Navigating the Complex Landscape of Semiconductor Equipment Technologies
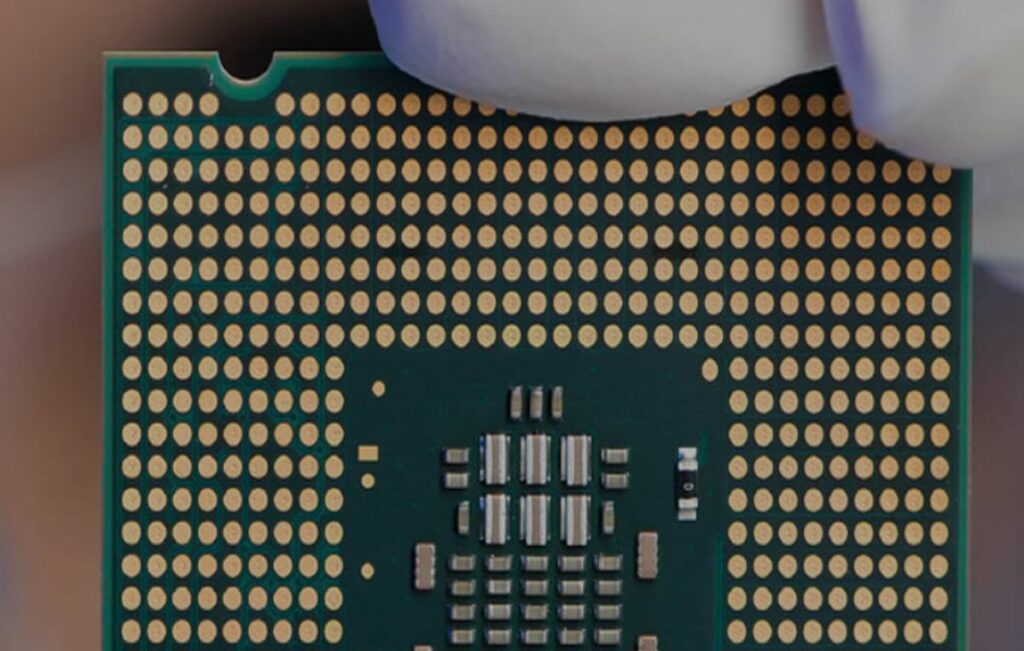
The semiconductor equipment technology sector is a dynamic and rapidly advancing field, pivotal to the progression of numerous industries. As companies strive to adapt to the latest technological demands, they face the intricate task of transforming their semiconductor fabrication facilities. These upgrades are essential for developing cutting-edge applications, but they bring a host of challenges and complexities. This article delves into the evolution of semiconductor equipment technologies, the obstacles encountered during fab conversions, the impact of geopolitical factors, the importance of collaboration and innovation, and the future trends that will shape the industry.
Key Takeaways
- Upgrading semiconductor fabs is crucial for staying competitive, but it requires navigating a complex ecosystem of technology and engineering challenges.
- The integration of advanced materials and nanotechnology is driving innovation in semiconductor manufacturing, leading to improved performance and new market opportunities.
- Geopolitical tensions, particularly between the US and China, are influencing the strategic decisions and adaptability of companies within the semiconductor sector.
- Collaboration with industry leaders and investment in sustainable resources are key strategies for successful fab upgrades and maintaining health and safety standards.
- To remain at the forefront of the semiconductor industry, companies must stay informed about emerging trends and be prepared to harness expertise to meet future challenges.
The Evolution of Semiconductor Fabrication Technologies
Upgrading Fabrication Processes for Cutting-edge Applications
The relentless pursuit of innovation in the semiconductor industry has made upgrading fabrication processes a necessity for maintaining a competitive edge. The integration of Artificial Intelligence (AI) and robotics is a testament to the industry’s commitment to precision and efficiency. These advancements are not only crucial for the current generation of semiconductor devices but also pave the way for future applications that demand even greater performance.
To successfully upgrade fabrication processes, several key steps must be taken:
- Comprehensive analysis of existing systems and identification of potential bottlenecks.
- Strategic planning to incorporate new technologies without disrupting ongoing operations.
- Implementation of advanced materials and nanotechnology to enhance device capabilities.
