Choosing the Right Silicon Wafer Supplier: Factors to Consider
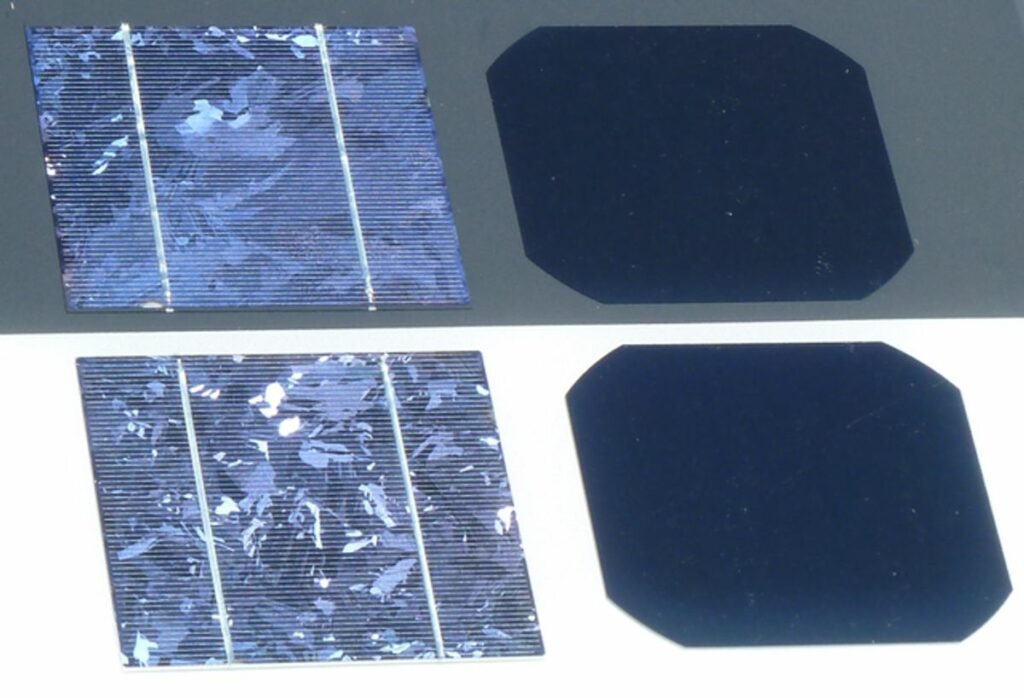
Selecting the right silicon wafer supplier is a critical decision that impacts the quality, performance, and cost-effectiveness of semiconductor manufacturing. With a plethora of materials, fabrication techniques, and suppliers available in the market, it’s essential to consider a range of factors to ensure the best outcomes for your specific application. This article will guide you through the key considerations when choosing a silicon wafer supplier, from understanding semiconductor materials to optimizing wafer yield and fostering strong ecosystem partnerships.
Key Takeaways
- The choice of semiconductor material, such as GaN, GaAs, or SiGe, significantly affects chip performance and reliability.
- Selecting a wafer fabricator involves analyzing trade-offs in price, performance, size, and power to optimize the solution for your ASIC.
- Strong ecosystem partnerships, leveraging decades of design experience, and robust supply chain relationships are vital for ensuring quality.
- When choosing package, assembly, and test suppliers, balance cost, quality, and turnaround time while considering the impact on product integrity.
- Incorporating EDA tools and effective product qualification strategies, like utilizing YieldWerx, is crucial for process optimization and increased profitability.
Understanding Semiconductor Materials and Their Impact
Comparing GaN, GaAs, and SiGe
When selecting a semiconductor material, it’s crucial to understand the unique properties and applications of GaN, GaAs, and SiGe. GaN, GaAs, and SiGe offer unique properties for various semiconductor applications. Each material brings its own set of advantages to the table, influencing the performance and suitability for specific devices.
SiGe is known for combining the low-cost and mature manufacturing processes of silicon with the high carrier mobility of germanium. This makes it particularly suitable for high-speed integrated circuits, especially in RF and mixed-signal applications. However, SiGe may not reach the maximum operating frequencies of GaAs or GaN and can require more complex manufacturing processes.
GaAs stands out with its high electron mobility and direct bandgap, which is ideal for efficient light emission and absorption. This makes GaAs wafers well-suited for high-speed applications like microwave devices and high-speed transistors. On the other hand, GaN is recognized for its high electron mobility and wide bandgap, which are beneficial for high-power applications.
