Advancements in Wafer Growth Techniques for Enhanced Semiconductor Performance
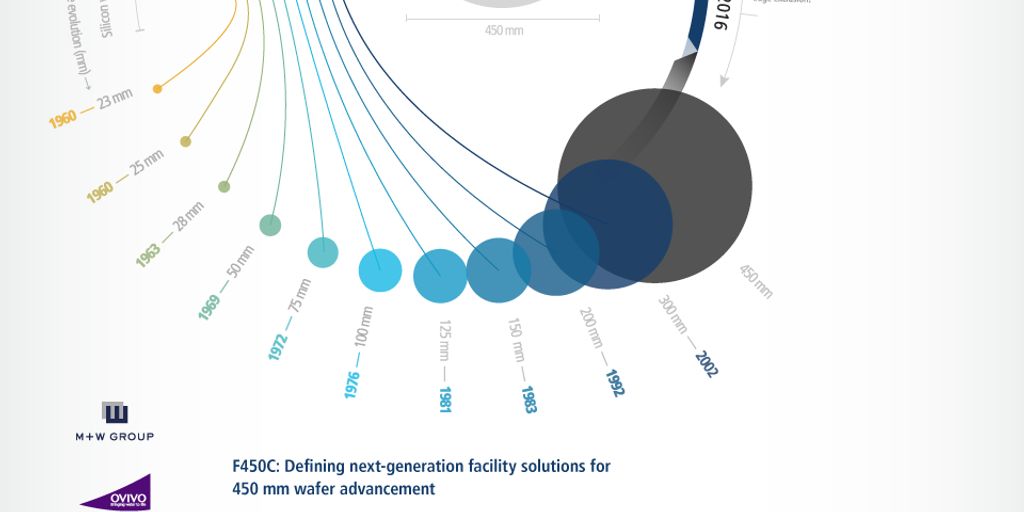
The world of semiconductor technology is always changing, with new advancements making electronic devices better and more powerful. Wafer growth techniques are a big part of this progress. From creating super-thin wafers to using lasers for precise cuts, these methods are improving how we make semiconductors. This article will explore the latest in wafer growth techniques and how they are helping to make electronics more efficient.
Key Takeaways
- New methods in epitaxial growth are creating more complex and efficient structures.
- Innovations in ultra-thin wafer manufacturing are achieving better thickness control and quality.
- Laser dicing technology is improving the precision and surface quality of wafers.
- Larger wafer sizes are boosting productivity and efficiency in semiconductor manufacturing.
- Automation in wafer handling is leading to greater accuracy and faster production processes.
Epitaxial Growth Techniques
Epitaxial growth is a method used to add layers of material on a wafer. This helps in creating complex structures with better properties. Scientists are always looking for new ways to grow silicon crystals better and faster. These new methods help make crystals that are super pure and work great in electronics. This means our gadgets can keep getting smaller and better.
Ultra-Thin Wafer Manufacturing
Manufacturing ultra-thin silicon wafers is pushing the limits of silicon wafer thinness. These wafers are known for their reduced thickness, which offers benefits like better flexibility, higher integration density, and improved performance. They are used in many semiconductor technologies, such as microelectronics, sensors, and optoelectronics. Achieving precise thickness control and uniformity is crucial for their successful production.
Innovations in Wafer Dicing
Laser Dicing Technology
Laser dicing technology has revolutionized the wafer dicing process. It offers higher precision and less damage compared to traditional methods. This technology uses focused laser beams to cut wafers, which results in cleaner and more accurate cuts. The reduced mechanical stress also means fewer defects and higher yields.
Precision and Surface Quality
Achieving high precision and excellent surface quality is crucial in wafer dicing. Advanced laser systems and novel dicing techniques have made it possible to achieve these goals. These innovations help in minimizing chipping and cracking, ensuring that the wafers meet the stringent quality standards required for semiconductor devices.
Challenges and Solutions
Despite the advancements, wafer dicing still faces several challenges. Issues like thermal damage and debris generation can affect the quality of the diced wafers. However, ongoing research and development are focused on finding solutions to these problems. For instance, the use of self-dicing materials and improved cooling systems are some of the approaches being explored to overcome these challenges.
