Exploring the Process: A Detailed Look at Silicon Wafer Manufacturing
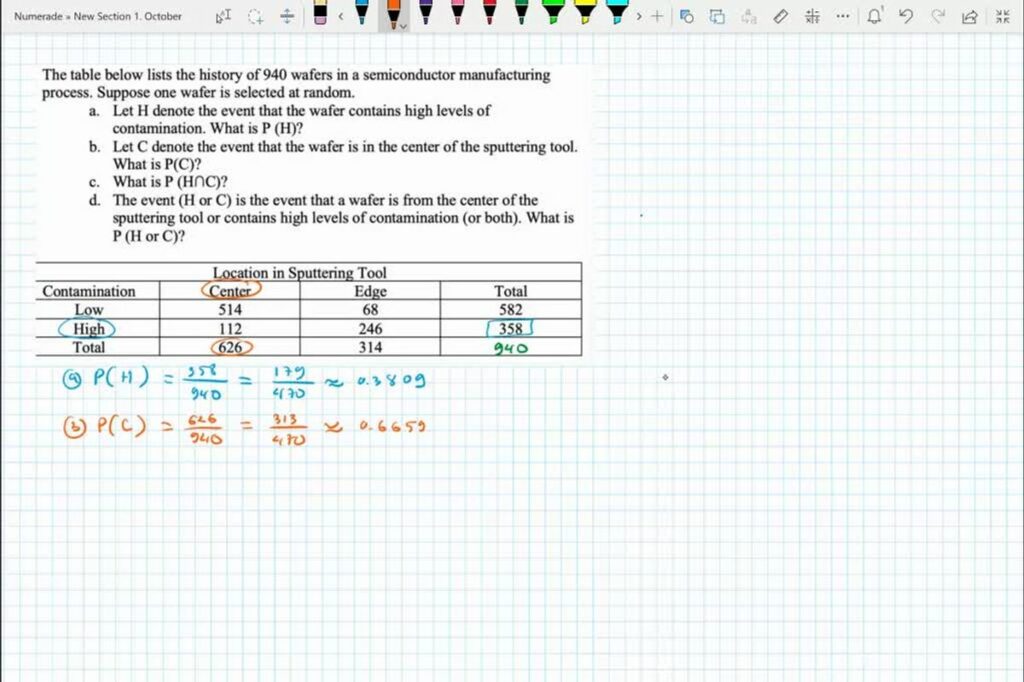
Silicon wafer manufacturing is the cornerstone of modern microprocessor production, a process that transforms raw silicon into the brains of countless electronic devices. This detailed exploration sheds light on the meticulous and technologically advanced procedures involved in creating the integrated circuits (ICs) that power our digital world. From the fundamental steps of wafer fabrication to the cutting-edge techniques in IC development, we delve into the precision, challenges, and innovations that define this fascinating field.
Key Takeaways
- Silicon wafer manufacturing is a complex, multi-step process critical for producing microprocessors with precise and intricate circuitry.
- Techniques such as photolithography, doping, etching, and layering are fundamental to creating the transistor patterns that define a chip’s capabilities.
- Quality control and security measures are essential in ensuring the production of reliable, efficient, and tamper-proof microprocessors.
- Environmental considerations are increasingly important, with a focus on reducing resource consumption, managing hazardous waste, and moving towards sustainable practices.
- The future of IC fabrication is being shaped by advancements in nanotechnology, which promise smaller, more powerful, and energy-efficient components.
The Fundamentals of Silicon Wafer Fabrication
Understanding Silicon as a Semiconductor
Silicon stands at the heart of the semiconductor industry, primarily due to its exceptional electrical properties that can be manipulated to create either conductive or insulating materials. Silicon wafers are central to this industry, serving as the substrate for microprocessors and integrated circuits (ICs). These wafers are thin slices of highly pure crystalline silicon, which undergo a complex manufacturing process to become the foundation of electronic devices.
The versatility of silicon stems from its ability to be doped with impurities to alter its electrical conductivity. This characteristic is crucial for the production of semiconductors, where precise control over electrical properties is necessary. Depending on the application, other materials like gallium arsenide may be used, but silicon remains the most common substrate for its balance of cost, availability, and performance.
