Charting a Path for Success: Best Practices in Semiconductor Training Programs
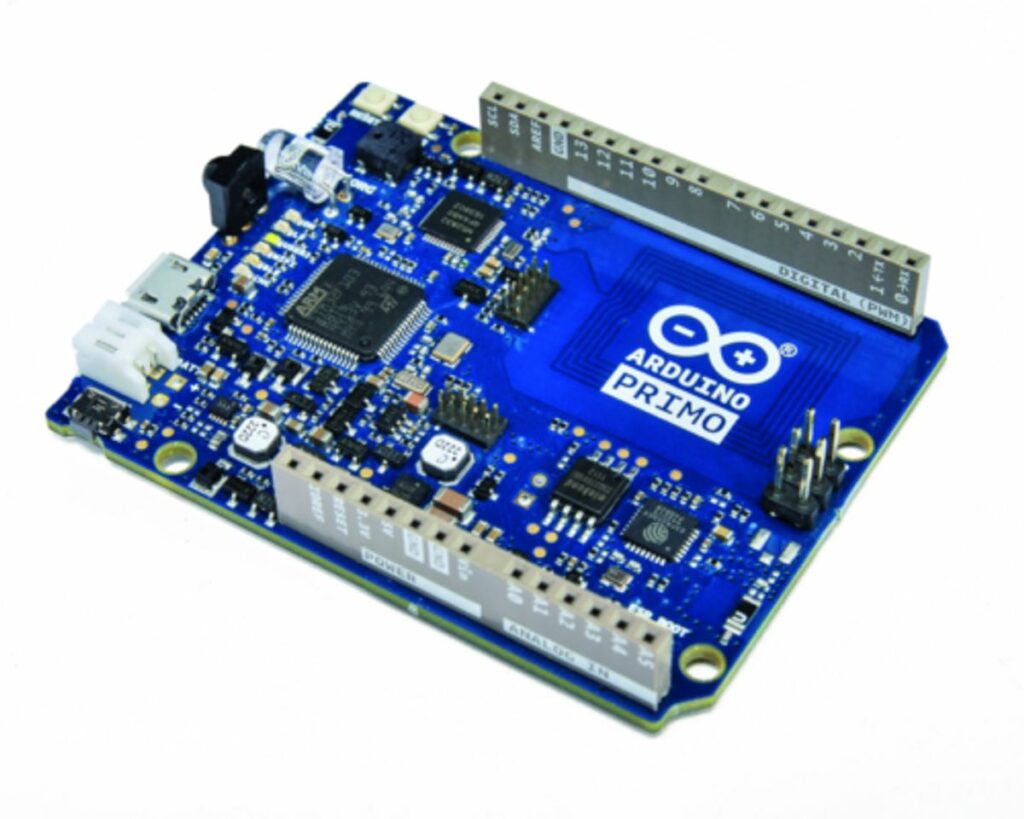
The semiconductor industry stands at the forefront of technological innovation, driving advancements that shape our modern world. As this field evolves at an unprecedented pace, the training and development of semiconductor professionals become increasingly critical. This article delves into the best practices for semiconductor training programs, highlighting strategies to foster innovation and expertise, optimize manufacturing processes, manage costs efficiently, ensure quality assurance, and prepare for future technological challenges.
Key Takeaways
- Revamping engineering education and integrating AI expertise are crucial for addressing future challenges in semiconductor fabrication and embracing the EDA 4.0 revolution.
- Advanced characterization management, effective wafer testing protocols, and leveraging big data are key to optimizing semiconductor manufacturing processes.
- Cost management strategies, such as understanding software change costs and implementing advanced automated test equipment, are vital for maintaining a balance between cost and innovation.
- Adopting best practices in metrology, defect data management, and adhering to strict quality standards, including those for aerospace defense, are essential for advancing quality assurance in semiconductor production.
- Preparing for future semiconductor technologies involves understanding the impact of high-NA lithography, tackling heat dissipation challenges, and leveraging multi-beam writers in EUV mask development.
Fostering Innovation and Expertise in the Semiconductor Industry
Rethinking Engineering Education for Future Challenges
The semiconductor industry is at a pivotal point where rethinking engineering education is not just beneficial, but necessary. With rapid technological advancements, educators must adapt curricula to prepare students for the complexities of modern semiconductor design and manufacturing. This involves a shift towards interdisciplinary learning and hands-on experience with cutting-edge tools and methodologies.
Key industry figures such as Art Scott and Liz Allan have emphasized the importance of evolving educational approaches to keep pace with industry demands. The integration of systems thinking, as highlighted in graduate programs, is crucial for developing engineers who can understand and optimize the intricate systems within semiconductor technology.
