Boosting Efficiency in Semiconductor Production: Techniques and Tools
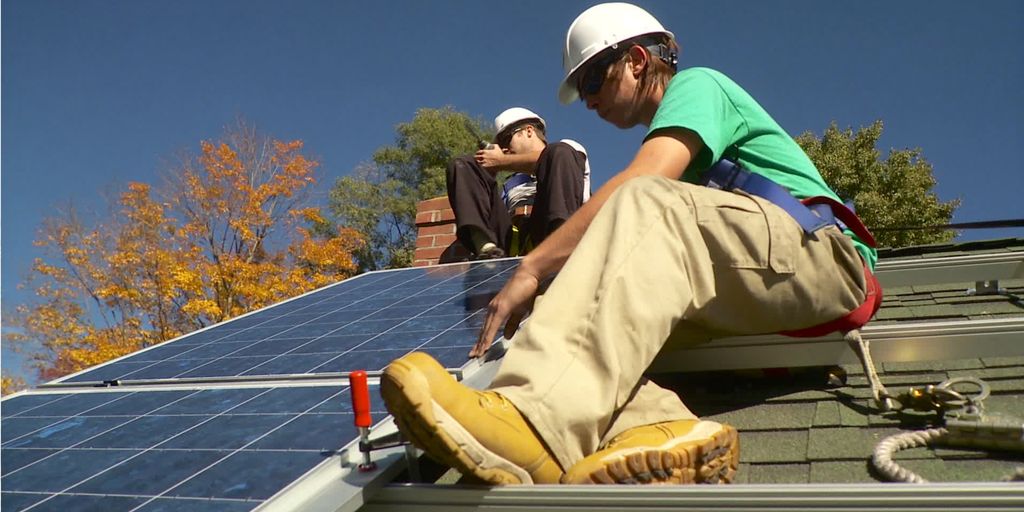
In the dynamic field of semiconductor production, efficiency is paramount. This article explores various strategies and technologies aimed at enhancing the productivity and output of semiconductor manufacturing. From the integration of cutting-edge technologies to the implementation of lean manufacturing principles, we delve into how these approaches can optimize operations and boost overall efficiency.
Key Takeaways
- Modern technologies and lean principles significantly enhance manufacturing optimization.
- AI, IoT, and big data analytics are pivotal in improving process control and efficiency.
- Energy efficiency and resource optimization are crucial in sustainable semiconductor fabrication.
- Maintenance and defect management are key to improving equipment efficiency and yield rates.
- Case studies and success stories provide actionable insights and validate the effectiveness of these strategies.
Strategies for Semiconductor Manufacturing Optimization
Integrating AI and Digital Transformation
The integration of AI and digital transformation is pivotal in enhancing the efficiency and output of semiconductor manufacturing. AI-driven analytics and automation can significantly reduce downtime and improve yield.
Applying Lean Manufacturing Principles
Lean manufacturing principles focus on minimizing waste and maximizing productivity. Key strategies include:
- Streamlining production processes
- Reducing inventory levels
- Improving worker productivity
Utilizing Process Improvement Techniques
Effective process improvement techniques are crucial for consistent quality and yield enhancement. Techniques such as Statistical Process Control (SPC), Design of Experiments (DOE), and Failure Mode and Effects Analysis (FMEA) are commonly employed to achieve these goals.
Emerging Technologies and Best Practices
Adoption of Advanced Materials
The semiconductor industry is increasingly turning to advanced materials such as gallium carbide to enhance the performance and efficiency of devices. These materials are crucial for developing smaller, more powerful electronic components that can withstand higher voltages and temperatures.
Incorporating IoT for Real-Time Monitoring
IoT technologies are revolutionizing real-time monitoring in semiconductor manufacturing. By integrating sensors and connected devices, manufacturers can track production processes more closely, leading to significant improvements in defect detection and yield optimization.
Leveraging Big Data and Analytics
The use of big data and analytics is becoming indispensable in semiconductor production. Cloud-based solutions facilitate the aggregation and analysis of vast amounts of data, enabling better decision-making and more effective defect management. This strategic approach helps in maintaining high standards of precision and efficiency across global operations.
The Importance of Energy Efficiency in Semiconductor Fabrication
Implementing Energy-Saving Technologies
In the dynamic landscape of semiconductor manufacturing, optimising energy usage is imperative for sustainability and profitability. A report by McKinsey highlights that while device power consumption has decreased, energy used during chip production has not seen similar improvements. Implementing energy-saving technologies can significantly reduce operating expenses, which can account for 5 to 30 percent of fab operating costs.
Optimizing Resource Utilization
Efficient resource utilization is crucial in reducing energy consumption. The EU’s Energy Efficiency Directive aims to cut energy use by 20% by 2020, emphasizing the importance of strategic resource management. Companies are encouraged to adopt innovative power solutions and prioritize investments that enhance energy efficiency.
Adapting to Market Demands
As demand for silicon is expected to continue rising, maximizing production capacity while conserving energy is essential. During peak times, energy conservation may not be prioritized, but it becomes critical when demand decreases. Establishing a robust energy management program, starting with monitoring and measuring energy use, is vital for adapting to fluctuating market demands and ensuring long-term sustainability.
