A Comprehensive Guide to the Wafer Semiconductor Process
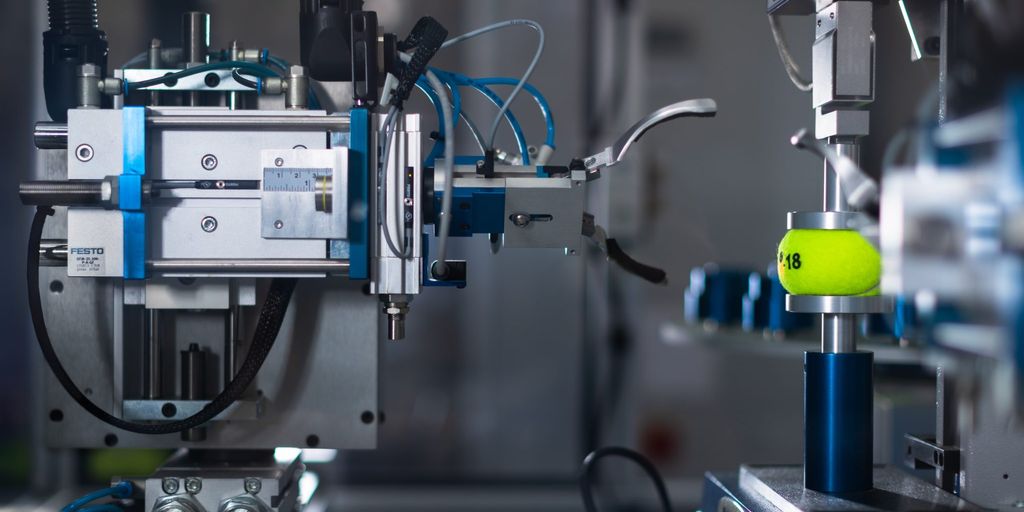
This guide offers a comprehensive exploration of semiconductor wafers from their structure to their complex manufacturing processes. Whether you’re a student or a professional in the electronics industry, you’ll gain a deep understanding of this technology that shapes our daily lives. Let’s dive in and explore the fascinating world of semiconductor wafers!
Key Takeaways
- Understanding the material composition and crystal orientation of semiconductor wafers is crucial for their performance.
- The wafer manufacturing process involves multiple stages including crystal growth, wafer slicing, and polishing.
- Photolithography is a key step in wafer processing, involving photoresist application, mask alignment, and exposure.
- Various etching techniques such as wet, dry, and plasma etching are used to define the wafer’s features.
- Quality control and testing are essential to ensure the reliability and performance of semiconductor wafers.
Understanding the Structure of Semiconductor Wafers
Semiconductor wafers are the foundational building blocks of modern electronics, powering devices from phones and laptops to cars and airplanes. Despite their ubiquity, many people are unaware of their structure and function. This section delves into the essential aspects of semiconductor wafers, including their material composition, crystal orientation, and dimensions.
Material Composition
Semiconductor wafers are primarily made from silicon, although other materials like gallium arsenide and silicon carbide are also used for specific applications. The choice of material impacts the wafer’s electrical properties and suitability for different types of devices.
Crystal Orientation
The crystal orientation of a wafer is crucial for its performance. Wafers are typically cut from a single crystal ingot, and the orientation is defined by the arrangement of atoms in the crystal lattice. Common orientations include <100>, <110>, and <111>, each offering different electrical and mechanical properties.
Wafer Dimensions
Wafers come in various sizes, typically measured in millimeters or inches. Standard diameters include 150mm, 200mm, and 300mm. The thickness of the wafer also varies depending on the application, with common thicknesses ranging from 200 to 800 micrometers. The table below summarizes standard wafer dimensions:
Diameter (mm) | Diameter (inches) | Thickness (µm) |
---|---|---|
150 | 6 | 675 |
200 | 8 | 725 |
300 | 12 | 775 |
Understanding these fundamental aspects is essential for anyone involved in the semiconductor industry, whether you’re a student, researcher, or professional.
The Wafer Manufacturing Process
Crystal Growth Techniques
The first step in the wafer manufacturing process is crystal growth. This involves heating the semiconductor material to a high temperature and then gradually cooling it down to form a single crystal. The quality of the crystal is crucial as it directly impacts the performance of the final semiconductor devices. Common techniques include the Czochralski process and the Float Zone process.
Wafer Slicing Methods
Once the crystal is grown, it is sliced into thin wafers using a diamond saw. This process, known as wafering, requires precision to ensure uniform thickness and minimal damage to the crystal structure. The sliced wafers are then subjected to edge grinding to prevent chipping and cracking.
Polishing and Cleaning
After slicing, the wafers undergo polishing to achieve an extremely smooth surface. This step is essential for subsequent photolithography and etching processes. The wafers are then cleaned to remove any contaminants that could affect device performance. Polishing and cleaning are critical to ensuring the wafers meet stringent quality standards.
Photolithography in Wafer Processing
Photolithography is a crucial optical process in the fabrication process, as it is used to create intricate circuit patterns on a single wafer’s surface. This is achieved by coating the wafer with a photosensitive material, called a photoresist, and then exposing it to high-wavelength deep ultraviolet (DUV) or extreme ultraviolet (EUV) light through a mask containing the desired pattern. The exposed photoresist undergoes a chemical change, which allows it to be selectively removed. It leaves behind a precise pattern that is essential for the subsequent steps in semiconductor manufacturing.
Etching Techniques for Semiconductor Wafers
Etching is an essential step in the semiconductor fabrication process that involves the selective removal of material from the wafer to create the desired structures and features. This process is used to define the shapes of various components, such as transistors, capacitors, and interconnects, by removing the unmasked regions of the wafer. The desired region of the wafer is protected using a photoresist and the undesired portion is removed. In this section, we will discuss the key aspects of etching.
