Maximizing Efficiency in Wafer Fab Processes
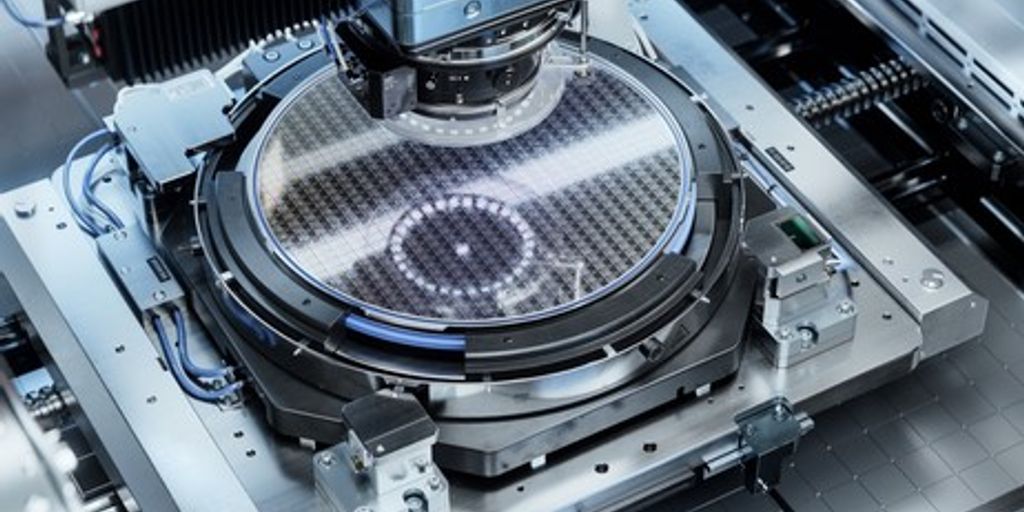
The semiconductor industry is at a turning point, with wafer fabrication plants looking to boost efficiency using the latest trends and new methods. This article will explore advancements in wafer fab equipment and processes, strategies to improve fab yield and cut costs, and the push for energy-efficient and sustainable manufacturing. We’ll also look at the changes in device structures and the new opportunities in memory and chip technologies.
Key Takeaways
- Innovative lithography, etching, and deposition methods are transforming wafer fabrication.
- Preventive maintenance and real-time monitoring are key to improving fab yield.
- Using lower-cost nodes and optimizing resources can significantly reduce operational costs.
- Energy-efficient practices and equipment are essential for sustainable wafer manufacturing.
- AI, machine learning, and chiplet technology are driving the future of wafer fab processes.
Advancements in Wafer Fab Equipment
Innovative Lithography Techniques
The semiconductor industry is at a pivotal juncture with wafer fab operations seeking to maximize efficiency through cutting-edge trends and innovative approaches. Innovative lithography techniques are at the forefront of this transformation. These methods allow for the creation of smaller and more complex patterns on wafers, which is essential for the production of advanced semiconductor devices.
Enhanced Etching Processes
Enhanced etching processes have also seen significant advancements. These processes are crucial for defining the intricate features of semiconductor devices. By improving the precision and control of etching, manufacturers can achieve higher yields and better performance in their products.
Next-Generation Deposition Methods
Next-generation deposition methods are another area of significant progress. These methods involve the precise application of materials onto wafers, which is essential for creating the various layers of semiconductor devices. With the advent of these new techniques, the industry is poised to overcome current limitations in production capacities.
Strategies for Improving Fab Yield
Preventive Maintenance Practices
To boost fab yield, it’s crucial to shift from reactive to preventive maintenance. Regularly scheduled maintenance can significantly reduce unexpected equipment failures. This approach ensures that tools are always in optimal condition, minimizing downtime and maximizing productivity.
Real-Time Monitoring Systems
Implementing real-time monitoring systems allows for immediate detection of any irregularities in the fab process. These systems provide valuable data that can be used to make quick adjustments, ensuring that the manufacturing process remains stable and efficient.
Yield Enhancement Programs
Yield enhancement programs focus on identifying and eliminating the root causes of yield loss. These programs often involve cross-functional teams that work together to analyze data, run experiments, and implement solutions. By continuously improving processes, fabs can achieve higher yields and better overall performance.
Cost Reduction in Wafer Fab Operations
Utilizing Lower Cost Nodes
One effective way to cut costs in wafer fab operations is by using lower cost nodes for certain integrated circuit (IC) functions. By choosing nodes that are less complex and not performance-critical, manufacturers can save a lot on fabrication costs. These mature nodes often have higher yields and lower production expenses compared to advanced nodes.
Optimizing Resource Allocation
Efficient resource allocation is key to reducing costs. This involves careful planning and management of materials, equipment, and labor. By optimizing the use of these resources, fabs can minimize waste and improve overall efficiency. Here are some strategies:
- Prioritize equipment recovery and maintenance
- Conduct regular planned maintenance
- Manage parts and materials efficiently
Reducing Material Waste
Minimizing material waste is another crucial aspect of cost reduction. This can be achieved through better process control and by adopting more efficient manufacturing techniques. For example, innovations in substrate patterning and chiplet assembly can lead to significant savings. Additionally, mixing pre-designed dies to create new products can also help in reducing design costs.
