How Wafer Size Impacts the Efficiency of Semiconductor Manufacturing
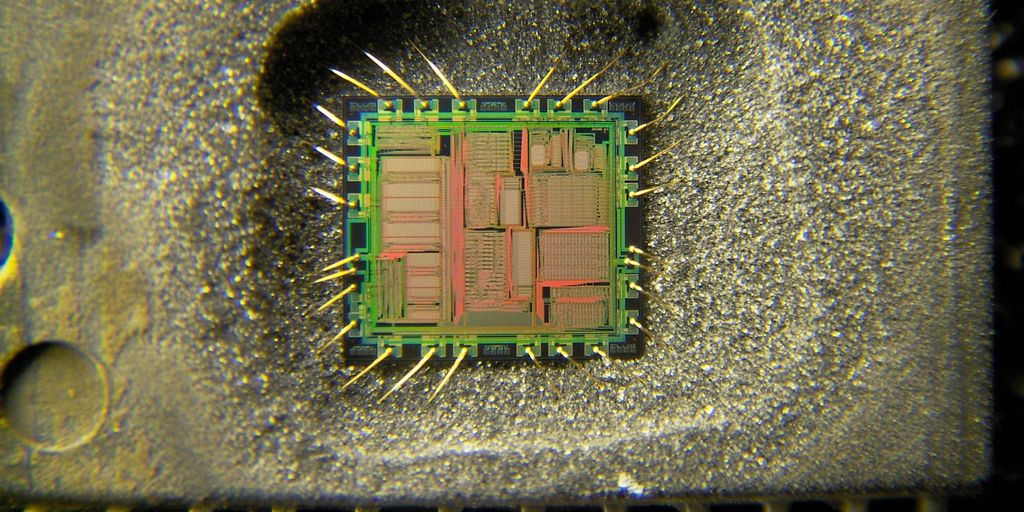
The role of wafer size in semiconductor manufacturing is pivotal, influencing various aspects from production efficiency to cost implications. As the industry evolves, understanding how wafer size impacts the manufacturing process and the strategic decisions behind its selection is essential for optimizing operational efficiency and staying competitive.
Key Takeaways
- Wafer size directly influences the number of chips produced, affecting overall manufacturing efficiency and cost per chip.
- Larger wafer sizes, such as 450 mm and 675 mm, are currently being discussed within the industry to further increase production efficiency and reduce costs.
- The decision to select a wafer size is strategically driven, considering both investment and operational implications over a span of five to ten years.
- Technological and operational considerations dictate the choice of wafer size, balancing between technical feasibility and economic viability.
- Future trends in wafer size will continue to impact the semiconductor industry, necessitating ongoing research and adaptation to new standards.
Understanding Wafer Size in Semiconductor Manufacturing
Overview of Wafer Sizes
Wafer sizes in semiconductor manufacturing have evolved significantly, primarily driven by the need for more chips per wafer and greater cost efficiency. Currently, the standard wafer diameter is 300mm, or about 12 inches, although 450mm wafers are in development. The thickness of the wafer is typically a few millimeters, optimized for handling and processing.
Role of Wafer Size in Chip Production
The size of the wafer directly influences the number of chips that can be produced on a single wafer. Larger wafers allow for more chips to be manufactured, thereby increasing the output and reducing the cost per chip. This scalability is crucial for meeting the growing demands of advanced semiconductor applications.
Strategic Decisions Behind Wafer Size Selection
Selecting the appropriate wafer size is a strategic decision that involves balancing technical capabilities and economic considerations. Most semiconductor facilities have focused on 200 mm wafers since they allow for the balance of both the technical and business aspects. However, the shift towards 300 mm wafers is evident due to their ability to produce more operational chips and reduce costs per die, making them a more economically viable option in the long run.
Economic Implications of Wafer Size Choices
Cost Analysis of Different Wafer Sizes
The choice of wafer size significantly influences the overall cost of semiconductor manufacturing. Larger wafers, such as the 300 mm, often lead to higher initial costs but can provide economies of scale if the yield rates are managed effectively. Conversely, smaller wafers like the 200 mm are cheaper to produce but may result in higher per-unit costs due to lower throughput.
