Advancements in Wafer Growth: Exploring New Technologies
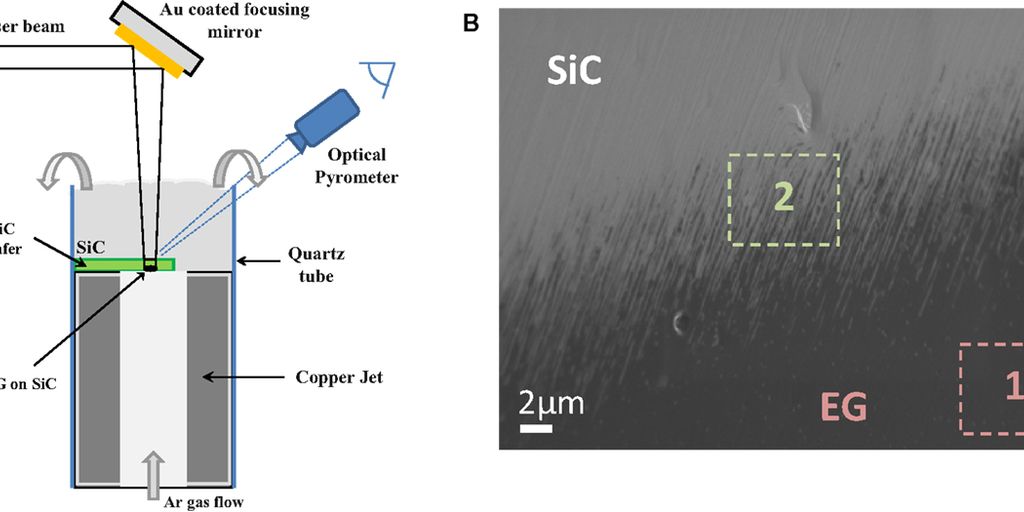
Silicon wafer technology is a driving force in the world of electronics. From smartphones to computers, these tiny slices of silicon are at the heart of many devices we use daily. This article dives into the latest advancements in wafer growth, showcasing new techniques and technologies that are pushing the boundaries of what is possible.
Key Takeaways
- New methods in epitaxial growth are helping create more complex and efficient structures.
- Innovations in ultra-thin silicon wafer manufacturing are achieving better thickness control and quality.
- Laser dicing technology is improving the precision and surface quality of wafers.
- Larger wafer sizes are boosting productivity and efficiency in semiconductor manufacturing.
- Automation in wafer handling is leading to greater accuracy and faster production processes.
Epitaxial Growth Techniques
Layer Deposition Methods
Scientists are always looking for new ways to grow silicon crystals better and faster. These new methods help make crystals that are super pure and work great in electronics. This means our gadgets can keep getting smaller and better.
Heterostructure Formation
Epitaxial growth is key for making complex structures called heterostructures. These structures have special layers that improve how devices work. By carefully adding these layers, we can make electronics that are more powerful and use less energy.
Material Quality Enhancement
Improving the quality of the materials used in epitaxial growth is crucial. Better materials mean better performance for the devices we use every day. Researchers are finding ways to make these materials even purer and more efficient, which helps in making advanced electronic devices.
Ultra-Thin Silicon Wafer Manufacturing
Manufacturing ultra-thin silicon wafers is pushing the limits of silicon wafer thinness. These wafers are known for their reduced thickness, which offers benefits like better flexibility, higher integration density, and improved performance. They are used in many semiconductor technologies, such as microelectronics, sensors, and optoelectronics. Achieving precise thickness control and uniformity is crucial for their successful production.
Advancements in Wafer Dicing Technology
Recent advancements in wafer dicing technology have led to significant improvements in precision, reduced damage, and increased throughput. These innovations are crucial for meeting the stringent requirements of modern semiconductor manufacturing.
Laser Dicing Systems
Laser dicing systems represent a major leap forward in wafer dicing technology. These systems use focused laser beams to cut wafers with high precision, minimizing physical damage and contamination. This method ensures cleaner cuts and higher accuracy, which is essential for producing high-quality semiconductor devices.
Precision Improvement
Innovative approaches, such as novel dicing techniques and materials, have allowed for higher precision in the dicing process. Equipment and tooling innovations, including different types of dicing saws and blades, play a vital role in achieving superior quality and performance. These advancements ensure that the dicing process meets the high standards of the semiconductor industry.
