The Importance of Wafer Level Reliability Testing in Semiconductor Manufacturing
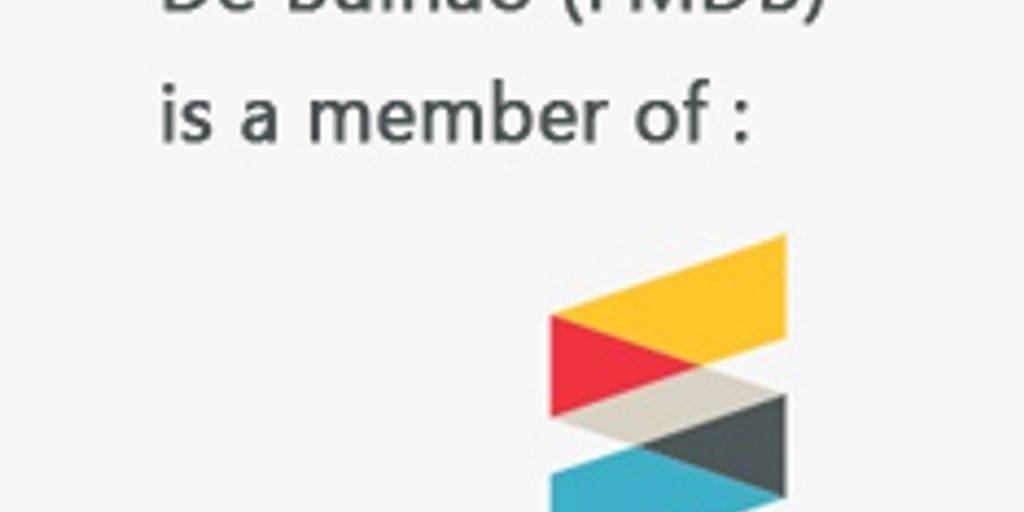
Wafer level reliability testing is a key part of making semiconductors. As technology gets better and devices get smaller, it’s more important than ever to make sure these tiny parts work well. By testing wafers in different ways and watching how they perform, makers can guess how they will work in real life. This helps keep quality high and makes devices work better.
Key Takeaways
- Wafer level reliability testing helps make sure devices last longer and work better.
- Different tests can find problems early, helping to keep quality high.
- This testing can predict how devices will work in real-world conditions.
- It helps fix issues before they become big problems.
- Using these tests can make devices more reliable and reduce failure rates.
Why Wafer Level Reliability Testing is Crucial in Semiconductor Manufacturing
Wafer level reliability testing is essential in semiconductor manufacturing for several reasons. By identifying potential failures early, it helps in enhancing the durability of the devices and ensures they meet stringent quality standards. This testing is especially important as technology advances and devices become smaller and more complex.
Ensuring Device Longevity
Wafer level reliability testing plays a key role in ensuring the longevity of electronic devices. By subjecting wafers to various stress tests, manufacturers can predict how well these devices will perform in real-world conditions. This not only helps in maintaining high quality and performance standards but also boosts overall product reliability.
Meeting Quality Standards
Meeting quality standards is a critical aspect of semiconductor manufacturing. Wafer level reliability testing helps in catching defects early, which in turn improves yield and reduces testing costs. This ensures that the final products are of high quality and meet the required standards.
Predicting Real-World Performance
Predicting real-world performance is another significant benefit of wafer level reliability testing. By closely monitoring the performance of wafers under different conditions, manufacturers can gain insights into how these devices will behave in actual use. This helps in making necessary adjustments and improvements to enhance product performance.
Common Methods Used in Wafer Level Reliability Testing
Wafer level reliability testing (WLRT) is vital for making sure semiconductor devices last a long time and work well. This section looks at the main methods used in WLRT, each tackling different potential problems and performance issues.
Challenges Addressed by Wafer Level Reliability Testing
Structural Failures
Wafer level reliability testing helps identify and mitigate structural failures in semiconductor devices. These failures can occur due to defects in the materials or issues during the manufacturing process. By catching these problems early, manufacturers can prevent costly recalls and ensure the longevity of their products.
Electromigration Issues
Electromigration is the gradual movement of metal atoms caused by the flow of electric current. This can lead to circuit failures over time. Wafer level reliability testing allows for the detection of electromigration issues before they become critical, ensuring the device’s performance remains stable throughout its lifespan.
