A Deep Dive into Silicon Wafer Semiconductors: Fabrication and Applications
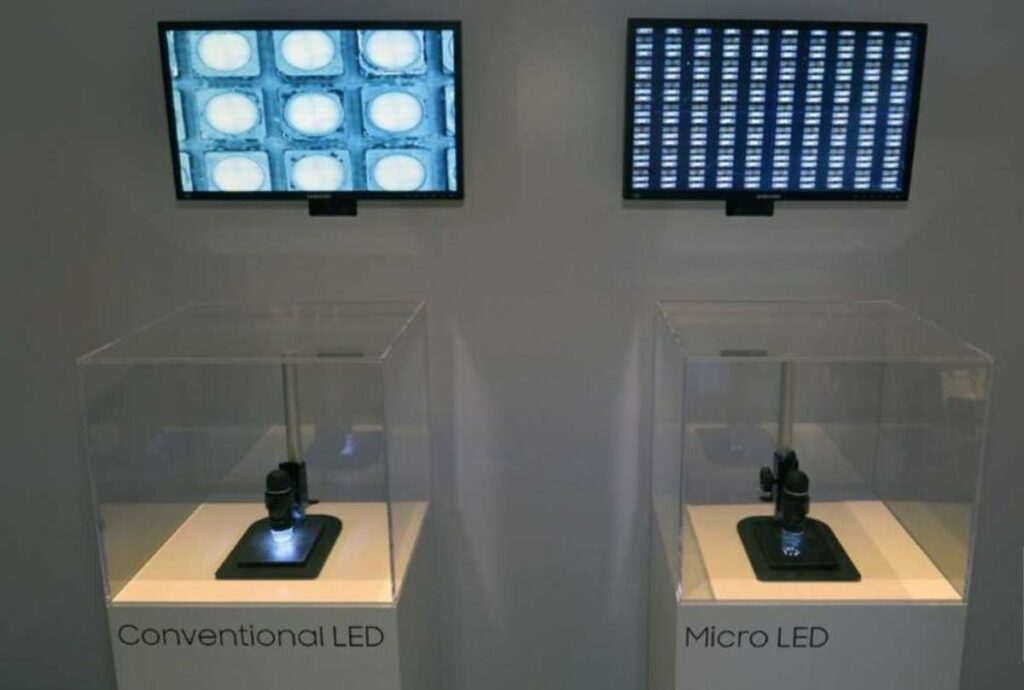
Silicon wafer semiconductors are the cornerstone of modern technology, powering everything from smartphones to satellites. This article takes a deep dive into the intricate world of silicon wafer fabrication and its myriad applications, exploring how these thin slices of silicon have revolutionized industries and what the future holds for this dynamic field.
Key Takeaways
- Silicon wafers are essential for a myriad of applications, including microelectronics, MEMS, and sensors, driving advancements in high-voltage devices and isolation layers.
- Fabrication techniques have evolved with technologies like CZ and FZ, while ALD and TSVs play pivotal roles in enhancing semiconductor manufacturing.
- The semiconductor market is segmented by wafer type, production technology, and application, with a growing demand for different wafer diameters and specialized types like polished, annealed, and SOI wafers.
- Innovations in device manufacturing such as new patterning technologies, etch variation reduction, and advanced wafer inspection are crucial for maintaining quality and performance.
- The industry faces challenges in reliability, cost management, and post-silicon analysis, but also opportunities in addressing these issues through emerging technologies and process improvements.
The Evolution of Silicon Wafer Fabrication Techniques
From CZ to FZ: A Comparison of Production Technologies
The semiconductor industry has witnessed a significant transition from the traditional Czochralski (CZ) method to the more advanced Float Zone (FZ) technique for silicon wafer production. The FZ method offers superior purity and quality, making it highly sought after for high-performance applications. The intrinsic undoped FZ silicon wafers are particularly notable for their minimal impurities compared to CZ techniques.