Energy Efficiency in Wafer Fabrication
Adopting Sustainable Practices
In the semiconductor industry, adopting sustainable practices is crucial for reducing environmental impact. Implementing green manufacturing techniques can significantly lower energy consumption and waste. Companies are increasingly focusing on renewable energy sources and recycling programs to minimize their carbon footprint.
Energy-Efficient Equipment
Using energy-efficient equipment is another key strategy. Modern wafer fabs are investing in advanced machinery that consumes less power while maintaining high performance. For instance, laser-based silicon carbide wafer manufacturing has shown potential for zero material loss and high throughput, making it an excellent choice for energy efficiency.
Minimizing Power Consumption
Minimizing power consumption involves optimizing various processes within the fab. This includes using smart sensors and automation to monitor and control energy usage in real-time. By doing so, fabs can ensure that they are not only saving energy but also reducing operational costs. Additionally, regular maintenance of equipment can prevent energy wastage and improve overall efficiency.
Emerging Trends in Wafer Fab Processes
The semiconductor industry is at a pivotal juncture with wafer fab operations seeking to maximize efficiency through cutting-edge trends and innovative approaches. This article will delve into the advancements in wafer fabrication equipment and processes, strategies for enhancing fab yield and reducing costs, as well as the push towards energy efficiency and sustainable manufacturing. Additionally, we will explore the evolution of device structures and the emerging opportunities in memory and
Challenges in Wafer Fab Manufacturing
Wafer fab manufacturing is a complex process with several challenges that need to be addressed to ensure efficiency and high yield. Maintaining process uniformity is one of the top challenges. Process engineers must ensure that each wafer is processed uniformly to avoid yield losses. This requires precise controls and consistent maintenance.
Maintaining Process Uniformity
Maintaining uniformity across wafers is crucial. Any misstep can result in yield losses, rendering wafers useless for device manufacturing. Engineers must adhere to tight tolerances and ensure that each step in the process is meticulously controlled.
Ensuring Cleanroom Standards
Cleanrooms are essential in wafer fab manufacturing to prevent contamination. Strict protocols must be followed to maintain cleanliness. This includes regular cleaning, monitoring particle levels, and ensuring that all personnel follow proper procedures.
Managing Equipment Downtime
Equipment downtime can significantly impact production schedules. Regular maintenance and timely repairs are necessary to minimize downtime. Implementing preventive maintenance practices can help in identifying potential issues before they lead to equipment failure.
Optimizing Production Scheduling
Scheduling in wafer fabs is a complex task due to the constant changes in production runs and priorities. Each fab may handle hundreds of different types of wafers for various customers, each with different due dates. Maximizing machine utilization while managing these variables is no easy feat.
Dynamic Scheduling Algorithms
Dynamic scheduling algorithms are essential for handling the ever-changing environment in wafer fabs. These algorithms can adapt to new production runs and shifting priorities, ensuring that the fab operates efficiently. One innovative approach involves using AI-based scheduling software, which can optimize the entire process without needing predefined rules.
Balancing Multiple Wafer Types
Balancing multiple wafer types is another critical aspect of production scheduling. Each wafer type may have different processing requirements and due dates, making it challenging to schedule them effectively. Advanced scheduling systems can help manage these complexities by prioritizing tasks based on various factors, such as urgency and resource availability.
Maximizing Machine Utilization
Maximizing machine utilization is crucial for improving productivity in wafer fabs. This involves ensuring that all machines are used to their full potential, minimizing downtime and bottlenecks. Implementing real-time monitoring systems can provide valuable insights into machine performance, helping to identify areas for improvement and optimize scheduling decisions.
Conclusion
In conclusion, maximizing efficiency in wafer fab processes is essential for the semiconductor industry to thrive. By adopting proactive strategies, such as regular maintenance and smart scheduling, fabs can significantly improve their yields and reduce costs. The shift towards energy-efficient and sustainable manufacturing practices is not just beneficial but necessary for future growth. As technology advances, the industry must continue to innovate and adapt to meet the ever-changing demands. By focusing on these key areas, wafer fabs can ensure they remain competitive and capable of delivering high-quality products to their customers.
Frequently Asked Questions
What are some advancements in wafer fab equipment?
New tools and methods, like innovative lithography, better etching, and next-gen deposition, are making wafer fab equipment more efficient.
How can we improve fab yield?
You can boost fab yield by doing regular maintenance, using real-time monitoring, and having programs to enhance yield.
What are some ways to reduce costs in wafer fab operations?
Lowering costs can be achieved by using cheaper nodes, optimizing how resources are used, and cutting down on material waste.
How can we make wafer fabrication more energy-efficient?
Adopting green practices, using energy-saving equipment, and minimizing power use can make wafer fabrication more energy-efficient.
What are the emerging trends in wafer fab processes?
New trends include using AI and machine learning, adopting chiplet technology, and evolving device structures.
What challenges do wafer fab manufacturers face?
Manufacturers struggle with keeping processes uniform, maintaining cleanroom standards, and managing equipment downtime.