Advances in Wafer Fabrication Technology
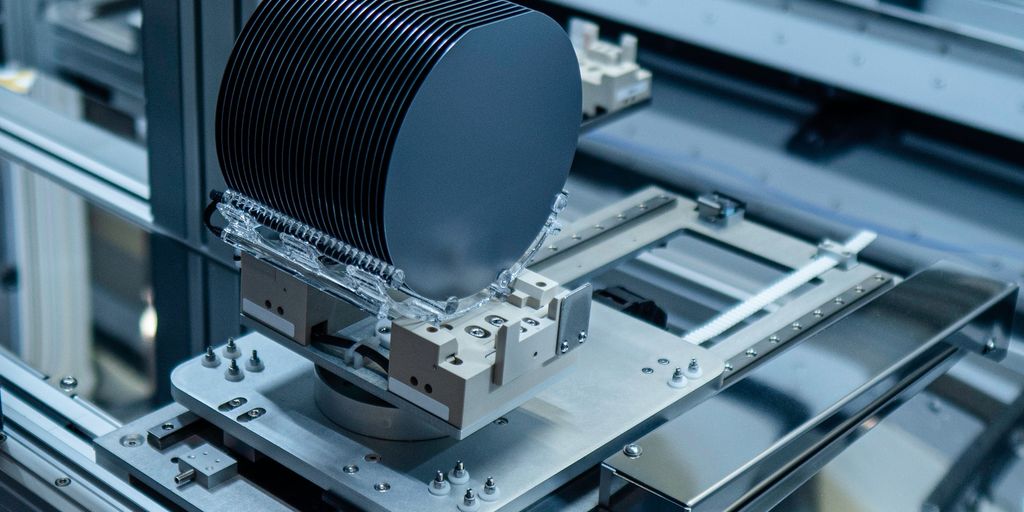
The realm of wafer fabrication technology is witnessing remarkable advancements that are setting new standards in semiconductor manufacturing. These innovations encompass a broad spectrum of developments, from enhanced equipment precision to the integration of cutting-edge materials and techniques. This article delves into the latest trends and technologies that are shaping the future of wafer fabrication, highlighting their implications and benefits for the industry.
Key Takeaways
- Advancements in wafer fabrication equipment are crucial for meeting the increasing precision requirements of modern semiconductor manufacturing.
- Customization and flexibility in fabrication processes are essential to adapt to complex and specific semiconductor design needs.
- The integration of nanotechnology in wafer fabrication is revolutionizing the industry by enhancing process control and enabling material manipulation at the atomic level.
- Emerging materials and novel crystal growth techniques are paving the way for more efficient and higher quality semiconductor production.
- The development of technologies like TSMC’s ‘chip on wafer on substrate’ is pushing the boundaries of transistor density and integrated circuit design.
Advancements in Wafer Fabrication Equipment
Enhanced Precision and Control
The relentless pursuit of miniaturization in semiconductors has necessitated enhanced precision and control in wafer fabrication equipment. The ability to maintain exacting standards is crucial as the complexity and the diminutive size of semiconductor structures escalate. This precision ensures high output quality and minimizes component rejection rates, which are critical for cost-effective manufacturing.
Automation in Semiconductor Manufacturing
Automation has become a cornerstone in modern semiconductor manufacturing, offering significant improvements in both efficiency and reliability. Comprehensive automation solutions provided by equipment suppliers are essential for meeting the increasing demands of advanced semiconductor device development.
Reducing Manual Handling and Costs
The shift towards automation not only enhances the precision but also significantly reduces manual handling of wafers. This reduction in physical handling helps in minimizing the risk of contamination and damage, thereby improving yield rates. Moreover, automation plays a pivotal role in cutting down operational costs and boosting productivity in fabrication facilities.
Customization in Wafer Fabrication Processes
Meeting Specific Manufacturing Needs
In the semiconductor industry, the ability to meet specific manufacturing needs is crucial. Customization in wafer fabrication processes allows manufacturers to adapt equipment and techniques to the unique requirements of each semiconductor product. This adaptability is essential for maintaining high precision and process optimization.
Adapting to Complex Semiconductor Designs
As semiconductor designs become increasingly complex, the need for adaptable wafer fabrication processes becomes more apparent. Customized equipment can handle the intricate details of advanced semiconductor structures, ensuring that each component meets stringent quality standards.
Flexibility in Production Techniques
Flexibility in production techniques is vital for responding quickly to market changes and technological advancements. Customized wafer fabrication processes enable manufacturers to switch between different production methods with ease, thereby enhancing overall efficiency and reducing time-to-market for new semiconductor products.
The Role of Wet Processing in Semiconductor Prototyping
Importance of Cleanliness
In semiconductor prototyping, maintaining an immaculate environment is crucial. Wet processing ensures that each wafer is free from contaminants, which is essential for the high precision required in later stages like photolithography and etching.
Precision in Early Stages
The early stages of semiconductor fabrication set the foundation for device functionality. Accurate wet processing techniques are vital to ensure that subsequent layers and patterns align correctly, impacting the overall device performance.
Efficiency in Prototype Development
Wet processing not only enhances the cleanliness and precision but also contributes to the efficiency of the prototyping process. Streamlined wet processing steps can significantly reduce the time from concept to prototype, accelerating the pace of innovation in semiconductor technology.
