Efficient Wafer Processing Strategies
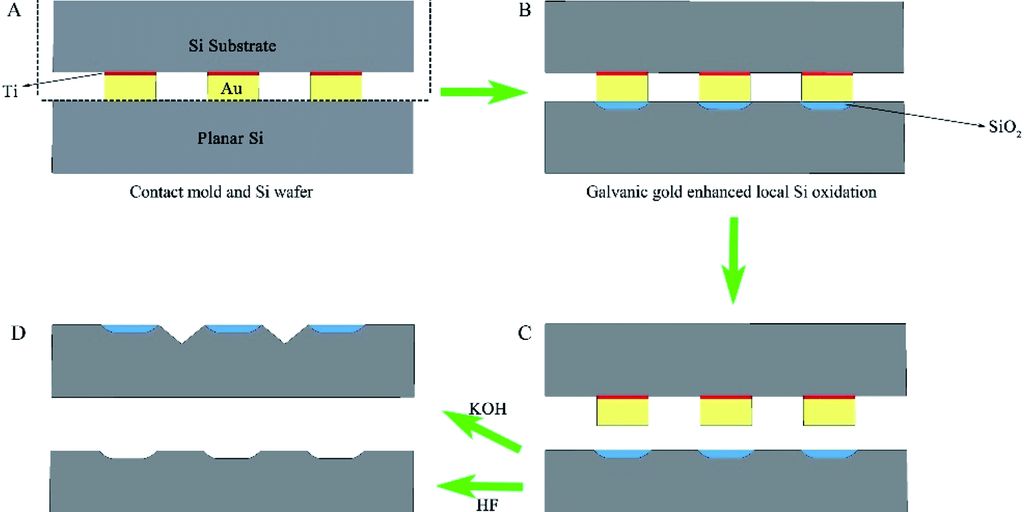
The article ‘Efficient Wafer Processing Strategies’ explores various techniques and innovations aimed at optimizing the wafer processing in semiconductor manufacturing. From minimizing wafer breakage to implementing cutting-edge cleaning technologies, the strategies discussed are crucial for enhancing production efficiency and quality. This article provides a comprehensive overview of the processes involved and highlights the latest advancements in the field.
Key Takeaways
- Implementing advanced wafer processing strategies can significantly reduce breakage and enhance the quality of semiconductor devices.
- Wafer thinning techniques such as mechanical grinding and chemical-mechanical planarization are critical for achieving ultra-thin chips with minimal thickness tolerances.
- Optimizing wafer dicing processes through precise equipment settings and process parameters is essential for improving product quality and manufacturing yields.
- Regular maintenance and calibration of equipment are vital for maintaining processing efficiency and preventing defects in wafer production.
- Innovations in wafer processing, including new dicing technologies and tailor-made software solutions, are pivotal for developing smaller, faster, and more efficient semiconductor components.
Overview of Wafer Processing Strategies
Minimizing Wafer Breakage
Implementing effective wafer processing strategies is crucial for minimizing wafer breakage. This not only reduces material waste but also enhances the overall yield of the production process.
Ensuring High-Quality Semiconductor Devices
High-quality semiconductor devices are essential for meeting the demands of modern technology. Through meticulous wafer processing, manufacturers can ensure that each semiconductor meets the required standards of performance and reliability.
Key Benefits of Effective Wafer Processing
Effective wafer processing offers numerous benefits including improved product quality, increased efficiency, and reduced costs. These advantages make it a critical aspect of semiconductor manufacturing.
Wafer Thinning Techniques
Mechanical Grinding
Mechanical grinding is a critical method for wafer thinning, involving the removal of material using a diamond and resin-bonded grind wheel. The process is meticulously guided by a grind recipe that determines spindle speed and material removal rate. Prior to grinding, a protective layer of grinding tape is applied to the wafer’s front. This method comprises two main steps: Coarse Grinding for rapid material removal and Fine Grinding for more precise thinning.
Chemical-Mechanical Planarization
Chemical-Mechanical Planarization (CMP) offers a unique approach to wafer thinning, combining chemical slurry with mechanical polishing to achieve ultra-smooth surfaces. This technique is essential for achieving thickness tolerances of ≤1µm, crucial for the production of ultra-thin chips. CMP is particularly effective in minimizing surface defects and ensuring uniform thickness across the wafer.
Achieving Ultra-Thin Chips
The ultimate goal of wafer thinning is to produce chips that are not only smaller but also functionally superior. Thinning the entire wafer after front-end processing is the most effective strategy for producing ultra-thin chips. This process addresses critical industry demands such as improved heat management, reduced chip stress, and increased packaging and dicing yield, thereby streamlining the packaging and dicing processes and reducing defects like chipping.
Challenges in Wafer Dicing
Precision and Accuracy
Achieving precision and accuracy in wafer dicing is crucial for the production of high-quality semiconductor devices. Various strategies, such as optimizing blade speed and pressure, can be employed to enhance these aspects.
Die Chipping and Breakage
Die chipping and breakage are significant challenges that can reduce yield and increase production costs. Techniques to mitigate these issues include adjusting the dicing blade’s properties and optimizing the dicing process to minimize stress on the wafer.
Contamination and Cleanliness
Maintaining cleanliness and avoiding contamination are essential for ensuring the performance and reliability of semiconductor devices. Stringent cleanliness standards are required, and effective contamination control strategies are crucial in the wafer dicing process.
