Optimizing Your Semiconductor Process for Maximum Efficiency
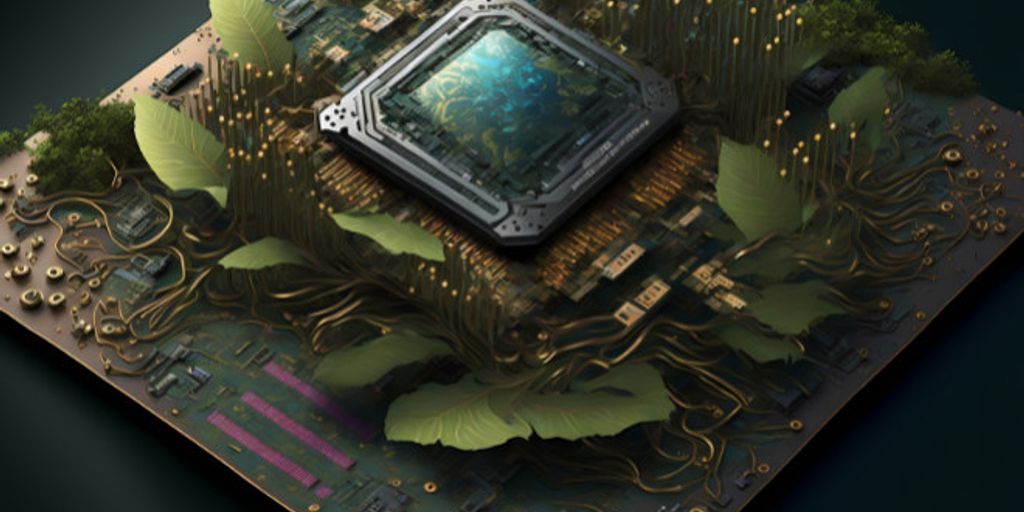
Optimizing semiconductor processes is essential for producing high-quality products efficiently. By fine-tuning various aspects of the manufacturing process, companies can significantly reduce waste, improve yield, and ensure the reliability of their devices. This article will explore different strategies and techniques to help manufacturers achieve maximum efficiency in their semiconductor processes.
Key Takeaways
- Yield optimization focuses on improving production to maximize high-quality output while minimizing waste and defects.
- Choosing the right materials is crucial for enhancing device performance and reliability.
- Advanced photolithography techniques can help overcome production bottlenecks and improve resolution.
- Proactive defect management is essential for early detection and correction of issues to maintain high yield.
- Regular equipment calibration and maintenance are critical for ensuring precision and optimal performance.
Yield Optimization Strategies
Identifying Inefficiencies
To boost yield in semiconductor manufacturing, the first step is to identify inefficiencies in the production process. This involves examining each stage to find bottlenecks and areas where resources are wasted. By pinpointing these issues, manufacturers can take targeted actions to improve overall efficiency.
Minimizing Waste and Defects
Reducing waste and defects is crucial for yield optimization. This can be achieved through various techniques such as defect avoidance and wafer reclaim. By focusing on these areas, manufacturers can increase the percentage of usable products, thereby enhancing productivity and reducing costs.
Implementing Continuous Improvement
Continuous improvement is an ongoing effort to enhance production processes. This involves regularly reviewing and refining methods to ensure they remain effective. Techniques like yield ramp acceleration can be employed to maintain high standards and adapt to new challenges, ensuring long-term success in yield optimization.
Material Selection for Enhanced Performance
Choosing the Right Materials
Selecting the right materials is crucial for the device’s functionality and reliability. Manufacturers must choose materials that meet specific device requirements while minimizing defects. This ensures that a higher percentage of manufactured components meet quality standards.
Impact on Device Reliability
The choice of materials directly impacts the reliability of the device. By adopting targeted techniques, semiconductor manufacturers can enhance product quality while also reducing production costs. This approach ensures that the devices are not only efficient but also durable.
Minimizing Defects
Optimizing material selection helps in minimizing defects, which is essential for yield improvement. When it is possible to design products with optimized layouts, material choices, and process tolerances, semiconductor manufacturers can streamline production processes. This minimizes the occurrence of yield-limiting issues.
Advanced Photolithography Techniques
Overcoming Bottlenecks
Photolithography is often seen as a bottleneck in semiconductor manufacturing due to its layered nature. Efficient capacity allocation in the photolithography area can significantly improve overall fab performance. The process involves three main steps: coating the wafer with a photoresist, exposing it to UV light to print the circuit pattern, and developing the image. Each wafer may pass through this process up to 40 times, making it crucial to manage efficiently.
Improving Resolution
Emerging technologies like extreme ultraviolet lithography (EUV) are essential for creating finer patterns on advanced chips. These technologies help in achieving higher resolution, which is vital for the performance of modern semiconductor devices. By using EUV, manufacturers can produce smaller and more complex circuit patterns, leading to better device performance.