Signal Transmission Crosstalk
Signal transmission crosstalk occurs when a signal transmitted on one circuit or channel creates an undesired effect on another circuit or channel. This can lead to data corruption and performance degradation. Wafer level reliability testing helps identify and address crosstalk issues, ensuring clear and reliable signal transmission in semiconductor devices.
Integration of Wafer Level Reliability Testing in the Manufacturing Workflow
Workflow Integration Strategies
Integrating wafer level reliability testing into the manufacturing workflow is essential for maintaining high-quality standards. This integration ensures that any issues are identified and addressed early in the production process. By doing so, manufacturers can prevent defects and improve the overall reliability of semiconductor devices.
Continuous Quality Control
Continuous quality control is a key aspect of integrating wafer level reliability testing. This involves real-time monitoring and analysis of wafers during the manufacturing process. By continuously checking for potential issues, manufacturers can make immediate adjustments, ensuring that each wafer meets the required standards.
Proactive Issue Resolution
Proactive issue resolution is another important benefit of integrating wafer level reliability testing. By identifying potential problems early, manufacturers can take corrective actions before the issues escalate. This not only saves time and resources but also enhances the overall efficiency of the manufacturing process.
Benefits of Implementing Wafer Level Reliability Testing
Enhancing Product Reliability
Wafer Level Reliability (WLR) testing is essential for making sure semiconductor devices work well over their expected lifespan. By spotting potential problems early, manufacturers can fix issues before they get worse, thus improving the overall reliability of the product.
Reducing Failure Rates
WLR testing helps in lowering the chances of device failures. By identifying and eliminating faulty devices early in the process, manufacturers can ensure that only the best-performing devices make it to the market. This proactive approach significantly reduces the failure rates.
Boosting Performance Standards
Through rigorous testing, manufacturers can ensure that their products not only meet but exceed performance standards. This is crucial for staying competitive in the fast-paced tech industry. By maintaining high quality and performance standards, manufacturers can boost their reputation and customer satisfaction.
Understanding Wafer Level Reliability Testing
Definition and Scope
Wafer Level Reliability (WLR) testing is a key step in making semiconductors. It checks how well a semiconductor will work over time. This testing looks at how the device handles things like heat and voltage. WLR testing helps find problems early, making sure the final product is good.
Importance in Modern Manufacturing
As technology gets better, semiconductors are getting smaller and more complex. This makes WLR testing even more important. By testing wafers early, companies can make sure their products will work well in real life. This helps keep quality high and customers happy.
Key Parameters Monitored
WLR testing looks at many things to make sure a semiconductor will last. Some key things checked are:
- Temperature changes
- Voltage stress
- Environmental factors
By keeping an eye on these, companies can make sure their products are strong and reliable.
Conclusion
In summary, wafer level reliability testing is a key part of making semiconductors. As technology gets better and devices get smaller, making sure these parts work well is more important than ever. By testing wafers under different conditions and watching how they perform, manufacturers can see how well these devices will work in real life. This not only helps keep high quality and performance but also builds trust with customers. Wafer level reliability testing is essential for the future of electronics, helping to make sure that the devices we use every day are reliable and long-lasting.
Frequently Asked Questions
Why is wafer level reliability testing important in semiconductor manufacturing?
Wafer level reliability testing is key because it makes sure electronic devices last long and work well. By spotting problems early, it helps make devices more durable and ensures they meet high quality standards.
What are some common methods used in wafer level reliability testing?
Some common methods include thermal cycling analysis, electromigration testing, and finite element modeling. These tests help in checking how well the wafers will perform under different conditions.
What challenges are addressed by wafer level reliability testing?
This testing tackles issues like structural failures, electromigration problems, and signal transmission crosstalk. If not managed well, these challenges can seriously affect the performance and reliability of semiconductor devices.
How is wafer level reliability testing integrated into the manufacturing workflow?
The testing is integrated by using strategies that ensure continuous quality control and proactive issue resolution. This means any problems can be fixed quickly, keeping the production process smooth.
What are the benefits of implementing wafer level reliability testing?
The main benefits include better product reliability, lower failure rates, and higher performance standards. It helps in making sure that the devices work well for a long time.
What is wafer level reliability testing?
Wafer level reliability testing is a way to check if semiconductor wafers will perform well in real-world conditions. It involves putting wafers through stress tests to see how they hold up, ensuring that the final products are reliable.