Essential Automation Equipment for Modern Production Lines
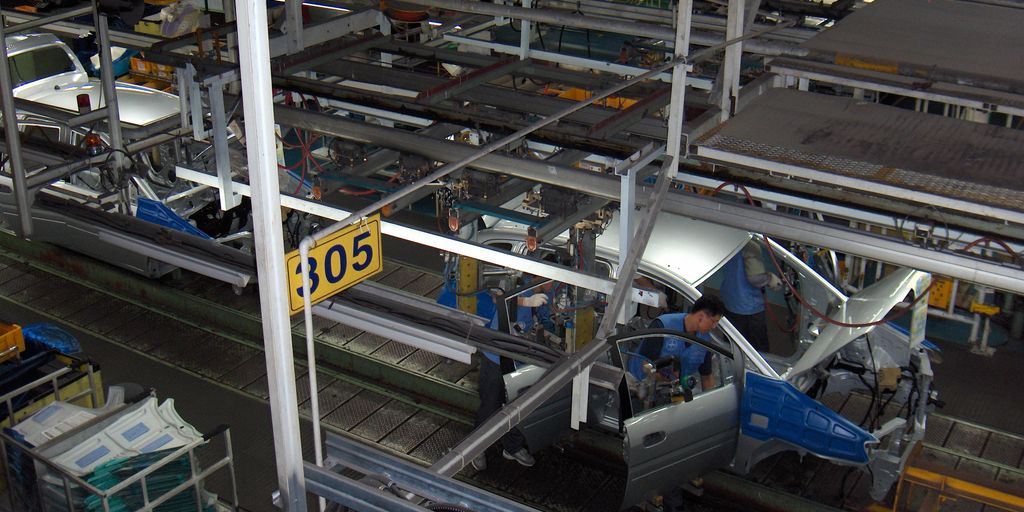
Automation equipment is pivotal in enhancing the efficiency and productivity of modern production lines. These systems range from simple standalone machines to complex, integrated solutions that handle everything from material handling to final quality control with minimal human intervention. Understanding the essential automation equipment helps in optimizing production processes and achieving higher throughput with greater precision.
Key Takeaways
- Automation equipment includes standalone machines, complex systems, and programmable elements that reduce the need for manual intervention.
- Single automated machines can be strategically placed in production lines to target specific efficiency improvements.
- Automated production lines handle entire manufacturing processes, significantly reducing manual tasks and errors while increasing output.
- End-to-end automation solutions are particularly prevalent in industries like automotive, where they streamline everything from assembly to painting.
- Flexible and integrated automation systems adapt to changing production demands, allowing for automated changeovers and increased customization.
Overview of Automation Equipment
Definition and Components
Automation equipment encompasses a range of machines, robots, and applications designed to minimize human intervention in production or warehouse activities. Key components include automated storage and retrieval systems (ASRS), sortation devices, and conveyors, which are integral to modern industrial operations.
Types of Automation Equipment
There are various types of automation equipment tailored for different industries, including automotive, agricultural, and food and beverage processing. Each type is designed to enhance efficiency and streamline operations in specific sectors.
Benefits in Production Lines
Automation significantly enhances production efficiency by reducing manual labor and increasing consistency across operations. Benefits include:
- Greater control and precision
- Lower operating costs
- Improved product quality
- Increased production speeds
Single Automated Machines
Single automated machines represent a more focused approach to automation, where individual machines within a manufacturing setup are equipped with automation features. These machines are designed to perform specific tasks with a high degree of precision and efficiency.
Strategic Placement
Single automated machines are versatile and can be strategically placed within a production line to optimize efficiency in targeted areas. This type of automation is particularly suitable for processes that require specialized attention or where the integration of a comprehensive automated system doesn’t make sense.
Versatility in Production
These systems play a key role in achieving precision, consistency, and speed in manufacturing. By relying on Automated Manufacturing Systems, industries can ensure the seamless coordination of different components, leading to enhanced overall efficiency.
Optimization of Efficiency
The strategic placement and versatility of single automated machines allow for significant improvements in production efficiency. They are essential in processes that demand high precision and consistent output, making them invaluable in sectors like pharmaceuticals, robotics, and semiconductors.
Automated Production Lines
Complex Manufacturing Processes
Automated production lines excel in handling complex manufacturing processes. From the initial input of raw materials to the final assembly of the product, each step is meticulously controlled and executed by automated systems, ensuring precision and consistency.
Reduction of Manual Intervention
The integration of automated systems significantly reduces manual intervention. This shift not only enhances safety by minimizing human interaction with machinery but also boosts overall operational efficiency. The use of programmable logic controllers (PLCs) ensures that each operation is executed with exact timing and sequence, further reducing the likelihood of errors.
Increased Production Volumes
By streamlining processes and reducing downtimes, automated production lines are capable of achieving higher production volumes. This efficiency is crucial for industries aiming to meet high demand while maintaining quality. The synchronization of various stations within the production line ensures a continuous and smooth flow of operations, leading to optimal output rates.