Integrated circuits are essentially a set of electronic circuits on a single silicon chip. By embedding components such as transistors, diodes, and capacitors, these chips can perform a wide range of functions. The specific circuitry on an IC determines its role, from simple analog devices to complex microprocessors. The manufacturing process, while sharing basic steps across different ICs, can vary in complexity and cost, reflecting the diversity of applications and technological requirements.
The Step-by-Step Process of Wafer Creation
The journey of a silicon wafer begins with the purification of raw silicon into a highly pure form. This is a critical foundation for the subsequent steps, as impurities can significantly affect the wafer’s performance. Following the purification process, the next step is the creation of a silicon cylinder, known as a Silicon Ingot. The most common method used for this is the Czochralski process, which involves dipping a seed crystal into molten silicon and slowly pulling it out while rotating, allowing the silicon to solidify in a controlled manner.
Once the ingot is formed, it is then sliced into thin discs, which are the wafers themselves. These wafers are polished to a mirror finish, ensuring that the surface is free of any defects that could interfere with the circuitry. The wafers are then ready to undergo further processing, such as photolithography, to create the intricate patterns necessary for integrated circuits.
The entire process requires a high level of precision and cleanliness, as even the smallest particle can disrupt the delicate structures being formed on the wafer. As such, much of the manufacturing takes place in cleanrooms, where the environment is carefully controlled to minimize contamination.
Photolithography: Patterning the Silicon Surface
Photolithography stands as a cornerstone in the manufacturing of integrated circuits, where precision is paramount. This process involves projecting a specific pattern onto the silicon wafer using a light-sensitive chemical called a photoresist. The wafer, coated with this photoresist, is exposed to ultraviolet light through a photomask, which imprints the desired circuit pattern.
Once the exposure is complete, the wafer undergoes a development process where the exposed photoresist is removed, revealing the patterned silicon beneath. This pattern then serves as a guide for subsequent steps such as doping and etching, which further define the intricate electronic pathways necessary for the microprocessor’s functionality.
The accuracy of photolithography is critical, as it directly impacts the efficiency and reliability of the final product. To ensure this precision, manufacturers employ advanced equipment and stringent quality control measures throughout the process.
Advanced Techniques in Microprocessor Manufacturing
Doping: Modifying Electrical Properties
Doping is a critical step in semiconductor device fabrication, where impurities are intentionally introduced to the pure silicon to alter its electrical properties. The process of doping is what transforms silicon into a more efficient semiconductor, capable of conducting electricity under certain conditions. This is essential for creating the p-type and n-type regions that form the building blocks of diodes, transistors, and integrated circuits.
The doping process can be achieved through various methods, such as ion implantation or diffusion. Each method has its own set of parameters that must be carefully controlled to achieve the desired electrical characteristics. For instance, the concentration of dopants, the temperature of the process, and the duration of exposure all play a role in the final outcome.
Method | Dopant Concentration | Temperature | Duration |
---|---|---|---|
Ion Implantation | High | Moderate | Short |
Diffusion | Low to Moderate | High | Long |
The choice of doping method depends on the specific requirements of the semiconductor device being fabricated. It is a delicate balance between achieving optimal electrical properties and maintaining the integrity of the silicon crystal structure. As the industry moves towards nanotechnology, the precision in doping techniques becomes even more crucial, with atomic-level accuracy required for the latest generation of microprocessors and integrated circuits.
Etching and Layering: Building the Circuit Architecture
The etching and layering phase is crucial in defining the intricate pathways that will form the circuit architecture of the microprocessor. Etching involves selectively removing material to create the desired pattern on the silicon wafer, while layering adds different materials to build up the circuit. This process is repeated multiple times to achieve the complex multilayer structures that define modern ICs.
During the etching process, techniques such as wet chemical etching or plasma etching are employed. Each method has its advantages and specific use cases, often determined by the level of precision required and the type of material being etched. For instance, plasma etching allows for finer control and is better suited for creating smaller features.
