A Deep Dive into the Semiconductor Manufacturing Process
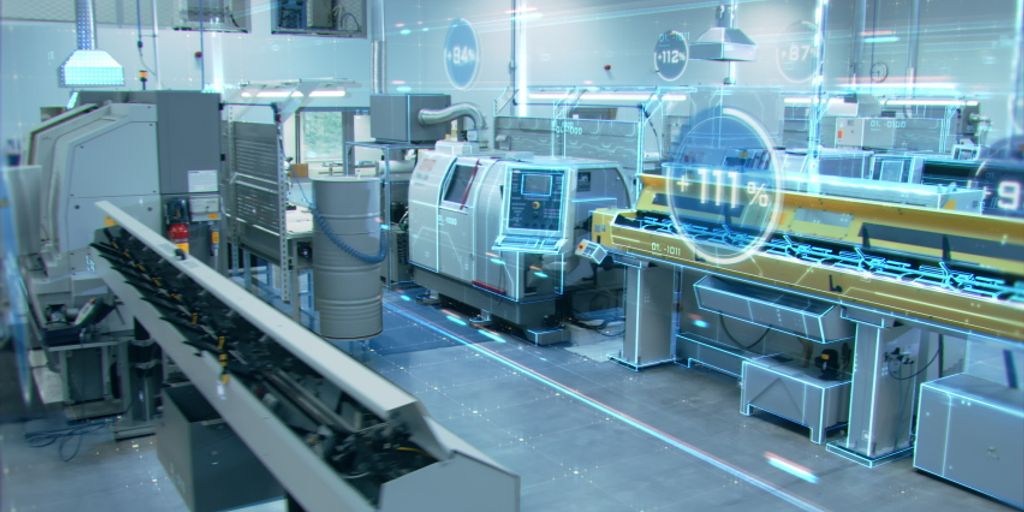
The semiconductor manufacturing process is a marvel of modern engineering, encompassing a multitude of intricate steps to transform raw silicon into the powerful microchips that drive our electronic devices. From the initial formation of silicon ingots to the final assembly and packaging of semiconductors, each stage requires precision, control, and a deep understanding of material science. This article will take you through the key stages of semiconductor manufacturing, shedding light on the complexities and technologies that make it all possible.
Key Takeaways
- Semiconductor manufacturing involves highly sophisticated processes, starting from raw silicon wafer production to final assembly and packaging.
- Photolithography is a critical step in defining the intricate circuit patterns on the silicon wafer.
- Doping processes such as ion implantation and diffusion are essential for modifying the electrical properties of the semiconductor.
- Various deposition techniques, including Chemical Vapor Deposition (CVD) and Physical Vapor Deposition (PVD), are used to add layers to the wafer.
- Maintaining cleanroom standards is crucial to prevent contamination and ensure the quality and reliability of semiconductor products.
The Intricacies of Wafer Production
The process of puzzling out the fabrication process of silicon wafers is fundamental to semiconductor manufacturing. Silicon wafers, the cornerstone of contemporary electronics, undergo a methodical evolution from raw materials to intricate semiconductor components. This journey begins with the formation of a silicon ingot, followed by precise slicing and polishing, and concludes with thorough cleaning to ensure a pristine surface for subsequent steps.
Photolithography: Crafting Circuit Patterns
Photolithography is a key process in the semiconductor industry that involves transferring patterns onto a substrate using light. This technique is crucial for defining the intricate circuit patterns on a chip. The process begins with the application of a photoresist layer, which is sensitive to ultraviolet light.
Photoresist Application
The lithography process starts with the application of photoresist, a light-sensitive material, onto the wafer. This layer is essential for creating the desired patterns during the exposure step.
Exposure and Development
During this stage, the chip wafer is inserted into a lithography machine where it’s exposed to deep ultraviolet (DUV) or extreme ultraviolet (EUV) light. The light has a wavelength ranging from 365 nm for less complex designs to 13.5 nm for advanced patterns. The photoresist is developed and removed at the pattern marked by the lithography.
Etching Techniques
The exposed oxide is then etched, typically with reactive ion etching, which generates ions in a plasma and accelerates them onto the surface. The ions react with the oxide material and also remove oxide material directly through kinetic energy. This step is crucial for defining the final circuit patterns on the wafer.
Doping: Modifying Electrical Properties
Doping in semiconductor production is the intentional introduction of impurities into an intrinsic (undoped) semiconductor for the purpose of modulating its electrical properties. This process is crucial for creating the P-type and N-type regions that are essential for semiconductor functionality.
Ion Implantation
Ion implantation involves bombarding the wafer with positive or negative ions to tune the electrical conducting properties of specific regions. This process allows the flow of electricity to be controlled, enabling the creation of transistors, which are the basic building blocks of microchips.
Diffusion Processes
In diffusion processes, dopant atoms are introduced to the silicon wafer at high temperatures, allowing them to diffuse into the crystal lattice. This method is used to create well-defined regions with specific electrical properties.
Annealing
Annealing is a thermal process used to repair damage to the silicon crystal lattice caused by ion implantation. It also helps to activate the dopant atoms, ensuring they are correctly positioned within the lattice to achieve the desired electrical characteristics.
Layer Deposition Techniques
Layer deposition techniques are essential in semiconductor manufacturing, enabling the creation of various layers on a silicon wafer. These techniques can be broadly categorized into three main types: Chemical Vapor Deposition (CVD), Physical Vapor Deposition (PVD), and Atomic Layer Deposition (ALD).
Chemical Vapor Deposition (CVD)
Chemical Vapor Deposition is a technique used for forming a solid coating on the wafer by passing a gas flow over the wafer surface. This process is highly versatile and can be used to deposit a wide range of materials, including insulators, conductors, and semiconductors. CVD is crucial for creating uniform layers that are essential for the subsequent steps in semiconductor manufacturing.
