Revolutionizing the Industry: The Rise of Silicon Carbide Manufacturers
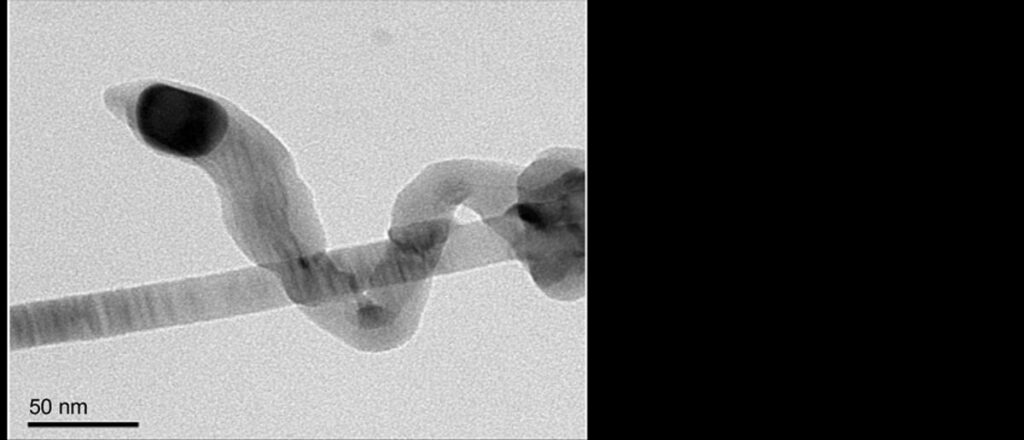
Silicon carbide (SiC), a compound of silicon and carbon atoms, has emerged as a revolutionary material in the semiconductor industry due to its exceptional properties such as hardness, thermal conductivity, and corrosion resistance. Its significance spans across various sectors, including electronics, automotive, and energy, propelling the growth of SiC manufacturers. This article delves into the market landscape, growth drivers, challenges, and future outlook of the SiC industry, with a focus on the burgeoning Indian market.
Key Takeaways
- Silicon carbide’s superior properties are driving its adoption over traditional silicon in power electronics, particularly for efficient power conversion in electric vehicles and renewable energy systems.
- The Indian market is witnessing a significant rise in SiC demand, with market analysis forecasting robust growth, driven by advancements in power electronics and the automotive sector.
- Challenges such as resistance to material transition, limited supply chain infrastructure, and compatibility concerns are critical restraints that SiC manufacturers must address to accelerate market adoption.
- Opportunities for SiC manufacturers include leveraging the trend of miniaturization and higher power density, as well as catalyzing the expansion of renewable energy infrastructure.
- The future of SiC manufacturing is promising, with strategies for scaling production and distribution being pivotal for tapping into predicted market growth and emerging trends across various industries.
Understanding Silicon Carbide’s Market Landscape
Defining Silicon Carbide and Its Industrial Significance
Silicon carbide (SiC) is a compound of silicon and carbon, known for its exceptional hardness and thermal properties. It has been a pivotal material since the late 19th century, initially used for sandpapers, grinding wheels, and cutting tools. In modern times, its applications have expanded significantly due to its high thermal conductivity and resistance to corrosion.
SiC’s industrial significance lies in its versatility and efficiency. It is a critical component in semiconductor devices, which are essential for the functioning of a wide range of electronic equipment. Additionally, its use in ceramics and refractories showcases its durability and ability to withstand extreme environments.
The following table outlines the various applications and end-uses of SiC in the industry:
Application | End-Use |
---|---|
Metallurgy | Heavy Engineering |
Abrasives | Automotive, Aerospace |
Refractory | Military and Defense |
Electrical & Electronics | Consumer Electronics, Healthcare |
Other | Various Industries |
The adoption of SiC in these applications is driven by its unique properties, which enable improved performance and efficiency in products and systems across multiple sectors.
The Indian Silicon Carbide Market: An Overview
The Indian market for Silicon Carbide (SiC) has been witnessing a significant surge, with projections indicating a robust growth trajectory. In 2023, the market size was valued at USD 41,356.70 thousand and is anticipated to expand to USD 93,942.90 thousand by 2031, flourishing at a compound annual growth rate (CAGR) of 10.8%. This growth is reflective of the increasing demand for SiC in various applications due to its superior properties.