While CZ remains prevalent due to its cost-effectiveness and scalability, FZ silicon wafers are preferred where the utmost quality is required. Below is a comparison of key attributes between CZ and FZ silicon wafers:
-
CZ Silicon Wafers:
- Cost-effective
- Scalable for mass production
- Higher levels of oxygen impurities
-
FZ Silicon Wafers:
- Higher purity levels
- Lower oxygen content
- Better for sensitive electronic applications
The choice between CZ and FZ wafers ultimately depends on the specific requirements of the semiconductor devices being manufactured. As the industry continues to evolve, the demand for FZ wafers is expected to grow, especially in sectors that prioritize performance over cost.
Advancements in Atomic Layer Deposition (ALD) Technology
Atomic Layer Deposition (ALD) technology has become a cornerstone in the fabrication of semiconductor devices, enabling the application of ultra-thin layers that are essential for insulating layers and gate dielectrics in transistors. The precision of ALD is pivotal for the miniaturization of electronic components, ensuring uniform coverage even on complex three-dimensional structures.
The market for single wafer ALD is witnessing significant growth, with projections indicating an increase from $2.6 billion in 2022 to between $4.2 billion and $5.0 billion by 2027. This growth is characterized by a Compound Annual Growth Rate (CAGR) of 10-14% from 2022 to 2027, highlighting the expanding role of ALD in semiconductor manufacturing.
Potential applications of ALD technology are diverse and impactful, including:
- Coating of nanoporous materials.
- Hybrid techniques combining ALD with Molecular Layer Deposition (MLD).
- Applications in energy conversion, such as fuel cells and photovoltaics.
- Energy storage solutions.
The scale-up and commercialization of ALD processes are also underway, enhancing productivity for both rigid and flexible substrates, including roll-to-roll deposition. This advancement is crucial for meeting the increasing demand for sophisticated semiconductor devices.
The Role of Through-Silicon Vias (TSVs) in Semiconductor Manufacturing
Through-Silicon Vias (TSVs) have revolutionized the way we approach semiconductor design and packaging. By allowing for vertical connections between different layers of a semiconductor stack, TSVs enable a more compact and efficient design, which is crucial for the miniaturization of electronic devices.
The integration of TSVs into semiconductor manufacturing has been pivotal in advancing the performance of multi-die configurations. This technology facilitates high-speed data transfer and improved power efficiency by reducing the distance electrical signals need to travel.
The fabrication process of TSVs involves several critical steps:
- Creation of deep holes in the silicon wafer
- Insulation of the via walls
- Filling the vias with conductive material
- Planarization of the wafer surface
Moreover, the use of high aspect ratio TSVs and the development of sacrificial layers have been significant in pushing the boundaries of semiconductor manufacturing. The table below summarizes the key aspects and benefits of TSV technology:
Aspect | Benefit |
---|---|
Vertical Integration | Enhanced performance and space-saving |
High-Speed Data | Reduced latency and increased throughput |
Power Efficiency | Lower power consumption |
Design Flexibility | Greater design options for ICs |
As the industry moves towards more complex and powerful devices, the role of TSVs will continue to grow, making them an indispensable part of modern semiconductor technology.
Silicon Wafer Applications Across Industries
Microelectronics and MEMS: The Foundation of Miniaturization
The relentless pursuit of miniaturization in the tech industry has been significantly propelled by the advancements in microelectronics and MEMS (Microelectromechanical Systems). These systems represent a convergence of electrical and mechanical engineering, and are pivotal in the development of compact, high-performance devices. MEMS technology has evolved from a niche research topic to a mature, multidisciplinary field that is integral to a wide array of applications.
Microelectronics, on the other hand, has enabled the creation of smaller, more efficient, and more reliable electronic components. This has been crucial for the development of wearable devices, which demand compact form factors without sacrificing functionality or display quality. For instance, MicroLEDs, with their minuscule die pitch sizes, are revolutionizing wearable displays by offering high resolution in a tiny footprint. However, as components shrink, manufacturing challenges escalate, highlighting the need for innovative solutions to mitigate damage during production processes.
