor Plastics and Wet Chemicals Markets
Semiconductor Plastics: Growth Forecast and Market Dynamics
The semiconductor plastic market is on the brink of a significant expansion, with a projected compound annual growth rate (CAGR) of 7.2% from 2024 to 2030. This growth is fueled by the material’s high temperature stability and its increasing importance in technology and sustainable energy applications.
Emerging trends, such as the demand for lightweight and flexible electronics, are driving the need for innovative materials. The market is responding with offerings like polyphenylene sulfide (PPS), which is expected to see the highest growth due to its high-temperature performance capabilities.
The competitive landscape is diverse, with key players including Ensinger, A&C Plastics, Boedeker Plastics, Victrex, Solvay, Evonik, and ZYPEEK. These companies are at the forefront of addressing the complexities and strategic importance of semiconductor plastics in the evolving tech landscape.
Year | Shipment Value (USD) |
---|---|
2018 | Data Not Available |
2024 | Data Not Available |
2030 | Projected Increase |
High-Purity Wet Chemicals: Meeting Industry Standards
In the semiconductor industry, the role of high-purity wet chemicals is pivotal. These specialized chemicals are integral to the processes of cleaning, etching, and polishing silicon wafers, which form the backbone of semiconductor devices. The market for these chemicals is characterized by the need for extreme purity, as even minute impurities can significantly impact the performance and reliability of the final product.
Market leaders such as KMG Chemicals Inc, BASF SE, Honeywell International LLC, and Eastman Chemical Company have set high standards in the provision of semiconductor grade wet chemicals. Their commitment to quality ensures that the stringent purity requirements of the industry are consistently met. Newer companies like Kredence Pvt Ltd and Jiangyin Jianghua Microelectronics Materials are also emerging, offering innovative solutions and competitive pricing, thus enriching the market landscape.
Company | Reputation | Innovative Solutions | Competitive Pricing |
---|---|---|---|
KMG Chemicals Inc | Strong | Yes | Moderate |
BASF SE | Strong | Yes | Moderate |
Honeywell International LLC | Strong | Yes | Moderate |
Eastman Chemical Company | Strong | Yes | Moderate |
Kredence Pvt Ltd | Growing | Yes | High |
Jiangyin Jianghua Microelectronics Materials | Growing | Yes | High |
The semiconductor grade wet chemicals market is not just about the chemicals themselves but also about the standards they must adhere to. The industry’s relentless pursuit of higher performance and efficiency drives the continuous evolution of these standards, ensuring that the production of semiconductors remains at the cutting edge of technological advancement.
Investment Trends and Competitive Landscape in Semiconductor Materials
The semiconductor materials market is witnessing a significant influx of investments, with companies strategically positioning themselves to capitalize on emerging opportunities. Globally, companies plan to invest about $1 trillion in semiconductor fabs through 2030, with most investment concentrated in Asia and the United States. This greenfield opportunity in semiconductors is indicative of the industry’s robust growth trajectory and the importance of securing a competitive edge.
Top players in the semiconductor plastics market are actively engaging in infrastructural development and value chain integration. These efforts are aimed at meeting the rising market demands and improving customer relations. The focus on high-temperature stability and advancements in technology underscores the critical role of semiconductor plastics in the sustainable energy sector.
Region | Investment Focus | Growth Potential |
---|---|---|
Asia | Semiconductor fabs | High |
United States | Semiconductor fabs | High |
The market dynamics reveal a compound annual growth rate (CAGR) of 7.2% from 2024 to 2030, highlighting the potential for substantial growth within the semiconductor plastic industry. Attention is also drawn to the demand for materials capable of withstanding high temperatures, such as polyphenylene sulfide (PPS), which is expected to see the highest growth in the market.
Conclusion
The semiconductor industry stands at the cusp of a transformative era, driven by the relentless pursuit of innovation and efficiency. As we have explored, trends such as the onshoring of manufacturing facilities, the rise of silicon carbide in automotive applications, and the growing demand for lightweight, flexible electronics are reshaping the landscape. Market dynamics indicate a robust growth trajectory, fueled by the electric vehicle boom, the integration of AI, ML, and IoT technologies, and the need for high-purity semiconductor chemicals. Despite challenges like skilled labor shortages and supply constraints, the industry’s future is bright, with substantial investments signaling confidence in its expansion. As semiconductor technology continues to power the future of tech innovation, it is imperative for stakeholders to adapt to emerging trends, foster strategic partnerships, and invest in talent development to harness the full potential of this dynamic sector.
Frequently Asked Questions
What are the driving forces behind the onshoring movement in semiconductor manufacturing?
The onshoring movement is driven by the need for high-tech industries to secure supply chains, reduce dependence on foreign manufacturers, and increase national security. Engaging in partnerships, rethinking talent strategies, enabling advanced technologies, and reassessing ROI expectations are key to its success.
How is Silicon Carbide influencing the automotive semiconductor industry?
Silicon Carbide is becoming increasingly popular in the automotive sector due to its efficiency in high-power applications. It’s pivotal for electric vehicles (EVs), facilitating better battery management, power electronics, and motor control which are essential for the shift towards vehicle electrification.
What impact do electric vehicles have on semiconductor demand?
The rise of electric vehicles has significantly increased the demand for semiconductors. EVs require sophisticated semiconductor components for energy efficiency, battery management, and overall vehicle performance, leading to a surge in the integration of semiconductor technology in the automotive industry.
What trends are shaping the future of lightweight and flexible electronics?
The demand for lightweight and flexible electronics is growing, with innovations in materials such as semiconductor plastics that offer high temperature stability. These advancements are key to new applications in technology and sustainable energy sectors.
How is the semiconductor workforce responding to the skilled labor shortage?
The industry is addressing the skilled labor shortage by investing in workforce development, enhancing educational programs, and creating partnerships to attract and train talent. These efforts are crucial to meet the increasing complexities of semiconductor manufacturing and design.
What are the market predictions for semiconductor plastics and high-purity wet chemicals?
The semiconductor plastics market is expected to grow at a CAGR of 7.2% from 2024 to 2030, driven by their critical role in technology and sustainable energy. The wet chemicals market is also growing due to the demand for high-purity substances that meet stringent industry standards, presenting opportunities for companies in the semiconductor materials sector.