Understanding the Benefits of Wafer Scale Package in Electronics
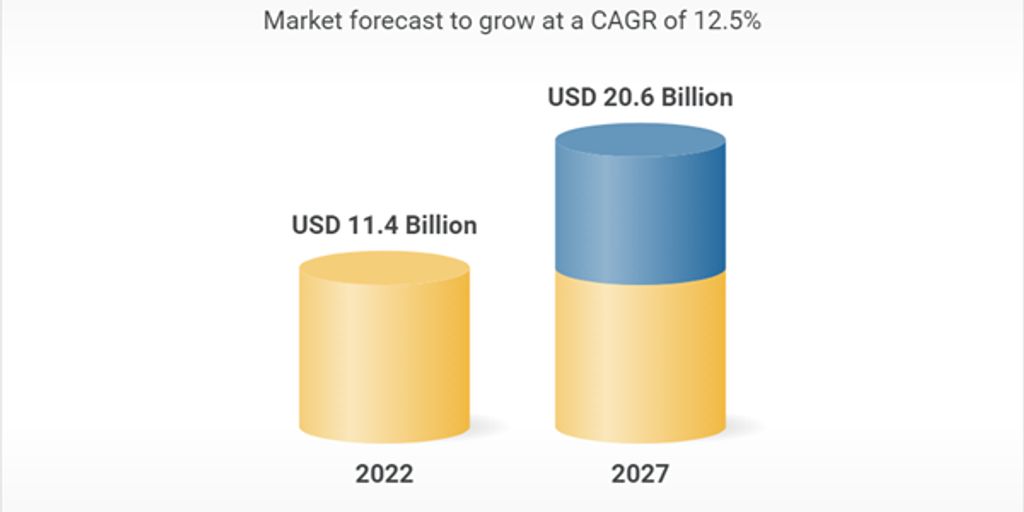
Wafer scale packaging is changing the world of electronics. It’s a new way to make electronic parts smaller and better. This method is helping to improve many devices, from smartphones to wearable gadgets. By using wafer scale packaging, companies can make products that are not only more efficient but also cost less to produce. Let’s dive into the benefits and see why this technology is so important.
Key Takeaways
- Wafer scale packaging helps make electronic devices smaller and more efficient.
- It improves signal quality by removing the need for bond wires.
- This method is cost-effective, making products cheaper to produce.
- It enhances the verification process, ensuring high-quality products.
- Wafer scale packaging is widely used in modern consumer electronics like smartphones and tablets.
Advantages of Wafer Scale Package in Modern Electronics
Wafer scale packaging (WSP) offers several benefits that make it a popular choice in modern electronics. One of the main advantages is enhanced signal integrity. By eliminating bond wires, WSP reduces inductance and improves electrical performance, which is crucial for high-speed signals. This means that devices can operate more efficiently and reliably.
Another significant benefit is the improved verification processes. With WSP, components are packaged directly on the wafer, allowing for easier and more accurate testing. This leads to higher quality and more reliable products, as potential issues can be identified and addressed early in the manufacturing process.
Cost efficiency is also a key advantage of WSP. The smaller footprint and reduced material usage result in lower production costs. Additionally, the streamlined packaging process can lead to faster production times, further reducing costs. These savings can be passed on to consumers, making electronic devices more affordable.
Wafer Scale Package vs Traditional Packaging Methods
Size and Form Factor
Wafer scale packaging (WSP) is like frosting an entire cake and then slicing it into pieces, while traditional packaging is like frosting individual cupcakes. This method results in a smaller-sized packaged chip, making it ideal for smaller device applications. WSP allows for higher levels of integration and cost reduction.
Performance Comparison
In wafer scale packaging, the electrical leads are contacted to the device while the chip is still on the wafer. This technique results in smaller and thinner packages, as they do not require large bond wires inside an epoxy package. This provides real benefits beyond reduced board space, both for PCB designers and IC manufacturing.
Manufacturing Differences
Traditional packaging involves multiple steps where each chip is individually packaged. In contrast, WSP applies packaging while the chip is still on the wafer, and only after the wafer is packaged is it separated from the semiconductor die. This streamlined process helps in reducing costs and improving efficiency.
