Understanding Wafer Size in Semiconductor Production
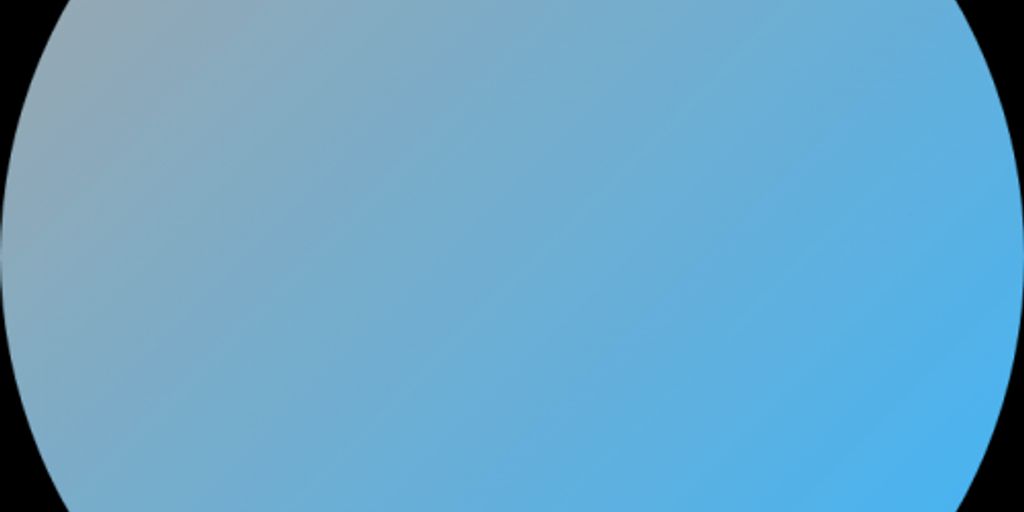
In the world of semiconductors, wafer size plays a crucial role in determining the efficiency and cost-effectiveness of production. Over the years, the industry has seen a shift from smaller to larger wafers, enabling the manufacturing of more devices from a single wafer. This transition not only supports the growing demand for electronic devices like smartphones and computers but also drives technological advancements in semiconductor fabrication.
Key Takeaways
- Larger wafer sizes allow for the production of more semiconductor devices from a single wafer, boosting productivity and efficiency.
- The semiconductor industry has gradually increased wafer sizes to improve throughput and reduce costs, with 300mm wafers currently being the standard.
- Future developments aim to introduce 450mm wafers, which could further enhance production capabilities and cost savings.
- Increasing wafer size presents significant challenges, including manufacturing difficulties, high investment requirements, and technological barriers.
- State-of-the-art semiconductor fabrication plants, known as fabs, are equipped to handle the current standard of 300mm wafers, with ongoing research into 450mm wafer technology.
The Importance of Wafer Size in Semiconductor Manufacturing
Wafer size plays a crucial role in semiconductor manufacturing. A larger wafer diameter enables producing more semiconductor devices from a single wafer, enhancing productivity and efficiency. If foundries still produced 1-inch wafers today, they wouldn’t be able to support the volume of smartphones, tablets, and PCs.
Impact on Production Efficiency
Larger wafers allow more dies per wafer, which ultimately brings down costs. Even small increases in wafer size significantly increase yields thanks to the extra surface area.
Cost Implications
The semiconductor industry has invested heavily to increase wafer size over the last 30 years. While foundries used to produce 1-inch wafers, today’s common wafer size is 300mm, which is 11.8 times larger than 1 inch. There is a clear plan to move towards a 450mm wafer size, which is 1.5 times larger than 300mm.
Technological Advancements
Increasing wafer size is not a trivial process. Silicon wafer manufacturing technologies were re-engineered to achieve the technology necessary to increase the wafer size over the years. It is difficult to grasp the amount of capital invested in size growth innovation, but it is estimated to be in the triple-digit billion USD range.
Evolution of Wafer Sizes Over Time
The historical trend of the size of the silicon wafer has seen significant changes. Initially, wafers were as small as 25mm in diameter. Over the years, the industry has transitioned to larger sizes to improve efficiency and reduce costs. This evolution has been driven by the need to produce more chips per wafer, which in turn lowers the cost per chip.
Historical Wafer Sizes
In the 1960s, wafers were typically 25mm in diameter. By the 1970s, sizes had increased to 50mm and 75mm. The 1980s saw the introduction of 100mm and 125mm wafers. This trend continued with 150mm and 200mm wafers becoming standard in the 1990s.
Transition to 300mm Wafers
The early 2000s marked the shift to 300mm wafers. This change was significant because it allowed for more chips to be produced per wafer, reducing the price per die by about 30-40%. The larger diameter wafers also meant that the cost of production steps increased more slowly than the wafer area, making it a cost-effective transition.
Future Prospects: 450mm Wafers
The next anticipated change in wafer size is the move to 450mm wafers. Although this transition has been slower than expected, it holds the promise of further reducing costs and increasing production efficiency. The industry continues to work towards overcoming the challenges associated with this shift, aiming to make 450mm wafers a reality in the near future.
Technical Specifications of Semiconductor Wafers
Diameter Variations
Semiconductor wafers come in various diameters, ranging from 25mm to the current standard of 300mm. Larger wafers allow more dies per wafer, which ultimately brings down costs. The industry is also working on developing 450mm wafers for future high-volume manufacturing.
