Enhancing Quality and Efficiency: The Rise of Automated Test Equipment
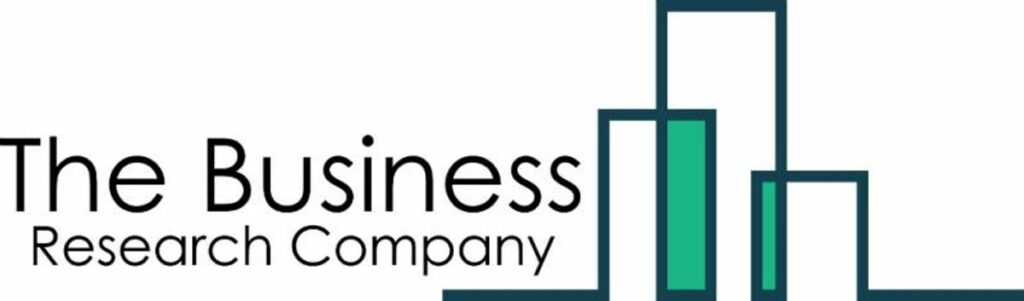
Automated Test Equipment (ATE) has become a cornerstone in the realm of electronics manufacturing, providing vital solutions for ensuring the quality and efficiency of electronic devices. The integration of advanced functionalities in ATE meets the challenges posed by the miniaturization of components and the rapid pace of production cycles. With the electronics industry evolving rapidly, ATE systems are crucial for maintaining high standards of device reliability and performance. This article explores the rise of ATE, highlighting its evolution, key components, innovations, and market trends that signal its growing importance in the manufacturing landscape.
Key Takeaways
- The evolution of ATE is closely tied to the challenges of miniaturization and the need for precision testing to ensure device reliability in electronics manufacturing.
- Critical components such as Industrial PCs, handlers, probers, and mass interconnect systems significantly enhance ATE performance and efficiency.
- Innovations in non-memory ATE systems are driven by the demand for high precision and comprehensive testing capabilities, leading to the development of modular ATE platforms.
- Optimizing test processes with ATE involves enhancing test coverage, fostering collaboration across teams, and utilizing trend analysis for continuous improvement.
- Market trends in ATE reflect a surge in demand for consumer and automotive electronics, spurring innovation in portable testing solutions and predicting future growth in ATE development.
The Evolution of Automated Test Equipment in Electronics Manufacturing
Meeting the Challenges of Miniaturization
The relentless drive towards miniaturization in electronics has been a defining trend, with Automated Test Equipment (ATE) evolving to meet the intricate demands of testing smaller and more complex Printed Circuit Board Assemblies (PCBAs). As the size of electronic components and systems decreases, the challenges in ensuring their quality and functionality increase exponentially.
The miniaturization of ATE components is not just a trend but a necessity, driven by the need for space-saving solutions that can perform complex tests on these miniature devices. This shift has led to the development of portable ATE devices that are not only compact but also equipped to handle the sophisticated testing required for today’s electronics. These advancements reflect the industry’s commitment to innovation and its ability to adapt to the changing landscape of electronics manufacturing.
The growth of the Internet of Things (IoT) and connected devices further catalyzes the demand for ATE. The integration of sensors and other miniature components into a wide array of products necessitates ATE that can execute detailed and precise tests. This ensures that despite the increased complexity due to miniaturization, device reliability and performance standards are uncompromised.
Ensuring Device Reliability Through Precision Testing
The relentless advancement in semiconductor technology has made precision testing an indispensable part of the manufacturing process. As devices become more complex and integrated, Automated Test Equipment (ATE) must perform detailed and precise tests to meet stringent reliability and performance standards. The role of ATE is particularly crucial in the era of miniaturization, where even the smallest defects can lead to significant failures.
Automated tests are designed to reduce human error and ensure consistent, reproducible results. By following predefined steps and criteria, ATE systems eliminate the risk of human mistakes and misinterpretation. This uniformity is essential for tracking errors and regressions, ultimately enhancing the dependability of test results and the trust stakeholders place in them.
