A Comprehensive Guide to the Wafer Manufacturing Process
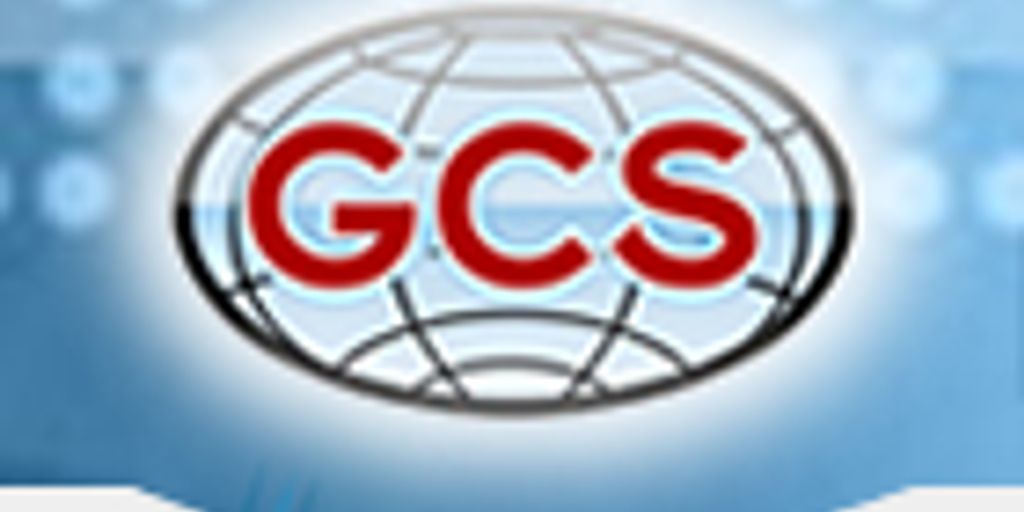
This guide will take you through the entire process of making semiconductor wafers. From the materials used to the final product, you’ll learn each step in a way that’s easy to understand. Whether you’re a student or just curious, this guide will help you see how these tiny chips power the devices we use every day.
Key Takeaways
- Semiconductor wafers are essential for modern electronics.
- Silicon is the most common material used for wafers.
- There are several methods to grow crystals for wafers, like the Czochralski method.
- Photolithography is a key process in making patterns on wafers.
- Quality control ensures that wafers meet strict standards.
Understanding Semiconductor Materials
Types of Semiconductor Materials
Semiconductors are materials that have electrical conductivity between that of a conductor and an insulator. Silicon is the most commonly used semiconductor material due to its abundance and favorable properties. However, other materials like Gallium Nitride (GaN), Silicon Carbide (SiC), and Graphene are also gaining attention. These emerging materials offer unique advantages for specific applications, such as high-power and high-frequency uses for GaN and SiC, and flexible electronics for Graphene.
Properties of Silicon
Silicon is favored in semiconductor manufacturing because of its excellent electrical properties and natural abundance. It has a crystalline structure that allows for efficient electron movement, making it ideal for creating integrated circuits. Additionally, silicon can withstand high temperatures and is relatively easy to purify, which is crucial for producing high-quality semiconductor devices.
Purification Processes
Purifying silicon involves several steps to remove impurities and achieve the desired level of purity. The most common method is the Czochralski process, where a seed crystal is dipped into molten silicon and slowly pulled out to form a large, single crystal ingot. Another method is the Float-Zone process, which uses a high-frequency coil to melt a small region of a silicon rod, allowing impurities to be segregated and removed. These purification techniques are essential for ensuring the performance and reliability of semiconductor devices.
Crystal Growth Techniques
Czochralski Method
The Czochralski process, named after Polish scientist Jan Czochralski, is a method used to grow single crystals of semiconductors, metals, salts, and synthetic gemstones. It starts with a seed crystal dipped into a crucible of molten silicon. The seed, attached to a rod, is slowly pulled up and rotated. As it rises, the molten silicon cools and solidifies, keeping the crystal structure of the seed. The result is a large, cylindrical crystal of silicon, known as a boule. This boule is then sliced into thin wafers for semiconductor manufacturing.
Float-Zone Process
The Float-Zone process is another technique for growing high-purity silicon crystals. Unlike the Czochralski method, it doesn’t use a crucible. Instead, a rod of polycrystalline silicon is passed through a heating coil, melting a small region. This molten zone is moved along the rod, and as it cools, it forms a single crystal. This method is known for producing silicon with fewer impurities.
Bridgman-Stockbarger Technique
The Bridgman-Stockbarger technique involves melting the material in a container and then slowly cooling it from one end to the other. The container is moved through a temperature gradient, allowing the material to solidify gradually. This method is often used for materials that are difficult to grow using other techniques.
Wafering: From Ingot to Wafer
Wafering is the critical process in semiconductor manufacturing where cropped silicon blocks are transformed into thin, flat wafers, ready for subsequent electronic device fabrication. This stage involves slicing the blocks with high precision to ensure that the resulting wafers meet stringent thickness and flatness specifications crucial for the functionality and reliability of semiconductor devices.
Photolithography in Wafer Manufacturing
Photoresist Application
Photolithography starts with applying a light-sensitive material called photoresist onto the wafer. This coating is crucial as it will help create the intricate patterns needed for the circuits. The wafer is spun at high speeds to ensure an even layer of photoresist.