- Continuous monitoring and optimization of the upgraded processes to ensure peak performance.
Emerging technologies, such as AI, are revolutionizing the way semiconductor fabs operate. By leveraging machine learning models, fabs can now predict and prevent equipment failures, optimize energy consumption, and significantly improve yields. This not only accelerates the time-to-market for new products but also ensures that the semiconductor devices meet the high standards required for cutting-edge applications.
The Role of Advanced Materials and Nanotechnology
The integration of advanced materials and nanotechnology is a pivotal factor in the semiconductor industry’s evolution. These technologies are not only enhancing device performance but also enabling new applications. For instance, the use of novel materials like graphene and carbon nanotubes has led to the development of transistors that are faster and more energy-efficient than their silicon counterparts.
Collaborative efforts are essential in overcoming the challenges posed by these sophisticated technologies. Public-private partnerships and research consortia are instrumental in driving innovation, as they facilitate the sharing of knowledge and resources. The recent addition of new nanofabrication equipment at MIT.nano is a testament to the industry’s commitment to advancing research and development.
Despite the promise of these technologies, the transition to advanced manufacturing processes is complex. It requires a comprehensive understanding of the fabrication ecosystem and a strategic approach to managing the intricate systems within semiconductor fabs. The table below outlines some of the key challenges and potential solutions in implementing advanced materials and nanotechnology in semiconductor manufacturing.
Optimizing Systems for Enhanced Performance and Efficiency
In the pursuit of enhanced performance and efficiency, semiconductor manufacturers are turning to innovative solutions that leverage the power of artificial intelligence (AI) and machine learning. The integration of AI into semiconductor fabrication is revolutionizing the industry by optimizing production processes, improving yields, and reducing time-to-market. Machine learning models are particularly adept at analyzing large datasets to identify patterns, predict equipment failures, and optimize energy consumption, marking a new era of efficiency and agility in manufacturing.
However, the path to optimization is not without its challenges. Despite meticulous planning, unforeseen complications can arise during fab conversions, such as compatibility issues between systems or production bottlenecks. These challenges necessitate a combination of agility, adaptability, and robust problem-solving capabilities to ensure smooth progress and maintain the delicate balance between innovation and operational stability.
Key Takeaways:
- Samsung’s System LSI Business is at the forefront of integrating security and efficiency into semiconductor solutions.
- AI and machine learning are pivotal in optimizing energy usage and production workflows.
- The advent of technologies like 5G is set to further influence the strategic direction and partnerships within the semiconductor industry.
Challenges in Semiconductor Fab Conversions
Understanding the Fabrication Ecosystem
Semiconductor fabrication facilities, or fabs, are intricate environments where the slightest change can have far-reaching implications. Understanding the fabrication ecosystem is critical when considering upgrades or conversions to accommodate new technologies or improve efficiencies. These facilities are not just about the advanced equipment; they encompass a complex network of materials, processes, and quality control systems that are all interdependent.
The process of converting a fab involves several key steps:
- Assessing the current capabilities and limitations of the facility.
- Identifying the necessary technological upgrades and sourcing the right equipment.
- Revising workflows to integrate new processes while minimizing downtime.
- Implementing stringent quality control measures to ensure the new processes meet industry standards.
By carefully navigating these steps, manufacturers can mitigate risks and ensure a smooth transition during fab upgrades. Partnering with industry leaders and investing in the right resources are essential strategies for successfully managing the complexities of the fabrication ecosystem.
Navigating Engineering Complexities in Facility Upgrades
The complexity of semiconductor fab conversions is a testament to the marvels of engineering involved in these facilities. Upgrading equipment and reconfiguring production lines are just the tip of the iceberg. Deep knowledge of the fabrication ecosystem is essential, encompassing everything from the materials used to the quality control measures in place.
Substantial investments are required to navigate these complexities successfully. Not only does this involve significant capital expenditure, but also a strategic allocation of resources. Personnel must be retrained, and a learning curve is associated with new technologies. The table below outlines the key areas of investment and considerations:
Area of Investment | Consideration |
---|---|
Equipment Upgrades | Capital Expenditure |
Production Line Reconfiguration | Resource Allocation |
Personnel Retraining | Learning Curve |
Moreover, the risk of unforeseen complications cannot be ignored. Despite careful planning, challenges such as compatibility issues and production bottlenecks may arise, necessitating a robust approach to problem-solving to maintain smooth operations.