Material | High Electron Mobility | Direct Bandgap | Suitable Applications |
---|---|---|---|
SiGe | Yes | No | High-speed ICs, RF |
GaAs | Yes | Yes | Microwave devices |
GaN | Yes | Yes | High-power devices |
Material Reliability and Chip Performance
The reliability of semiconductor chips is intrinsically linked to the materials from which they are made. Material choice not only influences the performance but also the longevity and stability of the final product. For instance, materials like GaN, GaAs, and SiGe each bring distinct properties that can affect the chip’s ability to withstand temperature variations, power densities, and operational frequencies.
When selecting a semiconductor material, it’s crucial to consider the specific application and its requirements. Here’s a brief comparison of the materials:
- GaN: Offers high electron mobility, which is ideal for high-frequency, high-power applications.
- GaAs: Provides superior electron velocity, making it suitable for high-speed and low-noise applications.
- SiGe: Combines the manufacturability of silicon with the speed of germanium, useful for high-frequency analog applications.
Understanding the trade-offs between these materials is essential for optimizing chip performance. For example, GaN’s high power efficiency might be preferred for power amplifiers, while SiGe’s frequency capabilities could be more beneficial for certain analog circuits. Ultimately, the right material selection will ensure that the chip meets the desired performance criteria without compromising on reliability.
The Role of Material in Semiconductor Manufacturing
The selection of the semiconductor material is a pivotal decision in the manufacturing process, as it directly influences the performance and reliability of the final chip. Silicon wafers, recognized for their versatility and electrical properties, serve as the foundational substrate for a vast array of microelectronic devices. The material’s inherent characteristics dictate the chip’s capabilities and are a determining factor in its application suitability.
Material selection is not just about the electrical properties; it also impacts the manufacturing yield. Defects in the wafer can propagate through the subsequent manufacturing steps, leading to a lower yield of functional chips. Therefore, optimizing the choice of material is crucial for minimizing defects and enhancing the overall yield. The following table summarizes the key considerations when selecting a semiconductor material:
Factor | Consideration |
---|---|
Electrical Properties | Conduction efficiency, bandgap |
Mechanical Strength | Resistance to breakage during processing |
Thermal Conductivity | Heat dissipation capabilities |
Chemical Stability | Resistance to corrosion and other reactions |
In the context of semiconductor manufacturing, the role of the material extends beyond its physical and chemical properties. It is also about the scalability and cost-effectiveness of the production process. Manufacturers must balance these factors to ensure that the chosen material not only meets the technical requirements but is also viable for mass production.
Evaluating Semiconductor Wafer Fabricators
Factors Influencing Wafer Yield
The yield of a wafer is a critical metric in semiconductor manufacturing, reflecting the number of good dies that can be produced from a single wafer. Several key factors play a role in influencing this yield, each contributing to the overall efficiency and cost-effectiveness of production.
- Purity of silicon wafers: The foundational material for chip fabrication must be of high quality to ensure minimal defects.
- Precision in photolithography: Accurate patterning is essential for creating the intricate circuits of a chip.
- Doping and etching processes: These steps must be carefully controlled to achieve the desired electrical properties and circuit shapes.
- Equipment calibration: Properly maintained and calibrated equipment is necessary to maintain consistent manufacturing standards.
- Defect management strategies: Identifying and addressing defects early in the process can significantly improve yield.
- Complexity of chip design: More complex designs tend to have lower yields due to increased chances of errors.
Employing strategies such as statistical process control and leveraging tools like yieldWerx can help manufacturers monitor and optimize these factors. As a result, they can achieve better yield rates and enhance the profitability of semiconductor production.
Optimizing Gross Die Yield
Maximizing gross die yield is essential for semiconductor manufacturers aiming to achieve cost-effectiveness while upholding high-quality standards. This process involves a meticulous approach to monitoring and refining wafer fabrication processes, utilizing tools such as statistical process control and advanced cloud-based solutions.
High gross die yield is indicative of successful yield optimization, a critical factor for producing cost-effective and high-quality integrated circuits. It not only affects profitability but also informs strategic decisions in wafer yield and defect management, underscoring the need for precision in manufacturing.
To enhance gross die yield, manufacturers must focus on several key areas:
- Material Selection: The choice of materials can significantly affect the yield due to inherent material properties.
- Fabrication Techniques: Variations in processes like photolithography and etching can introduce defects.