Surface Quality Enhancement
Advanced surface treatment and cleaning technologies are essential for improving surface quality, minimizing defects, and ensuring high-quality wafer production. These technologies help maintain the cleanliness and accuracy required for modern semiconductor devices.
The wafer dicing services market is projected to reach USD 838.9 million by 2032, growing at a CAGR of 4.21% from 2023-2031. This growth highlights the increasing demand for advanced dicing technologies in the semiconductor industry.
Increasing Wafer Diameter for Enhanced Productivity
Benefits of Larger Wafer Sizes
One of the main innovations in silicon wafer technology is the move to larger wafer sizes. Larger wafers, like 300mm and beyond, offer several benefits. Increased productivity is a major advantage, as the larger surface area allows for more devices to be made on a single wafer. This leads to higher device yield and lower costs. The bigger surface area also means more devices can be integrated, boosting performance and functionality.
Technological Challenges
Moving to 450mm (18 inches) wafers can further boost productivity. However, this change comes with its own set of challenges. Stress on the wafer can improve yield and die quality, but it also needs advanced handling and processing techniques to keep the wafer intact.
Future Prospects
As technology advances, the industry is shifting towards larger wafers. This change not only makes production more efficient but also helps in cutting costs. This makes semiconductor technology more accessible to everyone.
New Crystal Growth Methods
The development of new methods of crystal growth is at the forefront of research in the field. Scientists and engineers are constantly exploring innovative techniques to grow silicon crystals more efficiently and with even greater purity. These advancements aim to produce crystals with optimal electrical properties for semiconductor applications, ensuring the continued miniaturization and enhancement of electronic devices.
Automation in Wafer Handling
Automation in wafer handling is transforming the semiconductor industry. Modern machinery and robotic systems are now essential for moving and handling wafers with utmost precision and efficiency. These technologies not only enhance productivity but also reduce human intervention, streamlining the manufacturing process.
Future Trends in Silicon Wafer Technology
The silicon wafers for semiconductor market evaluation provides insights into major business trends that will impact growth between 2024 and beyond. As demand for advanced electronic devices rises, the market is expected to see significant expansion. This growth is driven by the need for more efficient and powerful semiconductors.
To stay competitive, companies are investing heavily in research and development. This investment is crucial for discovering new materials and improving existing technologies. By focusing on innovation, the industry aims to meet the ever-growing demands for better performance and reliability in electronic devices.
The semiconductor industry must adapt to changing market needs. This includes developing new technologies that can handle higher performance requirements and more complex applications. As technology evolves, so does the need for more advanced silicon wafers, pushing the industry to continuously innovate and improve.
Conclusion
In conclusion, the advancements in wafer growth technology are paving the way for a new era in the semiconductor industry. From epitaxial growth techniques to ultra-thin wafer manufacturing and innovative dicing methods, each development brings us closer to more efficient and powerful electronic devices. The continuous push for larger wafer sizes, better surface quality, and new materials ensures that the industry remains at the forefront of technological innovation. As we move forward, these advancements will not only enhance the performance of electronic devices but also open up new possibilities for future technologies. The journey of innovation in wafer growth is ongoing, and its impact on the semiconductor industry is profound and far-reaching.
Frequently Asked Questions
What is epitaxial growth in semiconductor manufacturing?
Epitaxial growth is a method used to add layers of material on a wafer. This helps in creating complex structures with better properties.
How are ultra-thin silicon wafers made?
Ultra-thin silicon wafers are made using advanced thinning techniques and thin film transfer technologies to ensure precise thickness control.
What advancements have been made in wafer dicing technology?
Recent advancements in wafer dicing technology include the use of laser dicing systems, which improve precision and surface quality.
Why are larger wafer sizes beneficial?
Larger wafer sizes, like 300mm and beyond, are beneficial because they increase productivity, yield more devices, and reduce costs.
What are some new methods for growing crystals in wafers?
New methods for growing crystals in wafers include the use of alternative materials and techniques to improve efficiency and quality control.
How does automation improve wafer handling?
Automation in wafer handling improves accuracy and efficiency in manufacturing and helps integrate new systems with existing ones.