Ensuring Quality Control During Process Transitions
In the intricate dance of semiconductor fab conversions, quality control stands as the guardian of product integrity and reliability. Any deviation from the established processes can lead to defects, compromising the components and, by extension, the manufacturer’s reputation.
The conversion process is fraught with potential complications, from compatibility issues to production bottlenecks. These challenges necessitate a combination of agility, adaptability, and robust problem-solving to maintain the smooth progression of upgrades. Here are some key considerations for ensuring quality control during process transitions:
- Meticulous planning to anticipate and mitigate risks
- Continuous monitoring of production to detect deviations early
- Implementing robust quality control management practices (QCMP)
- Training personnel to adapt to new systems and processes
Maintaining production continuity is crucial, as fabs operate on tight schedules where downtime equates to financial losses. Disruptions not only affect yields and quality but also customer satisfaction. Therefore, it is imperative to execute conversions with precision to minimize downtime and uphold quality standards.
Strategic Adaptability in the Geopolitical Arena
Navigating US-China Technological Tensions
The U.S.-China Chip War represents a significant challenge for companies operating within the semiconductor sector. As tensions escalate, organizations like Teradyne are finding themselves at the crossroads of geopolitical dynamics and the fiercely competitive semiconductor industry. The strategic adaptability of these companies is crucial in maneuvering through the complexities introduced by the US’s export controls, which aim to curb China’s semiconductor manufacturing capabilities.
The battle for technological supremacy has far-reaching implications for global tech trade and serves as a critical case study. The evolving dynamics between the United States and China will undoubtedly influence the strategies of semiconductor companies. Those able to navigate these complexities will be closely scrutinized and may serve as a barometer for success in this high-stakes environment.
At the heart of the matter, the US aims to protect its semiconductor industry and national security interests by restricting sales of chips and chip-making equipment to Chinese companies. In response, China is pushing to accelerate its self-reliance in semiconductor production. The outcomes of this conflict will shape the future of the global semiconductor industry for years to come.
Regulatory Challenges and Market Positioning
In the semiconductor industry, regulatory compliance is a critical factor that influences both operational processes and market dynamics. Teradyne, known for its sophisticated testing equipment, is at the forefront of this challenge. The company must constantly adapt to the evolving regulatory landscape, particularly the stringent US export controls that aim to limit China’s semiconductor manufacturing capabilities. This situation necessitates strategic adjustments, such as diversifying supply chains and increasing investments in research and development (R&D).
The Asia-Pacific semiconductor industry, including key players like Teradyne, faces additional regulatory challenges. Manufacturers are required to adhere to a variety of safety standards, environmental regulations, and other compliance measures. These requirements can significantly impact the cost and complexity of semiconductor production. To offset potential losses in markets like China, companies are exploring new markets and deepening collaborations with US chipmakers, who are currently benefiting from government incentives under initiatives like the CHIPS Act.
Looking ahead, the semiconductor industry must continue to expand its ecosystem and foster market growth despite these challenges. Collaborative research efforts and public-private partnerships are essential in fostering innovation and addressing the shared challenges of shrinking feature sizes, increased complexity, and rising production costs.
Maintaining Competitiveness Amidst Export Controls
In the wake of stringent export controls, companies like Teradyne are at the forefront of a delicate balancing act. Teradyne’s strategic adaptability is crucial as it faces the dual challenge of complying with U.S. regulations while striving to preserve its market share in China. The company’s response includes a multipronged approach:
- Diversifying supply chains to mitigate risks
- Ramping up R&D investments to innovate beyond restrictions
- Exploring new markets to compensate for potential losses
- Strengthening partnerships with U.S. chipmakers, leveraging incentives such as the CHIPS Act
These steps are not just reactive measures but are part of a broader strategy to ensure long-term resilience and growth. The evolving dynamics of the U.S.-China chip war serve as a backdrop for companies to reassess and fortify their global strategies. Teradyne’s ability to navigate these complexities will be a barometer for success in the semiconductor industry’s high-stakes environment.