Key players such as CUMI EMD, SNAM Abrasives Pvt Ltd, and Entegris have established a strong presence in the Indian market, dominating the landscape in 2021. Their influence is bolstered by continuous investments in research and development, strategic market initiatives, and an expansive global presence.
The market is segmented based on product type, device, wafer size, application, and end-use. The segments that are poised for the most significant growth offer valuable insights into the core applications driving the market. Among the product types, black and green SiC variants are prevalent, catering to different industry requirements.
Key Market Dynamics Influencing Silicon Carbide Adoption
The growing demand for power electronics is a significant driver in the adoption of silicon carbide (SiC), particularly in India. This demand stems from the need for efficient power conversion across various sectors, including electric vehicles, renewable energy, and industrial motors. SiC’s superior properties, such as enhanced performance and system efficiency, make it a preferred choice over traditional silicon-based devices.
However, the transition from traditional materials to SiC faces resistance due to compatibility, adaptability, and redesign concerns. These challenges slow down the adoption process as industries are wary of potential disruptions to existing systems. Additionally, the limited supply chain infrastructure for SiC poses a restraint, affecting the market’s ability to meet the rising demand.
Despite these challenges, the market presents opportunities for growth through the increasing trend of miniaturization and higher power density requirements. The expansion of renewable energy infrastructure also offers a promising avenue for SiC adoption. Key players such as CUMI EMD, SNAM Abrasives Pvt Ltd, and Entegris have been identified as dominant forces in the Indian SiC market, indicating a concentrated market landscape.
Driving Forces Behind Silicon Carbide’s Growth
The Surge in Demand for Power Electronics
The surge in demand for power electronics is a significant driver for the silicon carbide (SiC) industry. As the world moves towards more energy-efficient solutions, SiC’s superior properties over conventional silicon-based devices are becoming increasingly important. This demand is particularly evident in sectors such as electric vehicles (EVs), renewable energy, and industrial motors.
In the realm of electric vehicles, SiC devices are crucial for enhancing efficiency, extending driving range, and accelerating charging times. These benefits are not just theoretical; they are being realized in practical applications, as evidenced by the recent launch of STMicroelectronics N.V.‘s third-generation STPOWER SiC MOSFETs, which are tailored for electric vehicles and powertrains.
The renewable energy sector also benefits from SiC’s capabilities, especially in solar and wind power systems that require efficient power conversion. SiC-based power electronics improve the performance and resilience of these systems, making them more reliable and efficient.
Furthermore, the trend towards miniaturization and higher power density in electronics is another area where SiC shows great promise. SiC devices enable the creation of smaller, more powerful devices that are essential for aerospace and portable electronics, where space and weight are at a premium.
Silicon Carbide’s Role in Electric Vehicle Innovation
The electrification of the automotive industry has been significantly accelerated by the integration of silicon carbide (SiC) technology in electric vehicles (EVs). SiC-based power electronics, such as Metal-Oxide-Semiconductor Field-Effect Transistors (MOSFETs), are now at the forefront of this transformation. These components are crucial for EVs as they enhance efficiency, extend driving ranges, and enable faster charging times.
The following table highlights the advantages of SiC in EV power electronics compared to traditional silicon (Si) devices:
Feature | Silicon (Si) | Silicon Carbide (SiC) |
---|---|---|
Efficiency | Moderate | High |
Driving Range | Standard | Extended |
Charging Time | Longer | Reduced |
SiC’s superior thermal conductivity and minimal resistance are pivotal in supporting the high-voltage requirements of modern EVs. This has led to a surge in demand for SiC components, with manufacturers like STMicroelectronics launching advanced SiC MOSFETs tailored for electric vehicles. Such innovations are not only enhancing vehicle performance but are also instrumental in the growth of the SiC market.
Renewable Energy and the Need for Efficient Power Conversion
The relentless pursuit of efficiency in renewable energy systems has positioned silicon carbide (SiC) at the forefront of power electronics innovation. SiC-based power electronics offer enhanced efficiency and reliability, crucial for the performance and resilience of power conversion systems in sustainable energy applications. This is particularly true for solar and wind power infrastructure, where high voltage switching and power conversion are paramount.