Layering, on the other hand, involves depositing various materials such as metals, insulators, and semiconductors. These materials are added in thin layers to form the electronic components and their interconnections. The table below summarizes some common materials used in the layering process and their functions:
Material | Function |
---|---|
Silicon Dioxide | Insulator |
Polysilicon | Conductor |
Metal Alloys | Interconnects |
Ensuring the precision of these steps is paramount, as any deviation can lead to defects that compromise the performance of the final product. Manufacturers employ sophisticated monitoring and control systems to maintain the integrity of the IC throughout the fabrication process.
The Role of Nanotechnology in IC Fabrication
Nanotechnology is revolutionizing the field of integrated circuits (ICs) by enabling the manipulation of materials at an atomic or molecular scale. This precision allows for the creation of smaller, more efficient, and powerful microprocessors, paving the way for advancements in various technologies. The application of nanotechnology in IC fabrication is not just about miniaturization; it also enhances performance and reduces power consumption.
The integration of nanotechnology into IC manufacturing processes has led to the development of new fabrication techniques. These include the use of nanomaterials and nanoimprint lithography, which contribute to the production of next-generation microprocessors. The table below outlines some of the key benefits of incorporating nanotechnology into IC fabrication:
Benefit | Description |
---|---|
Size Reduction | Enables further miniaturization of electronic components. |
Performance Increase | Improves processing power and speed. |
Power Efficiency | Reduces energy consumption, leading to longer battery life. |
Innovation Potential | Opens new possibilities for device functionality and applications. |
As the demand for more powerful and energy-efficient devices grows, the role of nanotechnology in IC fabrication becomes increasingly significant. It is a driving force behind the continuous evolution of microprocessors, which are essential for the advancement of future technology, including the Internet of Things (IoT) and sustainable energy solutions.
Quality Control and Assurance in IC Production
Ensuring Precision and Cleanliness
In the realm of integrated circuit (IC) production, ensuring precision and cleanliness is paramount. The intricate nature of microprocessors demands that every step of the manufacturing process is executed with the utmost accuracy. To achieve this, manufacturers employ a variety of cleaning methods to prepare silicon wafers for the subsequent phases of fabrication.
One such method highlighted by WaferPro involves a comprehensive cleaning regimen that includes solvent, RCA, ozone, megasonic, and cryogenic processes. Each technique addresses different contaminants and is critical in maintaining the purity of the wafer surface. For instance, solvent cleaning removes organic residues, while RCA cleaning is effective against metallic and particle contamination.
The importance of these processes cannot be overstated, as even the smallest impurity can lead to defects that compromise the performance of the final product. As a result, manufacturers adhere to strict protocols and utilize advanced equipment to ensure that every wafer meets the industry’s high standards for cleanliness and quality.
Testing for Reliability and Efficiency
Ensuring that integrated circuits (ICs) meet the highest quality standards is critical in the semiconductor industry. Reliability testing serves as a first line of defense against potential faults that could compromise the dependability of electronic devices. This phase involves rigorous procedures to detect and address any deficiencies before the products reach the market.
Performance and power consumption are key metrics in the evaluation of ICs. Devices are increasingly designed with power efficiency in mind, particularly in portable devices where battery life is crucial. Techniques such as power gating help to reduce power consumption, which in turn minimizes heat production and enhances both device longevity and performance.
The following table summarizes the main aspects considered during the testing phase:
Aspect | Importance |
---|---|
Performance | Ensures device meets operational specifications |
Power Consumption | Critical for battery life and heat management |
Longevity | Indicates the expected lifespan of the device |
By adhering to stringent testing protocols, manufacturers can guarantee that their products are not only efficient but also reliable over time, addressing the specific type and complexity of each device.
Security Measures Against Tampering
In the semiconductor industry, the integrity of microprocessors and integrated circuits (ICs) is critical, especially in high-security environments like financial services, healthcare, and government systems. To mitigate risks of unauthorized access to sensitive information, manufacturers have been adopting secure manufacturing processes. These processes are designed to prevent tampering and ensure the integrity of the devices throughout the supply chain.
The industry’s approach to security is multifaceted, involving both hardware and software measures. Secure hardware designs are developed to be resistant to tampering and exploitation, while robust security protocols at the software level protect against vulnerabilities. This ongoing challenge requires advanced technology, industry collaboration, and stringent security practices to maintain data privacy and computing system integrity.
