The Journey of a Silicon Wafer: From Production to Application
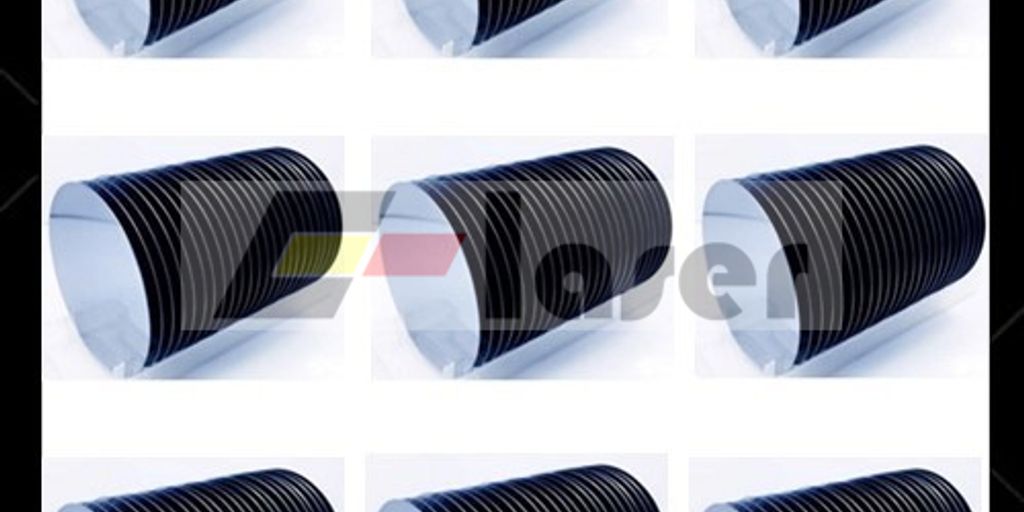
The journey of a silicon wafer begins with the extraction of silicon from sand. This silicon undergoes several steps to become the thin, shiny wafers used in electronics. Each stage, from purification to cutting and polishing, plays a crucial role in making sure the wafers meet high standards. Silicon wafers are essential in many modern technologies, from computers to solar panels.
Key Takeaways
- Silicon is extracted from sand and purified to create polysilicon.
- Polysilicon is formed into ingots, which are then sliced into thin wafers.
- Wafers are polished and cleaned to remove any imperfections.
- Doping and etching processes add necessary features to the wafers.
- Silicon wafers are used in many applications, including semiconductors and solar cells.
Harvesting and Purifying Silicon
The journey of a semiconductor begins with the most basic form of silicon, derived from sand. The sand is purified to produce polysilicon, which is then melted and crystallized to form a round, flat wafer.
Manufacturing Silicon Wafers
Silicon wafer manufacturing is an intricate process that demands painstaking accuracy and strict quality control. The journey from silicon ingot to preliminary wafer is complete through several key steps.
Cutting Ingots into Wafers
The first step in making silicon wafers is producing high-purity silicon ingots. This is done using two main techniques: the Czochralski method and the float zone method. Once the ingots are ready, they are sliced into thin wafers using a diamond saw. Precision is crucial to ensure each wafer is of uniform thickness.
Polishing and Cleaning Wafers
After cutting, the wafers have rough surfaces that need to be smoothed. This is achieved through a polishing process that removes any surface irregularities. The wafers are then cleaned to eliminate any contaminants. This step is vital to prepare the wafers for the next stages of production.
Quality Control Measures
Quality control is a critical part of silicon wafer manufacturing. Each wafer undergoes rigorous testing to check for defects and ensure they meet the required specifications. This includes visual inspections, measurements of thickness, and tests for electrical properties. Maintaining high standards in quality control helps in minimizing defects and ensuring the reliability of the final product.
Doping and Etching Processes
Introduction to Doping
Doping is a crucial step in silicon wafer production. It involves adding impurities to the silicon to change its electrical properties. This process allows the silicon to conduct electricity better. There are two main types of doping: n-type and p-type. N-type doping adds elements like phosphorus, while p-type doping uses elements like boron.
Etching Techniques
Etching is used to remove layers from the silicon wafer to create patterns. There are two main types of etching: wet etching and dry etching. Wet etching uses liquid chemicals to dissolve materials, while dry etching uses gases. Both methods are essential for creating the intricate designs needed for electronic devices.
Layer Deposition Methods
Layer deposition involves adding thin layers of materials onto the silicon wafer. This is done using techniques like Chemical Vapor Deposition (CVD) and Physical Vapor Deposition (PVD). These layers are crucial for building the different parts of electronic circuits. The process must be carefully controlled to ensure the layers are uniform and free of defects.