The following table summarizes the key aspects of MEMS and microelectronics in the context of miniaturization:
Aspect | MEMS | Microelectronics |
---|---|---|
Focus | Sensors, microphones, speakers | Electronic circuits, memory devices |
Impact | Enables advanced functionalities in small devices | Facilitates power reduction and device reliability |
Challenge | Integration of mechanical and electrical systems | Scaling down size while maintaining performance |
Sensors and RF Devices: Enabling Smarter Technology
Silicon wafers are integral to the development of sensors and RF (Radio Frequency) devices, which are pivotal in the advancement of smart technology. Their unique combination of electrical and thermal properties makes them ideal for these applications. Sensors fabricated on silicon wafers are found in a myriad of devices, from smartphones to automotive systems, providing critical functionality such as motion detection, temperature measurement, and environmental monitoring.
RF devices, on the other hand, are essential for wireless communication. The collaboration between Rohde & Schwarz and ADI highlights the importance of silicon wafers in creating efficient and repeatable verification systems for wireless devices. In complex RF environments, the performance of wireless Battery Management Systems (wBMS) is crucial, and the use of silicon wafers ensures reliable operation under various conditions.
The table below outlines some key applications of silicon wafers in sensor and RF device technology:
Application Area | Example Devices |
---|---|
Automotive | Pressure sensors, Gyroscopes |
Consumer Electronics | Accelerometers, Ambient light sensors |
Industrial | Temperature sensors, Flow meters |
Communication | Antennas, RF Filters |
Memory and Logic Devices: The Backbone of Computing Power
Memory and logic devices are fundamental components in a vast array of electronic systems, serving as the primary means for storing and processing data. Silicon wafers play a crucial role in the fabrication of these devices, providing the substrate on which intricate circuits are built. The evolution of memory technology has led to the development of various types of memory, each with its own set of characteristics and applications.
One significant advancement in memory technology is the emergence of Resistive Random Access Memory (ReRAM). ReRAM is being recognized for its potential to revolutionize CPU memory, especially in high-bandwidth applications. Unlike traditional SRAM, which is limited by data transfer inefficiencies between the CPU and memory, ReRAM offers a promising solution. It aligns well with the integration into advanced logic devices and stands as a robust contender to replace SRAM in on-chip memory, particularly for high-bandwidth CPU applications.
The Von Neumann architecture, which is the foundation for most computing today, relies heavily on the efficient movement of data between the processor and memory. Innovations in memory technology, such as ReRAM, are critical in reducing energy consumption and processing delays, which are increasingly important in modern computing applications. As the industry continues to push the boundaries of what’s possible, the role of memory and logic devices remains central to the advancement of technology.
Market Dynamics and Segmentation of Silicon Wafers
Analyzing the Demand for Different Wafer Diameters
The demand for silicon wafers of various diameters is a critical factor in understanding market dynamics. Silicon wafer shipments and revenue have seen a notable decline in 2023, with a 14.3% decrease in shipments to 12,602 million square inches and a 10.9% contraction in revenue to $12.3 billion. This trend underscores the importance of analyzing wafer diameter preferences across different applications.
Wafer diameters are segmented based on their application in various electronic devices. The larger diameters, such as those above 300 mm, are predominantly used in advanced microelectronics due to their efficiency in mass production of chips. Conversely, smaller diameters, up to 100 mm, cater to niche markets that require specialized semiconductor devices.
Wafer Diameter | Typical Applications |
---|---|
Up to 100 mm | Specialized devices |
100 mm – 150 mm | MEMS, Sensors |
150 mm – 200 mm | RF Devices, Power Semiconductors |
200 mm – 300 mm | ICs, Logic Devices |
Above 300 mm | Advanced Microelectronics |
The market for silicon wafers is also influenced by the surge in demand for power electronics and optoelectronics devices, which require high resistivity silicon wafers for efficient energy conversion and high-speed data transmission.
Segmentation by Type: Polished, Annealed, and SOI Wafers
In the realm of silicon wafer manufacturing, the market is segmented by various types of wafers, each serving distinct purposes and applications. Polished wafers are known for their smooth surface, which is essential for high-precision devices. Annealed wafers undergo a heat treatment process to relieve internal stresses and improve their mechanical properties. Silicon-on-insulator (SOI) wafers, on the other hand, are used to create high-performance semiconductor devices with reduced parasitic capacitance.
