Understanding Wafer SiC: A Comprehensive Guide
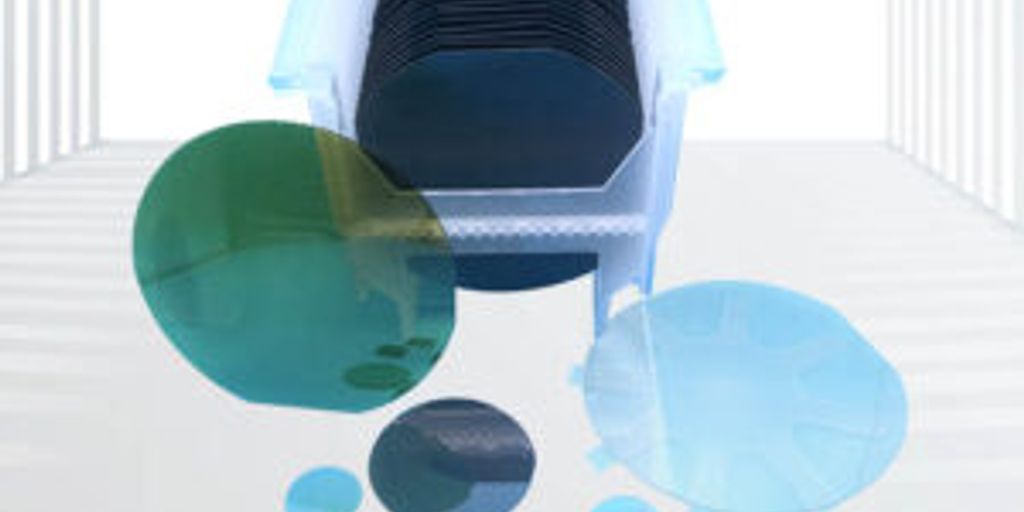
Silicon Carbide (SiC) wafers are revolutionizing the semiconductor industry. These wafers are made from a single crystal of SiC, a compound where silicon and carbon atoms are bonded together in a unique structure. This special bonding gives SiC wafers their incredible properties, making them ideal for high-performance electronics. This guide will walk you through everything you need to know about SiC wafers, from their basic properties to their applications and future trends.
Key Takeaways
- SiC wafers are made from a single crystal of silicon carbide, known for its strong bonding and unique properties.
- These wafers are essential in power electronics and radio frequency applications due to their high efficiency and performance.
- The process of making SiC wafers involves raw material extraction, manufacturing, and managing defects to improve yield.
- Recent advancements in SiC wafer technology are driving the semiconductor industry forward with innovative solutions.
- Understanding the electrical, thermal, and mechanical properties of SiC wafers is crucial for their effective application in various fields.
Fundamentals of SiC Wafers
Silicon Carbide (SiC) wafers are the foundation of a new generation of electronics. These wafers are made from a single crystal of SiC, a compound where silicon and carbon atoms form a strong, three-dimensional network. This unique structure, known as a tetrahedral bonding configuration, is key to SiC’s exceptional properties.
Crystal Structure and Composition
SiC’s crystal structure is a major reason for its outstanding features. The silicon and carbon atoms bond in a tetrahedral shape, creating a very strong and stable material. This structure allows SiC to handle high temperatures and voltages better than many other materials.
Key Properties and Advantages
SiC wafers have several important properties that make them valuable. They can operate at higher temperatures and voltages than silicon wafers. They also have better thermal conductivity, which means they can transfer heat more efficiently. These properties make SiC wafers ideal for high-power and high-frequency applications.
Comparison with Other Semiconductor Materials
When compared to other semiconductor materials, SiC stands out. Silicon, the most common semiconductor, can’t match SiC’s ability to work under extreme conditions. Gallium nitride (GaN) is another competitor, but SiC’s thermal properties give it an edge in many applications. In the past, researchers focused on the heteroepitaxial growth of SiC on silicon wafers because pure SiC substrates were not available. Now, with advancements in technology, SiC wafers are more accessible and are driving innovation in various fields.
Applications of SiC Wafers in Engineering
Silicon Carbide (SiC) wafers have become a game-changer in the engineering world, especially in power electronics and radio frequency (RF) applications. Their unique properties, like a wide bandgap, high breakdown electric field, and excellent thermal conductivity, make them perfect for creating high-performance, efficient devices.
From Raw Material to Powerhouse: Fabricating SiC Wafers
Silicon Carbide (SiC) wafers are the backbone of next-generation electronics, and their creation demands precision. Two main methods are used: Physical Vapor Transport (PVT) and High-Temperature Chemical Vapor Deposition (HTCVD). Mastering these techniques and managing defect control are crucial for producing high-quality SiC wafers.