To illustrate the shift in educational focus, consider the following points:
- Emphasis on practical, industry-relevant skills
- Incorporation of AI and machine learning into the curriculum
- Stronger partnerships between academia and industry
- Continuous learning opportunities to keep skills current
By addressing these areas, educational institutions can create a robust pipeline of talent that is equipped to tackle future challenges in the semiconductor industry.
Integrating AI with Engineering Expertise in Fabrication
The integration of Artificial Intelligence (AI) with engineering expertise is revolutionizing the semiconductor fabrication process. AI’s ability to analyze and interpret complex data is becoming indispensable in addressing the intricate challenges of semiconductor manufacturing. A fabrication plant, or fab, is a hub of data generation, often producing petabytes of information that can be leveraged to optimize production efficiency and quality.
To effectively utilize AI in the fab, several key steps must be followed:
- Establishing a robust data infrastructure to support AI initiatives.
- Implementing AI-driven analytics to identify patterns and anomalies in manufacturing data.
- Training AI models with historical data to predict and prevent defects.
- Integrating AI tools with existing engineering workflows to enhance decision-making.
By embracing AI, fabs can achieve a new level of precision and control, leading to improved yield rates and reduced time-to-market for semiconductor devices.
Embracing the EDA 4.0 and AI-Driven Technological Shift
The semiconductor industry is on the brink of a transformative era with the advent of EDA 4.0 and AI-driven technologies. These advancements are not just reshaping the design and manufacturing processes but are also setting new benchmarks for efficiency and innovation.
AI’s role in semiconductor manufacturing is becoming increasingly pivotal. By continuously learning from production data, AI systems can predict and prevent defects, optimize workflows, and enhance the overall quality of the semiconductor products. This shift towards AI integration is a critical step in maintaining a competitive edge in the fast-paced semiconductor market.
The following table highlights key areas where AI is making an impact in semiconductor manufacturing:
AI Application | Expected Outcome |
---|---|
Predictive Maintenance | Reduced downtime |
Defect Detection | Improved yield |
Process Optimization | Enhanced efficiency |
Quality Control | Consistent standards |
As we move forward, it is essential for professionals in the field to stay abreast of these changes and adapt their skills accordingly. The integration of AI into EDA tools is not just a trend but a necessity to meet the growing complexity of semiconductor designs and the demands of next-generation technologies.
Optimizing Semiconductor Manufacturing Processes
Advanced Characterization Management for Rapid Qualification
In the fast-paced world of semiconductor manufacturing, advanced characterization management is pivotal for rapid qualification of products. This process ensures that semiconductor devices meet the stringent standards required for performance and reliability before mass production. By leveraging big data analytics and automated testing systems, companies can significantly reduce the time-to-market for new semiconductor devices.
Key components of an effective characterization management system include Automated Reports, Design of Experiments (DOE), and Real-time Tracking of Yield Issues. These elements work in tandem to identify and rectify yield issues, thereby enhancing the overall production process. For instance, the use of Parametric Part Average Test (PAT) and Process Capability Index (CPK) metrics are essential in maintaining high-quality standards.
The following table outlines the core aspects of characterization management and their impact on semiconductor qualification:
Aspect | Description | Impact |
---|---|---|
Automated Reports | Streamlines data collection and analysis | Reduces qualification time |
DOE | Optimizes manufacturing parameters | Enhances device performance |
Real-time Tracking | Monitors yield issues promptly | Improves production yield |
As the semiconductor industry continues to evolve, the role of characterization management in maintaining a competitive edge cannot be overstated. It is a critical step in addressing the talent challenge in semiconductors, ensuring that the industry’s demand for qualified candidates is met with the highest standards of expertise.
Implementing Effective Wafer Testing and Analysis Protocols
In the realm of semiconductor manufacturing, wafer testing is a pivotal step in ensuring the quality and performance of the final product. This process not only verifies adherence to specifications but also delves into the analysis of test results to pinpoint the root causes of defects or performance issues. By transforming data into actionable insights, wafer testing and analysis play a crucial role in the continuous improvement of manufacturing processes.
The types of test wafers, including monitor, dummy, defect, or short loop wafers, each serve a unique purpose in upholding the stringent standards of semiconductor testing. Utilizing wafer probers and thorough chip and die tests, these wafers are instrumental in delivering semiconductor devices that are both reliable and of superior quality.
Best practices in wafer testing are paramount for the semiconductor industry. The commitment to high-quality testing underpins the reliability and functionality of semiconductor devices, which are foundational to nearly all contemporary technologies. It is essential for professionals in the field, from engineers to quality control experts, to be well-versed in these practices to maintain the industry’s reputation for excellence.
