An In-Depth Look at Wafer Probe Systems
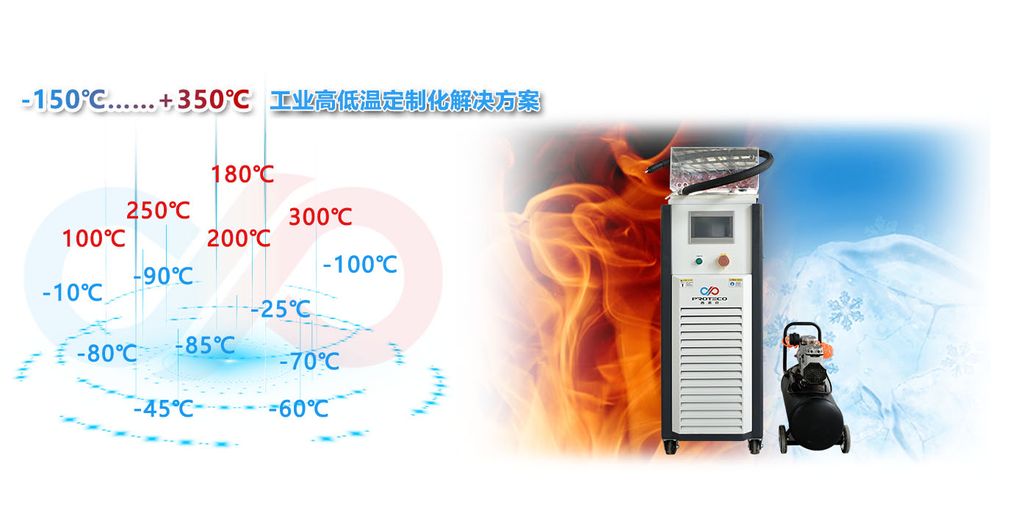
Wafer probe systems are crucial tools in the semiconductor industry. They help test and ensure the quality of tiny circuits on silicon wafers. This article will explore the basics, types, technical aspects, applications, challenges, and future trends of wafer probing systems.
Key Takeaways
- Wafer probing is essential for testing the electrical performance of circuits on silicon wafers.
- There are both manual and automated wafer probing systems, each with its own advantages.
- Technical aspects like temperature variations and accuracy play a significant role in wafer probing.
- Wafer probing is used for tasks like testing prototype integrated circuits and evaluating defects.
- Future trends in wafer probing include advancements in probe card design and the integration of AI.
The Basics of Wafer Probing
What is Wafer Probing?
Wafer probing is a crucial step in semiconductor development and manufacturing. During this process, each die on a wafer is electrically tested. This is done using an automated wafer probing system, which holds the wafer on a stable mount and places very thin pins on designated probe pads on the die. These probe pads, also known as contact or connection pads, are essential for establishing an electrical path between the wafer and the tester.
Importance in Semiconductor Manufacturing
Wafer probing holds significant importance in semiconductor and microelectronics manufacturing. It ensures that each integrated circuit (IC) on the wafer functions correctly before moving on to the next stage of production. This step is vital for assessing the characteristics of prototype integrated circuits and evaluating defect signs. Additionally, it provides highly accurate measurements and evaluations of a test element group (TEG) for an IC, which includes transistors, connectors, and other components.
Key Components of a Wafer Probe System
A wafer probe system consists of several key components:
- Probe Card: This is placed onto a prober and connected to a tester, establishing an electrical path between the wafer and the tester. The probe card connects with the pads of the IC chips on the wafer using its metallic elements or needles to transmit electrical data and necessary test parameters.
- Prober: This holds the wafer and positions the probe card accurately.
- Tester: This device sends electrical signals through the probe card to test the ICs on the wafer.
These components work together to ensure that the wafer probing process is efficient and accurate.
Types of Wafer Probing Systems
Wafer probing systems come in various types, each suited for different needs in semiconductor manufacturing. Understanding these types helps in choosing the right system for specific applications.
Manual Wafer Probing
Manual wafer probing is often used for initial testing and evaluation. It involves a technician manually positioning the wafer and probe card. This method is highly accurate but can be time-consuming and labor-intensive. It’s ideal for prototype integrated circuits and defect evaluation.
Automated Wafer Probing
Automated wafer probing systems are designed for high-volume production. These systems can perform tests quickly and with minimal human intervention. They are equipped with features like customizable setup and programming, and autonomous operation, making them efficient and reliable. Automated systems are essential for large-scale semiconductor manufacturing.
Comparison of Different Systems
When comparing manual and automated wafer probing systems, several factors come into play:
Feature | Manual Wafer Probing | Automated Wafer Probing |
---|---|---|
Accuracy | High | Moderate to High |
Speed | Slow | Fast |
Labor Requirement | High | Low |
Ideal for | Prototypes, Defects | High-volume Production |
Each system has its own strengths and weaknesses, and the choice depends on the specific requirements of the task at hand.
Technical Aspects of Wafer Probing
Electrical Testing Procedures
Electrical testing in wafer probing is crucial for ensuring the functionality of each die on a wafer. Wafer probing involves using a probe card to establish an electrical path between the wafer and the tester. This process helps identify defects in individual components before further processing.