The advantages of SiC inverter technology are not just theoretical; they are already being realized in the field. SiC devices enable smaller sizes and greater power densities compared to traditional silicon counterparts, a critical factor in industries where space and weight are at a premium. This miniaturization is unlocking a new era of energy efficiency, transforming device design to accommodate more compact and lightweight solutions without sacrificing performance.
The rise in electric vehicle (EV) adoption further underscores the significance of SiC in modern applications. With heightened efficiency, SiC devices contribute to extended driving ranges and accelerated charging times, amplifying their importance in the rapidly growing EV market. As the demand for renewable energy and efficient power conversion continues to climb, SiC manufacturers are poised to play a pivotal role in forwarding and revolutionizing applications in various sectors, including industrial machinery and renewable energy systems.
Challenges and Restraints in Silicon Carbide Adoption
Overcoming the Inertia of Traditional Material Use
The transition from well-established materials to innovative alternatives like silicon carbide (SiC) is often met with resistance. This reluctance stems from concerns about compatibility, adaptability, and the need for redesigning existing systems. Overcoming these barriers is essential for SiC to gain traction and for the market to expand into various applications.
Industries are hesitant to invest in SiC technology due to the potential disruptions it may cause to their current operations. However, the benefits of SiC, such as increased efficiency and the ability to support forward and revolutionizing applications in sectors like electric vehicles and renewable energy, make it a compelling choice for those looking to unlock a new era of energy efficiency.
To facilitate this shift, manufacturers and stakeholders must address these concerns by demonstrating the long-term advantages of SiC over traditional materials. This includes showcasing successful case studies, providing robust support for system redesign, and ensuring a smooth transition that minimizes operational disruptions.
Addressing the Limited Supply Chain Infrastructure
The limited infrastructure for silicon carbide production and distribution is a significant bottleneck. Insufficient facilities and logistics not only slow down material availability but also increase lead times and costs. This situation restricts market scalability, delays product launches, and undermines competitiveness, which is crucial for the broader adoption of SiC technology.
To address these challenges, manufacturers and stakeholders are exploring various strategies:
- Assessing strategic possibilities and creating effective action plans.
- Enhancing distributor mapping by region to improve logistics.
- Investing in domestic manufacturing to reduce reliance on foreign supply chains.
These steps are essential to ensure a steady and reliable supply chain that can support the growing demand for silicon carbide in various industries.
Navigating Compatibility and Redesign Concerns
As silicon carbide (SiC) continues to gain traction in various industries, compatibility and redesign concerns present significant challenges. Manufacturers must ensure that SiC components can integrate seamlessly with existing systems, which often necessitates substantial redesign efforts. This integration is crucial for the practical implementation of SiC in applications such as negative electrodes in lithium-ion batteries (LIBs).
The transition to SiC requires a careful evaluation of the compatibility with current technology platforms. For instance, the thermal expansion properties of SiC differ from traditional materials, which can lead to mechanical stresses if not properly accounted for. Additionally, the electrical characteristics of SiC, while advantageous, may require adjustments in circuit design to fully leverage its benefits.
To address these challenges, manufacturers are adopting a step-by-step approach:
- Assessment of existing systems for potential integration issues
- Design and simulation of SiC-based components
- Prototyping and testing to evaluate performance and identify unforeseen issues
- Iterative redesign to refine the compatibility of SiC components
The overall study suggests that commercially available SiC materials are worthy of consideration as negative electrodes in LIB upon deliberate redesign and compatibility checks. This process, while time-consuming, is essential for harnessing the full potential of SiC technology.
Emerging Opportunities for Silicon Carbide Manufacturers
Leveraging Miniaturization and Higher Power Density
Silicon carbide (SiC) devices are at the forefront of technological innovation, enabling smaller sizes and greater power densities compared to their silicon counterparts. This is particularly vital in industries such as aerospace and portable electronics, where space and weight are at a premium. The ability to create more compact and lightweight solutions without sacrificing performance is essential for meeting the demands of modern applications.
