The Silicon Wafer Manufacturing Process Explained
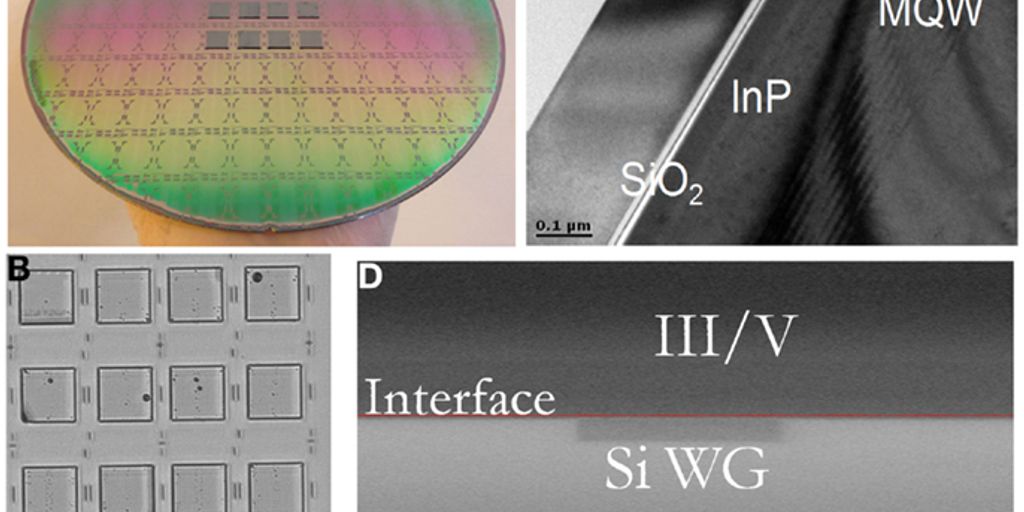
Silicon wafers are the foundational material for semiconductor devices, which are integral to modern electronics. The quality of these wafers is critical for the performance and reliability of devices such as microprocessors, memory chips, and sensors. This article delves into the intricate and precise process of silicon wafer manufacturing, from the extraction of raw materials to the final characterization and inspection of the wafers.
Key Takeaways
- Silicon wafer manufacturing starts with the extraction of silicon from silica sand, which undergoes purification to achieve high levels of purity.
- The crystal growth and ingot formation processes, including the Czochralski and Float Zone methods, are crucial for creating high-quality silicon ingots.
- Wafer slicing, edge grinding, and surface polishing are essential steps to prepare the silicon wafers for subsequent processing.
- Doping, oxidation, deposition, and photolithography are key techniques used to create the intricate patterns required for semiconductor devices.
- Rigorous testing, quality control, and final characterization ensure that the silicon wafers meet the stringent requirements for use in semiconductor manufacturing.
Raw Material Extraction and Purification
Silica Sand to Silicon
The primary raw material used in silicon wafer manufacturing is silica sand, which is abundant in nature. However, not all sand is suitable for manufacturing high-quality silicon wafers. The sand must be high-purity, with low impurities, such as iron, aluminum, and other materials, to ensure that the resulting silicon wafers are high quality. Once the raw silicon has been extracted, it must be purified to a high degree. This process involves removing impurities and contaminants from the raw material, typically sourced from sand.
Purification Techniques
The purification process involves several steps, including refining, zone melting, and solidification, which collectively increase the purity of the silicon to 99.9999% or higher. Extracted Silicon is then ground into a fine powder and fed into a Fluidized Bed Reactor (FBR), where it reacts with Hydrochloric Acid (HCL) at a temperature of 575K (about 300 degrees Celsius) and is heated until it turns into a liquid. It is then allowed to solidify into a silicon rod, or ingot, by using common fabrication methods like the Floating Zone or Czochralski process.
Crystal Growth and Ingot Formation
Czochralski Process
The Czochralski process is a widely used method for growing single-crystal silicon ingots. In this method, a polycrystalline silicon rod is melted in a crucible. Once the silicon charge is completely molten, a small crystal seed is lowered into the molten silicon. The seed crystal is slowly pulled out at a controlled rate, allowing a larger crystal to develop. Both the crystal and the crucible are rotated to improve uniformity and reduce impurities.