Investment Considerations
Investing in new wafer sizes involves considerable capital expenditure. Companies must weigh the benefits of increased production capacity and potentially lower costs per chip against the significant upfront investments in new equipment and technology adaptations.
Impact on Production Costs
The impact of wafer size on production costs extends beyond the cost of the wafer itself. It includes the costs associated with fabrication (FAB) and Outsourced Semiconductor Assembly and Test (OSAT). Here’s a simplified breakdown:
Wafer Size | FAB Cost | OSAT Cost |
---|---|---|
200 mm | Low | Moderate |
300 mm | High | High |
Larger wafers can lead to increased efficiency and lower long-term costs, but they require substantial initial investments and careful management of yield rates to be economically viable.
Technological Advancements and Wafer Size
Innovations in Wafer Manufacturing
The semiconductor industry has seen significant innovations in wafer manufacturing, particularly with the adoption of advanced techniques like Extreme Ultraviolet (EUV) Lithography. This method allows for smaller feature sizes on chips, enhancing the overall chip production efficiency.
Adaptation to Larger Wafer Sizes
As the industry shifts towards larger wafer sizes, such as the transition from 200mm to 300mm, the benefits become evident. This change has not only improved production yields but also reduced the cost per wafer, making large-scale manufacturing more feasible.
Challenges with Increasing Wafer Size
While the shift to larger wafers offers numerous advantages, it also presents unique challenges. These include the need for more sophisticated equipment and the potential for increased defects, which can impact the quality of the wafers. Managing these challenges is crucial for maintaining high standards in semiconductor manufacturing.
Operational Efficiency and Wafer Size
Improvements in Manufacturing Efficiency
By utilizing larger wafer sizes, semiconductor manufacturers can significantly enhance their operational efficiency. This is primarily because larger wafers allow for more chips to be produced on a single wafer, reducing the number of production cycles needed for the same quantity of chips.
Scaling Production with Wafer Size
As wafer sizes increase, the ability to scale production becomes more feasible. Larger wafers mean that more units can be processed simultaneously, which not only speeds up the manufacturing process but also reduces the cost per unit, making large-scale operations more economically viable.
Quality Control in Larger Wafers
While larger wafers offer many benefits, they also present unique challenges in terms of quality control. Ensuring the consistency and reliability of chips produced from larger wafers requires advanced monitoring and testing techniques. This is crucial as any defects can affect a larger batch of chips, potentially leading to higher costs and delays.
Strategic Impact of Wafer Size on the Semiconductor Industry
Market Trends Influencing Wafer Size
The semiconductor industry’s shift towards larger wafer sizes, such as the transition from 8 inches to 12 inches, is largely influenced by market demands for higher efficiency and lower costs. This trend is driven by the need to produce more chips per wafer, enhancing overall production efficiency.
Competitive Advantage through Wafer Size
Adopting larger wafer sizes can provide a significant competitive advantage. Companies that transition to larger wafers can achieve lower per-unit costs and improved yield, making them more competitive in the market. This strategic decision is often influenced by the potential for increased market share and profitability.
Future Projections for Wafer Sizes
Predictions indicate a continued trend towards larger wafer sizes in the semiconductor industry. The ongoing advancements in technology and manufacturing processes suggest that we may see the adoption of even larger wafers than the current 300mm standard. This progression will likely have profound implications for the semiconductor ecosystem, influencing everything from production strategies to market dynamics.
Case Studies: Wafer Size Optimization
Examples from Leading Semiconductor Firms
Several leading semiconductor firms have demonstrated the strategic importance of optimizing wafer size. For instance, a transition from 200 mm to 300 mm wafers by a prominent firm resulted in a 25% increase in productivity and significant cost savings. This shift not only optimized their manufacturing processes but also enhanced their competitive position in the market.
Lessons Learned in Wafer Size Expansion
The expansion to larger wafer sizes, such as the shift towards 450 mm, has not been without challenges. Key lessons include the necessity for substantial upfront investment and the need for alignment with equipment manufacturers to ensure readiness. The benefits, however, often outweigh the initial hurdles, leading to greater efficiencies and lower per-unit costs over time.
