Choosing the Right Wafer Testing Machine for Your Needs
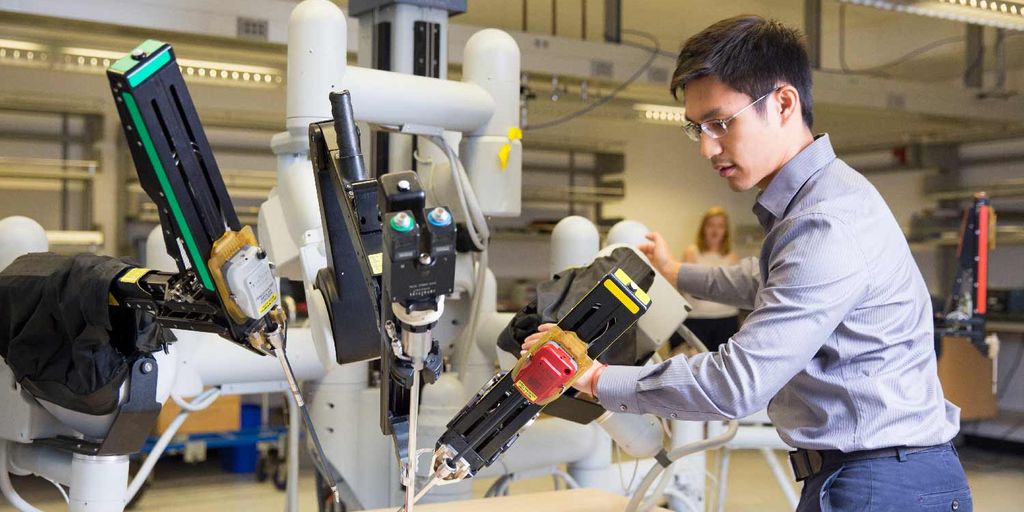
Choosing the right wafer testing machine is a critical decision for ensuring the quality and performance of semiconductor devices. With various types of machines available, each offering unique features and capabilities, it’s essential to understand your specific needs and evaluate the options carefully. This article will guide you through the different types of wafer testing machines, key features to look for, cost considerations, the importance of software integration, and how to ensure reliability and durability. Additionally, we’ll compare leading brands and discuss customization options to help you make an informed decision.
Key Takeaways
- Understand the different types of wafer testing machines, such as probe stations, automatic test equipment (ATE), and specialized testing systems.
- Key features to consider include precision and accuracy, throughput and speed, and compatibility with various wafer sizes.
- Evaluate the total cost of ownership, including initial investment, maintenance costs, and return on investment.
- Software integration is crucial for data analysis, user interface ease of use, and compatibility with existing systems.
- Ensure the reliability and durability of the machine by considering build quality, manufacturer support, and warranty and service agreements.
Understanding Different Types of Wafer Testing Machines
In the field of semiconductor testing, various types of test wafers are employed to meet specific manufacturing and quality assurance needs, utilizing chip probes and other techniques. Each type of test wafer, be it a monitor, dummy, defect, or short loop, plays a distinct role in maintaining high standards in semiconductor testing. These wafers, along with the use of wafer probers and comprehensive chip and die tests, contribute significantly to the production of reliable and high-quality semiconductor products.
Key Features to Look for in a Wafer Testing Machine
When selecting a wafer testing machine, it’s essential to consider several key features to ensure it meets your specific needs. Precision and accuracy are paramount, as even minor errors can significantly impact the quality and performance of wafers. High precision ensures that the machine can detect even the smallest defects, maintaining the high standards expected in today’s technology.
Precision and Accuracy
- High-resolution measurement capabilities
- Advanced calibration options
- Consistent and repeatable results
Throughput and Speed
Throughput and speed are critical for high-volume production environments. A machine with high throughput can test more wafers in less time, increasing overall efficiency. Look for machines that offer:
- Fast testing cycles
- Automated handling systems
- Parallel testing capabilities
Compatibility with Various Wafer Sizes
Compatibility with different wafer sizes is another important feature. Machines that can handle a range of sizes offer greater flexibility and can be used for various applications. Ensure the machine supports:
- Multiple wafer diameters
- Adjustable settings for different thicknesses
- Versatility for future needs
Evaluating the Cost of Wafer Testing Machines
When evaluating the cost of wafer testing machines, it’s essential to consider several factors that go beyond the initial purchase price. Understanding wafer cost is crucial for making an informed decision.
Initial Investment
The initial investment in a wafer testing machine can be substantial. This includes the cost of the machine itself, installation, and any necessary training for your staff. It’s important to compare different models and brands to find the best fit for your budget and needs.
Maintenance Costs
Maintenance costs are an ongoing expense that can add up over time. Regular maintenance is necessary to keep the machine running efficiently and to prevent costly breakdowns. Consider the availability of spare parts and the cost of service agreements when evaluating these expenses.