Applications of Wafer Scale Package in Consumer Electronics
Wafer Scale Packages (WSP) are becoming increasingly popular in consumer electronics due to their numerous benefits. These packages offer a smaller footprint and improved performance, making them ideal for modern devices. Below are some key applications of WSP in consumer electronics.
Technical Aspects of Wafer Scale Package
Wafer Scale Packages (WSP) bring several technical benefits to modern electronics. These packages are designed to optimize the relationship between the die and the package, ensuring efficient use of materials and space. Understanding these technical aspects is crucial for anyone involved in electronics design and manufacturing.
Future Trends in Wafer Scale Packaging
Emerging Technologies
The future of wafer scale packaging is bright, with emerging technologies leading the way. One of the most exciting advancements is the development of ultrathin wafers. These wafers offer better heat dissipation and increased performance while reducing power consumption and form factor. As technology progresses, we can expect to see more innovations that will further enhance the capabilities of wafer scale packaging.
Market Growth
The market for wafer scale packaging is expected to grow significantly in the coming years. According to the status of the advanced packaging industry 2024, the advanced packaging wafer forecast for 2024-2029 shows a steady increase. This growth is driven by the demand for smaller, more efficient electronic devices. As more companies invest in advanced packaging technologies, the market will continue to expand.
Research and Development
Research and development play a crucial role in the future of wafer scale packaging. Companies are constantly looking for new ways to improve packaging techniques and materials. For example, a new advanced packaging facility accelerates future of microelectronics integration. This focus on innovation will lead to more efficient and cost-effective packaging solutions, benefiting the entire electronics industry.
Challenges in Implementing Wafer Scale Package
Design Considerations
Designing wafer scale packages (WSP) comes with its own set of challenges. Engineers must ensure that the design is both efficient and effective, which often requires advanced simulation and modeling tools. These tools help in predicting how the package will perform under various conditions, but they can be complex and time-consuming to use.
Manufacturing Constraints
Manufacturing WSPs is not a straightforward task. The process involves multiple steps, each requiring precision and accuracy. Any small error can lead to significant issues down the line. Additionally, the materials used in WSPs, such as polymers and metals, need to be carefully selected and handled to maintain the integrity of the package.
Testing and Reliability
Testing wafer scale packages is crucial to ensure their reliability. This involves rigorous testing procedures to check for any defects or weaknesses. The testing phase can be lengthy and costly, but it is essential to guarantee that the final product meets the required standards. Ensuring reliability is particularly important for consumer electronics, where failure is not an option.
Impact of Wafer Scale Package on PCB Design
Wafer scale packaging has a significant impact on PCB design, offering several advantages that can transform how electronic devices are built and function. By eliminating bond wires, wafer-level packaged components can achieve higher signal integrity, which is crucial for high-speed signals. This makes it easier for board designers to work with these components, especially at higher frequencies.
Conclusion
In summary, wafer scale packaging offers numerous benefits for the electronics industry. By making components smaller and more efficient, it helps designers and manufacturers create better products. This technology improves signal integrity and makes the testing process easier, which means more reliable devices. As electronics continue to shrink in size, wafer scale packaging will play an even bigger role in the future. Whether you’re designing a new smartphone or another high-tech gadget, understanding and using wafer scale packaging can give you a real edge.
Frequently Asked Questions
What is wafer scale packaging?
Wafer scale packaging is a method where the integrated circuit (IC) is packaged while still on the wafer. Only after the packaging process is complete is the wafer cut into individual chips.
How does wafer scale packaging improve signal integrity?
Wafer scale packaging improves signal integrity by eliminating bond wires, which can introduce noise. This results in better performance for high-speed signals.
What are the main advantages of wafer scale packaging?
The main advantages are enhanced signal integrity, improved verification processes, and cost efficiency. It also helps in creating smaller and thinner packages.
Why is wafer scale packaging beneficial for smartphones?
Smartphones benefit from wafer scale packaging because it allows for smaller, thinner, and more efficient chips. This helps in saving space and improving the overall performance of the device.
What challenges are associated with wafer scale packaging?
Some challenges include design considerations, manufacturing constraints, and ensuring testing and reliability. Overcoming these challenges is essential for successful implementation.
What is the future of wafer scale packaging?
The future looks promising with emerging technologies, market growth, and ongoing research and development. As devices continue to get smaller, wafer scale packaging will play a crucial role.