- Equipment Calibration: Precision in equipment calibration is vital to minimize defects and improve yield.
Understanding the distinction between gross die yield and other yield metrics is crucial. Gross die yield specifically measures the ratio of usable chips to the total number produced on a wafer, reflecting the initial production effectiveness before further testing and assembly. This metric is a fundamental guide for yield and defect management strategies.
Navigating the Challenges of High Inventory Levels
The semiconductor industry is currently grappling with elevated inventory levels, which are contributing to a challenging sales environment. Suppliers are finding it necessary to offer discounts to secure orders, as a major wafer producer highlighted the difficulty of sales without price reductions. This situation underscores the importance of efficient inventory management to maintain profitability.
In response to the accumulation of inventory, some wafer factories are considering production cuts. The decision to adjust production is a delicate balance, as it must align with market demand projections, such as the 70 GW target set by the Silicon Industry of China Nonferrous Metals Industry Association for March. Effective strategies to manage high inventory levels include:
- Implementing robust inventory management systems
- Real-time visibility into stock levels and production schedules
- Continuous training programs for personnel
- Utilizing cloud-based solutions for data aggregation and analysis
These measures can help suppliers navigate the complexities of inventory management, ensuring that they can respond to market fluctuations and maintain operational efficiency.
The Importance of Ecosystem Partnerships
Leveraging Decades of ASIC Design Experience
The expertise of a semiconductor wafer supplier’s engineering team is a critical factor in the success of ASIC (Application-Specific Integrated Circuit) design and production. Our engineering team stands out with more average experience than any competitor, ensuring the highest quality in mixed-signal, RF, and high-voltage ASICs. This deep expertise translates into efficient custom IC design, aggressive NRE (Non-Recurring Engineering) quotes, and cost reductions.
Collaboration is key in ASIC development. A supplier that approaches each project with a collaborative attitude can significantly enhance the design process. Below is a list of areas where our team’s ASIC design expertise is particularly strong:
- High-Voltage
- Sensors and MEMs Interfacing
- Ultra-Low Power
- Precision Analog and Data Converters
- Wireless Communications
By choosing a supplier with a proven track record and a comprehensive understanding of ASIC design, customers can leverage decades of experience to achieve superior performance and efficiency in their semiconductor products.
Building Strong Supply Chain Relationships
In the semiconductor industry, strong supply chain relationships are crucial for ensuring a steady flow of materials and components. These relationships are particularly important for foundational semiconductor products, which may use nodes ranging from 45nm to smaller sizes. A robust supply chain can mitigate risks associated with fluctuating demand and supply disruptions.
To build and maintain these relationships, companies must focus on collaboration and communication. This involves sharing forecasts, production plans, and inventory levels to align expectations and capabilities. Regular meetings and joint problem-solving sessions can foster a sense of partnership and mutual investment in success. Additionally, integrating cloud-based solutions can enhance data sharing and decision-making across global operations.
Here are some key strategies for strengthening supply chain relationships:
- Establishing continuous training programs to keep personnel updated on technological advancements.
- Implementing cloud-based solutions for real-time data analysis and defect management.
- Engaging in joint strategic planning to address manufacturing challenges collaboratively.
- Utilizing tools like YieldWerx for semiconductor yield monitoring and optimization.
Ensuring Quality Through In-House Testing
In the competitive landscape of silicon wafer manufacturing, ensuring quality through in-house testing is a cornerstone for success. Suppliers that invest in comprehensive testing protocols not only meet but often exceed industry standards, setting a benchmark for reliability and performance. These standards are critical for maintaining the integrity of the semiconductor manufacturing process.
In-house testing encompasses a variety of procedures, each designed to identify and rectify potential issues before wafers reach customers. This proactive approach includes the use of Statistical Process Control (SPC) systems and real-time anomaly detection, which are essential for early intervention and defect reduction. By leveraging big data analytics and cloud-based solutions, suppliers can analyze vast datasets across production sites, fostering a culture of precision and innovation.
The table below outlines key aspects of in-house testing and their impact on quality assurance:
Testing Aspect | Impact on Quality Assurance |
---|---|
SPC System | Enhances early defect detection |
Real-time Alerts | Promotes immediate corrective action |
Data Analysis | Drives continuous improvement |
Cloud Integration | Enables cross-site data synergy |
Ultimately, the goal of in-house testing is to deliver wafers that not only comply with but advance the quality standards of the industry. Suppliers who demonstrate a commitment to rigorous testing are more likely to provide products that uphold the high expectations of semiconductor manufacturers and end-users alike.