Cost-Effective Solutions
While photolithography requires high capital investments, there are ways to make it more cost-effective. Implementing continuous improvement strategies and optimizing the use of existing equipment can help reduce costs. Additionally, investing in advanced technologies like EUV can offer long-term savings by improving yield and reducing defects.
Proactive Defect Management
Early Detection Methods
Early detection of defects is crucial for maintaining high yields in semiconductor manufacturing. Using various inspection techniques, such as optical and electron microscopy, helps identify defects early. This allows for timely corrective actions, reducing the impact on the overall yield.
Defect Analysis Tools
Understanding the origins and impacts of defects is essential. By categorizing defects, manufacturers can prioritize efforts on the most significant issues. Advanced tools, including AI and machine learning, can analyze defect patterns and suggest improvements.
Corrective Actions
Once defects are detected and analyzed, taking corrective actions is the next step. This can involve adjusting the manufacturing process, improving equipment calibration, or changing materials. Regular reviews and adjustments help in maintaining optimal conditions for maximum yield.
Equipment Calibration Best Practices
Regular Maintenance Schedules
Regular maintenance schedules are crucial for keeping equipment in top shape. Scheduled inspections help spot potential issues before they become big problems. This not only prevents unexpected breakdowns but also extends the lifespan of critical tools.
Precision Calibration Techniques
Calibration is not just a process; it’s an assurance of precision. Regular calibration ensures that tools operate within specified tolerances, guaranteeing accuracy in semiconductor processes. Adaptive calibration practices, which can be fine-tuned based on real-time performance data, keep tools in sync with the latest industry standards.
Impact on Yield
Equipment accuracy and maintenance are directly linked to yield. Calibration ensures equipment operates within precise parameters, which is important for tools like photolithography steppers. A proactive maintenance approach prevents potential yield-impacting issues, reducing downtime and equipment failures.
Technological Approaches to Yield Improvement
Predictive Analytics
Predictive analytics uses data to forecast future outcomes. By analyzing historical data, manufacturers can predict potential issues before they occur. This proactive approach helps in reducing unexpected downtimes and improving overall yield.
Automation and AI
Automation and artificial intelligence (AI) streamline the manufacturing process. Automated systems can handle repetitive tasks with high precision, while AI can optimize processes by learning from data. This combination leads to higher efficiency and fewer errors.
Real-Time Monitoring
Real-time monitoring involves continuously tracking the manufacturing process. This allows for immediate detection and correction of any issues, ensuring that the process stays within desired parameters. Real-time data helps in making quick decisions, which is crucial for maintaining high yield.
Optimizing Semiconductor Packaging
Efficient Layout Designs
When designing semiconductor products, optimized layouts are crucial. This approach not only streamlines production but also reduces the occurrence of yield-limiting issues. By focusing on efficient designs, manufacturers can significantly improve performance and time to market.
Material Choices
Selecting the right materials is essential for enhancing device reliability. The choice of materials directly impacts the functionality and longevity of the semiconductor devices. Manufacturers should prioritize materials that meet specific device requirements while minimizing defects.
Process Tolerances
Maintaining strict process tolerances is vital for achieving high yield in semiconductor packaging. By adhering to precise tolerances, manufacturers can ensure consistent quality and reduce the likelihood of defects. This practice is key to maintaining maximum production value and efficiency.
Conclusion
In conclusion, optimizing your semiconductor process is key to achieving maximum efficiency and high-quality output. By focusing on better design layouts, smart material choices, and precise process controls, manufacturers can significantly reduce waste and defects. Yield optimization, which aims to improve production processes and minimize inefficiencies, plays a crucial role in this. Implementing these best practices can help you reach and maintain the highest production value for your semiconductor equipment. Remember, every small improvement can lead to significant gains in the long run.
Frequently Asked Questions
What is yield optimization in semiconductor manufacturing?
Yield optimization is about improving the production process to get the most high-quality products. It focuses on reducing waste and defects.
How can material selection impact device reliability?
Choosing the right materials is crucial because it affects how well the device works and how long it lasts. Good material choices can also help reduce defects.
Why is photolithography important in semiconductor manufacturing?
Photolithography is a key step because it helps create the tiny patterns on semiconductor wafers. Better techniques can improve resolution and reduce costs.
What are some methods for early defect detection?
Early defect detection can be done using advanced tools and techniques like real-time monitoring and predictive analytics. These methods help catch problems early.
How does equipment calibration affect yield?
Regular calibration ensures that equipment is working correctly. This helps maintain high production quality and improves yield.
What role does automation play in yield improvement?
Automation and AI can make the production process more efficient by reducing human error and speeding up tasks. This leads to better yield and lower costs.