Understanding Wafer SiC: Applications and Benefits
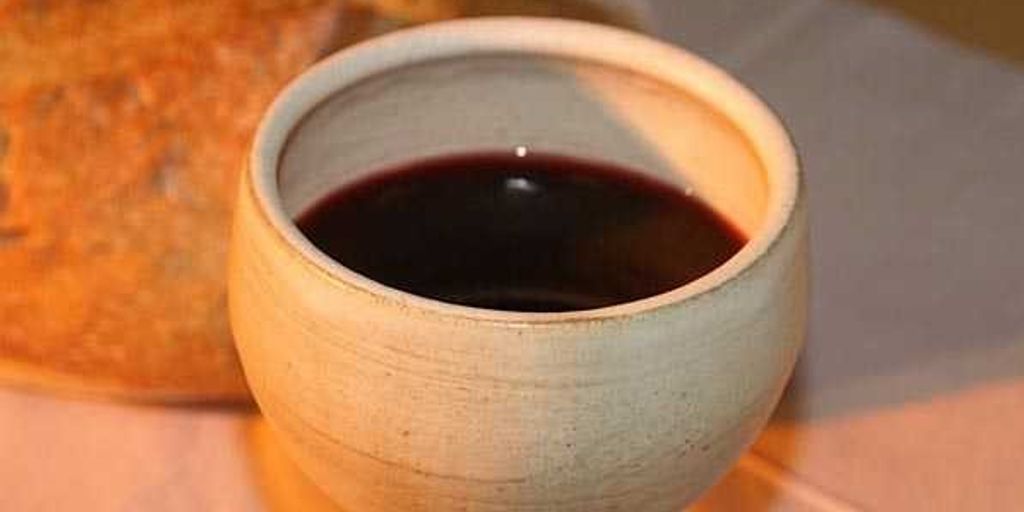
Silicon Carbide (SiC) wafers are changing the game in many fields, thanks to their amazing electrical and thermal properties. These wafers are super tough and can handle high temperatures and voltages, making them perfect for many uses. From power electronics to renewable energy systems, SiC wafers are helping to build better and more efficient devices. As new research and technology come along, we can expect SiC wafers to become even more important in the future.
Key Takeaways
- SiC wafers are known for their high thermal and electrical properties, making them ideal for various applications.
- They are tougher and can handle higher voltages compared to other semiconductor materials.
- SiC wafers are widely used in power electronics, renewable energy systems, and aerospace and defense sectors.
- The production of SiC wafers involves careful sourcing of raw materials, advanced manufacturing processes, and strict quality control.
- Future advancements in SiC technology promise even greater efficiency and performance for a range of applications.
What is a SiC Wafer?
A SiC wafer is a semiconductor material made from silicon carbide. It is known for its excellent electrical and thermal properties, making it a top choice for various applications. SiC wafers are particularly useful in power and voltage applications due to their high thermal resistance and hardness. They are commonly used in devices like Schottky diodes, Junction Barrier Schottky diodes, switches, and metal oxide semiconductor field-effect transistors (MOSFETs). The standard size for these wafers is 150mm in diameter, but some companies also produce 200mm-diameter SiC wafers.
Industrial Production of SiC Wafers
The production of SiC wafers is a detailed process that starts with sourcing the right raw materials. High-quality silicon carbide is essential for creating wafers that meet industry standards. The raw materials are carefully selected to ensure they have the necessary properties for the final product.
Raw Material Sourcing
The first step in producing SiC wafers is obtaining the raw materials. This involves selecting high-purity silicon carbide, which is crucial for the quality of the wafers. The materials must be free from impurities to avoid defects in the final product.
Manufacturing Processes
The manufacturing process of SiC wafers includes several steps. Initially, the raw silicon carbide is processed to form a crystal. This crystal is then sliced into thin wafers. These wafers undergo a reclaim process to remove any damaged surface layers. They are then repolished to achieve a device-ready surface. As the industry moves towards larger wafer sizes, the current batch tool method, which has a low throughput, will need to adapt to handle the increased demand.
Quality Control Measures
Quality control is a critical part of SiC wafer production. Each wafer is inspected for defects such as micropipes, dislocations, and stacking faults. These defects can affect the performance and reliability of the final product. Advanced inspection tools and techniques are used to ensure that each wafer meets the required standards. The new building for more SiC wafer production space will be equipped with state-of-the-art technology to further optimize the quality control process.
Applications of SiC Wafers in Engineering
Silicon Carbide (SiC) wafers are transforming the engineering world, especially in power electronics and renewable energy systems. Their unique properties, like high thermal conductivity and electrical efficiency, make them perfect for high-performance devices. Three key applications of SiC devices are in the automotive, high-power electronics, and renewable energy industries.