Physical Vapor Deposition (PVD)
Physical Vapor Deposition involves the physical transfer of material from a source to the wafer. This is typically achieved through methods such as sputtering or evaporation. PVD is particularly useful for depositing metals and other conductive materials. The process is generally faster than CVD but may not provide the same level of uniformity.
Atomic Layer Deposition (ALD)
Atomic Layer Deposition (ALD) used to be considered too slow to be of practical use in semiconductor manufacturing, but it has emerged as a critical tool for enabling advanced devices with atomic layer processes. ALD allows for the deposition of extremely thin and uniform layers, making it ideal for applications requiring high precision and control. The process involves the sequential use of gas phase chemical reactions to deposit material one atomic layer at a time.
Assembly and Packaging of Semiconductors
Once the semiconductor components are fabricated on wafers, they move to the assembly and packaging stage. Here, individual chips are cut, tested, and encapsulated into protective packages that make them ready for integration into electronic devices. Packaging is an essential part of semiconductor manufacturing and design. It affects power, performance, and cost on a macro level.
Die Bonding
Die bonding is the process of attaching the semiconductor die to a substrate or package. This step is crucial as it ensures the mechanical stability and electrical connectivity of the chip. Various techniques, such as epoxy bonding and eutectic bonding, are used depending on the application requirements.
Wire Bonding
Wire bonding involves creating electrical connections between the semiconductor die and the package leads using fine wires. This process is typically performed using gold or aluminum wires and is essential for the functionality of the final semiconductor device. Wire bonding is favored for its flexibility and reliability.
Encapsulation
Encapsulation is the final step in the assembly and packaging process. It involves sealing the semiconductor die and wire bonds in a protective material, usually a type of epoxy resin. This step is vital for protecting the delicate components from environmental factors such as moisture, dust, and mechanical stress.
Ensuring Quality: Inspection and Testing
Ensuring the quality and reliability of semiconductors is paramount in the manufacturing process. This involves a series of rigorous inspection and testing procedures to identify and rectify any defects or inconsistencies.
Maintaining Cleanroom Standards
One distinctive aspect of semiconductor manufacturing is the requirement for cleanroom environments. These facilities are meticulously controlled to minimize dust, contaminants, and particles that could compromise the quality of semiconductor components. Semiconductor manufacturing typically falls within ISO classes 1 through 5, where the air is meticulously filtered to maintain cleanliness.
Contamination Control
One of the major challenges of construction is maintaining clean construction protocols. Dust can get trapped within walls, panels, air ducts and get released into the cleanroom later due to building vibration, which can cause considerable manufacturing defects in produced chips. To avoid these issues, semiconductor companies have to use special construction companies with experience in clean protocols, which require early partitioning of building spaces and repeated cleaning of materials throughout.
Air Filtration Systems
Cleanroom environments rely heavily on advanced air filtration systems to maintain their stringent standards. These systems are designed to filter out even the smallest particles, ensuring that the air remains free of contaminants. The circulation of air typically goes from ceiling to floor and is cycled back into the cleanroom, maintaining a continuous flow of clean air.
Personnel Protocols
Despite strict cleanroom protocols and attire, cleanroom operators can inadvertently introduce particulate contamination. Monitoring the points where operators interact with wafers is essential to ensure a clean working environment. Air particle counters can help track any particulate shedding by operators. Personnel must follow rigorous protocols, including wearing specialized clothing and undergoing regular training to minimize contamination risks.
Conclusion
The semiconductor manufacturing process is a marvel of modern engineering, encompassing a multitude of intricate steps and requiring meticulous attention to detail. From the initial wafer fabrication to the final assembly and packaging, each phase is critical to ensuring the functionality and reliability of the integrated circuits that power our electronic devices. Beyond the core steps, additional processes such as measurement, inspection, and testing play vital roles in maintaining quality and performance. As technology continues to advance, the complexity and precision of semiconductor manufacturing will only increase, making it an ever-evolving field that remains at the forefront of innovation. For those intrigued by the world of chipmaking, there is always more to explore and discover in this fascinating industry.
Frequently Asked Questions
What is semiconductor manufacturing?
Semiconductor manufacturing is a critical industry that manufactures integrated circuits. These are sets of electronic circuits on a semiconductor material, typically made from silicon. The process is highly sophisticated and involves multiple steps to create functional semiconductor devices.
Why is contamination control important in semiconductor manufacturing?
Contamination control is paramount in semiconductor manufacturing because unmonitored contamination can significantly impact product yield and quality. Keeping the products free from contamination ensures higher efficiency and reliability of the final semiconductor devices.
What are the primary steps in the semiconductor manufacturing process?
The primary steps in semiconductor manufacturing include wafer production, photolithography, doping, layer deposition, assembly and packaging, and inspection and testing. Each of these steps involves specific techniques and processes to create integrated circuits on silicon wafers.
What is photolithography in semiconductor manufacturing?
Photolithography is a process used in semiconductor manufacturing to craft circuit patterns on silicon wafers. It involves applying a photoresist, exposing it to light to create a pattern, and then developing and etching the pattern onto the wafer.
How are electrical properties modified in semiconductors?
The electrical properties of semiconductors are modified through a process called doping. This involves introducing impurities into the silicon wafer through methods like ion implantation and diffusion processes, followed by annealing to activate the dopants.
What is the role of cleanrooms in semiconductor manufacturing?
Cleanrooms play a crucial role in semiconductor manufacturing by maintaining a controlled environment that minimizes contamination. This includes controlling particulate contamination through air filtration systems, contamination control protocols, and strict personnel protocols to ensure the highest quality of semiconductor devices.