Nanotechnology in Wafer Fabrication
Manipulating Materials at the Atomic Level
Nanotechnology has revolutionized wafer fabrication by enabling the manipulation of materials at the atomic or molecular level. This precision allows for the development of wafers with enhanced functionalities and superior performance characteristics.
Driving Innovation and Collaboration
Nanotechnology fosters significant innovation and collaboration within the semiconductor industry. It facilitates the exchange of knowledge and the development of new technologies, which are crucial for advancing the field.
Enhancing Process Control and Automation
The integration of nanotechnology in wafer fabrication has led to improvements in process control and automation. Nanotechnology-enabled sensors and monitoring devices provide real-time insights, which help in optimizing equipment performance and reducing downtime.
Emerging Materials in Wafer Fabrication
Two-Dimensional Materials
The exploration of two-dimensional materials is revolutionizing the semiconductor industry. These materials are critical for developing advanced electronic devices with enhanced properties such as improved electrical and thermal performance.
Monolithic 3D Integrated Circuits
Monolithic 3D Integrated Circuits represent a significant leap in semiconductor design. By stacking layers of circuits directly on top of each other, these circuits promise a substantial increase in transistor density and functionality.
Alternative to Silicon
As the industry seeks to surpass the limitations of traditional silicon, alternative materials are being explored. These materials not only promise to enhance the performance of electronic devices but also open the door to new technologies and applications that were previously unattainable.
Advances in Crystal Growth Techniques
Improving Wafer Surface Quality
The quest for perfection in semiconductor manufacturing drives the continuous improvement of wafer surface quality. Techniques such as chemical mechanical polishing and advanced epitaxial growth ensure surfaces are defect-free, which is crucial for the subsequent microfabrication processes.
Developing New Methods
Innovative crystal growth methods are pivotal in advancing semiconductor technology. Researchers are exploring new ways to enhance the efficiency and purity of silicon crystals, which are essential for the industry’s progression towards miniaturization and enhanced electronic devices.
Future of Semiconductor Efficiency
The semiconductor industry is poised for transformative changes with the development of new crystal growth techniques. These advancements promise to elevate the efficiency and quality of future electronic devices, steering the industry towards broader technological horizons.
The Impact of Silicon Interposers in Wafer Fabrication
Silicon interposers have revolutionized the semiconductor industry by enabling more complex and powerful integrated circuits. These components are crucial for achieving high-density and high-performance chip architectures.
TSMC’s Chip on Wafer on Substrate Technology
TSMC’s development of the CoWoS-S technology, which integrates chip on wafer on substrate, has set a benchmark in the industry. This technology allows for the integration of multiple chips and memory devices into a single package, significantly enhancing performance and reducing latency.
Largest Silicon Interposer Development
The development of the world’s largest silicon interposer, measuring nearly 2500mm2, marks a significant milestone. This interposer supports the integration of dual 600mm2 processors and multiple HBM memory devices, paving the way for advancements in high-performance computing and other demanding applications.
Enhancing Transistor Density
The use of silicon interposers has been instrumental in enhancing transistor density. This improvement is vital for the development of more efficient and compact electronic devices. The ongoing research and development in this area promise further enhancements, potentially leading to even more sophisticated semiconductor technologies.
Conclusion
The advancements in wafer fabrication technology have been pivotal in meeting the growing demands of the semiconductor industry. With the integration of nanotechnology, automation, and advanced packaging techniques, manufacturers are able to achieve higher precision and efficiency in production. These technological strides not only enhance the capabilities of semiconductor devices but also drive down costs and foster innovation. As the industry continues to evolve, the future of wafer fabrication looks promising, with potential breakthroughs in materials and processes that could redefine the technological landscape.
Frequently Asked Questions
What are the recent advancements in wafer fabrication equipment?
Recent advancements in wafer fabrication equipment include enhanced precision and control, increased automation, and a reduction in manual handling. These improvements have allowed fabrication shops to increase productivity and reduce costs while meeting the stricter requirements of modern semiconductor manufacturing.
How does customization benefit wafer fabrication processes?
Customization in wafer fabrication processes allows for meeting specific manufacturing needs, adapting to complex semiconductor designs, and providing flexibility in production techniques. This ensures that the fabrication process can accommodate the precision and cleanliness required at every stage of production.
What role does wet processing play in semiconductor prototyping?
Wet processing is crucial in semiconductor prototyping for maintaining cleanliness and precision in the early stages of development. This process is essential for ensuring the efficiency and effectiveness of prototype development, leading to better quality and yield in semiconductor production.
How is nanotechnology impacting wafer fabrication?
Nanotechnology plays a pivotal role in wafer fabrication by manipulating materials at the atomic level, driving innovation, and enhancing process control and automation. It enables new functionalities and promotes collaboration within the semiconductor industry, revolutionizing the manufacturing processes.
What are some emerging materials in wafer fabrication?
Emerging materials in wafer fabrication include two-dimensional materials and Monolithic 3D Integrated Circuits. These materials offer alternatives to traditional silicon and aim to improve transistor density and overall semiconductor performance.
What are the latest developments in crystal growth techniques?
The latest developments in crystal growth techniques focus on improving wafer surface quality, developing new methods, and enhancing the overall efficiency of semiconductors. These advancements promise to propel the semiconductor industry towards greater efficiency and technological innovation.