Wet Etching
Wet etching involves the use of chemical solutions to remove material from the wafer. This method is highly effective for etching large areas and is often used for materials like silicon dioxide and polysilicon. The process requires precise control to ensure that only the unwanted material is removed, leaving the desired structures intact.
Dry Etching
Dry etching uses gases or plasma to etch the wafer. This technique is particularly useful for creating fine patterns and is commonly used for etching metal layers and silicon substrates. Dry etching offers better control and selectivity compared to wet etching, making it ideal for advanced semiconductor devices.
Plasma Etching
Plasma etching is a type of dry etching that utilizes plasma to remove material from the wafer. This method provides excellent etch uniformity and selectivity, which are crucial for producing high-performance semiconductor devices. Plasma etching is often used in conjunction with other etching techniques to achieve the desired results.
Doping and Ion Implantation
Doping Methods
Doping is a critical step in semiconductor fabrication, involving the introduction of impurities into the semiconductor material to modify its electrical properties. These impurities, known as dopants, can create n-type or p-type regions within the device. Common doping methods include:
- Ion Implantation: This technique involves bombarding the wafer with a beam of ions, embedding them into the semiconductor material to create the desired regions.
- Diffusion: This method involves heating the semiconductor material and allowing dopant atoms to diffuse into the wafer.
Ion Implantation Process
Ion implantation is a widely used doping technique that involves the direct insertion of dopant ions into the semiconductor material. The process includes the following steps:
- Ionization: The desired dopant species are ionized.
- Acceleration: The ions are accelerated using an electric field.
- Implantation: The high-energy ions are directed toward the wafer surface, penetrating and embedding into the crystal lattice.
Ion implantation offers several advantages over other doping techniques, such as precise control over dopant concentration and depth, uniform distribution across the wafer surface, and low-temperature processing. However, it can also cause damage to the crystal lattice, which must be repaired through a subsequent annealing process.
Activation and Annealing
After ion implantation, the wafer undergoes an annealing process to activate the dopants and repair any damage to the crystal lattice. This process involves heating the wafer to a high temperature, allowing the dopant atoms to occupy substitutional sites in the crystal lattice and restoring the crystal structure. The annealing process is crucial for ensuring the quality and performance of the semiconductor device.
Metallization and Interconnects
Metallization and interconnects are crucial components of semiconductor devices, providing the electrical pathways that connect the various elements of the integrated circuit. These connections enable the transfer of electrical signals and power between transistors, resistors, capacitors, and other components on the wafer. In this section, we will discuss the key aspects of metallization and interconnects, including material selection, deposition techniques, and the challenges associated with scaling and performance.
Quality Control and Testing
Testing and quality control are essential aspects of the semiconductor fabrication process to ensure that the final product meets performance and reliability specifications. These processes involve various inspection, measurement, and evaluation techniques to identify and correct defects, improve process control, and maintain high manufacturing yields. In this section, we will discuss the key aspects of testing and quality control in semiconductor fabrication, including wafer inspection, electrical testing, and reliability assessment.
Choosing the Right Semiconductor Wafer
Selecting the appropriate semiconductor wafer for your specific application can be a challenging task. The process involves comprehending the characteristics of various semiconductor materials and the production methods utilized to manufacture them. Additionally, it entails understanding the demands of your application and identifying the semiconductor wafer that will best suit those requirements. When making this decision, one must contemplate several factors, including the material, dopant concentration, thickness, and quality of the wafer. It is also crucial to assess the cost of the wafer and the availability of the material.
Conclusion
In conclusion, this guide offers a comprehensive exploration of semiconductor wafers, from their structure to their complex manufacturing processes. Whether you’re a student or a professional in the electronics industry, you’ll gain a deep understanding of this technology that shapes our daily lives. By carefully controlling the crystal growth, wafer slicing, polishing, and cleaning processes, manufacturers can ensure that their wafers meet the stringent requirements necessary for the production of reliable, high-performance semiconductor devices. The semiconductor fabrication process is a complex and intricate series of steps that transform raw materials into highly advanced integrated circuits. With ongoing advances in materials, techniques, and equipment, the semiconductor industry continues to push the boundaries of innovation and scale, enabling the development of ever-smaller, more powerful electronic devices. We hope this guide has provided valuable insights and knowledge to help you navigate the fascinating world of semiconductor wafers.
Frequently Asked Questions
What are semiconductor wafers made of?
Semiconductor wafers are typically made from materials like silicon, silicon carbide, and gallium arsenide. These materials are chosen for their electrical properties and ability to form high-quality crystals.
What is the significance of crystal orientation in semiconductor wafers?
Crystal orientation affects the electrical properties of the semiconductor wafer. Different orientations can influence the wafer’s conductivity, making it crucial to select the appropriate orientation for specific applications.
How are semiconductor wafers manufactured?
The manufacturing process involves several steps: crystal growth, wafer slicing, polishing, and cleaning. Each step is critical to ensure the wafer meets the required standards for electronic device fabrication.
What is photolithography in wafer processing?
Photolithography is a process used to transfer patterns onto the semiconductor wafer. It involves applying a photoresist, aligning masks, and exposing the wafer to light to create intricate circuit designs.
What are the different etching techniques used in semiconductor wafer processing?
There are three primary etching techniques: wet etching, dry etching, and plasma etching. Each method has its advantages and is selected based on the specific requirements of the semiconductor fabrication process.
How do you choose the right semiconductor wafer for an application?
Choosing the right wafer involves considering factors such as material selection, application requirements, and cost. Understanding the characteristics of different semiconductor materials and their production methods is essential for making an informed decision.