Selecting Package, Assembly, and Test Suppliers
Criteria for Choosing the Right Supplier
Selecting the right package, assembly, and test supplier is a critical decision that can significantly affect the final product’s quality and cost-efficiency. The choice of supplier should align with your project’s specific needs, including performance requirements and budget constraints. It is essential to evaluate suppliers based on their expertise, quality assurance processes, and ability to deliver on time.
When considering a supplier, it’s important to assess their track record in the industry. Look for suppliers with a strong history of reliability and customer satisfaction. Additionally, the supplier’s capacity to handle your volume requirements and their flexibility in scaling production should be taken into account. A supplier’s responsiveness to unforeseen challenges and their problem-solving capabilities are also vital factors.
The wafer test is a crucial step in the semiconductor manufacturing process. It involves probing individual semiconductor devices on a wafer to identify defects and confirm functionality before further manufacturing. Ensuring that your supplier has robust testing protocols in place is paramount for maintaining high standards of quality.
Balancing Cost, Quality, and Turnaround Time
In the competitive landscape of semiconductor manufacturing, balancing cost, quality, and turnaround time is a critical challenge for suppliers. Cost considerations often drive the selection process, but compromising on quality can lead to increased defects and longer turnaround times due to rework. Conversely, prioritizing quality without regard to cost can render a product uncompetitive, while a focus on rapid turnaround might sacrifice both cost efficiency and quality.
To navigate this balance, suppliers must employ a strategic approach:
- Cost: Implementing cost-saving measures such as bulk purchasing, optimizing production processes, and adopting lean manufacturing principles.
- Quality: Ensuring adherence to industry standards, conducting rigorous in-house testing, and leveraging advanced SPC techniques.
- Turnaround Time: Streamlining supply chains, maintaining equipment calibration, and utilizing cloud-based solutions like yieldWerx for real-time process adjustments.
Ultimately, the goal is to achieve a synergy that maximizes yield and minimizes waste, without compromising the integrity of the final product. This requires a continuous improvement mindset and a willingness to invest in emerging technologies and best practices that drive efficiency and innovation.
The Impact of Testing on Final Product Integrity
The final stage of semiconductor production, testing, is pivotal in ensuring the integrity of the final product. Maintaining signal integrity is crucial in semiconductor testing, as it directly influences the performance and reliability of the chip. Test packages are meticulously engineered to minimize signal losses, reflections, and noise, which are essential for accurate testing outcomes.
Effective defect management plays a significant role in this phase. By employing various inspection techniques and categorizing defects, manufacturers can prioritize issues that significantly affect yield. This approach not only ensures the quality of each chip but also contributes to the overall yield optimization. Cloud-based solutions and big data analytics are increasingly being utilized to aggregate and analyze vast amounts of data, fostering a data-driven culture that prioritizes precision and efficiency.
The table below summarizes key aspects of testing that impact final product integrity:
Aspect | Description |
---|---|
Signal Integrity | Ensures accurate performance and reliability |
Defect Management | Prioritizes significant yield-affecting issues |
Data Analytics | Enables real-time tracking and yield issue rectification |
In conclusion, the role of testing in semiconductor manufacturing cannot be overstated. It is the safeguard that ensures that the chips meet the stringent requirements of the industry and that the final products perform as expected.
Incorporating EDA Tools and Product Qualification
The Role of EDA Tools in Wafer Production
Electronic Design Automation (EDA) tools are pivotal in the semiconductor manufacturing process, streamlining the journey from design to production. These tools assist engineers in creating complex integrated circuits (ICs) with higher precision and efficiency. EDA software encompasses a range of functionalities, from schematic capture and simulation to layout and verification, ultimately leading to the tapeout phase.
During tapeout, the finalized IC design is prepared for manufacturing. This critical step involves translating the design into a format suitable for photolithography, the process that etches the design onto the silicon wafer. EDA tools play a crucial role in ensuring that the design adheres to manufacturing constraints and is optimized for yield. The table below outlines some key EDA functionalities and their impact on wafer production:
EDA Functionality | Impact on Wafer Production |
---|---|
Schematic Capture | Facilitates accurate design representation |
Simulation | Predicts circuit behavior and performance |
Layout | Ensures design meets physical constraints |
Verification | Confirms design correctness before tapeout |
Post-tapeout, EDA tools continue to support the manufacturing process by providing data for yield analysis and enhancement. YieldWerx, for instance, enables manufacturers to fine-tune processes for multi-product wafers, incorporate retest operations, and implement redundancy schemes. By leveraging these tools, manufacturers can identify and rectify yield issues, leading to improved efficiency and profitability.