End-to-End Automation Solutions
Automotive Industry Applications
End-to-end automation solutions are revolutionizing the automotive industry by integrating advanced technologies like AI and IoT. This integration enhances the entire production process, from design to assembly, ensuring high precision and efficiency.
Material Handling and Conveyor Systems
These systems are crucial in automating the movement and management of materials throughout the factory. They reduce human error and significantly improve the speed and efficiency of production processes.
Paint, Coating, and Welding Stations
End-to-end automation extends to specialized stations such as painting, coating, and welding. Automated systems in these areas ensure consistent quality and faster production times, while also improving worker safety by reducing exposure to hazardous conditions.
Programmable Automation
Role in Production Efficiency
Programmable automation systems are pivotal in enhancing production efficiency by allowing precise control over manufacturing processes. These systems can be reprogrammed to adapt to new production requirements, ensuring continuous operation without significant downtime for adjustments.
Cost Reduction and Insight
The implementation of programmable automation significantly reduces operational costs by minimizing manual labor and enhancing process efficiency. Additionally, it provides valuable insights into production metrics, which can be leveraged for further optimizations.
Upgrading Manufacturing Processes
Programmable automation facilitates the upgrading of manufacturing processes by introducing flexibility and scalability. This is particularly beneficial in environments where product specifications frequently change, allowing for quick reconfiguration of production lines to accommodate new products or variants.
Industrial Automation Systems
Comprehensive System Upgrades
Industrial automation systems represent a significant upgrade over traditional manual operations, integrating advanced technologies to enhance control and efficiency across various sectors. These systems can range from simple controllers to complex SCADA systems that manage processes across different locations and technological layers.
Benefits of Smarter Facilities
Industrial automation transforms facilities into smarter environments, enhancing operational control and reducing costs. This shift not only improves quality and efficiency but also accelerates production times, making facilities more responsive to market demands.
Improving Quality and Efficiency
The implementation of industrial automation systems is crucial for improving both quality and efficiency in production processes. Examples of automation in action include warehouse automation, material handling, packaging, and quality control, all contributing to safer and more productive operations.
Equipment in Factory Automation
Vision and Imaging Systems
Vision and imaging systems are crucial in modern factory automation, providing the necessary data for precise control and monitoring of production processes. These systems include cameras, lenses, and advanced image processing software, which are essential for tasks such as quality control and robotic guidance.
Material Handling and Assembly
Material handling and assembly processes in factory automation are significantly enhanced by automated equipment. This includes conveyors, robotic arms, and automated storage and retrieval systems (ASRS), which streamline the movement and assembly of products, reducing manual labor and improving efficiency.
Quality Control and Inspection
In factory automation, quality control and inspection are paramount. Automated vision systems, sensors, and testing equipment play a key role in detecting defects and ensuring product quality. This automation enables continuous improvement in manufacturing processes, leading to higher standards and fewer errors.
Flexible and Integrated Automation
Adapting to Production Demands
Flexible automation systems are designed to adapt to changes in product design and production requirements. These systems can be easily reprogrammed or modified to perform different tasks, making them suitable for low-volume production lines with a high degree of customization.
Automated Changeovers
Changeovers can be performed automatically, reducing downtimes. This is particularly beneficial in environments where batch production is prevalent but also allows for more on-demand production and increased customization.
Customization and Batch Production
Flexible automation is essential for industries that require the ability to switch between different product types without extensive downtime or reprogramming. This capability supports a more dynamic production schedule and enhances the ability to meet specific customer demands.
Conclusion
In the rapidly evolving landscape of industrial production, the integration of essential automation equipment is pivotal for enhancing efficiency and scalability. From single automated machines that target specific processes to comprehensive automated production lines that handle everything from raw material to finished product, the benefits are substantial. These systems not only minimize manual intervention but also boost production volumes and reduce errors. As industries strive to meet increasing demands and maintain competitive edges, investing in advanced automation technologies—be it flexible, programmable, or end-to-end solutions—becomes indispensable. This adoption not only streamlines operations but also significantly cuts costs and improves overall product quality, making it a crucial step for any modern production line.
Frequently Asked Questions
What is automation equipment?
Automation equipment includes machines, robots, and applications such as conveyors and special devices used to automate production or warehouse activities with minimal human intervention.
What are the benefits of using automated production lines?
Automated production lines handle complex manufacturing processes, reduce the need for manual intervention, minimize errors, and increase production volumes, thereby enhancing overall efficiency.
How does programmable automation improve manufacturing processes?
Programmable automation allows for the upgrading of facilities, reducing costs, and providing better insights into expenses, manufacturing processes, and production rates.
What types of equipment are used in factory automation?
Factory automation uses equipment like cameras, image-capture equipment, conveyors, robotics, and quality control systems among others.
What is the role of industrial automation systems?
Industrial automation systems upgrade the entire facility, making it smarter and more efficient, which leads to lower operating costs, improved quality, and faster production times.
How does flexible automation adapt to production demands?
Flexible automation involves precise electromechanical controls for quick changeovers, reducing downtime, and allowing for increased product customization and batch production.