Temperature Variations and Their Impact
Wafer probing systems must operate effectively under various temperature conditions. Testing wafers at both low and high temperatures ensures their reliability. Temperature variations can affect the accuracy of measurements, making it essential to control the testing environment.
Accuracy and Precision in Measurements
Achieving high accuracy and precision in wafer probing is vital. The system must place probes precisely on designated pads to ensure reliable data. This accuracy is paramount for evaluating prototype integrated circuits and other components.
Applications of Wafer Probing
Prototype Integrated Circuits
Wafer probing is essential for testing prototype integrated circuits (ICs). It helps engineers verify the functionality of new designs before mass production. This step ensures that only functional ICs move forward in the manufacturing process. By catching issues early, companies save time and resources.
Defect Evaluation
Another critical application is defect evaluation. Wafer probing identifies defects in the semiconductor material or the manufacturing process. Engineers can then analyze these defects to improve future production runs. This process is vital for maintaining high-quality standards in semiconductor manufacturing.
Test Element Group (TEG) Analysis
Wafer probing is also used for Test Element Group (TEG) analysis. TEGs are small test structures on a wafer that help in evaluating the performance of various components like transistors and connectors. By probing these elements, engineers can gather data to optimize the design and manufacturing process. This ensures that the final product meets all performance criteria.
Challenges in Wafer Probing
Common Issues and Solutions
Wafer probing is a critical step in semiconductor manufacturing, but it comes with its own set of challenges. One common issue is the misalignment of probe pins, which can lead to inaccurate test results. To solve this, regular calibration and maintenance of the probing system are essential. Another frequent problem is the wear and tear of probe cards, which can be mitigated by using high-quality materials and implementing routine inspections.
Impact of Overtravel and Scrub Marks
Overtravel occurs when the probe pins press too hard on the wafer, causing damage. This can result in scrub marks, which are tiny scratches on the wafer surface. These marks can affect the performance of the integrated circuits. To minimize overtravel, it’s important to carefully control the force applied by the probe pins. Using advanced materials for probe tips can also help reduce the occurrence of scrub marks.
Maintaining High Planarity
High planarity is crucial for accurate wafer probing. If the wafer or the probe card is not perfectly flat, it can lead to uneven contact and unreliable test results. Achieving high planarity involves precise engineering and regular maintenance. Automated systems with real-time feedback can help maintain the required level of flatness, ensuring consistent and accurate measurements.
Future Trends in Wafer Probing Technology
Advancements in Probe Card Design
The design of probe cards is evolving rapidly. New materials and technologies are being used to create more durable and precise probe cards. These advancements help in handling the exponential growth in chip densities and the resulting tight pitches. Methods like cobra probing and micro spring probing are becoming more common, despite their higher costs.
Integration with AI and Machine Learning
Artificial Intelligence (AI) and Machine Learning (ML) are starting to play a significant role in wafer probing. These technologies can analyze vast amounts of data quickly and accurately, leading to better defect detection and process optimization. AI and ML can also predict potential issues before they occur, making the process more efficient.
Sustainability and Efficiency Improvements
The future of wafer probing also includes a focus on sustainability and efficiency. Companies are looking for ways to reduce waste and energy consumption in the probing process. This includes developing more energy-efficient machines and finding ways to recycle materials used in the process. Overall, the future growth prospects for the probe stations for semiconductor and wafer testing market are promising, but companies will need to overcome various challenges to achieve these goals.
Conclusion
In conclusion, wafer probe systems play a crucial role in the semiconductor industry. They help ensure the quality and functionality of integrated circuits before they move on to the next stages of production. By using automated systems to test each die on a wafer, manufacturers can identify and address defects early, saving time and resources. The precision and reliability of these systems are essential for producing high-performance electronic devices. As technology continues to advance, wafer probe systems will likely become even more sophisticated, further enhancing their importance in the manufacturing process.
Frequently Asked Questions
What is wafer probing?
Wafer probing is a process in semiconductor manufacturing where each die on a wafer is electrically tested. This helps ensure the functionality of the wafers before they move on to the next production stage.
Why is wafer probing important in semiconductor manufacturing?
Wafer probing is crucial because it helps identify defects and ensures the reliability of the integrated circuits. This step is essential for maintaining high production quality.
What are the main components of a wafer probe system?
A wafer probe system typically includes a wafer chuck to hold the wafer, a probe card with tiny needles to make contact with the die, and a tester to send and receive electrical signals.
How do manual and automated wafer probing systems differ?
Manual wafer probing is done by hand and is usually used for testing prototype circuits, while automated systems use machines to test multiple wafers quickly and accurately.
What challenges are associated with wafer probing?
Common challenges include dealing with overtravel and scrub marks, maintaining high planarity, and ensuring precise measurements despite temperature variations.
What future trends are expected in wafer probing technology?
Future trends include advancements in probe card design, the integration of AI and machine learning for better accuracy, and improvements in sustainability and efficiency.