The choice of wafer type is critical and is influenced by the intended application and performance requirements. Below is a summary of the key characteristics of each wafer type:
- Polished Wafers: Ideal for high-precision applications, offering a defect-free surface.
- Annealed Wafers: Heat-treated to enhance mechanical properties and reduce defects.
- SOI Wafers: Provide an insulating layer that improves performance and reduces power consumption.
Understanding these distinctions is crucial for semiconductor manufacturers as they strive to meet the evolving demands of the industry and deliver products that align with the latest technological advancements.
Application-Based Market Trends: From ICs to Power Semiconductors
The silicon wafer market is witnessing a significant transformation, driven by diverse applications ranging from integrated circuits (ICs) to power semiconductors. The market’s growth trajectory is underscored by the increasing demand for high-performance computing and energy-efficient devices. The Global Silicon Wafer Market, valued at $15.4 billion in 2022, is projected to reach $25.9 billion by 2032, growing at a CAGR of 5.4%.
In the realm of power electronics, the surge in electric vehicles (EVs) and renewable energy systems has catalyzed the need for advanced silicon carbide (SiC) and gallium nitride (GaN) wafers. These materials are pivotal for high-efficiency power conversion. The consolidation and growth in the SiC market, particularly with the integration of SiC epitaxy, reflect the industry’s adaptation to these emerging needs.
Market segmentation reveals a nuanced picture, with polished, annealed, and Silicon on Insulator (SOI) wafers each finding their niche. Polished wafers continue to dominate for standard ICs, while SOI wafers are gaining traction in RF and power applications due to their superior insulation properties.
- Integrated Circuits (ICs): The mainstay of microelectronics, driving the demand for polished wafers.
- Power Semiconductors: Increasingly adopting SiC and GaN for higher efficiency, impacting the market for specialized wafers.
- RF Devices: SOI wafers are preferred for their insulation benefits, essential in reducing interference.
As the industry evolves, the market trends reflect a shift towards more complex and profitable semiconductor packaging, indicating a broader trend of increasing complexity and value in the semiconductor ecosystem.
Innovations in Semiconductor Device Manufacturing
Emerging Patterning Technologies and Their Impact
The semiconductor industry is witnessing a transformative phase with the introduction of emerging patterning technologies. These advancements are crucial for the development of leading-edge chips, which are the cornerstone of modern electronics. Among these, double patterning techniques have become increasingly significant, allowing for finer features on chips by using multiple passes of a laser. This method has evolved with methodologies such as colored and colorless flows, enhancing the precision of semiconductor devices.
Applied Materials, a key player in the industry, has expanded its portfolio with technologies like the Producer XP Pioneer CVD patterning film and the Sym3 Y Magnum etch system. The Sculpta pattern-shaping system, in particular, has gained traction for its ability to refine EUV patterning and reduce defects. By lowering costs and improving yields, these innovations are setting new benchmarks for chipmaking in the angstrom era.
The impact of these technologies is not limited to manufacturing efficiency; they also play a pivotal role in driving the future of the semiconductor industry. As the demand for smarter and more capable devices grows, the reliance on advanced manufacturing techniques, including AI and IoT applications, becomes more pronounced. The table below summarizes the key emerging patterning technologies and their contributions to the industry:
Technology | Description | Impact |
---|---|---|
Double Patterning | Multiple laser passes for finer features | Enhanced precision |
Sculpta Pattern-Shaping | Refines EUV patterning, reduces defects | Lower costs, improved yields |
Producer XP Pioneer CVD | Advanced film for patterning | Complements lithography |
These technologies are not only shaping the present landscape of semiconductor manufacturing but are also pivotal in ensuring the industry’s growth, aligning with the broader technological trends.