Thickness and Flatness
The thickness of semiconductor wafers varies from around 500 to 900 micrometers (0.5-0.9mm), which is about as thick as 5-10 human hairs. The wafers are highly polished to achieve an extremely flat and smooth surface. This flatness is crucial for photolithography processes that etch tiny component details at nearly atomic scale.
Material Composition
Most semiconductor wafers are made from silicon, which is chosen for its excellent electrical properties. However, other materials like gallium arsenide and silicon carbide are also used for specific applications. The choice of material depends on the desired electrical characteristics and the specific requirements of the semiconductor device.
Challenges in Increasing Wafer Size
Increasing wafer size is not a trivial process. It requires significant changes in silicon wafer manufacturing technologies. The amount of capital invested in size growth innovation is enormous, likely in the triple-digit billion USD range.
Current Standard Wafer Sizes in the Industry
Common Sizes in Use
In the semiconductor industry, wafer sizes have evolved significantly over the years. Today, the most common sizes include 2-inch (51 mm), 4-inch (100 mm), 6-inch (150 mm), and 8-inch (200 mm) wafers. These sizes have been widely adopted due to their balance between cost and production efficiency.
State-of-the-Art Fabs
Modern fabrication plants, or fabs, primarily use 300mm wafers. These larger wafers allow for a significantly higher number of chips to be produced from a single wafer, enhancing overall production efficiency. During the 1980s and 1990s, these wafers were six inches (150mm) in diameter. Today, they are 12 inches (300mm), allowing for a significantly higher number of chips to be produced from a single wafer.
Development of 450mm Wafers
The industry is also looking towards the future with the development of 450mm wafers. These even larger wafers promise to further increase production efficiency and reduce costs. However, the transition to 450mm wafers presents several challenges, including the need for new manufacturing equipment and processes.
Benefits of Larger Wafer Sizes
Increased Yield
Larger wafers allow for more semiconductor devices to be produced from a single wafer. This enhances productivity and efficiency. For instance, a 300mm wafer can produce significantly more chips than a smaller wafer, which is crucial for supporting the high volume of modern electronics like smartphones and tablets.
Cost Reduction
With larger wafers, the cost per chip decreases. This is because the cost of the fabrication steps does not increase as quickly as the wafer area. For example, transitioning from 200mm to 300mm wafers reduced the price per die by about 30-40%. This cost efficiency is a major reason for the industry’s shift to larger wafers.
Enhanced Production Capabilities
Larger wafers also bring about improved production capabilities. The extra surface area allows for more dies per wafer, which in turn increases yields. This is especially important for high-volume manufacturing where even small increases in wafer size can lead to significant yield improvements.
Future Trends in Wafer Size Development
Research and Development
The semiconductor industry is always pushing the boundaries of technology. Research and development (R&D) efforts are crucial for the next generation of wafer sizes. Companies are investing heavily in R&D to overcome the physical and economic limits of current wafer technologies. This investment is expected to drive significant advancements in the coming years.
Industry Collaboration
Collaboration among industry players is essential for the successful development of larger wafers. By working together, companies can share knowledge, reduce costs, and accelerate innovation. Joint ventures and partnerships are becoming more common as the industry aims to achieve the next big leap in wafer size.
Potential Market Impact
The semiconductor silicon wafer market is expected to reach USD 13.93 billion in 2024 and grow at a CAGR of 3.82% to reach USD 16.81 billion by 2029. This growth highlights the increasing demand for advanced semiconductor technologies. Larger wafer sizes could lead to more efficient production processes, ultimately benefiting the entire industry.
Year | Market Size (USD Billion) |
---|---|
2024 | 13.93 |
2029 | 16.81 |
The future of wafer size development looks promising, with ongoing R&D, industry collaboration, and a growing market driving the next wave of innovation.
Conclusion
Understanding wafer size is crucial in the semiconductor industry. Larger wafers mean more chips can be made at once, which helps lower costs and boost production. Over the years, wafer sizes have grown from just 25mm to a whopping 300mm, with plans for even bigger sizes in the future. This growth hasn’t been easy or cheap, but it’s necessary to keep up with the demand for electronics like smartphones and computers. As technology advances, the push for larger wafers will continue, making it an exciting time for the industry.
Frequently Asked Questions
Why does wafer size matter?
A larger wafer size allows for more semiconductor devices to be made from a single wafer, boosting productivity and efficiency. If foundries still used 1-inch wafers today, they couldn’t keep up with the demand for smartphones, tablets, and PCs.
What are the common wafer sizes in the semiconductor industry?
Common wafer sizes range from 100mm to 450mm in diameter. The most advanced fabs use 300mm wafers, which help produce more chips per wafer. The industry is also working on developing 450mm wafers for future use.
How thin are semiconductor wafers?
Semiconductor wafers vary in thickness, typically ranging from 500 to 900 micrometers. This is about as thick as 5 to 10 human hairs.
What are the benefits of using larger wafer sizes?
Larger wafer sizes increase the number of chips produced per wafer, which helps lower costs and improve yields. This also enhances production capabilities.
What challenges come with increasing wafer size?
Increasing wafer size is complex and requires significant investment. The technology and manufacturing processes need to be re-engineered, which involves a lot of time and money.
What is the future of wafer sizes in the semiconductor industry?
The industry is actively researching and developing 450mm wafers. Collaboration among companies and ongoing research are crucial for this advancement, which could have a significant impact on the market.