Leveraging Big Data for Enhanced Semiconductor Testing
The semiconductor industry is increasingly turning to big data analytics to revolutionize testing processes. By harnessing the vast amounts of data generated during testing, companies can identify patterns and anomalies that were previously undetectable. This shift towards data-driven decision-making allows for more precise and efficient testing protocols.
Adaptive testing strategies, such as those highlighted in the Adaptive Test Ramps For Data Intelligence Era, are at the forefront of this transformation. Utilizing machine learning algorithms, these strategies dynamically adjust testing parameters in real-time, leading to significant improvements in device quality and yield.
The following table outlines key components of a big data analytics system in semiconductor testing:
Component | Function |
---|---|
Automated Testing System | Executes test sequences and collects data |
Data Archival | Stores historical test data for analysis |
Real-time Tracking | Monitors yield issues as they occur |
Root Cause Analysis | Identifies sources of yield losses |
Outlier Detection | Flags data points that deviate from expected patterns |
Embracing big data not only enhances testing but also paves the way for continuous improvement in semiconductor manufacturing. As the industry evolves, the integration of big data systems with existing testing protocols will become a standard, ensuring that semiconductor products meet the highest standards of quality and performance.
Strategies for Cost Management and Efficiency
Understanding the True Cost of Software Changes in the Industry
In the semiconductor industry, software changes are a constant, driven by the need to enhance features, fix bugs, and improve performance. However, the true cost of these changes often extends beyond the initial development effort. Industry experts like Peter Bennet have shed light on the multifaceted nature of these costs, emphasizing the importance of comprehensive evaluation.
When considering software updates, companies must account for the direct costs of development and testing, as well as the indirect costs associated with potential downtime, retraining staff, and the risk of introducing new defects. The balance between incremental change and the budget allocated for such updates can be precarious, as highlighted by the dilemma of predicting the impact of a firmware update.
To manage these costs effectively, a structured approach is necessary. Here is a suggested framework:
- Evaluate the necessity of the software change.
- Assess the potential risks and hidden costs.
- Plan for adequate testing and quality assurance.
- Budget for training and change management.
- Monitor the impact post-implementation to inform future changes.
Cutting Costs with Advanced Automated Test Equipment
The integration of advanced automated test equipment (ATE) in semiconductor manufacturing has proven to be a game-changer in cost management. By automating wafer tests and implementing in-fab ATE setups, companies like NI have seen a significant reduction in R&D project timelines and overall expenses. The initial ATE configuration combined various measurement tools with a custom probe card, all connected to a PXI instrumentation rack, streamlining the testing process.
The adoption of LabVIEW parametric test routines using PXI modular instruments has enabled fully automated, unattended wafer tests at multiple stages of production. This advancement not only enhances testing efficiency but also contributes to the effectiveness of the semiconductor research and development cycle. Below is a list of key benefits observed from the deployment of advanced ATE:
- Reduced R&D deliverable time
- Decreased operational costs
- Improved testing efficiency
- Enhanced testing effectiveness
Embracing these technologies is not just about reducing costs; it’s about optimizing the entire semiconductor manufacturing process for better outcomes and sustainability.
Balancing Cost and Innovation in Yield Management
In the competitive landscape of semiconductor manufacturing, balancing cost and innovation is crucial for sustainable yield management. A high yield means that a larger percentage of the manufactured ASICs meet the required functional and performance standards, thereby reducing waste and enhancing profitability.
Key factors influencing yield and quality include process optimization, defect management, and the integration of advanced technologies. Yield management strategies often revolve around the Six Sigma methodology and Statistical Process Control (SPC) to identify root causes of yield losses and implement corrective actions.
The table below outlines the components of a comprehensive Yield Management System (YMS) solution:
Component | Functionality |
---|---|
Automated Yield Monitoring | Real-time tracking and analysis of yield data |
Reporting & Analysis | In-depth performance reporting and trend analysis |
Data Archiving & Purge Module | Efficient data storage management and retrieval |
Yield Calculation Flexibility | Customizable yield calculation methods for various needs |
By leveraging tools like yieldWerx, manufacturers can adapt to the unique demands of semiconductor production, ensuring precision, efficiency, and innovation. It’s about finding the right mix of cost-saving measures and investment in yield enhancement software to maintain a competitive edge.
Advancing Quality Assurance in Semiconductor Production
Metrology and Defect Data Management Best Practices
In the realm of semiconductor production, metrology and defect data management are critical for ensuring high-quality outputs. Precision measurement and data collection form the foundation of effective defect management. Utilizing advanced software systems, such as yieldWerxTM, can automate the process of anomaly detection and trend analysis, leading to more efficient and accurate decision-making.