Larger Wafer Sizes
The semiconductor industry has adopted larger wafers to cope with the increased demand for chips as larger wafers provide more surface area per wafer. This shift to larger wafer sizes, such as 300mm, brings several benefits. Increased productivity is a major advantage, as the larger surface area allows for more devices to be made on a single wafer. This leads to higher device yield and lower costs. The bigger surface area also means more devices can be integrated, boosting performance and functionality.
Automation in Wafer Handling
Accuracy in Production
Automation in wafer handling is changing the semiconductor industry. Modern machines and robots are now crucial for moving and handling wafers with great precision. These technologies not only boost productivity but also cut down on human errors. This makes the manufacturing process smoother and more reliable.
Speed Enhancements
Automated systems can handle wafers much faster than humans. This speed helps in meeting the high demand for semiconductors. Faster handling means more wafers can be processed in less time, which is essential for keeping up with market needs.
Future Prospects
The future of wafer handling looks promising with more advancements in automation. New technologies are being developed to make the process even more efficient. As these systems evolve, we can expect even higher levels of precision and speed, further improving semiconductor production.
New Crystal Growth Methods
The development of new methods of crystal growth is at the forefront of research in the field. Scientists and engineers are constantly exploring innovative techniques to grow silicon crystals more efficiently and with even greater purity. These advancements aim to produce crystals with optimal electrical properties for semiconductor applications, ensuring the continued miniaturization and enhancement of electronic devices.
Wafer Coring Techniques
Wafer coring is the process of removing a part of a semiconductor wafer, usually a circular section, to leave behind a cavity or hole. This method can be used on silicon wafers, compound semiconductor wafers, and other substrates. The size, shape, and depth of the coring can be precisely controlled, making it a very flexible process.
Enhancing Semiconductor Capabilities
Wafer coring services have become a powerful tool in semiconductor manufacturing, unlocking new possibilities for better device performance, increased integration, cost savings, and design flexibility. By using coring techniques, manufacturers can optimize the use of expensive materials like silicon wafers and reduce waste. This method allows for the creation of cavities and specialized features within a single wafer, cutting down on the need for extra substrates or components.
Innovative Approaches
The precise control offered by wafer coring allows for unmatched design flexibility in semiconductor devices. Designers can adjust the size, shape, and depth of the coring to meet specific needs. This flexibility helps in integrating various components, such as sensors, actuators, or optical elements, in a way that maximizes their effectiveness. As wafer coring techniques keep advancing, new possibilities emerge, opening up avenues for more complex and efficient designs.
Industry Applications
Wafer coring is used in many industries, including MEMS devices, TSVs, photonic devices, and power devices. The ability to create cavities and incorporate specialized features within a single wafer eliminates the need for additional substrates or components, reducing manufacturing complexity and costs. With ongoing advancements in nanoscale coring, multi-material coring, and advanced integration techniques, the future of wafer coring looks promising.
Conclusion
In summary, the progress in wafer growth techniques is setting the stage for a new chapter in the semiconductor world. From advanced epitaxial growth to ultra-thin wafer production and cutting-edge dicing methods, each breakthrough brings us closer to creating more powerful and efficient electronic gadgets. The ongoing efforts to increase wafer sizes, improve surface quality, and explore new materials ensure that the industry stays ahead in technological advancements. As we look to the future, these innovations promise to continue driving the evolution of semiconductor technology, making our devices faster, smaller, and more reliable.
Frequently Asked Questions
What is epitaxial growth?
Epitaxial growth is a method where a crystal layer is grown on a wafer’s surface. This helps create complex structures with better properties.
Why are ultra-thin wafers important?
Ultra-thin wafers are crucial because they allow for better control over thickness and surface quality, leading to more efficient electronic devices.
How does laser dicing improve wafer quality?
Laser dicing uses lasers to cut wafers, which increases precision and improves the surface quality compared to traditional methods.
What are the benefits of larger wafer sizes?
Larger wafers, like 300mm ones, boost productivity and efficiency. They also help reduce costs by yielding more devices per wafer.
How does automation impact wafer handling?
Automation in wafer handling improves accuracy and speeds up production, making the manufacturing process more efficient.
What are the new methods for growing crystals in wafers?
New crystal growth methods focus on increasing purity and efficiency, which enhances the performance of semiconductor devices.