The surge in electric vehicle (EV) adoption further propels the demand for SiC-based power electronics. SiC devices offer heightened efficiency, extended driving range, and accelerated charging, amplifying their significance in EV technology. This trend underscores SiC’s pivotal role in advancing automotive electrification and fuels the expansion of the SiC market.
In the context of market opportunities, SiC’s attributes of efficiency, reliability, and minimal resistance are facilitating a seamless transition to high-voltage applications across various sectors. This includes electrified transportation, renewable energy, and aerospace, catalyzing market growth. The recent launch of third-generation STPOWER SiC MOSFETs by STMicroelectronics N.V. is a testament to the remarkable advancements in power density, energy efficiency, and reliability within the industry.
Catalyzing the Expansion of Renewable Energy Infrastructure
The relentless pursuit of enhanced efficiency and reliability in power conversion systems is a driving force behind the expansion of renewable energy infrastructure. Silicon carbide (SiC) stands at the forefront of this revolution, offering superior performance characteristics that are critical in solar and wind power applications.
SiC-based power electronics are increasingly preferred for their ability to operate at higher temperatures and frequencies, which translates into smaller, more efficient systems. This is particularly important in renewable energy sectors, where maximizing power density and minimizing space are paramount. The following points highlight the advantages of SiC in renewable energy:
- Improved performance and resilience of power conversion systems
- Higher efficiency in energy conversion processes
- Ability to handle higher power densities with reduced size
The market’s recognition of SiC’s transformative potential is evident in strategic partnerships and capacity expansions by industry leaders like Wolfspeed. These developments not only underscore Wolfspeed’s commitment to innovation but also reflect the growing demand for SiC solutions in sustainable energy applications.
Innovative Applications and 3D Printing Advancements
The integration of Silicon Carbide (SiC) into innovative applications is transforming industries by enabling more efficient and higher performance systems. Particularly in electric vehicles, industrial machinery, and renewable energy systems, SiC stands out for its ability to handle high temperatures and power levels, which are critical for these applications.
3D printing advancements are also opening new doors for SiC utilization. The ability to print complex shapes and components with SiC-infused materials is revolutionizing product design and manufacturing processes. This is especially pertinent in sectors where precision and material properties are paramount, such as aerospace and defense.
Opportunities for SiC in 3D printing include:
- Creation of intricate heat-resistant components
- Development of lightweight yet strong parts for aerospace
- Production of custom, high-performance industrial parts
These advancements not only enhance the capabilities of existing products but also pave the way for entirely new applications that were previously unattainable.
The Future Outlook of Silicon Carbide Manufacturing
Predicted Market Growth and Emerging Trends
The silicon carbide (SiC) industry is poised for significant growth, with a compound annual growth rate (CAGR) of 10.80% forecasted from 2023 to 2031. This robust expansion reflects the material’s increasing adoption across various sectors, driven by its superior properties and the escalating demand for efficient power solutions.
Market analysts predict a substantial rise in market size, from USD 41,356.70 thousand in the base year to an estimated USD 93,942.90 thousand by 2031. The following table encapsulates the projected market growth:
Year | Market Size (USD Thousand) |
---|---|
2023 | 41,356.70 |
2031 | 93,942.90 |
Emerging trends in the SiC market include a shift towards more energy-efficient systems and the integration of SiC in advanced applications such as electric vehicles and renewable energy systems. Manufacturers are also exploring innovative production techniques to meet the rising demand and address supply chain challenges.
Strategies for Scaling Production and Distribution
As the demand for Silicon Carbide (SiC) continues to escalate, manufacturers are exploring strategies to scale up production and enhance distribution networks. The challenge of scaling up SiC crystal growth is significant due to the complexity involved in producing high-quality crystals. To meet global production targets, manufacturers are seeking to expand their systems and capabilities.
One strategic approach involves significant capital investments in production facilities. For instance, a company headquartered in Durham, N.C., is undertaking a $6.5 billion capacity expansion. This expansion is not only a testament to the company’s commitment to long-term growth but also to sustainability and energy efficiency.
To address supply chain vulnerabilities, manufacturers are also focusing on diversifying and strengthening their supply networks. The acquisition of companies with enhanced production capabilities can lead to more resilient supply chains, which is vital in the current market scenario. Moreover, the integration of global supply chain strategies can provide customers with more comprehensive solutions, thereby improving market competitiveness.