Reducing Etch Variation: Techniques and Benefits
In the pursuit of ever-smaller and more efficient semiconductor devices, reducing etch variation has become a critical aspect of manufacturing. Etch variation can lead to significant performance discrepancies and yield loss, making its minimization a high priority. Design techniques and analysis tools are pivotal in achieving this, as they help to minimize the range of variability that can cause failure, thus increasing yield.
The introduction of systems like the Sym3 Y Magnum etch system by Applied Materials represents a leap forward in addressing etch variation. This system combines deposition and etch processes to smooth out line edge roughness before the actual etching, enhancing both yield and chip performance. Similarly, advancements in Atomic Layer Etching (ALE) allow for the precise crafting of nanoscale structures, which is essential for the fine details in devices like LEDs and high-frequency transistors.
The benefits of reducing etch variation are clear: improved device reliability, increased manufacturing yield, and the facilitation of next-generation semiconductor technologies. As dimensions shrink and the importance of atomic-level precision grows, these techniques will continue to be at the forefront of semiconductor fabrication.
The Significance of Wirebonding and Wafer Inspection in Quality Control
Wirebonding is a critical process in semiconductor manufacturing, where thin wires create interconnects between the integrated circuit (IC) and its package. This technique remains a staple in the industry due to its reliability and cost-effectiveness. Ensuring the integrity of these connections is paramount, as they are essential for the functionality of the final product.
Wafer inspection, on the other hand, is the science of detecting defects on silicon wafers. It is a non-negotiable step in quality control, as even the smallest imperfection can lead to device failure. Advanced inspection techniques are employed to identify and categorize defects, which can arise from various sources during the fabrication process.
The following table summarizes the common defects found during wafer inspection and their potential impacts:
Defect Type | Source | Potential Impact |
---|---|---|
Particulates | Contamination | Circuit failure |
Crystallographic defects | Imperfect crystal growth | Electrical abnormalities |
Pattern irregularities | Lithography errors | Functional inconsistencies |
As the industry moves towards smaller process nodes and more complex packaging techniques, the role of wirebonding and wafer inspection will only grow in importance. Manufacturers must continue to innovate and refine these processes to maintain high standards of quality and reliability in semiconductor devices.
Challenges and Opportunities in Silicon Wafer Semiconductor Industry
Addressing the Reliability Concerns in IC Design
Ensuring the reliability of integrated circuits (ICs) is a critical aspect of semiconductor manufacturing. As ICs become more complex, the potential for variability and defects increases. Testing procedures verify that ICs conform to predetermined quality standards, minimizing the likelihood of defective products reaching consumers. Extensive testing is not just a final step but an integral part of the design and production process.
To address reliability concerns, manufacturers employ a variety of strategies. These include the addition of in-circuit monitors and the consideration of circuit aging during the design phase. The table below outlines some key reliability enhancement techniques:
Technique | Description |
---|---|
In-Circuit Monitors | Real-time tracking of performance to anticipate failures. |
Design for Variability | Accounting for changes in performance over time and use. |
Post-Silicon Timing Analysis | Ensuring timing accuracy after the chip is fabricated. |
Electrical Line Resistance Checks | Verifying resistance levels to prevent electromigration. |
The industry is also witnessing a rise in the use of formal verification methods, which provide a mathematical proof that a design adheres to specified properties. This approach is becoming more prevalent as the variability becomes more problematic and diverse at advanced semiconductor nodes. By combining these techniques, manufacturers can significantly reduce test escapes and improve the overall reliability of ICs.
Cost Management at the Forefront of Process Nodes
As semiconductor devices continue to evolve, cost management has become a critical factor in the production of integrated circuits (ICs). The complexity of chips is on the rise, and with it, the need for advanced process nodes that can handle the increased density of transistors. However, this advancement comes with significant financial implications.
The tradeoffs between enhancing IC quality and managing production costs are becoming increasingly challenging. Balancing reliability against cost is essential, especially as devices become more domain-specific and chip complexity surges. The hidden costs and tradeoffs in IC quality are not always apparent, making it crucial for manufacturers to carefully consider their process node strategies.