The integration of various software tools is essential for a comprehensive approach to defect management. Below is a list of key software components that play a pivotal role in this process:
- Inspect Image Management
- Semiconductor Optical Memory Mapping
- Equipment Efficiency Monitoring Software
- Wafer Prober Control Module
- Semiconductor Failure Analysis Software
- Testing and Yield Analysis Software
Each component addresses a specific aspect of the semiconductor manufacturing process, from inspection to analysis, contributing to a robust strategy for managing metrology and defects. By leveraging big data analytics and real-time tracking, manufacturers can pinpoint the root causes of yield losses and rectify issues promptly, aligning with Six Sigma and SPC (Statistical Process Control) methodologies for continuous improvement.
Achieving Zero Defects with Yield Enhancement Software
In the pursuit of zero defects in semiconductor production, Yield Management Systems (YMS) have become indispensable. These systems empower manufacturers to handle high volumes of production analysis with a leaner engineering workforce. By analyzing yield data, YMS identifies potential yield detractors and facilitates rapid problem-solving.
Yield enhancement software, such as yieldWerx, offers a comprehensive platform that integrates with existing workflows. It provides actionable insights that drive continuous improvement in the manufacturing process. The software’s capabilities extend to advanced wafer testing and analysis, ensuring that each semiconductor meets the highest quality standards before it leaves the production line.
The table below outlines the core components of a typical YMS solution:
Component | Function |
---|---|
Automated Yield Monitoring | Real-time tracking and alerts |
Reporting & Analysis | In-depth performance data |
Data Archiving & Purge | Efficient data management |
Lot Genealogy | Traceability of production history |
By leveraging these tools, companies can not only enhance their yield but also align with rigorous quality assurance frameworks, such as those required in the aerospace defense industry. The goal is clear: to achieve a state of zero defects where every chip produced is synonymous with reliability and excellence.
Adhering to Aerospace Defense Semiconductor Quality Standards
The aerospace defense sector demands the utmost in quality and reliability for semiconductor components. Ensuring adherence to SAE Aerospace Standards is critical for maintaining the safety and reliability of all aspects of aviation. These standards encompass a wide range of requirements, from aircraft design and flight controls to aviation fuel and communications.
To meet these stringent standards, semiconductor manufacturers must implement robust quality assurance solutions. This includes the use of Yield Management Software specifically designed for the unique needs of the aerospace defense industry. Such software assists in optimizing yield in semiconductor manufacturing, which is vital for both quality and cost-efficiency.
The table below outlines key aspects of quality assurance in the semiconductor industry, highlighting the importance of comprehensive testing and data management:
Quality Assurance Aspect | Description |
---|---|
Yield Enhancement Software | Maximizes efficiency and quality in production. |
Big Data Analytics | Enables real-time tracking of yield issues and root cause analysis. |
Automated Testing Systems | Ensures each semiconductor meets the highest standards of quality. |
Data Archival and Genealogy Analytics | Maintains a detailed history for traceability and compliance. |
Preparing for the Future of Semiconductor Technology
High-NA Lithography and the Evolution of Semiconductor Design
The advent of High-NA (Numerical Aperture) Extreme Ultraviolet (EUV) lithography marks a pivotal moment in semiconductor design, enabling the creation of smaller, more complex chips. This technology is essential for advancing to the next generation of semiconductor nodes, where traditional lithography techniques reach their limits. High-NA EUV lithography achieves this by improving resolution and overlay accuracy, which are critical for patterning the minute features of advanced semiconductor devices.
One of the key benefits of High-NA EUV lithography is its compatibility with existing semiconductor manufacturing ecosystems. Importantly, it also minimized the new technology’s impact on the semiconductor ecosystem by allowing chipmakers to continue using traditionally sized reticles. This compatibility ensures a smoother transition and integration into current production lines, mitigating potential disruptions.
As we delve into the specifics of High-NA EUV lithography, here are five crucial aspects to consider:
- Enhanced resolution for advanced patterning
- Improved overlay accuracy for intricate designs
- Compatibility with existing reticle sizes
- Potential for increased throughput with future developments
- Necessity for new metrology and inspection techniques to manage complexity
Navigating the Challenges of Heat Dissipation in Modern Chips
As semiconductor devices continue to shrink and pack more power into tighter spaces, heat dissipation has emerged as a critical challenge. The advent of 3D-ICs and 2.5D interposer technologies has exacerbated this issue, with thermal gradients causing warpage and potentially trapping heat, leading to a ‘snowball effect’.