Transparency and responsible disclosure are also key components of security. Companies collaborate with security researchers to proactively identify and address vulnerabilities. When issues are discovered, prompt communication and the implementation of fixes are essential to maintain trust and device security. Recommended reading includes Integrated Circuit Lifecycles and Impact on Security, which provides further insights into these practices.
Environmental Considerations in Semiconductor Manufacturing
Resource Consumption and Waste Management
The production of microprocessors and integrated circuits (ICs) is a resource-intensive endeavor, demanding significant quantities of water, energy, and raw materials. The environmental footprint of these processes is substantial, with the generation of hazardous waste being a primary concern. This waste includes various chemicals and solvents that, if not managed correctly, can pose serious environmental threats.
Efforts to mitigate these impacts have led to the implementation of more sustainable manufacturing practices. Key initiatives include:
- Reducing the use of hazardous materials
- Improving energy efficiency in production processes
- Increasing the recyclability of components
Some companies have taken a step further by adopting closed-loop recycling systems, which allow for the recovery and reuse of materials from discarded devices. This approach not only reduces the demand for new raw materials but also minimizes waste output.
The table below summarizes the key resources consumed in semiconductor manufacturing and the waste management strategies employed:
Resource | Consumption | Waste Management Strategy |
---|---|---|
Water | High | Recycling and purification |
Energy | High | Renewable sources, efficiency improvements |
Raw Materials | Extensive | Closed-loop recycling, material recovery |
Addressing the environmental challenges associated with IC production and disposal requires a collaborative effort from manufacturers, consumers, and policymakers. Through innovation and a commitment to sustainable practices, the industry can reduce its environmental impact and contribute to a more sustainable future.
Hazardous Chemicals and Solvent Handling
The manufacturing of microprocessors and integrated circuits is a resource-intensive endeavor, demanding significant quantities of water, energy, and raw materials. This process not only consumes valuable resources but also produces hazardous waste, including various chemicals and solvents. Proper handling and disposal of these substances are crucial to prevent environmental contamination and ensure the safety of ecosystems.
In the face of these environmental challenges, the electronics industry has initiated a shift towards more sustainable practices. Efforts are being made to reduce the use of hazardous materials, enhance energy efficiency, and improve the recyclability of components. Some notable measures include:
- Adoption of closed-loop recycling systems to recover materials from discarded devices.
- Implementation of strategies to minimize waste generation during production.
- Development of new, less harmful chemical processes.
Despite these advancements, the disposal of electronic devices remains a pressing concern. E-waste, rich in toxic substances like lead and mercury, poses significant health risks when improperly managed. The industry’s response to these issues is multifaceted, involving innovation in manufacturing processes, consumer awareness, and robust policy frameworks to guide sustainable practices.
Advancements Towards Sustainable Practices
In the quest for sustainable semiconductor manufacturing, the electronics industry has made significant strides. Initiatives aimed at reducing hazardous materials, enhancing energy efficiency, and promoting the recyclability of components are at the forefront of these efforts. Notably, some companies have implemented closed-loop recycling systems, which not only curb the need for new raw materials but also diminish waste generation.
The design philosophy is also shifting towards products that are built to last and can be easily repaired. This approach is instrumental in prolonging device lifespans and minimizing e-waste. Such sustainable practices are increasingly becoming a part of regulatory frameworks, which advocate for responsible e-waste disposal and the advancement of eco-friendly technologies.
Addressing the environmental ramifications of IC production is a multifaceted challenge. It demands a collaborative approach involving manufacturers, consumers, and policymakers. Through innovation and a commitment to sustainable methods, the industry can lessen its ecological footprint and contribute to a greener future.
The Evolution and Future of Integrated Circuits
Historical Milestones in IC Development
The semiconductor industry has witnessed a series of revolutionary milestones that have dramatically transformed the landscape of technology. From the invention of the first functional IC by Jack S. Kilby in 1958 to the development of multi-core processors in the early 2000s, each advancement has been pivotal in shaping today’s digital world.
The 1980s and 1990s were particularly notable for the rapid advancements in microprocessor speed and power, adhering to Moore’s Law which suggested a doubling of transistors on a microchip approximately every two years. This era also saw the diversification of ICs into specialized types such as microcontrollers and digital signal processors.