To illustrate the financial considerations at different process nodes, here is a simplified cost comparison:
Process Node (nm) | Development Cost (USD) | Production Cost per Wafer (USD) |
---|---|---|
7 | 300 million | 10,000 |
10 | 150 million | 7,500 |
14 | 120 million | 6,000 |
These figures highlight the exponential increase in costs as the industry moves towards more advanced nodes. It is imperative for companies to optimize their processes and manage expenses to remain competitive in the market.
Post-Silicon Timing Analysis and Electrical Line Resistance Issues
In the semiconductor industry, post-silicon timing analysis is crucial for ensuring that integrated circuits meet their performance specifications after fabrication. This process involves a meticulous examination of timing paths and the identification of potential delays that could impact the overall functionality of the chip. The techniques include determining a series of variables that affect performance, determining the sensitivity of timing paths in the circuit to each variable, and implementing corrective measures to mitigate any identified issues.
Electrical line resistance, on the other hand, poses a significant challenge as semiconductor nodes advance. Increased resistance can lead to power loss and signal integrity problems, which are particularly problematic at smaller geometries. To address these issues, engineers employ various strategies, such as optimizing the physical layout and using materials with lower resistivity.
Recent discussions in the industry have highlighted the importance of balancing performance and accuracy during the timing signoff process. The following list presents some of the key considerations:
- Ensuring the precision of timing models
- Accounting for variability in manufacturing processes
- Incorporating circuit aging into variability
- Analyzing the impact of STI recess profile control on performance
These factors underscore the complexity of achieving reliable IC design and the ongoing efforts to refine post-silicon validation techniques.
Conclusion
In this comprehensive exploration of silicon wafer semiconductors, we have delved into the intricate processes of fabrication and the myriad of applications that these wafers enable. From the foundational role they play in microelectronics, MEMS, and optoelectronics to the cutting-edge developments in 3D integration and advanced patterning technologies, silicon wafers are the cornerstone of the semiconductor industry. Market segmentation has shown us the diversity in wafer types, production technologies, and applications, highlighting the tailored approaches for different electronic needs. As we have seen, the relentless pursuit of innovation in wafer inspection, ALD technology, and the securing of SiC wafer supply underscores the industry’s commitment to advancing technology. The insights gained from related blogs and industry news further emphasize the dynamic nature of this field, where reliability, cost-efficiency, and performance are continuously being optimized. Silicon wafer semiconductors are not just components; they are enablers of the technological marvels that define our modern world.
Frequently Asked Questions
What are the primary applications of high resistivity silicon wafers?
High resistivity silicon wafers are used in a variety of applications including microelectronics, MEMS, sensors, radiation detectors, optoelectronics, and in the development of high-voltage devices and isolation layers.
How has Atomic Layer Deposition (ALD) technology advanced semiconductor fabrication?
ALD technology has advanced semiconductor fabrication by enabling precise control over thin film deposition, which is crucial for developing sacrificial layers and high aspect ratio Through-Silicon Vias (TSVs), as well as for the application of metals in semiconductor devices.
What are the latest innovations in patterning technologies for semiconductor manufacturing?
The latest innovations include advanced patterning technologies that allow for the creation of finer features on semiconductor devices, essential for the progression towards smaller and more efficient electronic components.
What is the significance of wafer inspection and wirebonding in semiconductor device manufacturing?
Wafer inspection is critical for identifying defects on silicon wafers, ensuring high-quality outputs. Wirebonding is significant for creating interconnects between the integrated circuit (IC) and the package, which is vital for device functionality.
What challenges are associated with electrical line resistance in advanced semiconductor nodes?
As semiconductor nodes advance, electrical line resistance increases, which can lead to signal delay and power loss. This is a significant challenge that requires innovative solutions to ensure device reliability and performance.
How is the silicon wafer semiconductor industry segmented by wafer diameter and application?
The industry is segmented by wafer diameter into categories such as up to 100 mm, 100-150 mm, 150-200 mm, 200-300 mm, and above 300 mm. Applications include sensors, MEMS devices, RF devices, ICs, logic devices, memory, and others like RF filters and power semiconductors.