The growth of IoT and connected devices further catalyzes the demand for ATE, as rapid testing is required to keep up with the production pace while maintaining quality. The table below outlines the key benefits of precision testing with ATE:
Benefit | Description |
---|---|
Consistency | Automated tests execute scripts exactly, reducing variance and increasing reliability. |
Accuracy | ATE systems assess a wide range of parameters with high precision. |
Efficiency | Rapid testing aligns with fast production cycles, ensuring timely quality assurance. |
The Role of ATE in Rapid Production Cycles
In the fast-paced world of electronics manufacturing, Automated Test Equipment (ATE) plays a pivotal role in maintaining the momentum of production cycles. The integration of ATE systems is essential for meeting the high throughput demands while preserving the integrity and quality of electronic devices.
ATE systems streamline the testing process, significantly reducing the time required for quality assurance. This efficiency is achieved through the synergy of various components, such as Industrial PCs, which provide the computational might for complex testing procedures, and handlers that ensure the seamless movement of devices through the testing phases.
The impact of ATE on production cycles can be illustrated by the following key points:
- Accelerated testing processes allow for quicker time-to-market.
- Enhanced precision in testing reduces the incidence of defects and recalls.
- Real-time data analysis facilitates immediate feedback and adjustments.
As industries like Aerospace, Defense, and Healthcare increasingly rely on ATE for their mission-critical applications, the importance of ATE in rapid production cycles becomes even more pronounced. The ability to swiftly integrate and utilize new ATE technologies is a competitive advantage that manufacturers strive to achieve.
Key Components and Their Impact on ATE Performance
The Central Function of Industrial PCs
In the realm of Automated Test Equipment (ATE), Industrial PCs play a pivotal role as the brains of the operation. They provide the necessary computational power to manage and execute complex testing procedures, ensuring that electronic devices meet the stringent standards required for performance and reliability. Industrial PCs are tasked with coordinating the various components of ATE systems, from signal generation to data acquisition and analysis.
The responsibilities of Industrial PCs in ATE systems can be summarized as follows:
- Control and management of test sequences
- Data processing and storage
- User interface and system interaction
- Integration with other industrial automation systems
Given their central role, the performance of Industrial PCs directly impacts the efficiency and accuracy of the testing process. Manufacturers continually seek advancements in processing speed, data handling capabilities, and connectivity options to keep pace with the evolving demands of electronics testing.
Importance of Handlers in ATE Ecosystem
In the intricate landscape of Automated Test Equipment (ATE), handlers emerge as pivotal components, accounting for a significant portion of the market share within the ATE component segment. These mechanical systems are engineered to automatically position the device under test (DUT) within the ATE system, a function that is crucial for maintaining the delicate balance between speed and precision in high-volume manufacturing settings.
Handlers not only contribute to the overall efficiency of ATE systems but also play a key role in ensuring that the rapid testing required to keep up with the production of electronic devices does not compromise on quality. The reliance on handlers is underscored by their substantial market share, which is indicative of their integral role in the ATE ecosystem.
- Handlers Market Share: 34.2%
- Function: Automatic placement of DUT
- Impact: Enhanced testing efficiency and throughput
- Significance: Vital in high-volume manufacturing
The interplay between handlers and other ATE components such as Industrial PCs, Mass Interconnect systems, and Probers is also noteworthy. Each element contributes uniquely to the functionality and efficiency of ATE systems, with Industrial PCs providing the necessary computational power to manage complex testing processes.
Advancements in Probers and Mass Interconnect Systems
The relentless pursuit of efficiency in Automated Test Equipment (ATE) has led to significant advancements in probers and mass interconnect systems. Probers have evolved to meet the exacting demands of wafer testing, ensuring precise contact and accurate electrical tests on semiconductor wafers. These improvements have been pivotal in maintaining the integrity of the testing process, especially as device complexity increases.
Mass interconnect systems are the backbone of ATE, providing a robust interface for signal transmission between the test equipment and the devices under test. The advancements in these systems have streamlined the testing process, offering enhanced reliability and reduced setup times. The table below highlights the key improvements in probers and mass interconnect systems over recent years:
Year | Prober Advancements | Mass Interconnect Enhancements |
---|---|---|
2020 | Increased precision | Modular design for flexibility |
2021 | Faster setup times | Improved signal integrity |
2022 | Enhanced automation | Greater scalability |
2023 | Integration with ML analytics | Advanced diagnostics capabilities |
These innovations not only bolster the performance of ATE systems but also contribute to the overall quality and efficiency of the electronics manufacturing process. As the industry continues to evolve, the role of probers and mass interconnect systems in maintaining high testing standards becomes increasingly critical.
