Advancements and Challenges in Wafer Manufacturing for Modern Electronics
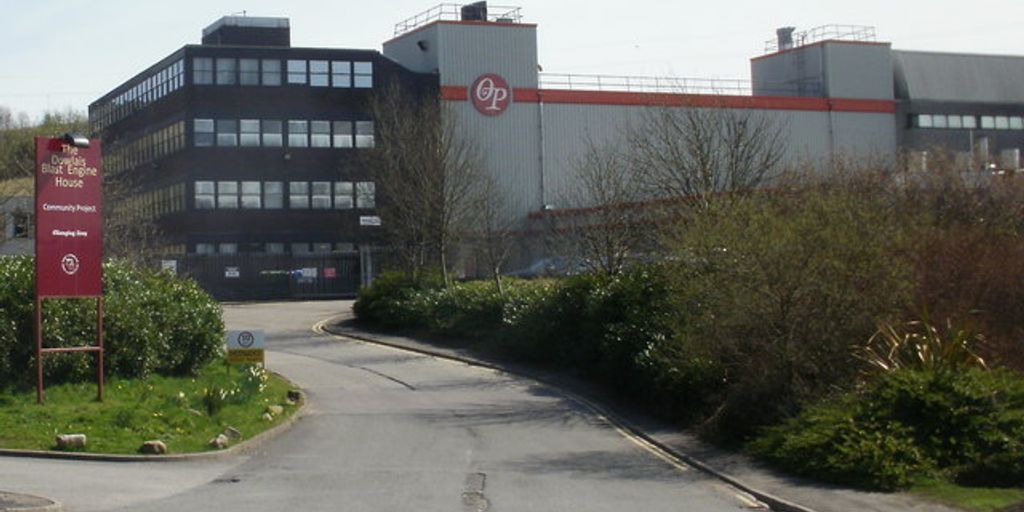
In the dynamic field of wafer manufacturing for modern electronics, the industry continuously evolves with technological advancements and faces various challenges. This article delves into the intricate processes of wafer manufacturing, exploring the significant trends, innovations, and obstacles within this crucial sector. From the importance of wafer dicing to the transformative effects of automation, we uncover the layers that make semiconductor wafers pivotal in today’s digital age.
Key Takeaways
- Wafer manufacturing is central to the semiconductor industry, influencing the performance and quality of electronic devices.
- Increasing wafer diameters and improving surface quality are primary trends that enhance production efficiency and reduce costs.
- Challenges in wafer dicing, such as die chipping and contamination, are critical to address for maintaining device quality.
- Innovations in dicing technology and materials handling are driving the industry towards higher precision and sustainability.
- The integration of automation and the shift towards larger wafers offer both challenges and opportunities for job growth and innovation.
Overview of Wafer Manufacturing
Importance in Semiconductor Industry
Silicon wafer manufacturing is pivotal in the semiconductor industry, serving as the foundational substrate for integrated circuits and microchips. This process is essential for the vast array of electronic devices that define our modern world.
Key Techniques and Processes
The journey from a single crystal to a polished, tested silicon wafer involves advanced technology and precision engineering. Key processes include crystal formation, slicing, polishing, and doping, each critical for developing the electronic structures needed in semiconductor devices.
Emerging Innovations
Innovations in wafer manufacturing aim to enhance efficiency and reduce costs, driving the development of new technologies. These advancements are crucial for meeting the increasing demands of the electronics industry and supporting the growth of new applications.
Trends in Silicon Wafer Manufacturing
Increasing Wafer Diameter
The semiconductor industry is witnessing a significant shift towards larger wafers. This trend is driven by the need to enhance production efficiency and reduce costs, allowing for more chips to be produced from a single wafer. The increasing wafer diameter is a pivotal trend shaping the future of semiconductor technology, making it more accessible and cost-effective.