Collaboration and Innovation in Semiconductor Manufacturing
Partnering with Industry Leaders for Successful Upgrades
In the fast-paced world of semiconductor manufacturing, strategic partnerships are not just beneficial; they are a necessity for success. Partnering with industry leaders such as Samsung System LSI Business and HBC-Semicons can provide a wealth of expertise and resources that are crucial for navigating the complexities of fab upgrades. These collaborations help expand the ecosystem, ensuring that the dynamic needs of the industry are met with agility and precision.
The journey towards upgrading semiconductor fabs is fraught with complexity and risks. By leveraging the strengths of established industry leaders, manufacturers can mitigate these risks and ensure a smoother transition. The table below highlights the key benefits of such strategic partnerships:
Benefit | Description |
---|---|
Expertise | Access to specialized knowledge and cutting-edge technology. |
Resources | Investment in the necessary tools and systems for upgrades. |
Risk Mitigation | Shared responsibility and reduced impact of potential setbacks. |
Market Growth | Enhanced capabilities leading to increased competitiveness. |
Ultimately, the goal is to achieve minimal disruption during the upgrade process while maximizing return on investment. This requires meticulous planning and execution, which is greatly facilitated by the guidance and support of experienced partners. The health and safety of all individuals involved in the process are also prioritized, ensuring a responsible approach to innovation and growth.
Investing in Resources for Sustainable Growth
In the dynamic world of semiconductor manufacturing, investing in the right resources is crucial for sustainable growth. Companies are expanding their ecosystems to address the need for eco-conscious computing, which is integral to the digital transformation across various industries.
Strategic adjustments are necessary to navigate the challenges that come with growth. For instance, Teradyne’s approach to diversifying its supply chain and increasing R&D investments exemplifies the proactive measures companies must take. These efforts, coupled with exploring new markets and deepening collaborations, are essential to maintaining a competitive edge.
The table below highlights the key areas of investment for sustainable growth in the semiconductor industry:
Area of Investment | Description |
---|---|
Eco-Conscious Computing | Addressing the need for environmentally friendly technology. |
R&D | Staying ahead of regulatory restrictions and technological advancements. |
Supply Chain Diversification | Reducing dependency on single sources and mitigating risks. |
Market Exploration | Identifying and penetrating new markets to expand reach. |
Collaborations | Partnering with industry leaders to leverage shared expertise. |
By understanding the intricacies of fab conversions and prioritizing health and safety, semiconductor manufacturers can emerge stronger and more resilient. Partnering with trusted industry leaders like HBC-Semicons ensures that companies can navigate these transitions with confidence.
Prioritizing Health and Safety in Manufacturing Environments
In the semiconductor industry, the health and safety of the workforce are paramount. Ensuring a safe manufacturing environment is not only a regulatory requirement but also a critical factor in sustaining productivity and morale. The implementation of comprehensive Environmental, Health, and Safety (EHS) programs is essential to identify potential hazards and mitigate risks.
Key components of an effective EHS program include:
- Regular risk assessments and safety audits
- Continuous training and education for employees
- Adoption of industry best practices and standards
- Emergency response planning and drills
- Monitoring and controlling exposure to hazardous materials
By proactively addressing these areas, manufacturers can create an Injury Free Environment (IFE), which is instrumental in minimizing accidents and occupational illnesses. Moreover, the growing concern over PFAS (per- and polyfluoroalkyl substances) highlights the need for stringent environmental controls to prevent contamination and protect both employees and the surrounding community.
Future Trends and Opportunities in Semiconductor Technologies
Staying Abreast of Industry Developments
In the dynamic realm of semiconductor technologies, staying abreast of industry developments is not just beneficial; it’s imperative for survival. The industry is at the forefront of technological innovation, addressing the need for eco-conscious computing and contributing to the ongoing digital transformation across industries.
The 2024 semiconductor industry outlook by Deloitte highlights five semiconductor trends that could shape the chip market in the year ahead. These insights are crucial for companies looking to maintain a competitive edge. For instance, the integration of semiconductor smart factories is a trend that’s gaining momentum, promising to revolutionize the future of semiconductor manufacturing.
