An Overview of the Various Types of Automation in Industry
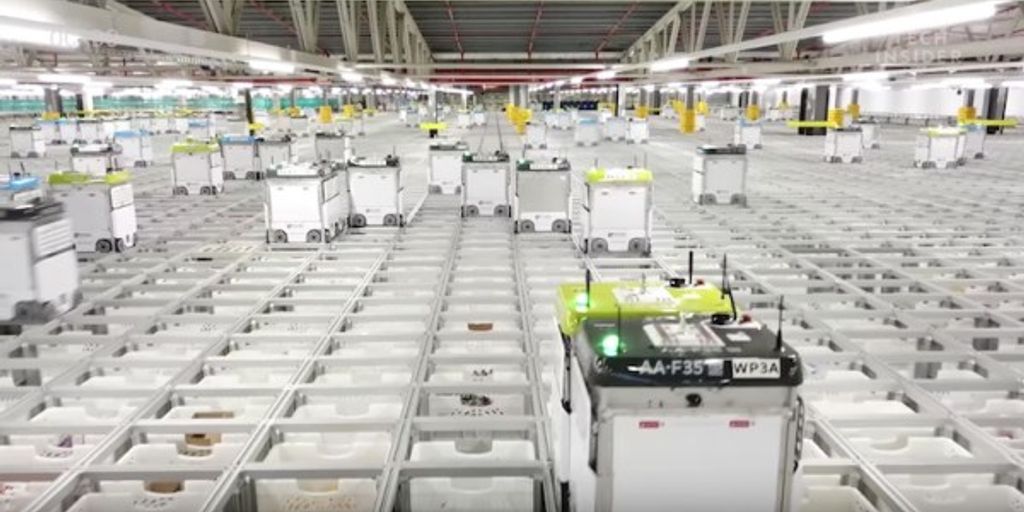
The realm of industrial automation embodies a vast array of technologies and methodologies designed to enhance efficiency and productivity across various sectors. This comprehensive overview delves into the different types of automation systems, the pivotal role of robotics, specific applications in manufacturing and the automotive industry, and the interplay between automation and information technology. It also addresses the challenges faced in implementing these systems and proposes potential solutions.
Key Takeaways
- Understanding the fundamental concepts and the historical evolution of automation helps in appreciating its impact on modern industries.
- Different types of automation systems like fixed, programmable, and flexible automation cater to varied industrial needs and applications.
- Robotics, including industrial, collaborative, and mobile robots, play a crucial role in enhancing automation processes.
- Specific sectors like manufacturing and automotive have uniquely integrated automation for improved productivity and efficiency.
- Challenges such as integration complexities and maintaining flexibility need strategic solutions to leverage automation effectively.
Defining Automation in Industrial Contexts
Core Concepts of Automation
Automation in industrial contexts refers to the use of control systems and information technologies to reduce the need for human work in the production of goods and services. Automation is essential in enhancing productivity and efficiency.
Evolution of Industrial Automation
The evolution of industrial automation has transitioned from mechanical systems to digital technology. This shift has been pivotal in increasing the speed and accuracy of production processes.
Impact on Modern Industries
Automation has a profound impact on modern industries, significantly altering workforce dynamics and operational efficiency. It enables industries to maintain competitiveness in a global market.
Types of Automation Systems
Fixed Automation
Fixed automation, also known as hard automation, involves the use of specific equipment to automate a sequence of operations that are highly standardized. This type of automation is characterized by high initial investment but offers high production rates and is best suited for mass production with low product variability. Examples include rotary kilns in cement manufacturing or automated assembly lines in the automotive industry.
Programmable Automation
Programmable automation allows for the reprogramming of equipment to accommodate different product configurations. This flexibility makes it ideal for batch production where product designs are not constant. Key industries that benefit from programmable automation include electronics manufacturing and automotive parts assembly, where production volumes are lower and product design changes are frequent.
Flexible Automation
Flexible automation represents the highest level of adaptability in automation systems. It integrates the ability to change over to different product styles quickly and with minimal intervention. This system is often driven by computer-controlled processes that can adjust operations dynamically based on real-time data. Industries leveraging flexible automation often see significant improvements in production efficiency and reduction in downtime.
Role of Robotics in Automation
Industrial Robots
Industrial robots have revolutionized production lines across various sectors, significantly enhancing efficiency and precision. These robots are programmed for tasks such as welding, painting, and assembling, which are repetitive and potentially hazardous for human workers. The adoption of industrial robots not only improves productivity but also reduces the risk of injury in factory settings.
Collaborative Robots
Collaborative robots, or cobots, are designed to work alongside human workers, adding a layer of flexibility and safety to the workplace. They are equipped with sensors and software that allow them to detect and adapt to human presence, making them ideal for tasks that require human-robot interaction. Cobots are increasingly used in industries for tasks that are too intricate for traditional robots.
Mobile Robotics
Mobile robotics technology is advancing rapidly, bringing new capabilities to automation. These robots move through environments using various sensors and mapping technologies. They are particularly useful in warehousing and distribution, where they can navigate large spaces efficiently to transport goods. The integration of mobile robotics in these areas leads to significant improvements in logistics and handling.