Optimizing the Wafer Dicing Process
Equipment Settings and Process Parameters
Optimizing the wafer dicing process is crucial for semiconductor manufacturers to achieve higher yields, reduce costs, and improve product quality. Master precision cutting with our dicing blade operations guide. Several factors can impact the efficiency and precision of the dicing process, including equipment settings and process parameters.
Material Properties Impact
Choosing the most suitable dicing method and process parameters for a specific wafer material and application is crucial for achieving optimal results. Factors such as material properties, die size, and required throughput should be considered when selecting between mechanical, laser, or plasma dicing techniques.
Continuous Improvement in Manufacturing
Achieving precision and accuracy in wafer dicing:
- Optimizing dicing parameters can help minimize contamination.
- Use of cleanroom facilities and equipment is recommended to maintain cleanliness during the dicing process.
Equipment Calibration and Maintenance
Importance of Regular Maintenance
Regular maintenance is crucial for ensuring the longevity and efficiency of wafer processing equipment. Routine checks and servicing prevent unexpected downtimes and maintain optimal performance levels, which are essential for high-quality wafer production.
Impact on Wafer Processing Efficiency
Proper calibration and maintenance of equipment directly impact the processing efficiency and quality of the wafers. Misaligned or poorly maintained equipment can lead to defects in the wafers, affecting the overall yield and quality.
Strategies for Effective Calibration
To achieve effective calibration, follow these steps:
- Implement advanced process control (APC) systems to adjust process parameters in real-time based on inline metrology data.
- Utilize predictive maintenance techniques to foresee and mitigate potential equipment failures.
- Ensure strict material handling protocols to maintain the integrity of both the equipment and the wafers.
Wafer Cleaning Techniques
Maintaining Cleanliness
Maintaining cleanliness in wafer processing is crucial to prevent defects and ensure high-quality semiconductor devices. The primary method used for decades is the RCA clean process, which involves acidic hydrogen peroxide and ammonium hydroxide solutions. This method is essential for removing organic residues and microscopic particles from the wafer surface.
Minimizing Contamination
To minimize contamination, it’s vital to control the environment and handle materials properly during the cleaning process. The implementation of optimized cleaning technologies, such as ozone treatments, has enhanced the effectiveness of traditional methods. These advancements help in achieving the stringent cleanliness required for today’s high-performance semiconductors.
Advancements in Cleaning Technologies
Recent advancements in wafer cleaning technologies have focused on improving efficiency and reducing environmental impact. Newer methods include using less hazardous chemicals and more precise application techniques to ensure thorough cleaning without damaging the wafer. These innovations are crucial for keeping pace with the evolving demands of semiconductor manufacturing.
Innovations in Wafer Processing
Developments in Dicing Technologies
Recent years have seen significant developments in dicing technologies, particularly with the introduction of advanced laser dicing systems. These systems enhance precision and reduce damage, crucial for maintaining the integrity of the wafers during the dicing process.
Enhancements for Smaller, Faster Components
The drive towards smaller, faster components in semiconductor devices has spurred numerous enhancements in wafer processing. Innovations such as self-dicing materials, which allow for controlled fracturing under specific conditions, are pivotal in this advancement.
Tailor-Made Software Solutions
To complement the physical innovations in wafer processing, tailor-made software solutions have been developed. These software tools optimize the dicing parameters and process controls, ensuring high efficiency and minimal wastage during the wafer dicing process.
Conclusion
In conclusion, the implementation of efficient wafer processing strategies is crucial for the advancement of semiconductor manufacturing. By focusing on minimizing wafer breakage, optimizing the wafer thinning and dicing processes, and maintaining cleanliness, manufacturers can achieve higher yields, reduce costs, and produce high-quality semiconductor devices. These strategies not only address current industry demands for smaller, faster, and more energy-efficient components but also pave the way for continuous improvement in semiconductor operations. The integration of manual, semi-automatic, and fully automated processes, along with the adoption of new technologies, ensures that semiconductor manufacturing remains at the forefront of technological innovation.
Frequently Asked Questions
What are the primary goals of wafer thinning?
The primary goals of wafer thinning are to achieve thickness tolerances of ≤1µm and reduce wafers to final thicknesses as low as 20 µm, improving heat management, reducing chip stress, and increasing packaging and dicing yield.
How can wafer breakage be minimized?
Implementing effective wafer processing strategies, such as careful handling, optimized equipment settings, and advanced dicing techniques, can help minimize wafer breakage and ensure the production of high-quality semiconductor devices.
What are the key methods for wafer thinning?
The key methods for wafer thinning include mechanical grinding and chemical-mechanical planarization, each offering unique benefits in the thinning process.
What strategies enhance precision and accuracy in wafer dicing?
Enhancing precision and accuracy in wafer dicing involves optimizing equipment settings, process parameters, and considering material properties to achieve higher yields and improve product quality.
What are the common challenges in wafer dicing?
Common challenges in wafer dicing include achieving precision and accuracy, managing die chipping and breakage, and maintaining cleanliness to minimize contamination.
How can continuous improvement be achieved in semiconductor manufacturing?
Continuous improvement in semiconductor manufacturing can be achieved by using optimization strategies with manual and semi-automatic operations, running processes on fully automated wafer fabrication equipment, and implementing tailor-made software solutions.