Benefits of Using SiC Wafers
Thermal Conductivity
Silicon carbide (SiC) wafers are known for their excellent thermal conductivity. This means they can handle high temperatures without breaking down. This property makes them perfect for devices that generate a lot of heat, like power electronics.
Electrical Efficiency
SiC wafers also offer high electrical efficiency. They can operate at higher voltages and frequencies compared to traditional silicon wafers. This makes them ideal for a variety of electrical and optical devices, ensuring better performance and lower energy loss.
Durability and Hardness
Another key benefit of SiC wafers is their durability and hardness. They are much harder than other semiconductor materials, which means they can withstand harsh conditions. This makes them suitable for applications in demanding environments, such as aerospace and defense.
In summary, the advantages of SiC components in various applications are clear. They offer superior thermal and electrical properties, along with unmatched durability, making them a top choice in the semiconductor industry.
Future Developments in SiC Wafer Technology
The future development and adoption of SiC wafer technology are expected to accelerate, driven by ongoing research in crystal growth techniques, epitaxial growth methods, and packaging solutions, as well as the increasing demand for energy-efficient and high-power applications.
Challenges in SiC Wafer Manufacturing
Defect Control
One of the biggest hurdles in SiC wafer manufacturing is controlling crystal defects. Issues like micropipes, dislocations, and stacking faults can disrupt the performance of SiC devices. Manufacturers must meticulously control these defects to ensure high-quality wafers. This involves advanced techniques and constant monitoring to reduce defect densities.
Yield Improvement
Improving yield is another significant challenge. The complex process of SiC manufacturing often results in lower yields compared to other semiconductors. To address this, companies are investing in better equipment and refining their processes. This not only helps in increasing the number of usable wafers but also in reducing costs.
Cost Considerations
The cost of producing SiC wafers is relatively high. Factors like expensive raw materials and sophisticated manufacturing processes contribute to this. Additionally, the transition to larger wafer sizes, such as 8-inch wafers, is difficult and costly. As of 2024, there are a limited number of 8-inch wafer suppliers, which adds to the challenge. Companies are continuously working on ways to make the production more cost-effective without compromising on quality.
Market Demand for SiC Wafers
Semiconductor Industry Trends
Today, the semiconductor industry is expanding at a rapid rate, which means that wafer supply is crucial to success. To accommodate the increased demand for SiC semiconductors, chipmakers are increasingly turning to both in-house and external sources to create the necessary silicon and SiC wafers. These in-house sources will help chipmakers realize economies of scale and reduce costs.
Key Market Players
Several companies are leading the charge in the SiC wafer market. These companies offer a range of SiC-based products, including power devices, sensing and control, and high-temperature materials. The decline in SiC wafer prices is an inevitable trend, towards which most companies hold a positive attitude. As CGEE stated, the expansion of market space and the drive to improve process efficiency are key factors.
Future Market Projections
The future development and adoption of SiC wafer technology are expected to accelerate, driven by ongoing research in crystal growth techniques, epitaxial growth methods, and packaging solutions, as well as the increasing demand for energy-efficient and high-power applications. The market is striving for power device price parity with Si-based devices, which will further boost demand.
Conclusion
In conclusion, SiC wafers are transforming the world of electronics with their outstanding electrical and thermal properties. These wafers are not only tough and heat-resistant but also perfect for high-power and high-voltage uses. As research continues, we can expect even more amazing applications to emerge. From renewable energy systems to electric vehicles and beyond, SiC technology is paving the way for a future filled with efficient and high-performing devices. The journey of SiC wafers is just beginning, and their potential seems limitless.
Frequently Asked Questions
What is a SiC wafer?
A SiC wafer is a type of semiconductor made from silicon carbide. It has excellent electrical and thermal properties, making it ideal for various applications, especially in power electronics and high-temperature environments.
What are the key properties of SiC wafers?
SiC wafers are known for their high thermal conductivity, electrical efficiency, and extreme hardness. These properties make them suitable for high-power and high-voltage applications.
How do SiC wafers compare to other semiconductors?
Compared to other semiconductors, SiC wafers offer better thermal resistance and electrical performance. They are more durable and can handle higher voltages, making them ideal for demanding applications.
What are common applications of SiC wafers?
SiC wafers are commonly used in renewable energy systems like solar inverters and wind turbine converters, electric vehicle chargers, industrial motor drives, high-voltage transmission systems, and aerospace and defense applications.
What sizes do SiC wafers come in?
The most common size for SiC wafers is 150mm in diameter, but there are also 200mm wafers available. These sizes are typically used for power conversion applications.
What is the future of SiC wafer technology?
The future of SiC wafer technology looks promising with ongoing research in crystal growth techniques, epitaxial growth methods, and packaging solutions. As demand for energy-efficient and high-power applications grows, SiC technology will continue to advance.