Automation in Manufacturing
CNC Machines
Computer Numerical Control (CNC) machines represent a significant advancement in manufacturing automation. These machines use computerized controls to operate and manipulate machine tools, which can perform complex cuts and shapes with high precision. The use of CNC machines greatly enhances production speed and consistency while reducing human error.
Assembly Line Automation
Assembly line automation has revolutionized the way products are manufactured. By using automated systems, manufacturers can ensure a more efficient and consistent production process. Key benefits include increased production rates, better product quality, and reduced labor costs. Automation in assembly lines often involves the integration of various technologies such as robotics, sensors, and conveyor systems.
Quality Control Systems
Quality control systems in manufacturing automation use advanced technologies to inspect and ensure product quality. These systems often employ sensors, cameras, and other measurement devices to detect defects and ensure products meet quality standards. The implementation of these systems helps in maintaining high-quality production with minimal human intervention, ensuring reliability and safety in the manufacturing process.
Automation in the Automotive Industry
Robotic Assembly
In the automotive industry, robotic assembly lines have revolutionized the production process by enhancing speed, precision, and consistency. Robots are now integral to assembling parts such as engines, chassis, and even intricate components like wiring harnesses. The use of robotics has not only improved production efficiency but also reduced human error and workplace injuries.
Painting and Welding Automation
Automated painting and welding systems have significantly improved both the quality and speed of these processes. Precise control over these operations allows for uniform application and minimizes material wastage. Innovations in this area continue to evolve, pushing the boundaries of what automated systems can achieve in terms of both performance and environmental sustainability.
Supply Chain Automation
The integration of automation within the automotive supply chain has streamlined operations from procurement to delivery. Automated systems manage inventory, track parts, and ensure timely delivery, which is crucial for maintaining the pace of production without delays. This level of automation supports a lean manufacturing approach, optimizing the entire supply chain and reducing overhead costs.
Information Technology and Automation
Data Management Systems
In the realm of industrial automation, Data Management Systems (DMS) are crucial for efficiently handling large volumes of data generated by automated processes. These systems facilitate the storage, retrieval, and analysis of data, ensuring that information is accessible and usable for decision-making.
- Storage Solutions: Centralized databases, cloud storage
- Data Processing: Real-time processing capabilities
- Security Measures: Encryption, access controls
AI and Machine Learning
AI and Machine Learning technologies are transforming automation by enabling systems to learn from data, improve over time, and make autonomous decisions. This integration significantly enhances efficiency and adaptability in automated processes.
- Predictive Maintenance: Reducing downtime by predicting equipment failures
- Quality Control: Enhancing product quality through advanced analytics
- Adaptive Manufacturing: Adjusting operations based on real-time data
Network and Infrastructure Management
Effective management of network and infrastructure is vital for supporting the complex systems involved in industrial automation. Ensuring robust connectivity and security is paramount for the seamless operation of automated systems.
- Connectivity Solutions: High-speed networks, wireless communication
- Security Protocols: Firewalls, intrusion detection systems
- System Monitoring: Continuous monitoring of network health and performance
Challenges and Solutions in Industrial Automation
Integration Complexities
Integrating new automation technologies into existing systems often presents significant challenges. Key issues include compatibility with legacy systems, data synchronization, and workflow disruptions. Effective solutions involve careful planning, modular integration strategies, and possibly the use of middleware.
Maintaining Flexibility
To remain competitive, industries must maintain a high degree of flexibility in their automation systems to adapt to new processes and product changes. This requires scalable and modular automation solutions that can be easily updated or reconfigured.
Ensuring Reliability and Safety
Automation systems must be reliable and safe to protect both the production process and human workers. Strategies to enhance reliability include regular maintenance schedules, rigorous testing of new systems, and redundancy in critical components. Safety can be further ensured through strict adherence to industry standards and continuous training for staff.
Conclusion
In conclusion, the diverse types of automation in industry, ranging from robotic process automation to AI-driven predictive maintenance, are revolutionizing how businesses operate. Each type of automation offers unique benefits, enhancing efficiency, reducing costs, and improving product quality. As industries continue to evolve, the integration of these technologies will become increasingly crucial. Companies that effectively implement and adapt to these automation technologies will likely lead in productivity and innovation, setting new standards in their respective fields.
Frequently Asked Questions
What is industrial automation?
Industrial automation refers to the use of control systems, such as computers or robots, and information technologies for handling different processes and machineries in an industry to replace a human being. It is the second step beyond mechanization in the scope of industrialization.
How has automation evolved over the years?
Automation has evolved from mechanical systems and analog controls to digital computer-based technology, significantly increasing efficiency, productivity, and reliability across various industries.
What are the main types of automation systems?
The main types of automation systems include fixed automation, programmable automation, and flexible automation, each serving different production needs and scales.
What role do robots play in industrial automation?
Robots in industrial automation streamline operations, enhance precision and efficiency, and can be found in roles ranging from assembly lines to material handling and inspection tasks.
How does automation impact the automotive industry?
Automation in the automotive industry includes robotic assembly, painting, welding, and supply chain management, leading to higher production rates and increased safety and quality.
What are the challenges associated with industrial automation?
Challenges in industrial automation include integration complexities, maintaining operational flexibility, and ensuring reliability and safety of automated systems.