Innovations in Non-Memory ATE Systems
Demand for High Precision in Non-Memory Semiconductor Testing
The relentless advancement in semiconductor technology has led to an era where precision is paramount. The intricate designs and shrinking node sizes of today’s semiconductor devices demand high-precision testing to ensure they meet the stringent reliability and performance standards required by the industry.
Non-memory ATE systems have become critical in addressing these needs, offering a range of testing capabilities that are essential for verifying the complex functionalities integrated into modern semiconductors. These systems are designed to execute detailed tests that can accurately assess various parameters, from electrical characteristics to signal integrity.
The table below highlights the key factors driving the demand for high-precision non-memory ATE systems:
Factor | Description |
---|---|
Design Complexity | Increased integration of advanced functionalities in smaller chip sizes. |
Performance Standards | Need to meet high reliability and functionality standards for diverse applications. |
Industry Trends | Growth of IoT and connected devices requiring meticulous validation. |
As the semiconductor industry continues to evolve, the role of non-memory ATE in ensuring the quality and reliability of devices becomes increasingly indispensable. Manufacturers are investing in these sophisticated testing solutions to keep pace with the rapid growth of electronics design complexity and to maintain a competitive edge in the market.
Comprehensive Testing Capabilities for Quality Assurance
Automated Test Equipment (ATE) systems have revolutionized the approach to Quality Assurance (QA) in the electronics industry. The implementation of comprehensive test suites ensures that a wide range of scenarios are validated, significantly reducing the likelihood of regression issues and bolstering software functionality.
The scalability of ATE systems allows for repeated execution of automated tests without the constraints of time and resources that typically limit manual testing. This ensures a thorough validation of software functionality under various conditions, exposing hidden defects and guaranteeing reliable performance. The result is a product that maintains user satisfaction and loyalty, contributing to a prompt time-to-market.
ATE systems not only enhance test coverage but also optimize test execution. Automation Test Engineers configure dashboards and reports to provide stakeholders with real-time insights into test status, progress, and quality metrics. This level of detail supports informed decision-making and proactive risk management, essential for maintaining high standards in product quality.
The Shift Towards Modular ATE Platforms
The industry’s pivot to modular Automated Test Equipment (ATE) platforms is a direct response to the dynamic nature of electronic device manufacturing. Modular systems are increasingly favored for their ability to be customized, addressing the specific testing requirements of a wide array of products. This flexibility is crucial in a market characterized by rapid technological advancements and a diverse product range.
Modular ATE platforms are not only adaptable but also scalable, making them a cost-effective solution for manufacturers. They can be easily upgraded or reconfigured, which means that the same system can be used for different devices over time, reducing the need for multiple dedicated testing systems. The following table highlights the key benefits of modular ATE platforms:
Benefit | Description |
---|---|
Flexibility | Tailored to meet specific testing needs |
Scalability | Can grow with production demands |
Cost-Effectiveness | Reduces the need for multiple systems |
Upgradability | Easily updated to handle new technologies |
The shift towards modular ATE platforms signifies a promising direction for the industry, with the potential to enhance both the quality and efficiency of the testing process.
Optimizing Test Processes with Automated Test Equipment
Enhancing Test Coverage and Process Efficiency
Automated Test Equipment (ATE) has revolutionized the way testing is conducted in the electronics industry. By running more test cases across various platforms and devices, ATE enables a higher level of test coverage, ensuring that products are rigorously evaluated under diverse conditions. This comprehensive approach to testing is critical for early problem detection, which in turn leads to better product quality.
The efficiency of test processes is also significantly improved with ATE. Automation takes over repetitive tasks, freeing up test engineers to focus on more complex issues that require human insight. Moreover, the ability to perform parallel testing in multiple environments not only reduces resource consumption but also shortens the test cycle duration. As a result, teams can maintain high productivity levels while ensuring the reliability and quality of their products.