Improving Surface Quality
To meet the stringent demands for high-performance electronics, improving the surface quality of silicon wafers has become crucial. Enhanced surface quality ensures better yield and performance of the final electronic devices, which is essential for maintaining competitiveness in the fast-paced tech industry.
Developing New Crystal Growth Methods
Innovation in crystal growth methods is critical for advancing the capabilities of silicon wafers. New techniques are being developed to optimize the crystal structure, which directly impacts the efficiency and performance of the wafers. These advancements are essential for keeping up with the increasing demand for high-quality microchips in various electronic applications.
Challenges in Wafer Dicing
Die Chipping and Breakage
One of the main challenges in wafer dicing is die chipping and breakage. These defects can occur when the cutting process generates excessive stress or heat, leading to fractures, cracks, or other damage to the die’s edges. Chipping and breakage can reduce the yield and overall quality of the final semiconductor devices, resulting in increased production costs. To address these issues, several strategies can be employed, including optimizing blade speed, adjusting feed rates, and using protective coatings.
Contamination and Cleanliness
Maintaining the cleanliness of the diced dies and avoiding contamination is another critical challenge. Contaminants, such as particles or residues from the dicing process, can negatively impact the performance and reliability of the final semiconductor devices. Stringent cleanliness standards are required in the semiconductor industry, making contamination control a crucial aspect of wafer dicing.
Precision and Accuracy
Achieving precision and accuracy in wafer dicing is essential for ensuring high-quality semiconductor devices and maximizing yield rates. Various strategies can be employed to enhance precision and accuracy during the wafer dicing process, such as implementing advanced vision systems, utilizing laser cutting technologies, and refining blade alignment techniques.
Innovations in Wafer Dicing Technology
Advancements in Cutting Techniques
Recent years have seen significant advancements in wafer dicing technology, particularly in cutting techniques. Advanced laser dicing systems have emerged as a leading innovation, offering higher precision and reduced damage to the wafers. These systems utilize finely tuned lasers to make precise cuts without physical contact, minimizing mechanical stress and potential contamination.
Enhancements in Material Handling
Material handling in wafer dicing has also seen innovative improvements. The introduction of automated systems and robotics has enhanced the accuracy and efficiency of the dicing process. These systems ensure delicate handling of wafers, reducing the risk of human error and improving throughput in manufacturing environments.
Improvements in Contamination Control
Controlling contamination is crucial in wafer dicing to maintain the integrity of the semiconductor devices. Recent innovations include the development of self-dicing materials and the use of plasma dicing equipment. These technologies help to minimize contamination risks by reducing the need for external mechanical forces and improving the cleanliness of the dicing environment.
The Impact of Technological Advancements and Automation
Effects on Production Efficiency
Technological advancements and automation have significantly increased production efficiency in wafer manufacturing. These innovations allow for faster processing times and reduced human error, leading to higher throughput and better quality control.
Challenges with Skilled Labor Shortages
The integration of advanced technologies necessitates a higher level of skill and training. The industry is experiencing a shortage of skilled labor, which could potentially hinder growth and innovation. Efforts to retrain and upskill workers are crucial to address this gap.
Opportunities for Job Growth
Despite the challenges, technological advancements create substantial opportunities for job growth within the sector. New roles are emerging, particularly in areas requiring specialized knowledge of automation and process optimization. This shift underscores the importance of continuous learning and adaptation in the workforce.
Production Trends and Their Implications
Shift Towards Larger Wafers
In the ever-evolving landscape of silicon wafer manufacturing, one of the most significant trends is the increasing wafer diameter. This shift not only enhances production efficiency but also helps in reducing costs, making semiconductor technology more accessible.
Cost Reduction Strategies
The drive towards larger wafers is intrinsically linked to cost reduction strategies. By producing more chips from a single wafer, manufacturers can decrease the cost per chip, which is crucial in a highly competitive market.
Opportunities for Innovation
The exploration and integration of new semiconductor materials are emerging as pivotal trends. These materials could offer superior electrical, thermal, or optical properties, opening the door to new technologies and applications previously deemed unattainable.