Return on Investment
Return on investment (ROI) is a critical factor in the decision-making process. A machine with a higher initial cost may offer better performance and lower maintenance costs, leading to a better ROI in the long run. Evaluate the machine’s impact of best practices in wafer testing and how it can improve your overall production efficiency.
Importance of Software Integration in Wafer Testing
Software integration in wafer testing is crucial for enhancing the efficiency and effectiveness of the semiconductor manufacturing process. Integration with the overall manufacturing workflow ensures that insights gained from wafer test analysis can be promptly and effectively implemented, leading to immediate improvements in the manufacturing process. This continuous flow of information enables a proactive approach to quality control.
Ensuring Reliability and Durability in Wafer Testing Machines
The build quality of a wafer testing machine is a critical factor in its reliability and durability. High-quality materials and robust construction ensure that the machine can withstand the rigors of continuous use. Look for machines that feature corrosion-resistant components and sturdy frames to minimize wear and tear over time.
Reliable manufacturer support is essential for maintaining the longevity of your wafer testing machine. This includes access to technical support, regular software updates, and availability of replacement parts. A manufacturer with a strong support network can help you quickly resolve any issues that arise, ensuring minimal downtime.
A comprehensive warranty and service agreement can provide peace of mind and protect your investment. These agreements often cover routine maintenance, repairs, and sometimes even upgrades. Ensure that the warranty terms are clear and that the service agreements offer sufficient coverage to meet your needs.
Comparing Leading Brands of Wafer Testing Machines
When it comes to wafer testing machines, several brands stand out due to their reputation, customer reviews, and proven performance in the industry. Choosing the right brand can significantly impact the efficiency and reliability of your testing processes.
Customizing Wafer Testing Machines for Specific Applications
In the demanding world of semiconductor manufacturing, the wafer fabrication process stands out for its precision and stringent cleanliness requirements. Customizing wafer testing machines to meet specific applications can significantly enhance efficiency and accuracy.
Tailoring to R&D Needs
Research and Development (R&D) environments often require highly flexible and adaptable testing solutions. WHY CUSTOMIZATION AND FLEXIBILITY ARE NEEDED IN WAFER FABRICATION EQUIPMENT. This flexibility allows for rapid prototyping and testing of new semiconductor designs, ensuring that innovative ideas can be quickly validated and iterated upon.
Adapting for High-Volume Production
For high-volume production, the focus shifts to throughput and reliability. Customizing wafer testing machines to handle large quantities of wafers efficiently can lead to significant time savings. For instance, learn how irlabs automated wafer prober reduced time for fault analysis of a wafer from 10 minutes per device to 1 minute per device by automating probing. This kind of customization ensures that production lines run smoothly and meet the high demands of the market.
Special Features for Niche Markets
Certain niche markets may require specialized testing features that are not commonly found in standard wafer testing machines. These can include unique environmental controls, specific types of probes, or integration with other specialized equipment. The world’s first fully modular, field upgradable wafer testing systems offer a range of accessories and features that can be added as needed, making them ideal for these specialized applications.
Conclusion
Choosing the right wafer testing machine is a critical decision that impacts the efficiency and quality of semiconductor manufacturing. As we’ve discussed, it is essential to carefully evaluate your technical requirements, such as reach, weight, footprint, payload, throughput, reliability, and precision. Different applications may demand different types of wafers and testing methods, from electrical testing to advanced imaging techniques like Scanning Electron Microscopy (SEM) and Focused Ion Beam (FIB). By understanding your specific needs and the capabilities of various testing machines, you can ensure that your wafer testing process is both effective and precise, ultimately leading to higher quality outcomes in your semiconductor production.
Frequently Asked Questions
What are the different types of wafer testing machines?
The main types of wafer testing machines include Probe Stations, Automatic Test Equipment (ATE), and Specialized Testing Systems. Each type serves different testing needs and applications.
What key features should I look for in a wafer testing machine?
When selecting a wafer testing machine, consider features such as precision and accuracy, throughput and speed, and compatibility with various wafer sizes.
How do I evaluate the cost of a wafer testing machine?
Evaluating the cost involves considering the initial investment, maintenance costs, and the potential return on investment. It’s important to weigh these factors to determine the overall value.
Why is software integration important in wafer testing machines?
Software integration is crucial for data analysis capabilities, user interface and ease of use, and compatibility with existing systems. Good software can greatly enhance the efficiency and effectiveness of the testing process.
What should I consider to ensure the reliability and durability of a wafer testing machine?
To ensure reliability and durability, consider the build quality, manufacturer support, and warranty and service agreements. These factors can affect the long-term performance of the machine.
Can wafer testing machines be customized for specific applications?
Yes, wafer testing machines can be tailored to meet specific needs such as R&D requirements, high-volume production, or niche market features. Customization can optimize performance for particular applications.