Understanding Silicon Wafer Sizes: A Complete Overview
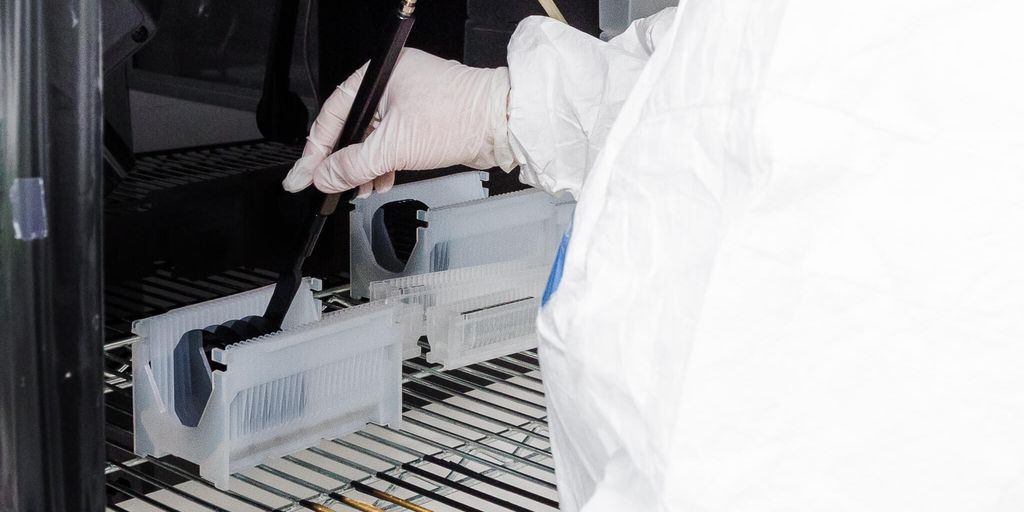
Silicon wafers are the foundation of modern electronics, found in everything from computers to smartphones. These thin slices of silicon are essential for making integrated circuits. Understanding the different sizes of silicon wafers, their evolution, and their applications can help you grasp the basics of semiconductor manufacturing. Let’s dive into the world of silicon wafers and explore their sizes, advantages, and impact on technology.
Key Takeaways
- Silicon wafers come in various sizes, typically ranging from 1 inch to 12 inches in diameter.
- Larger silicon wafers increase productivity and reduce manufacturing costs.
- The thickness and strength of a silicon wafer are crucial for its performance and durability.
- Circular silicon wafers are the most common, but other shapes are also used for specialized applications.
- Choosing the right wafer size depends on the specific needs and future goals of the project.
The Evolution of Silicon Wafer Sizes
Historical Milestones
The historical trend of the size of the silicon wafer has seen significant changes over the decades. Initially, silicon wafers were available in sizes as small as 25.4 mm (1 inch). Over time, the industry saw the introduction of 50 mm (2 inches) and 75 mm (3 inches) wafers. By the mid-1970s, 100 mm (4 inches) wafers became the standard. This trend continued with the development of 125 mm (5 inches), 150 mm (6 inches), and 200 mm (8 inches) wafers. Today, 300 mm (12 inches) wafers are common, and the industry is looking towards even larger sizes in the future.
Technological Advancements
Technological advancements have played a crucial role in the evolution of silicon wafer sizes. As technology improved, manufacturers were able to produce larger wafers with higher precision. This allowed for more integrated circuits to be placed on a single wafer, increasing efficiency and reducing costs. The move from 200 mm to 300 mm wafers, for example, significantly boosted productivity and lowered manufacturing expenses.
Future Trends
Looking ahead, the industry is exploring the potential of even larger wafers. The next milestone is expected to be 450 mm (17.7 inches) wafers. These larger wafers promise to further enhance productivity and cost-efficiency. However, the transition to these sizes will require significant technological and manufacturing advancements.
Common Silicon Wafer Sizes and Their Applications
Silicon wafers come in a variety of sizes, each suited for different applications. The most common sizes are 2 inch, 3 inch, 4 inch, 6 inch, 8 inch, and 12 inch. These sizes refer to the diameter of the wafer, which is measured in inches. The thickness of a silicon wafer is typically a few hundred micrometers.
Standard Sizes
Standard silicon wafer sizes are widely used in the semiconductor industry. The most common sizes include:
- 2 inch
- 3 inch
- 4 inch
- 6 inch
- 8 inch
- 12 inch
These sizes are popular because they meet the needs of most semiconductor manufacturing processes.
Specialized Sizes
In addition to these standard sizes, silicon wafers are also available in other, non-standard sizes. For example, wafers with diameters of 1 inch, 5 inch, 8 inch, or 12 inch may be used for certain specialized applications. Silicon wafers are also available in a variety of shapes, including square and rectangular, although circular wafers are the most common.
Industry Usage
The size of a silicon wafer is typically determined by the intended use of the wafer and the production process involved. Smaller wafers may be used for the production of smaller microelectronic devices, while larger wafers may be used for the production of larger devices or for more efficient manufacturing processes. The size of a wafer can also affect the cost of the wafer and the final product.
Advantages of Larger Silicon Wafers
Increased Productivity
Larger silicon wafers allow for more chips to be produced in a single manufacturing run. This means that more integrated circuits (ICs) can be made at once, boosting overall production. Higher chip density per wafer leads to improved manufacturing throughput.
Cost Efficiency
With larger wafers, the cost per chip decreases. This is because more chips can be made from a single wafer, spreading the cost of production over a larger number of chips. This helps in reducing the overall cost of semiconductor manufacturing.