Mask Alignment and Exposure
Next, a mask containing the circuit design is carefully aligned over the wafer. Ultraviolet (UV) light is then shone through the mask, transferring the pattern onto the photoresist-coated wafer. The areas exposed to the UV light harden, while the unexposed areas remain soft.
Developing and Etching
The wafer is then developed, which means the soft, unexposed photoresist is washed away, revealing the pattern. Following this, an etching process removes the exposed silicon dioxide, leaving behind the desired circuit design. This step is critical for defining the intricate features of the semiconductor device.
Doping and Ion Implantation
Doping is a key step in wafer manufacturing where small amounts of impurities are added to silicon wafers to change their electrical properties. These impurities can be electron-donating elements like phosphorus or arsenic, or electron-accepting elements like boron or aluminum. This process creates either n-type or p-type silicon, which is essential for making semiconductor devices.
Doping Methods
Before the ion implanter, doping was achieved by diffusion. In this method, wafers are exposed to a gas containing the desired impurity, which then diffuses into the silicon at high temperatures. This method is simple but less precise.
Ion Implantation Process
Ion implantation is a more advanced technique where ions of the impurity are accelerated and embedded into the silicon wafer. This method allows for precise control over the amount and location of the impurities. The photoresist material blocks the ions from entering areas that could lead to defects and is removed after implantation by ashing or using chemicals.
Annealing and Activation
After ion implantation, the wafer undergoes heat processing to activate the ions and repair any damage caused during implantation. This step is crucial for creating micro-transistors and ensuring the wafer has the desired electrical properties.
Metallization and Interconnects
Metal Deposition Techniques
Metallization is the process of adding metal layers to connect different parts of an integrated circuit. Aluminum and copper are the most commonly used metals. These metals are deposited onto the wafer using techniques like Chemical Vapor Deposition (CVD) and Physical Vapor Deposition (PVD).
Patterning and Etching
Once the metal layers are deposited, they need to be patterned to form the electrical pathways. This is done using advanced lithography and etching techniques. The metal is etched away in specific areas to create the intricate connections required for the circuit to function properly.
Interconnect Formation
After patterning, the metal layers form the interconnects that link various components of the circuit. These interconnects are crucial for the flow of electricity through the device. A protective layer is often added afterward to shield the metal from damage and contamination.
Quality Control and Testing
Ensuring the quality and reliability of semiconductor wafers is crucial. Inspection, measurement, and evaluation methods are utilized to maintain quality control, including wafer inspection, electrical testing, and reliability testing.
Defect Inspection
Defect inspection is the first step in quality control. This involves checking the wafer for any physical defects that might have occurred during the manufacturing process. Advanced tools and techniques are used to detect even the smallest imperfections.
Electrical Testing
Electrical testing ensures that all circuits on the wafer function correctly. This process, often called wafer probing, involves contacting each die on the wafer to measure parameters like current flow and voltage characteristics. Faulty dies are identified and marked for discarding.
Reliability Testing
Reliability testing is performed to ensure that the chips will perform well over time. This includes subjecting the chips to various stress tests to simulate real-world conditions. Only chips that pass these rigorous tests make it to the market.
Advancements in Wafer Manufacturing
Innovations in Materials
The semiconductor industry is always looking for new materials to improve wafer performance. One major development is the use of silicon-on-insulator (SOI) wafers. These wafers help reduce power consumption and increase speed in electronic devices. Another exciting area is the use of 300mm silicon wafers, which allow for more chips to be produced from a single wafer, making the process more efficient.
Process Automation
Automation is transforming wafer manufacturing. Robots and advanced software are now used to handle wafers with extreme precision. This reduces human error and increases production speed. Automated systems also help in monitoring and controlling the manufacturing environment, ensuring consistent quality.
Future Trends
Looking ahead, the focus will be on increasing efficiency and reducing costs. New technologies aim to minimize kerf loss, which is the material lost during the cutting process. This will help maximize the number of wafers produced from each silicon block. Additionally, there is ongoing research into new methods for wafer fabrication, including advanced lithography and etching techniques.
Conclusion
In conclusion, the wafer manufacturing process is a fascinating journey from raw materials to the tiny chips that power our modern devices. This guide has walked you through each step, from the initial crystal growth to the final polishing. By understanding these processes, we can appreciate the incredible technology that goes into making the electronics we use every day. Whether you’re a student, a hobbyist, or a professional, we hope this guide has provided you with valuable insights into the world of semiconductor wafers. Keep exploring and stay curious!
Frequently Asked Questions
What materials are used to make semiconductor wafers?
Semiconductor wafers are mainly made from silicon, but other materials like gallium arsenide and silicon carbide are also used.
How is silicon purified for wafer production?
Silicon is purified through a series of chemical processes that remove impurities, resulting in high-purity silicon suitable for wafer production.
What is the Czochralski method?
The Czochralski method is a process where a seed crystal is dipped into molten silicon and slowly pulled up to form a large, single crystal ingot.
Why is photolithography important in wafer manufacturing?
Photolithography is crucial because it allows precise patterns to be created on the wafer surface, which are essential for forming electronic circuits.
What happens during the doping process?
During doping, impurities are added to the silicon wafer to change its electrical properties, which is vital for creating semiconductor devices.
How are wafers tested for quality?
Wafers undergo various tests, including defect inspection, electrical testing, and reliability testing, to ensure they meet quality standards.