Lastly, manufacturers are leveraging market research to understand production and capacity on a geographical scale, ensuring that distribution networks are optimized to meet demand efficiently.
Anticipating the Impact of Silicon Carbide on Various Industries
The auto industry is at the forefront of adopting silicon carbide (SiC) technology, with a keen focus on electric vehicles (EVs). Automakers and suppliers are actively seeking to secure supplies of SiC semiconductors, driven by the promise of faster battery charging times and overall improved performance. This push is indicative of the broader trends across various sectors.
Silicon carbide’s influence extends beyond automotive to areas such as aerospace, military and defense, and consumer electronics. Each of these industries stands to benefit from SiC’s superior thermal conductivity and resistance to corrosion. For instance, in aerospace, SiC can lead to more efficient power electronics, which is critical for both performance and safety.
The table below summarizes the potential impact of SiC across different industries:
Industry | Potential Impact |
---|---|
Automotive | Enhanced EV performance, faster charging |
Aerospace | Improved power electronics, safety enhancements |
Military & Defense | Advanced semiconductor applications |
Consumer Electronics | Higher power density in devices |
As we look to the future, the adoption of SiC is poised to catalyze significant changes. Manufacturers must navigate the challenges of transitioning from traditional materials and address the limited supply chain infrastructure to fully realize the potential of SiC in various applications.
Conclusion
As we stand on the cusp of a technological revolution, the rise of silicon carbide (SiC) manufacturers heralds a transformative era for various industries. The unique properties of SiC, such as its exceptional hardness, thermal conductivity, and resistance to corrosion, are driving its adoption in power electronics, automotive, aerospace, and renewable energy sectors. Despite challenges such as the transition from traditional materials and limited supply chain infrastructure, the market is poised for significant growth, fueled by the increasing demand for power electronics and the rise of electric vehicles. India’s SiC market, in particular, is expected to flourish, with projections indicating robust expansion by 2031. The future of SiC is bright, with its potential to enable miniaturization, higher power density, and the expansion of renewable energy infrastructure, ultimately revolutionizing the industry and paving the way for more efficient, sustainable, and high-performing solutions.
Frequently Asked Questions
What is Silicon Carbide and why is it significant in industry?
Silicon carbide (SiC) is a compound made of silicon and carbon atoms arranged in a crystal lattice. It is known for its hardness, thermal conductivity, and resistance to corrosion, making it valuable in electronics, automotive, and abrasives. SiC is used in semiconductor devices, ceramics, and refractories, offering enhanced performance over traditional materials.
How is the Indian Silicon Carbide market shaping up?
The Indian Silicon Carbide (SiC) market is experiencing growth driven by the demand for power electronics, with applications in electric vehicles, renewable energy, and industrial motors. Key players like CUMI EMD, SNAM Abrasives Pvt Ltd, and Entegris are dominating the market, which is expected to grow at 10.8% from 2021 to 2028.
What are the main drivers for the adoption of Silicon Carbide?
Key drivers include the surge in demand for power electronics, the role of SiC in electric vehicle innovation, and the need for efficient power conversion in renewable energy. SiC’s superior properties enable higher performance and efficiency, catalyzing the transition from traditional silicon-based devices.
What challenges do Silicon Carbide manufacturers face?
Manufacturers face challenges like resistance to transitioning from traditional materials, limited supply chain infrastructure, and compatibility and redesign concerns. Overcoming these barriers is crucial for the widespread adoption and market expansion of SiC technology.
What emerging opportunities exist for Silicon Carbide manufacturers?
Opportunities for manufacturers include leveraging miniaturization and higher power density for aerospace and portable electronics, catalyzing the expansion of renewable energy infrastructure, and exploring innovative applications such as 3D printing advancements.
What does the future hold for Silicon Carbide manufacturing?
The future outlook for Silicon Carbide manufacturing is promising, with predicted market growth and emerging trends. Strategies for scaling production and distribution are being developed to meet the anticipated impact of SiC on various industries, including automotive, aerospace, and consumer electronics.