Technological Benefits
Larger wafers also bring technological advantages. They provide a larger surface area, which can be beneficial for certain types of advanced semiconductor devices. However, it’s important to note that larger wafers can be more prone to defects like contamination and warpage. Careful process optimization is crucial to maximize the benefits and ensure high yield and production efficiency.
Understanding Wafer Thickness and Strength
Mechanical Strength
The thickness of a silicon wafer is determined by the mechanical strength of the material. It must be thick enough to support its own weight during handling without cracking. Wafers made from materials other than silicon will have different thicknesses even if they have the same diameter.
Thickness Standards
Thickness standards for silicon wafers vary depending on their size and application. For instance, ultra-thin wafers, which are less than 200 μm thick, are used in specific high-performance devices. However, these thin wafers are more prone to bending or breaking due to their reduced mechanical strength.
Impact on Manufacturing
The thickness of a wafer significantly impacts the manufacturing process. Thicker wafers provide better mechanical and thermal stability, which is crucial during processing steps. On the other hand, thinner wafers are preferred for certain applications to maintain device performance, especially in 3D stacking technologies. Balancing thickness and mechanical integrity is essential in silicon wafer technology.
Comparing Circular and Non-Circular Silicon Wafers
Shape Variations
Silicon wafers come in different shapes, with circular being the most common. However, non-circular wafers like square and rectangular ones are also used. The choice of shape often depends on the specific application and manufacturing needs.
Application Differences
Circular wafers are widely used in the semiconductor industry due to their ease of production and compatibility with existing equipment. On the other hand, non-circular wafers are often chosen for specialized applications where the shape can offer unique advantages.
Manufacturing Challenges
Producing non-circular wafers can be more challenging and costly. The silicon purification process typically results in cylindrical rods, which are then cut into circular wafers. This makes circular wafers cheaper to produce. Non-circular wafers require additional processing steps, increasing both time and cost.
How Silicon Wafer Size Affects Semiconductor Manufacturing
Production Processes
The size of a silicon wafer is typically determined by the intended use of the wafer and the production process involved. For example, smaller wafers may be used for the production of smaller microelectronic devices, while larger wafers may be used for the production of larger devices or for more efficient manufacturing processes. The size of a wafer can also affect the cost of the wafer and the final product.
Device Compatibility
The size of a chip wafer is typically determined by the intended use of the wafer and the production process involved. For example, smaller wafers may be used for the production of smaller microelectronic devices, while larger wafers may be used for the production of larger devices or for more efficient manufacturing processes. The size of a wafer can also affect the cost of the wafer and the final product.
Cost Implications
The size of the silicon wafer is another important consideration in silicon wafer technology. The standard silicon wafer size is 300mm, although the trend is growing in favor of larger sizes. This is mostly due to the higher productivity and efficiency that a larger wafer size can provide. Larger wafer size indicates:
- Increased productivity
- Cost efficiency
- Technological benefits
To increase yields to decrease prices, semiconductor manufacturers helped the industry evolve wafer diameters that are now 450mm!
Choosing the Right Silicon Wafer Size for Your Needs
Selecting the correct silicon wafer size is crucial for your project’s success. The size of a silicon wafer is typically determined by the intended use of the wafer and the production process involved. Smaller wafers are often used for producing tiny microelectronic devices, while larger wafers are preferred for bigger devices or more efficient manufacturing.
Factors to Consider
When choosing a wafer size, consider the following:
- Device Requirements: Smaller devices need smaller wafers, while larger devices benefit from bigger wafers.
- Production Efficiency: Larger wafers can lead to increased productivity and lower costs.
- Cost: The size of the wafer can impact the overall cost of both the wafer and the final product.
Industry Standards
The standard silicon wafer size is 300mm, but there is a growing trend towards larger sizes due to their higher productivity and efficiency. Here are some common sizes:
Diameter (mm) | Common Use |
---|---|
25.4 | Specialized applications |
100 | Small-scale production |
200 | Medium-scale production |
300 | Large-scale production |
450 | Future trends |
Future-Proofing Your Choice
To ensure your choice remains relevant, consider future trends in wafer sizes. The industry is moving towards larger wafers for increased productivity and cost efficiency. Keeping an eye on these trends can help you make a more informed decision.
Conclusion
Silicon wafers come in many sizes, each serving different needs in the tech world. From small 1-inch wafers to large 12-inch ones, each size has its own use. Bigger wafers help make more chips at once, which can lower costs and boost efficiency. As technology grows, the trend is moving towards even larger wafers. Understanding these sizes helps us see how tech keeps getting better and more affordable. So, next time you use a gadget, remember that the tiny silicon wafer inside plays a big role in making it work.
Frequently Asked Questions
What are the common sizes of silicon wafers?
Silicon wafers come in several standard sizes, such as 2 inch, 3 inch, 4 inch, 6 inch, 8 inch, and 12 inch. These measurements refer to the diameter of the wafer.
Why are larger silicon wafers preferred in manufacturing?
Larger silicon wafers are often preferred because they can improve productivity and reduce costs. Bigger wafers allow more chips to be made at once, making the process more efficient.
What is the typical thickness of a silicon wafer?
The thickness of a silicon wafer is usually a few hundred micrometers, which is just a few thousandths of an inch.
Are there non-standard sizes of silicon wafers?
Yes, besides the common sizes, silicon wafers also come in non-standard sizes like 1 inch, 5 inch, and others. They can also be found in different shapes like square and rectangular.
How does wafer size affect semiconductor manufacturing costs?
The size of the wafer can impact manufacturing costs. Larger wafers can lower costs because they allow for more efficient production processes and less material waste.
What factors should be considered when choosing a silicon wafer size?
When choosing a silicon wafer size, consider factors like the intended use, production process, and future needs. Industry standards and compatibility with existing equipment are also important.