A Deep Dive into Wafer Fab Singapore: Trends and Technologies
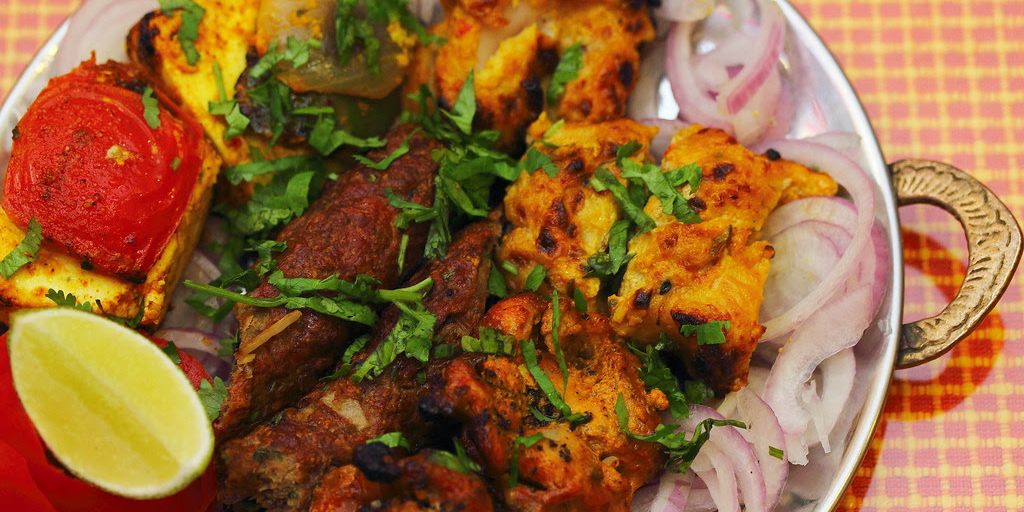
Wafer fabrication, or wafer fab, is a critical part of making semiconductors. In Singapore, this industry is growing fast with new technologies and big investments. Companies like Siltronic and UMC are leading the way with advanced facilities and innovative processes. This article explores the latest trends, technologies, and challenges in wafer fab in Singapore.
Key Takeaways
- Siltronic’s new FabNext in Singapore is a state-of-the-art facility expected to start production in 2024.
- UMC is building a new 22nm wafer fab in Singapore, enhancing the country’s semiconductor landscape.
- Cleanrooms are crucial in wafer fabrication, and new technologies are improving their efficiency.
- Singapore plays a significant role in the global wafer manufacturing market, with trends like reshoring impacting its share.
- Demand for wafers in Singapore is driven by applications in 5G, IoT, automotive, and consumer electronics.
Siltronic’s FabNext: A State-of-the-Art Wafer Fab in Singapore
Siltronic is making significant strides with its new 300mm wafer fab, known as FabNext, in Singapore. This project represents a €2 billion investment and is described as state-of-the-art and highly cost-efficient. The first wafers are expected to be available in 2024. The construction of FabNext is supported by long-term purchase agreements (LTAs) and prepayments from several leading customers.
UMC’s New 22nm Wafer Fab: Enhancing Singapore’s Semiconductor Landscape
Project Overview and Timeline
United Microelectronics Corporation (UMC) has announced plans to build a new advanced manufacturing facility next to its existing 300mm fab (Fab12i) in Singapore. The first phase of this greenfield fab will have a monthly capacity of 30,000 wafers, with production expected to commence in late 2024. The planned investment for this project is US$5 billion. UMC has operated as a pure-play foundry supplier in Singapore for more than 20 years and the location is also the company’s designated R&D center for advanced specialty technologies.
Technological Capabilities
The new fab, known as Fab12i P3, will be one of the most advanced semiconductor foundries in Singapore, providing UMC’s 22/28nm processes. This facility will leverage unmatched power efficiency and reduced die size, enabling mobile device manufacturers to enhance battery life of their products. The company’s 2022 capex budget will be revised upward to US$3.6 billion to account for the Fab12i expansion.
Economic Impact
UMC’s expansion in Singapore is expected to further diversify the company’s manufacturing footprint. Over the past two decades, UMC has benefited from Singapore’s vision to attract high-tech firms through strong infrastructure, ecosystem, and talent pool. Numerous new R&D projects in collaboration with customers will enter production when the new facility comes online. Dr. Beh Swan Gin, Chairman of the Singapore Economic Development Board, stated that UMC plays an important role in Singapore’s semiconductor manufacturing sector and that the expansion aligns with Singapore’s vision to grow and deepen its role in the global supply chain for semiconductors.
Cleanroom Innovations in Wafer Fab Singapore
Importance of Cleanrooms
Cleanrooms are a crucial part of electronics manufacturing. They ensure that the environment is free from dust and other particles that could damage the delicate wafers. Maintaining a cleanroom is essential for producing high-quality semiconductors. Even the smallest contamination can lead to defects in the final product.
Latest Cleanroom Technologies
New technologies can make cleanrooms more reliable, cost-effective, and efficient. For instance, real-time monitoring systems help track particulate levels and ensure a clean working environment. Advanced air filtration systems and automated cleaning robots are also being used to maintain cleanliness standards.