Float Zone Process
In the Float Zone (FZ) process, a polycrystalline silicon rod is vertically mounted in a growth chamber. The rod is heated using non-contact radio-frequency (RF) inductive heating to create a molten material zone within the rod. The seed crystal, with a known orientation, is attached to the bottom of the rod. The rod moves through the heating zone, and the crystal grows as the molten zone passes along the rod. This method produces high-purity crystals as the molten zone does not come into contact with any chamber components.
Ingot Shaping
After the crystal growth, the ingot undergoes shaping to prepare it for wafer slicing. The ingot is ground to a uniform diameter and its ends are cropped. This step ensures that the ingot has the desired dimensions and is free from any irregularities. The final large crystal has a cylindrical shape, completing the process of creating a single-crystal silicon ingot.
Wafer Slicing and Surface Preparation
Slicing Techniques
Silicon wafers are cut using a circular blade with embedded diamond splinters. This process involves slicing the silicon crystal into precise, thin discs, ensuring that each wafer has the correct orientation for optimal electronic performance. However, only a single wafer on each diamond saw can be cut at a time, making this technique less productive than grinding (cut by wire saw). The primary advantage of the wire saw method is its ability to cut hundreds of wafers simultaneously with a single wire. However, the sliced wafer surface is more bumpy and uneven compared to wafers cut with a circular saw. Thus, those wafers require a longer time for subsequent grinding processes.
Edge Grinding
After slicing, the wafer edges are often sharp and can cause damage during handling. Edge grinding is performed to round the edges, reducing the risk of chipping and breaking. This step is crucial for maintaining wafer integrity throughout the manufacturing process.
Surface Polishing
After the wafers have been sliced, they undergo a series of cleaning and polishing steps to prepare them for the fabrication of electronic devices. The first step is a cleaning process that removes any residual silicon dust from the slicing process. This is typically done using a combination of chemicals and ultrasonic agitation. Following the cleaning process, the wafers are polished to ensure they are flat and have a uniform thickness, which is crucial for the performance of semiconductor devices.
Doping and Layer Deposition
Doping Methods
Doping involves the addition of either electron-donating elements, such as phosphorus or arsenic, or electron-accepting elements, such as boron or aluminum. The introduction of these impurities creates either an excess or a deficiency of electrons in the silicon lattice, resulting in either n-type or p-type silicon, respectively. The controlled introduction of these impurities allows for the creation of specific electrical properties in the silicon wafer, which is essential for the fabrication of semiconductor devices.
Oxidation and Deposition
The process begins with a silicon wafer. Wafers are sliced from a salami-shaped bar of 99.99% pure silicon (known as an ‘ingot’) and polished to extreme smoothness. Thin films of conducting, isolating, or semiconducting materials – depending on the type of structure being made – are deposited on the wafer to enable the first layer to be printed on it. This important step is commonly known as ‘deposition‘. The deposition of these thin films is typically done using techniques such as chemical vapor deposition (CVD), physical vapor deposition (PVD), or atomic layer deposition (ALD). The choice of thin film materials and deposition methods depends on the specific requirements of the semiconductor device being manufactured.
Photolithography
As microchip structures ‘shrink’, the process of patterning the wafer becomes more complex. Advances in deposition, as well as etch and lithography, are enablers of shrink and the pursuit of Moore’s Law. These advances include the use of new materials and innovations that enable increased precision when depositing these materials. Photolithography is a critical step in this process, allowing for the precise patterning of the wafer surface to create the intricate circuits required for modern electronic devices.
Etching and Patterning
Etching plays a crucial role in the production of microelectronic components, with every substrate undergoing this essential process before reaching completion. Within the etching process, a protective masking material is applied to the substrate, rendering it resistant to the etching reagent’s effects. This masking material can take various forms, including photoresists generated through lithography, or in certain instances, more durable masks like silicon nitride may be employed.
