Efficiency and Precision: The Evolution of Semiconductor Manufacturing
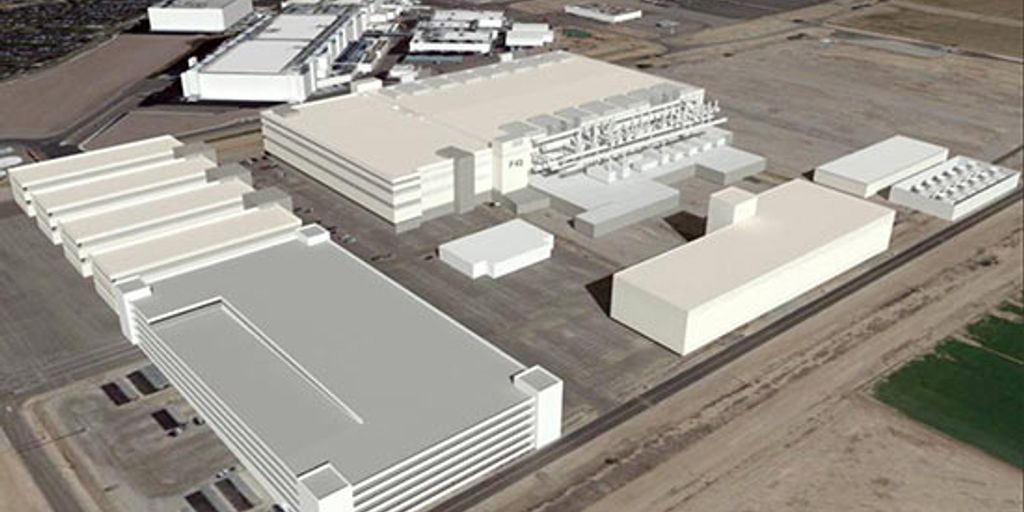
The evolution of semiconductor manufacturing encapsulates the transition from rudimentary manual processes to today’s sophisticated automated systems. This journey, driven by technological advancements, has been pivotal in meeting the ever-increasing demand for smaller, faster, and more efficient semiconductor devices. The industry’s focus on precision and efficiency not only enhances device performance but also addresses economic and environmental concerns, ensuring sustainability in the high-stakes market of semiconductor production.
Key Takeaways
- The shift from manual to automated semiconductor manufacturing has significantly increased production efficiency and device reliability.
- Advancements in CNC technology and automation have enabled unprecedented precision in semiconductor fabrication, reducing defects and variability.
- The development of nanoscale manufacturing techniques like FinFET and multiple patterning has been crucial in continuing Moore’s Law.
- Stringent quality control measures and advanced testing standards are essential for maintaining consistency and minimizing defects in semiconductor production.
- High-volume production techniques are vital for meeting global demand, ensuring that semiconductor manufacturing remains both efficient and cost-effective.
The Historical Progression of Semiconductor Manufacturing
From Manual to Automated Processes
The journey from manual assembly lines to highly automated and precise manufacturing processes marks a significant evolution in semiconductor manufacturing. This transition has enabled the production of semiconductor devices at unprecedented scales and speeds, reflecting a major shift in how these critical components are created.
Key Technological Milestones
Semiconductor manufacturing has been defined by several key technological milestones. These include the development of silicon dominance, the rise of MOS technology, and the microprocessor revolution. Each milestone has played a pivotal role in shaping the industry, driving it towards greater efficiency and capability.
Impact on Device Evolution
The advancements in semiconductor manufacturing have had a profound impact on the evolution of devices. Smaller, faster, and more efficient devices have become possible due to innovations such as advanced lithography techniques and the introduction of nanotechnology. These developments have not only enhanced device performance but also expanded their applications across various sectors.
Advancements in Precision Manufacturing
Role of CNC and Automation
Recent years have seen remarkable developments in CNC technology, each aiming at enhancing precision, efficiency, and versatility. These advancements are pivotal in meeting the stringent standards required in semiconductor manufacturing, where maintaining tolerances within a few microns is crucial.
Improvements in Tooling and Control
- High-Precision Tooling: The introduction of ultra-precise cutting tools has allowed for even finer work at the micron level, crucial for semiconductor applications. These tools have higher durability and can maintain sharpness for longer periods, ensuring consistent quality.
- Advanced Control Systems: Modern CNC machines are equipped with sophisticated control systems that offer greater precision and control over the manufacturing process.
Effects on Semiconductor Device Quality
Precision manufacturing is the backbone of the semiconductor industry. The industry’s ability to create increasingly smaller and more powerful semiconductor devices relies heavily on advancements in precision manufacturing techniques and technologies. The pursuit of precision is a driving force behind the continuous evolution and innovation in semiconductor manufacturing.
Challenges in Miniaturization and Nanoscale Manufacturing
Scaling to Atomic Dimensions
As semiconductor devices shrink to atomic dimensions, manufacturers face significant challenges, including quantum effects and leakage currents. The precision required at this scale is unprecedented, demanding innovations like advanced lithography techniques and new materials.
Overcoming Quantum Effects and Leakage
The reduction in feature size increases the occurrence of quantum effects and leakage, which can significantly impact device performance. To address these issues, the industry has developed solutions such as FinFET technology, which helps to control leakage and improve electrical conductivity.
Innovations like FinFET and Multiple Patterning
To continue scaling down device sizes while maintaining functionality, the semiconductor industry has embraced technologies like FinFET and multiple patterning. These innovations are crucial for achieving the desired transistor density and performance in modern integrated circuits.