- 1958: Jack S. Kilby presents the first functional IC
- 1978: Introduction of Intel 8086, the basis for x86 architecture
- Early 2000s: Arrival of multi-core processors
- Ongoing: Development of complex ICs for telecommunications, like Qualcomm Snapdragon series
Emerging Trends in Microprocessor Design
The relentless pursuit of enhanced computing capabilities has led to groundbreaking trends in microprocessor design. Quantum computing chips represent a significant leap forward, utilizing quantum mechanics to vastly outpace traditional processors in complex calculations. This innovation holds potential for transformative impacts across various sectors, including cryptography and pharmaceuticals.
Energy efficiency has become a paramount concern as devices proliferate and their demands escalate. Strides in reducing power consumption are pivotal, not only for prolonging battery life but also for mitigating heat output, which in turn boosts device longevity and performance.
The evolution from single-core to multi-core processors marks a notable trend in the quest for speed. Multi-core technology enables simultaneous execution of multiple instructions, enhancing processing power and efficiency. Companies like AMD are at the forefront of this advancement, continually pushing the boundaries of processor architecture.
- Quantum Computing Chips
- Energy Efficiency Optimization
- Multi-Core Processor Development
These trends underscore the dynamic and ever-progressing nature of microprocessor technology, as designers strive to meet the growing demands for speed, efficiency, and versatility in computing.
The Impact of Electronic Waste and Recycling Initiatives
The rapid technological advancements and the resulting short lifespan of electronic devices have led to a significant increase in electronic waste (e-waste). E-waste management has become a critical environmental challenge, as microprocessors and integrated circuits (ICs) contain harmful substances like lead, mercury, and cadmium, which pose health risks when they leach into the environment.
In response to these concerns, the electronics industry has been adopting more sustainable practices. Key initiatives include:
- Reducing hazardous material use
- Improving energy efficiency in production
- Enhancing the recyclability of components
Some companies have implemented closed-loop recycling systems, which recover materials from discarded devices to manufacture new ones. This approach not only minimizes waste but also lessens the demand for raw materials.
Moreover, there is an increasing focus on designing products for longevity and repairability. This aims to extend the lifespan of devices, thereby reducing e-waste generation. Such efforts are often supported by regional regulations that mandate responsible e-waste disposal and recycling, fostering the development of environmentally friendlier technologies.
Addressing the environmental impact of IC production and disposal requires a collaborative effort from manufacturers, consumers, and policymakers. Through innovation and commitment to sustainable practices, the industry can reduce its environmental footprint and contribute to a more sustainable future.
Conclusion
The journey through the intricate world of silicon wafer manufacturing reveals a process that is as complex as it is critical to the modern digital landscape. From the initial design to the final product, each step of manufacturing microprocessors and integrated circuits (ICs) demands precision, advanced technology, and a commitment to quality. While the environmental impact of this process cannot be overlooked, ongoing advancements, such as the integration of nanotechnology, hold the promise of more efficient and sustainable production methods. As we continue to push the boundaries of what is possible in silicon wafer manufacturing, we pave the way for future innovations that will further transform our technological capabilities.
Frequently Asked Questions
What are the main steps involved in silicon wafer manufacturing?
The main steps include photolithography, doping, etching, and layering to create intricate patterns of transistors and connections on the chip.
Why is the fabrication process for microprocessors so complex and costly?
The process is complex and costly due to the high level of precision and cleanliness required to produce reliable and efficient microprocessors.
How do the complexity and cost of manufacturing vary among different types of ICs?
Simple ICs, such as basic analog devices, may be cheaper and less complex to manufacture than microprocessors or highly specialized custom ICs.
What environmental challenges are associated with the production and disposal of microprocessors and ICs?
The challenges include substantial resource consumption, generation of hazardous waste, and the handling of chemicals and solvents that can harm the environment if not managed properly.
How does nanotechnology influence the future of microprocessor and IC fabrication?
Nanotechnology allows for manipulation of materials on an atomic or molecular scale, leading to smaller, more powerful, and energy-efficient components, which opens new possibilities for innovation.
What measures are taken to ensure the security and integrity of microprocessors during manufacturing?
Secure manufacturing processes are implemented to prevent tampering and ensure the integrity of microprocessors and ICs throughout the supply chain.