Navigating the complexity of converting semiconductor fabs requires a deep understanding of these trends. By harnessing the collective expertise of industry stakeholders, companies can navigate the complexities of tomorrow’s semiconductor landscape with confidence and foresight.
Harnessing Expertise for Tomorrow’s Challenges
The semiconductor industry stands at the cusp of a transformative era, where innovation and collaboration are paramount to overcoming the hurdles of tomorrow. As we venture into this new phase, it is essential to leverage the collective wisdom and experience of the sector’s brightest minds.
To ensure a robust response to future challenges, the industry must focus on several key areas:
- Fostering collaborative research efforts through public-private partnerships and consortia.
- Embracing the principles of Industry 4.0 and integrating advanced technologies like AI.
- Prioritizing eco-conscious computing to address the environmental impact of digital transformation.
These strategic initiatives will not only drive technological advancements but also contribute to a more efficient and sustainable semiconductor ecosystem. By harnessing expertise across these domains, the industry can confidently navigate the complexities of the future, ensuring continued growth and innovation.
Exploring New Markets and Applications
The semiconductor industry is on the brink of a new era, with emerging technologies catalyzing a transformation in manufacturing processes. These innovations are not just enhancing device performance but are also carving out new niches in the market. For instance, the integration of AI and IoT is creating a demand for semiconductors in previously untapped sectors.
To capitalize on these opportunities, companies are exploring strategic partnerships and expanding their ecosystems. Collaborations with industry leaders are proving essential in navigating the complexities of new applications. Moreover, these alliances are instrumental in overcoming the challenges of shrinking feature sizes and rising production costs.
The future of the semiconductor industry is deeply intertwined with emerging technologies like AI, IoT, and advanced manufacturing techniques. As the industry evolves, it is crucial to stay abreast of these developments to harness their full potential. The table below outlines some of the key areas where semiconductor applications are expected to grow:
Market Segment | Expected Growth Area |
---|---|
Automotive | Autonomous vehicles |
Healthcare | Wearable devices |
Consumer Tech | Smart home systems |
Industrial | Automation solutions |
In conclusion, the semiconductor industry must continue to foster innovation and collaboration to explore new markets and applications. By doing so, it will not only sustain growth but also drive technological advancement across various sectors.
Conclusion
The journey through the intricate terrain of semiconductor equipment technologies is both challenging and rewarding. As we have explored, the semiconductor industry is at the forefront of technological innovation, with advancements in materials, nanotechnology, and manufacturing processes reshaping the future. The conversion of semiconductor fabs, while complex, is a testament to the industry’s commitment to progress and efficiency. Companies like Teradyne exemplify the strategic adaptability required to thrive amidst geopolitical tensions. The path ahead is laden with obstacles, yet it is clear that with the right expertise, resources, and foresight, the semiconductor sector can continue to drive technological breakthroughs and maintain its pivotal role in the global economy.
Frequently Asked Questions
What are the main factors driving the evolution of semiconductor fabrication technologies?
The main factors include the demand for cutting-edge applications, the integration of advanced materials and nanotechnology, and the need for enhanced performance and efficiency in semiconductor devices.
What are some of the challenges faced during semiconductor fab conversions?
Challenges include understanding the intricate fabrication ecosystem, navigating engineering complexities in facility upgrades, and ensuring quality control during process transitions.
How are geopolitical tensions affecting the semiconductor industry?
Geopolitical tensions, particularly between the US and China, are creating strategic challenges for companies due to technological tensions and export controls that impact manufacturing capabilities and market positioning.
Why is collaboration important in semiconductor manufacturing?
Collaboration is key to successfully upgrading facilities, investing in sustainable growth, and ensuring health and safety standards. Partnering with industry leaders can provide the expertise and resources needed for complex fab conversions.
What future trends are likely to shape the semiconductor industry?
Key trends include ongoing technological advancements, the need for industry-wide expertise to tackle emerging challenges, and the exploration of new markets and applications for semiconductor technologies.
How can semiconductor manufacturers maintain competitiveness amid export controls?
Manufacturers can maintain competitiveness by adapting strategically to regulatory challenges, investing in innovation, and finding alternative markets or developing self-sufficiency in semiconductor production.