Photolithography in Silicon Wafer Production
Photolithography is all about the process of transferring intricate patterns onto a silicon wafer. This method is crucial for creating the tiny features that make modern electronics work.
Mask Creation and Alignment
The first step in photolithography is making a mask. This mask has the pattern that will be transferred onto the wafer. Aligning the mask perfectly with the wafer is essential to ensure the pattern is accurate.
Exposure and Development
Next, the wafer is coated with a light-sensitive material called photoresist. The mask is placed over the wafer, and light is shined through it. The light changes the photoresist, making it easier to remove in some areas. After exposure, the wafer goes through a development process to wash away the altered photoresist, leaving the desired pattern.
Etching Patterns onto Wafers
Finally, the wafer undergoes etching. This step removes the material where the photoresist was washed away, creating the final pattern on the wafer. The result is a silicon wafer with the intricate designs needed for various applications.
Applications of Silicon Wafers
Silicon wafers have multiple applications, playing a crucial role in various technologies. These thin, circular slices of silicon are essential in many fields, from electronics to renewable energy.
Use in Semiconductor Devices
Silicon wafers are the backbone of semiconductor devices. They are used to create integrated circuits (ICs) found in computers, smartphones, and other electronic gadgets. Without silicon wafers, modern electronics wouldn’t exist. The wafers undergo a series of processes, including doping and etching, to form the tiny components that make up ICs.
Role in Solar Cells
Silicon wafers are also vital in the production of solar cells. These cells convert sunlight into electricity, providing a renewable energy source. The wafers are treated to create a photovoltaic effect, which is the basis for solar power. This application is particularly important as the world shifts towards more sustainable energy solutions.
Emerging Technologies
In addition to traditional uses, silicon wafers are finding new applications in emerging technologies. For instance, they are used in the development of advanced sensors and microelectromechanical systems (MEMS). These technologies have a wide range of applications, from medical devices to automotive systems. As technology continues to evolve, the role of silicon wafers is expected to expand even further.
Challenges in Silicon Wafer Production
Silicon wafer manufacturing is an intricate process that demands painstaking accuracy and strict quality control. This difficult journey involves several challenges that manufacturers must overcome to ensure high-quality wafers.
Maintaining Purity Levels
One of the primary challenges is maintaining the purity of the silicon. Even the smallest impurity can affect the performance of the final product. Manufacturers use advanced techniques to keep the silicon as pure as possible, but this requires specialized equipment and expertise.
Minimizing Defects
Another significant challenge is minimizing defects in the wafers. Defects can occur at any stage of the production process, from cutting the ingots to polishing the wafers. Strict quality control measures are essential to identify and eliminate these defects, ensuring that only the best wafers make it to the market.
Scaling Production Efficiently
Scaling production efficiently is also a major hurdle. As demand for silicon wafers increases, manufacturers must find ways to produce more wafers without compromising on quality. This often involves investing in new technologies and optimizing existing processes to increase output while maintaining high standards.
In summary, the journey of a silicon wafer from production to application is fraught with challenges. However, with the right techniques and equipment, manufacturers can overcome these obstacles and produce high-quality wafers that meet the demands of various industries.
Conclusion
The journey of a silicon wafer is truly fascinating. It starts from raw silicon, often derived from sand, and goes through many steps to become the thin, shiny wafers used in electronics. Each step, from purification to slicing and imprinting, requires great care and precision. This process is crucial because these wafers are the foundation of many devices we use every day, like computers and smartphones. Understanding this journey helps us appreciate the technology that powers our world.
Frequently Asked Questions
What is the first step in making silicon wafers?
The first step is harvesting silicon from sand. This raw silicon is then purified to obtain polysilicon.
How are silicon ingots formed?
Silicon ingots are created by melting purified polysilicon and forming it into a large, cylindrical shape.
What happens after the silicon ingots are formed?
The ingots are sliced into thin wafers, which are then polished and cleaned to ensure they are smooth and free of impurities.
What is doping in silicon wafer production?
Doping adds impurities to the silicon wafers to change their electrical properties, which is crucial for making electronic devices.
How is photolithography used in making silicon wafers?
Photolithography involves creating a mask, aligning it with the wafer, exposing it to light, and then developing it to etch patterns onto the wafer.
What are some uses of silicon wafers?
Silicon wafers are used in semiconductor devices, solar cells, and many emerging technologies.