Quality Control in Semiconductor Manufacturing
Ensuring Consistency and Minimizing Defects
Ensuring consistency and minimizing defects are critical for maintaining high standards in semiconductor manufacturing. The use of cleanrooms and advanced monitoring systems plays a significant role in achieving these goals. Rigorous protocols and regular audits help in maintaining the integrity of the manufacturing environment, crucial for the production of high-quality semiconductors.
Testing Methods and Standards
Precision in testing methods is essential for identifying even the most subtle defects in semiconductor devices. Advanced testing techniques, such as automated optical inspection and electron microscopy, ensure that only components meeting the highest standards reach the market. This meticulous approach to quality control is vital for sustaining device reliability and performance.
Impact on Device Reliability and Performance
The impact of rigorous quality control on device reliability and performance cannot be overstated. Precision manufacturing directly influences the performance and reliability of semiconductor devices. Small deviations in the fabrication process can lead to significant issues, such as electrical inefficiencies or device failure. Therefore, maintaining strict quality control measures is imperative for meeting the high-performance requirements of modern semiconductor devices.
High-Volume Production Techniques
Scale of Operations and Global Demand
The semiconductor industry operates on a massive scale to meet the global demand for electronic devices. Precision manufacturing enables consistent and reproducible fabrication processes, ensuring that large quantities of high-quality semiconductor components can be produced efficiently and reliably.
Precision in Mass Production
Precision is critical when handling materials with specific electronic properties, ensuring the successful integration of these materials into semiconductor devices. Advanced technologies like extreme ultraviolet (EUV) lithography require exceptional precision to achieve smaller feature sizes.
Efficiency and Reliability in Output
The precision in manufacturing processes directly influences the performance and reliability of semiconductor devices. Small deviations or imperfections in the fabrication process can lead to electrical inefficiencies, reduced speed, or even device failure. Achieving precise dimensions and material characteristics is crucial for meeting performance requirements.
Advanced Materials and Technologies
New Materials in Semiconductor Fabrication
The semiconductor industry continuously integrates new materials with enhanced electronic properties to improve device performance. High-k dielectrics and strained silicon are examples of materials that have significantly boosted transistor efficiency and reliability.
3D Architectures and Their Advantages
Innovative 3D architectures, like those involving graphene and silicon carbide, address the challenges of miniaturization. These structures not only enhance the device’s electrical properties but also contribute to more sustainable manufacturing practices.
Continuing Moore’s Law with Advanced Techniques
The relentless pursuit of Moore’s Law is supported by advanced manufacturing techniques, including precision optical lithography. These techniques are crucial for scaling down to atomic dimensions while maintaining the functionality and efficiency of semiconductor devices.
Economic Impacts of Efficient Semiconductor Manufacturing
Cost Reduction and Increased Yield
Efficient semiconductor manufacturing techniques have significantly reduced the cost per wafer, enhancing the economic viability of semiconductor production. This cost efficiency is achieved through advanced precision manufacturing, which minimizes defects and maximizes yield. The industry’s focus on scaling and clustering also contributes to cost savings, making large-scale investments more appealing.
Market Competitiveness
The ability to produce semiconductors efficiently is crucial for maintaining a competitive edge in the global market. Companies that adopt innovative manufacturing technologies can better meet the rapidly increasing demand for high-performance electronic devices, thus securing a significant market share.
Sustainability and Environmental Considerations
The semiconductor industry is increasingly focusing on sustainability. Efforts to reduce the use of hazardous materials and to implement energy-efficient processes are essential for minimizing environmental impact. These practices not only comply with global environmental standards but also improve the industry’s public image and long-term sustainability.
Conclusion
The journey of semiconductor manufacturing from its rudimentary beginnings to the cutting-edge processes of today underscores a relentless pursuit of efficiency and precision. As we have explored, the evolution of this industry is marked by significant advancements in technology that have not only enhanced the quality and performance of semiconductor devices but also addressed the challenges of scaling and complexity. The future of semiconductor manufacturing promises even greater innovations, as the industry continues to adapt to the demands for smaller, faster, and more efficient components. This ongoing evolution will undoubtedly continue to shape the technological landscape, driving progress in countless fields that rely on semiconductor technology.
Frequently Asked Questions
What is semiconductor manufacturing?
Semiconductor manufacturing is the process of creating semiconductor devices used in electronic systems. It involves various fabrication techniques to produce smaller, faster, and more efficient devices, adapting to technological advancements and growing demands.
How has semiconductor manufacturing evolved over time?
Semiconductor manufacturing has evolved from manual production methods to high-tech automated processes. This evolution includes advancements in precision manufacturing, miniaturization, and the use of advanced materials and technologies to meet the needs of modern electronic devices.
What role does precision manufacturing play in the semiconductor industry?
Precision manufacturing is crucial in the semiconductor industry due to the microscopic scale and intricate details of semiconductor devices. It ensures high reliability, performance, and yield by minimizing defects and achieving precise dimensions and material characteristics.
What are the challenges of nanoscale semiconductor manufacturing?
Nanoscale semiconductor manufacturing faces challenges such as quantum effects, leakage currents, and process variability. Innovations like FinFET and multiple patterning techniques are crucial to overcome these challenges and continue device scaling.
How does high-volume production impact semiconductor manufacturing?
High-volume production in semiconductor manufacturing requires precise and reproducible processes to meet global demand. Precision manufacturing enables the production of large quantities of high-quality components efficiently and reliably.
What are the economic impacts of efficient semiconductor manufacturing?
Efficient semiconductor manufacturing leads to cost reduction, increased yield, and enhanced market competitiveness. It also contributes to sustainability by reducing waste and improving the overall cost efficiency of production.