Transient thermal gradients present a particularly vexing problem. These gradients can shift unpredictably, influenced by workload variations and can cause significant issues in high-density chips. At advanced nodes, what were once minor annoyances now demand serious attention and sophisticated management strategies.
To combat these challenges, engineers are turning to a combination of innovative cooling solutions and simulation techniques. For instance, thermal-mechanical co-simulation allows for the analysis of heat distribution and mechanical stress in real-time, providing insights into potential hotspots and structural integrity under varying operational conditions. Additionally, best practices for applying thermal interface materials are crucial for optimizing heat transfer and minimizing thermal resistance.
The table below outlines some of the key strategies for managing heat in modern semiconductor devices:
Strategy | Description |
---|---|
Enhanced Heatsinks | Utilizing advanced materials and designs to improve heat dissipation. |
Thermal Interface Materials | Applying materials with high thermal conductivity to facilitate heat transfer. |
Simulation Tools | Employing software for predictive modeling of thermal behavior. |
Dynamic Workload Management | Adjusting operations to manage heat generation and distribution. |
In conclusion, addressing the heat dissipation challenge is not only about keeping devices cool but also about ensuring the longevity and reliability of semiconductor components. As the industry moves towards even smaller geometries and more complex packaging, the importance of effective thermal management will only continue to grow.
The Role of Multi-Beam Writers in EUV Mask Development
The introduction of the multi-beam mask writer MBM-3000 marks a significant advancement in EUV mask production. Launched in 2023, this cutting-edge technology is designed to meet the intricate demands of next-generation EUV lithography. With its 12-nm beamlets, the MBM-3000 offers unprecedented precision, paving the way for more complex and miniaturized semiconductor designs.
The impact of multi-beam writers on EUV mask development is profound. These systems enable a level of detail and accuracy that was previously unattainable, ensuring that semiconductor manufacturers can keep pace with the rapid evolution of chip design. The following list outlines the key benefits of utilizing multi-beam writers in the production process:
- Enhanced resolution and pattern fidelity
- Increased throughput due to parallel processing
- Reduced mask production time
- Improved yield through precise defect control
As the semiconductor industry continues to push the boundaries of what’s possible, the role of technologies like the MBM-3000 becomes increasingly critical. It not only represents a leap forward in manufacturing capabilities but also underscores the importance of continuous innovation in the tools used for semiconductor fabrication.
Conclusion
In the ever-evolving landscape of semiconductor manufacturing, the importance of comprehensive training programs cannot be overstated. As we’ve explored throughout this article, from the insights of industry experts like Mark Camenzind and Allen Rasafar to the case studies highlighting the transformative power of advanced technologies, it’s clear that success hinges on a well-informed and skilled workforce. By embracing best practices such as integrating AI and engineering expertise, managing yield with cutting-edge lithography, and leveraging data analytics for precision and efficiency, companies can chart a path for success. The semiconductor industry stands at the forefront of innovation, and through continuous learning and adaptation, it will continue to thrive in an increasingly competitive global market. Let us commit to excellence in training, ensuring that the workforce is equipped to meet the challenges of today and the opportunities of tomorrow.
Frequently Asked Questions
How is AI integration transforming semiconductor fabrication?
AI integration is enhancing semiconductor fabrication by improving process control, increasing automation, and enabling predictive maintenance. This leads to higher yields, reduced defects, and more efficient use of resources.
What is EDA 4.0 and how does it affect the semiconductor industry?
EDA 4.0 refers to the latest evolution in electronic design automation, incorporating AI and machine learning to automate complex design tasks, optimize chip layouts, and reduce time-to-market for semiconductor products.
What are the benefits of advanced characterization management in semiconductor manufacturing?
Advanced characterization management allows for faster qualification of semiconductor devices by providing detailed analysis of materials and structures, leading to improved reliability and performance of the final product.
How can semiconductor companies manage costs effectively without compromising on innovation?
Companies can manage costs by investing in automated test equipment, optimizing yield management strategies, and implementing software changes carefully to balance the need for innovation with the financial realities of the industry.
What quality assurance practices are critical for aerospace defense semiconductor production?
For aerospace defense semiconductor production, strict quality assurance practices such as adherence to industry standards, zero-defect initiatives, and rigorous metrology and defect data management are critical to ensure reliability and safety.
What challenges does high-NA lithography present, and how are they being addressed?
High-NA lithography presents challenges such as complex mask design and increased heat dissipation. These are being addressed with advanced mask development techniques, like multi-beam writers, and innovative cooling solutions for modern chips.