Challenges and Solutions
Despite strict protocols, operators can still introduce contamination. Monitoring points where operators interact with wafers is essential. Air particle counters can help track any particulate shedding by operators. Additionally, continuous training and adherence to cleanroom protocols are vital to minimize contamination risks.
Market Dynamics and Trends in Wafer Fab Singapore
Global Manufacturing Share
Singapore plays a crucial role in the global wafer manufacturing landscape. Approximately 60% of wafers are processed in Western countries like North America and Europe, while around 19% are handled in Japan. The rest are produced in Greater China and Southeast Asia, including Singapore and Malaysia. Despite the push for reshoring, mainland China is expected to increase its share in the coming years.
Impact of Reshoring Trends
Reshoring trends are influencing the semiconductor industry worldwide. Companies are reconsidering their manufacturing locations due to geopolitical tensions and supply chain disruptions. This shift could impact Singapore’s wafer fab industry, but the country remains a key player due to its established infrastructure and expertise.
Future Market Predictions
The future of wafer fab in Singapore looks promising. With ongoing investments and technological advancements, the country is well-positioned to maintain its competitive edge. Analysts predict steady growth in the sector, driven by demand for advanced technologies and applications like 5G, IoT, and automotive electronics.
Technological Challenges in Wafer Manufacturing
Complexity of Wafer Production
Producing wafers is a tough and slow process. There is no Moore’s Law for wafer manufacturing, meaning advancements don’t happen as quickly as in other tech areas. It took 14 years for silicon wafer revenues to return to the levels they were at in 2007. Even now, the average selling prices are still 36% below what they were back then.
Supply Chain Issues
Wafer suppliers can’t just speed up production to meet demand. Over the next five years, manufacturers plan to add 25 new 200mm lines to help meet the growing need for applications like 5G, automotive, and IoT devices. But where will they get the wafers needed for this expansion?
Innovations in Wafer Technology
Creating multiple copies of an integrated circuit on a single silicon wafer involves many steps. This includes forming patterned layers on and within the substrate. Throughout this complex process, controlling contamination is crucial, especially focusing on particulate contamination. Replacing silicon and organic substrates with new materials will require huge shifts in manufacturing, creating challenges that will take years to solve.
Applications Driving Demand in Wafer Fab Singapore
5G and IoT Devices
The rise of 5G and the Internet of Things (IoT) is a major driver for wafer fabs in Singapore. These technologies require advanced chips that can handle high-speed data and connectivity. As a result, wafer manufacturers are adding new production lines to meet this growing demand. This shift is crucial for supporting devices like analog, power management, and display driver integrated circuits (ICs), MOSFETs, microcontroller units (MCUs), and sensors.
Automotive Industry
The automotive industry is another significant sector driving demand for wafers. Modern vehicles are increasingly reliant on semiconductor chips for various functions, from engine control to advanced driver-assistance systems (ADAS). This trend is pushing wafer fabs to innovate and expand their capacity to meet the needs of automotive manufacturers.
Consumer Electronics
Consumer electronics, including smartphones, tablets, and laptops, continue to be a major market for wafer fabs. The constant demand for more powerful and efficient devices means that wafer fabs must continually advance their technologies. This sector remains a significant driver for 300mm wafers, as highlighted by industry experts.
Application | Key Technologies |
---|---|
5G and IoT Devices | Analog ICs, Power Management, Display Drivers, MCUs |
Automotive Industry | Engine Control, ADAS |
Consumer Electronics | Smartphones, Tablets, Laptops |
The geographic supply chain diversification provided by Singapore’s wafer fabs supports demand from non-China customers, making it a strategic location for semiconductor manufacturing.
Conclusion
In conclusion, the wafer fabrication industry in Singapore is experiencing significant growth and technological advancements. Companies like Siltronic and UMC are making substantial investments to expand their facilities and enhance their production capabilities. Despite the challenges and complexities involved in wafer manufacturing, the industry continues to innovate and meet the increasing demand for semiconductors. As Singapore solidifies its position as a key player in the global semiconductor market, it will be interesting to see how these trends and technologies evolve in the coming years.
Frequently Asked Questions
What is Siltronic’s FabNext?
Siltronic’s FabNext is a new 300mm wafer fab in Singapore. It’s a state-of-the-art facility with a €2 billion investment. The first wafers are expected to be ready in 2024.
What is the significance of cleanrooms in wafer fabrication?
Cleanrooms are crucial in wafer fabrication as they prevent contamination during the manufacturing process. They maintain a controlled environment to ensure the quality of the wafers.
How much is UMC investing in its new wafer fab in Singapore?
UMC is investing $5 billion in its new 22nm wafer fab in Singapore. The facility will have a monthly capacity of 30,000 wafers and is expected to start production in late 2024.
What are the main applications driving demand for wafers in Singapore?
The main applications driving demand for wafers in Singapore include 5G and IoT devices, automotive industry needs, and consumer electronics.
What challenges do wafer manufacturers face?
Wafer manufacturers face challenges like the complexity of wafer production, supply chain issues, and the need for constant innovation in wafer technology.
What is the global manufacturing share of wafers?
Approximately 60% of wafers are processed in North America and Europe, around 19% in Japan, and the rest in Greater China and Southeast Asia, including Singapore.