Innovative Approaches to Wafer Utilization
Innovative approaches to wafer utilization involve not just increasing the size but also improving the layout and design to maximize yield. Techniques such as multi-patterning and advanced lithography have been pivotal. These innovations allow for more dies per wafer, significantly reducing waste and enhancing overall yield efficiency.
The Future of Wafer Sizes in Semiconductor Manufacturing
Predictions on Wafer Size Trends
The semiconductor industry is poised for significant changes in wafer size trends over the next decade. As the demand for more powerful and efficient chips grows, manufacturers are likely to continue pushing the boundaries of current wafer sizes. The industry might see a rise in the production capacity of 8-inch wafers, as well as a gradual shift towards larger sizes like 300 mm and potentially 450 mm.
Potential for New Wafer Sizes
Exploring the potential for new wafer sizes reveals a strategic and investment-heavy landscape. The decision to adopt new wafer sizes involves careful consideration of production costs, technological feasibility, and market demand. Future facilities may focus on even larger wafers, such as 675 mm, to drive down costs and enhance production efficiency.
Implications for the Semiconductor Ecosystem
The implications of changing wafer sizes extend far beyond simple manufacturing concerns. They impact the entire semiconductor ecosystem, including supply chain dynamics, equipment manufacturers, and end-user industries. As wafer sizes evolve, the industry must adapt to these changes, ensuring that all stakeholders are prepared for the shifts in technology and market demands.
Applications of Different Sized Silicon Wafers
Use Cases in Various Industries
Different sized silicon wafers are utilized across various industries, each with specific requirements that dictate the optimal wafer size. For instance, the automotive industry often uses larger wafers for more complex integrated circuits, while mobile devices may require smaller, more compact wafers to fit into limited spaces.
Benefits of Specific Wafer Sizes
The benefits of specific wafer sizes are closely tied to production efficiency and cost-effectiveness. Larger wafers, such as the 300mm, allow for more chips per wafer, reducing the cost per chip and enhancing production throughput. This is particularly beneficial in high-volume industries like consumer electronics.
Technological Constraints and Opportunities
While larger wafers offer significant advantages in terms of production scale and cost reduction, they also present unique challenges. The transition to larger wafers requires substantial investment in new manufacturing technologies and equipment. However, this also opens up opportunities for innovation in wafer fabrication and handling techniques, potentially leading to breakthroughs in semiconductor manufacturing.
Conclusion
In conclusion, the size of the wafer plays a pivotal role in the efficiency of semiconductor manufacturing. Larger wafers allow for more chips per batch, which not only enhances production efficiency but also reduces the cost per chip, making it a strategic choice for manufacturers. As the industry continues to evolve, the decision on wafer size will remain a critical factor, influenced by both economic and strategic considerations. This understanding is essential for stakeholders in the semiconductor industry as they plan for future developments and investments.
Frequently Asked Questions
What factors are considered when selecting a wafer size for semiconductor manufacturing?
Factors such as cost, yield, and the strategic and investment implications are crucial in determining the wafer size. These factors ensure the balance between technical capabilities and business objectives.
How does wafer size impact the efficiency of semiconductor manufacturing?
Larger wafer sizes can produce more chips per batch, enhancing operational efficiency and reducing the cost per die. This results in lower semiconductor production costs and improved supply chain dynamics.
What are the current trends in wafer sizes in the semiconductor industry?
The industry is exploring larger wafer sizes, such as 450 mm and potentially 675 mm, to increase efficiency and output. These sizes are still under discussion and research for practical implementation.
What is the role of wafer size in cost management within semiconductor manufacturing?
Wafer size directly influences the cost per chip by determining how many dies can be fabricated on a single wafer. Larger wafers allow for more dies, reducing the overall production costs and enhancing economic efficiency.
What are the technological challenges associated with increasing wafer size?
Scaling up wafer size involves challenges such as the need for new equipment, adjustments in manufacturing processes, and maintaining quality control over a larger surface area, which can increase initial investment costs.
How far in advance do semiconductor manufacturing facilities plan for wafer size changes?
Facilities typically plan and determine which wafer sizes to support for the next five to ten years, considering the significant expenses and strategic planning required for each wafer size upgrade.