Wet Etching
Wet etching uses chemical baths to wash the wafer. This method is highly effective for removing large amounts of material quickly. However, it can be less precise than dry etching, making it more suitable for less intricate patterns.
Dry Etching
Dry etching uses gases to define the exposed pattern on the wafer. This method allows for greater precision and is often used for creating the intricate patterns that will form the various components on the semiconductor wafer, such as transistors and interconnects.
Pattern Transfer
Following photolithography, the next step is etching, which removes the unprotected parts of the wafer, creating the intricate patterns that will form the final semiconductor devices. Etch processes must precisely and consistently form increasingly conductive features without impacting the overall integrity and stability of the chip structure. Advanced etch technology is enabling chipmakers to use double, quadruple, and spacer-based patterning to create the tiny features of the most modern semiconductor devices.
Wafer Testing and Quality Control
The quality of the silicon wafers is critical to the performance and reliability of semiconductor devices. This process checks the quality and performance of wafers, the thin slices of silicon used to make electronic circuits. The wafers are measured for flatness and thickness to meet the required specifications. They are inspected for defects such as scratches, cracks, and contamination, affecting their performance in semiconductor devices. The wafers are also tested for their electrical properties, such as resistivity and carrier concentration, to ensure they are suitable for semiconductor devices.
Final Wafer Characterization
Surface Characterization
Surface characterization is essential to ensure that the silicon wafers are flat and have a uniform thickness. This process involves inspecting the wafers for defects such as scratches, cracks, and contamination, which can affect their performance in semiconductor devices. The quality of the silicon wafers is critical to the performance and reliability of semiconductor devices.
Mechanical Properties
Mechanical properties of the wafers, such as their resistance to damage from electricity and solvents, are evaluated. Manufacturers use computer-controlled probes to meticulously examine each section of the wafer. If the criteria are met, the wafer is deemed ready for further processing.
Thermal Properties
Thermal properties are also assessed to ensure the wafers can withstand the operational demands. This includes evaluating the wafers’ ability to dissipate heat effectively, which is crucial for maintaining the performance and longevity of semiconductor devices.
Conclusion
The silicon wafer manufacturing process is a highly intricate and precise operation that transforms raw materials like silica sand into the fundamental building blocks of modern electronic devices. From the extraction of pure silicon to the meticulous steps of doping, photolithography, etching, and deposition, each phase is crucial in ensuring the quality and performance of the final semiconductor products. The importance of high purity and precise electrical properties in silicon wafers cannot be overstated, as even the smallest impurities can lead to significant operational failures. As technology continues to advance, the demand for high-quality silicon wafers will only grow, underscoring the ongoing need for innovation and precision in this essential industry.
Frequently Asked Questions
What is silicon wafer processing?
Silicon wafer processing refers to the manufacturing steps involved in producing high-quality silicon wafers for use in semiconductor devices such as microprocessors, memory chips, and sensors. The process involves converting raw materials such as silica sand into pure silicon.
How is pure silicon extracted from quartz?
The extraction process involves heating quartz in a high-temperature furnace in the presence of carbon, which reduces the silicon dioxide to silicon.
What are the main steps involved in silicon wafer manufacturing?
The main steps include raw material extraction and purification, crystal growth and ingot formation, wafer slicing and surface preparation, doping and layer deposition, etching and patterning, wafer testing and quality control, and final wafer characterization.
What is the Czochralski process?
The Czochralski process is a method of crystal growth used to obtain single crystal silicon. It involves melting high-purity silicon in a crucible and then slowly drawing a seed crystal from the melt to form a cylindrical ingot.
Why is surface polishing important in wafer manufacturing?
Surface polishing is crucial because it creates a flat, smooth surface on the silicon wafer, which is essential for subsequent processing steps such as doping, photolithography, and etching.
What role do doping and layer deposition play in wafer manufacturing?
Doping and layer deposition are critical for creating the intricate patterns of transistors, wiring, and other components on the silicon wafer. Doping introduces impurities to modify the electrical properties, while layer deposition adds thin films of various materials.