Strategies for Effective Product Qualification
Effective product qualification is a critical step in ensuring the reliability and performance of semiconductor devices. Maximizing gross die yield within semiconductor manufacturing necessitates a focused strategy on detailed process optimization and diligent equipment calibration. This involves a series of steps, including:
- Automated Testing System (ATS) implementation for consistent testing procedures.
- Utilizing Design of Experiments (DOE) to identify optimal process parameters.
- Applying big data analytics to detect patterns and outliers that can inform process improvements.
- Ensuring Process Capability Index (CPK) is within acceptable limits to guarantee process stability.
Moreover, the role of yieldWerx in process optimization cannot be overstated. By adjusting for multi-product wafers and factoring in retest operations, yieldWerx helps streamline the qualification process. It also aids in identifying the root causes of yield losses, thereby enabling manufacturers to rectify issues and enhance overall semiconductor production efficiency.
Utilizing YieldWerx for Process Optimization
In the pursuit of process optimization, yieldWerx stands out as a pivotal tool for semiconductor manufacturers. By integrating yieldWerx, companies can fine-tune their manufacturing processes, addressing the root causes of yield losses with precision. The software’s ability to adjust for multi-product wafers and factor in retest operations significantly enhances process efficiency.
yieldWerx’s Gross Die Per Wafer Calculator module is particularly beneficial. It allows engineers to tailor yield calculations to the unique demands of their operations and product specifications, ensuring that yield metrics are a true reflection of factory performance. This level of customization eliminates the need for complex scripting and provides a clear path to increased profitability.
The cloud-based nature of yieldWerx also means that manufacturers have access to powerful analytical tools. These tools are instrumental in pinpointing yield detractors and facilitating the implementation of effective yield enhancement strategies. As a result, semiconductor manufacturers can expect a maximized yield rate, which is crucial for staying competitive in the fast-paced semiconductor industry.
Conclusion
In summary, selecting the right silicon wafer supplier is a multifaceted decision that hinges on a deep understanding of the semiconductor market, the specific needs of your application, and the capabilities of potential suppliers. Factors such as the quality of raw materials, precision of fabrication processes, and the ability to manage defects play a critical role in wafer yield, which in turn affects the overall efficiency and profitability of semiconductor manufacturing. With the current market dynamics of high inventory levels and production costs, alongside the necessity for high operating rates, it’s essential to partner with a supplier that can navigate these challenges effectively. By considering these elements and leveraging the expertise of fab agnostic suppliers like CSS, you can ensure that your priorities are met and that you receive the best possible solution for your unique ASIC needs.
Frequently Asked Questions
What are the key factors to consider when choosing semiconductor materials?
Choosing semiconductor materials involves considering the specific application and requirements, as well as evaluating the advantages and disadvantages of materials such as GaN, GaAs, and SiGe. Material selection impacts chip reliability and performance.
How does CSS ensure the selection of the best wafer fabricator for my ASIC project?
CSS is fab agnostic and selects the best wafer manufacturer based on a tradeoff analysis of price, performance, size, and power, aligning their priorities with the unique requirements of your ASIC project.
What challenges are wafer suppliers facing with current market conditions?
Wafer suppliers are struggling with elevated inventory levels, high production costs, and high operating rates. The high inventory has led to sales difficulties, often necessitating discounts to secure orders.
How does Custom Silicon Solutions ensure quality in their semiconductor supply chain?
Custom Silicon Solutions leverages nearly three decades of ASIC design experience and conducts in-house testing on their 8,000 square foot test floor. They also have strong relationships with key manufacturing and service providers to meet supply chain needs.
What factors influence wafer yield and how can they be optimized?
Wafer yield is influenced by fabrication precision, raw material quality, equipment calibration, defect management, and chip design complexity. Employing statistical process control and cloud-based solutions like yieldWerx can optimize these factors for better yields.
How do high operating rates in the wafer market impact manufacturers?
High operating rates, which have exceeded 85%, are driven by a resurgence in downstream demand. Maintaining these rates helps wafer manufacturers mitigate non-silicon production expenses amidst robust polysilicon prices.