Advancements in SiC Wafer Technology
Silicon Carbide (SiC) wafer technology is advancing rapidly, driven by several key innovations. These advancements are shaping the future of the semiconductor industry and enabling new applications.
Recent Innovations
One of the most significant advancements is the development of larger SiC wafers. Larger wafers, reaching up to 150mm and even 200mm in diameter, allow for more devices to be integrated on a single chip. This leads to higher production throughput and reduced manufacturing costs per unit area.
Another important innovation is the improvement in crystal growth techniques. These techniques have led to higher quality wafers with fewer defects, which is crucial for high-performance applications.
Future Trends
The future of SiC wafer technology looks promising with ongoing research in various areas. Some of the key trends include:
- Enhanced epitaxial growth methods to produce better quality layers.
- Advanced packaging solutions to improve device performance and reliability.
- Increased focus on energy-efficient and high-power applications.
Impact on Semiconductor Industry
The advancements in SiC wafer technology are having a profound impact on the semiconductor industry. SiC wafers are becoming indispensable components in advanced power electronics and other high-performance applications. As the demand for high-quality wafers continues to grow, SiC technology is expected to play a pivotal role in the next phase of semiconductor innovation.
Defect Control and Yield Improvement
SiC wafers, despite their excellent properties, face several challenges. Defects such as micropipes, dislocations, stacking faults, and impurities can significantly impact device performance. These defects can create unwanted pathways for electricity, leading to issues like premature device failure.
To tackle these challenges, manufacturers use a multi-pronged approach:
- Crystal Growth Optimization: Many defects originate during crystal growth. By carefully controlling growth parameters like temperature gradients, gas flow rates, and impurity levels, manufacturers can minimize defect formation from the start.
- Advanced Inspection Methods: Using state-of-the-art inspection tools helps in early detection and correction of defects.
- Post-Growth Processing: Techniques such as chemical mechanical polishing (CMP) are employed to further reduce surface defects.
Yield management becomes crucial as chips become more complex and feature sizes shrink. Managing yield – the percentage of good chips on a wafer – is a major challenge. Techniques like fault tolerance and redundancy are used to mitigate the impact of defects, although they add complexity. The primary areas of improvement in SiC materials have been heightened crystal quality, reduced defectivity, and better yields.
Deeper Dig into SiC Wafers Properties
Electrical Properties
Silicon Carbide (SiC) wafers have a unique electronic band structure that gives them exceptional electrical properties. Their wide bandgap of 3.26 eV allows them to operate at higher voltages and temperatures compared to silicon. This makes SiC ideal for high-power and high-frequency applications. Additionally, SiC has a high breakdown field of 2.8 MV/cm, which means it can handle more electric field before breaking down.
Thermal Properties
SiC wafers are known for their excellent thermal conductivity, which is about 370 W/mK. This is more than double that of silicon, making SiC a great choice for devices that generate a lot of heat. The high thermal conductivity helps in efficiently dissipating heat, ensuring the device remains cool and operates reliably even under high power conditions.
Mechanical Properties
The mechanical strength of SiC wafers is another standout feature. They are incredibly hard and have a high Young’s modulus, which means they are very stiff and resistant to deformation. This makes SiC wafers durable and reliable for use in harsh environments. Their mechanical robustness also contributes to their longevity and performance stability in various applications.
Conclusion
In summary, Silicon Carbide (SiC) wafers are transforming the world of electronics with their remarkable properties. They are becoming essential in power electronics and RF applications due to their high efficiency and performance. As the semiconductor industry continues to grow, the demand for SiC wafers will only increase, driving further innovation and development. Understanding the fundamentals and advancements in SiC technology is crucial for anyone involved in the field. The future of electronics looks bright with SiC paving the way for more powerful and efficient devices.
Frequently Asked Questions
What is a SiC wafer?
A SiC wafer is a thin slice of silicon carbide, a material made from silicon and carbon atoms. It’s used in making electronic devices because of its strong and durable properties.
Why are SiC wafers important in electronics?
SiC wafers are important because they can handle high temperatures and voltages better than other materials. This makes them perfect for high-performance and energy-efficient electronic devices.
How are SiC wafers made?
SiC wafers are made by combining raw materials, growing a crystal, and then slicing it into thin wafers. The process is complex and requires precise control to ensure high quality.
What are the common uses of SiC wafers?
SiC wafers are commonly used in power electronics, radio frequency applications, and emerging technologies like MEMS and sensors. They help improve the performance and efficiency of these devices.
What challenges exist in making SiC wafers?
Making SiC wafers is challenging because it involves precise control of the materials and processes to avoid defects. Ensuring high quality and yield rates can be difficult.
What advancements are being made in SiC wafer technology?
Recent advancements in SiC wafer technology include better manufacturing techniques, improved defect control, and new applications. These innovations are helping to make SiC wafers more efficient and widely used in the semiconductor industry.