A Comprehensive Guide to Boosting Gross Die Yield on Wafers
Enhancing Defect Management
Effective defect management is crucial for boosting gross die yield. By identifying and addressing defects early in the production process, manufacturers can significantly reduce scrap rates and improve yield. Key strategies include:
- Implementing advanced imaging and detection technologies.
- Regularly updating defect databases to reflect new findings.
- Training staff on best practices for defect identification and resolution.
Applying Statistical Process Control
Statistical Process Control (SPC) is a methodical approach that uses statistical methods to monitor and control a process. This helps ensure the process operates at its full potential:
- Set clear control limits.
- Use real-time data to make adjustments.
- Regularly review process performance and implement necessary changes.
Integrating Cloud-Based Solutions
Cloud-based solutions offer scalable and flexible options for data management and analysis, which are essential for optimizing wafer production. Benefits include:
- Enhanced data accessibility and sharing across departments.
- Improved decision-making through real-time analytics.
- Reduced IT overhead and increased operational efficiency.
Need to Boost Semiconductor Fab Efficiency? Look to Maintenance
Improving Equipment Recovery
Proactive management of equipment recovery is crucial for reducing downtime and enhancing operational efficiency. By focusing on preventive measures and quick responses to equipment issues, fabs can maintain continuous production without significant interruptions.
Planning Effective Maintenance
Effective maintenance planning involves scheduling activities during non-peak production times to minimize disruption. This strategic approach not only ensures equipment reliability but also optimizes resource allocation, supporting overall fab efficiency.
Managing Parts Efficiently
Efficient parts management is essential for maintaining a steady flow of production. By organizing and tracking parts inventory accurately, fabs can avoid delays caused by missing or faulty components, thus sustaining an uninterrupted production line.
Process Improvement Techniques
Statistical Process Control (SPC)
Statistical Process Control (SPC) is a method used to monitor and control process variations in semiconductor manufacturing. By using SPC, manufacturers can ensure product quality and consistency, which are critical in the high-stakes environment of semiconductor production. This technique helps in identifying and addressing factors that limit yield, making it a cornerstone of process improvement.
Design of Experiments (DOE)
Design of Experiments (DOE) is utilized to systematically optimize process parameters. This approach allows for a structured testing of multiple variables to determine their effect on the overall process. By implementing DOE, manufacturers can achieve more efficient and predictable production outcomes.
Failure Mode and Effects Analysis (FMEA)
Failure Mode and Effects Analysis (FMEA) is a proactive tool used to anticipate and prevent potential failures before they occur. This technique involves reviewing components, assemblies, and subsystems to identify possible failure modes, their causes and effects, and mitigating them effectively.
Case Study: Successful Semiconductor Manufacturing Optimization
Analyzing Success Factors
In this case study, the semiconductor manufacturing company achieved significant improvements by integrating AI and digital transformation. Key success factors included strategic technology adoption and continuous process evaluation.
Learning from Best Practices
The company’s approach to adopting lean manufacturing principles and process improvement techniques provides valuable insights. These practices not only reduced costs but also improved yield rates, showcasing a model for industry peers.
Implementing Proven Strategies
The implementation of proven strategies such as AI integration and digital transformation led to measurable improvements:
Metric | Improvement |
---|---|
Yield Rates | 20% |
Production Costs | -15% |
Operational Efficiency | 25% |
These results underscore the effectiveness of targeted optimizations in semiconductor manufacturing.
Conclusion
In conclusion, a combination of modern technologies, lean principles, and proven process improvement techniques can significantly enhance semiconductor manufacturing optimization. By leveraging these strategies, manufacturing managers can address the unique challenges of the semiconductor industry, improve production efficiency, and enhance product quality. Embracing practices such as precise defect management, statistical process control, and the integration of AI and machine learning, along with cloud-based solutions for data analysis, is essential for boosting efficiency and achieving superior outcomes in semiconductor production.
Frequently Asked Questions
What are the key strategies for optimizing semiconductor manufacturing?
Key strategies include integrating AI and digital transformation, applying lean manufacturing principles, and utilizing proven process improvement techniques like SPC, DOE, and FMEA.
How can emerging technologies boost semiconductor production efficiency?
Emerging technologies such as the adoption of advanced materials, IoT for real-time monitoring, and big data analytics can significantly enhance production efficiency and product quality.
What role does energy efficiency play in semiconductor fabrication?
Energy efficiency is crucial for reducing operational costs and supporting sustainability. Implementing energy-saving technologies and optimizing resource utilization are vital for energy-efficient practices.
How can maintenance improve semiconductor fab efficiency?
Effective maintenance strategies like improving equipment recovery, planning effective maintenance schedules, and managing parts efficiently can increase equipment availability and operational efficiencies.
What are the benefits of boosting gross die yield in semiconductors?
Boosting gross die yield improves product quality and operational efficiency, reduces waste, and enhances profitability by minimizing defects and optimizing production processes.
What can be learned from successful semiconductor manufacturing optimizations?
Successful optimizations demonstrate the importance of embracing modern technologies and process improvements, which can lead to significant improvements in yield rates, production costs, and overall operational efficiency.