The Role of Silicon Wafers in Modern Technology
Applications in Electronics
Silicon wafers are integral to the production of a wide array of electronic devices, including computers, smartphones, and solar panels. Their role as the substrate for integrated circuits and microchips makes them a cornerstone of the semiconductor industry. The precision in manufacturing these wafers directly influences the performance and efficiency of the final electronic products.
Growth Driven by Demand
The demand for more advanced and efficient electronics has led to significant growth in the silicon wafer industry. This growth is not only a testament to the increasing reliance on electronic devices but also highlights the critical role of silicon wafers in enabling technological advancements. The industry’s expansion is propelled by the continuous need for innovation in electronics.
Challenges and Opportunities
While the industry faces challenges such as the need for high precision and the risk of contamination during manufacturing, these are also areas ripe for innovation. Opportunities for job growth and technological breakthroughs are abundant, as the industry seeks to overcome these hurdles and meet the growing global demand for high-quality silicon wafers.
Future Directions in Wafer Manufacturing
Sustainability Initiatives
The semiconductor industry is increasingly embracing sustainability initiatives, focusing on renewable energy sources and reducing environmental impact. This shift not only aligns with global environmental goals but also enhances the industry’s reputation and long-term viability.
Integration of Alternative Materials
The integration of alternative materials is set to revolutionize wafer manufacturing. Materials such as silicon carbide and gallium nitride offer superior properties that can significantly improve the performance and efficiency of electronic devices.
Anticipated Technological Breakthroughs
Exciting technological breakthroughs are anticipated in the near future, driven by relentless innovation and research. These advancements promise to further elevate the capabilities of semiconductors, making them more efficient, faster, and more reliable.
Conclusion
In conclusion, the advancements and challenges in wafer manufacturing for modern electronics highlight a dynamic and evolving industry. From increasing wafer diameters to improving surface quality and exploring new crystal growth methods, the industry is pushing the boundaries of technology to meet the rising demand for sophisticated electronic devices. However, challenges such as die chipping, contamination, and the need for precision continue to test the limits of current technologies. The future of semiconductor manufacturing lies in addressing these challenges while embracing innovative solutions that enhance efficiency and sustainability. As the industry continues to evolve, it will undoubtedly play a pivotal role in shaping the technological landscape of tomorrow.
Frequently Asked Questions
What are semiconductor wafers?
Semiconductor wafers are thin slices of semiconductor material, such as silicon, used as the substrate for integrated circuits and other electronic devices. They are fundamental to modern electronics like computers, smartphones, and solar panels.
What are the main challenges faced during the wafer dicing process?
The primary challenges during wafer dicing include die chipping and breakage, contamination and cleanliness, and precision and accuracy. Addressing these challenges is crucial for ensuring high-quality semiconductor devices and maximizing yield rates.
What are some innovations in wafer dicing technology?
Innovations in wafer dicing technology include advancements in cutting techniques, enhancements in material handling, and improvements in contamination control. These developments help address the challenges of complex semiconductor devices.
How is the semiconductor industry impacted by increasing wafer diameter?
Increasing the wafer diameter allows more chips to be produced from a single wafer, enhancing production efficiency and reducing costs. This trend is significant as it makes semiconductor technology more accessible and economical.
What opportunities does technological advancement and automation offer in semiconductor manufacturing?
Technological advancements and automation improve production efficiency, reduce costs, and increase the yield of semiconductor manufacturing. They also create opportunities for job growth, particularly in areas driven by the demand for advanced electronics and renewable energy.
What role do sustainability initiatives play in the future of wafer manufacturing?
Sustainability initiatives in wafer manufacturing focus on reducing environmental impact, integrating alternative materials, and promoting energy efficiency. These efforts are crucial for meeting global sustainability goals and ensuring the industry’s long-term viability.