Optimizing the test execution environment is another key aspect where ATE shines. Automated test engineers work closely with infrastructure teams to ensure that all necessary data and configurations are in place for accurate and reliable testing. This collaboration is essential for achieving optimal test conditions and further enhancing the efficiency of the testing process.
Collaboration Across Teams for Quality and Performance Standards
The integration of automated test equipment (ATE) into the development cycle fosters a continuous feedback loop that is essential for maintaining high quality and efficiency. Automation Test Engineers play a pivotal role in this process, working closely with developers and DevOps teams to optimize continuous integration (CI) workflows and streamline test execution. This collaboration ensures that testing is not only thorough but also swift, allowing for rapid iterations and improvements.
Cross-functional collaboration is key to enhancing the quality of automated tests. By sharing knowledge and aligning on best practices, teams can encourage a culture of quality that permeates every stage of the testing lifecycle. The table below illustrates the areas of collaboration and their impact on test quality and efficiency:
Area of Collaboration | Impact on Test Quality | Impact on Test Efficiency |
---|---|---|
CI Workflow Optimization | Ensures thorough coverage | Reduces time to market |
Parallel Testing | Increases test reliability | Maximizes resource utilization |
Test Script Reuse | Maintains consistency | Saves time and effort |
Furthermore, Automation Test Engineers configure dashboards and reports to provide stakeholders with real-time insights into test status and progress. This level of transparency enables informed decision-making and proactive risk management, ultimately leading to a more robust and reliable product.
Trend Analysis for Continuous Improvement in Testing
In the realm of Automated Test Equipment (ATE), trend analysis plays a pivotal role in elevating the quality and efficiency of testing processes. By meticulously examining test results, engineers can discern patterns and trends that signal opportunities for enhancement. This analytical approach is not only about identifying flaws but also about forecasting potential issues, thereby preemptively improving test coverage and process efficiency.
Collaboration is key in this endeavor. Automation Test Engineers work alongside cross-functional teams to establish quality gates, thresholds, and acceptance criteria. These standards are aligned with business objectives and key performance indicators (KPIs), ensuring that the testing process contributes to the overall success of the product.
The adoption of cloud-based testing solutions is a notable trend within the ATE market. These solutions offer remote access and centralized data management, which are essential for a more efficient and flexible testing environment. Moreover, engineers maintain and optimize the health and performance of the test environment, ensuring consistent and reliable test results across various conditions.
To facilitate continuous improvement, engineers create custom reports and dashboards that provide stakeholders with real-time insights into test status, progress, and quality metrics. This level of transparency empowers informed decision-making and proactive risk management, ultimately leading to a more robust and reliable product.
Market Trends and Growth Prospects in Automated Test Equipment
The Surge in Demand for Consumer and Automotive Electronics
The global automated test equipment market is experiencing a significant upswing, driven by the proliferation of smart devices and the IoT revolution. The demand for ATE solutions is intensifying as they become essential for testing the efficiency, durability, and compliance of these complex devices with communication standards. The market, valued at USD 7643.8 million in 2023, is projected to grow steadily, with a CAGR of 3.1% from 2024 to 2030.
In the automotive sector, the swift transition towards electric and autonomous vehicles is amplifying the need for ATE. These vehicles, laden with sophisticated electronic systems, necessitate comprehensive testing to meet industry standards. The integration of Advanced Driver Assistance Systems (ADAS), infotainment, and electrification components has markedly increased the reliance on ATE to ensure safety, reliability, and performance.
The continuous evolution within the semiconductor industry, coupled with advancements in automotive electronics, is reshaping the ATE landscape. As product lifecycles shorten and the demand for high-quality electronics escalates, ATE is pivotal in enabling manufacturers to keep pace with rapid market developments and the integration of emerging technologies such as 5G, IoT, and AI.
Innovation in Portable and On-Site Testing Solutions
The trend towards portable and field-deployable test instruments is a response to the growing necessity for on-site testing and maintenance. This shift is particularly evident in industries where rapid troubleshooting and repair are crucial to maintaining operational efficiency. Portable ATE systems are not only space-saving but also capable of performing complex tests on miniature electronic components and systems, addressing the demand for on-the-go testing capabilities.
Modular ATE platforms are becoming increasingly popular, offering the flexibility to be tailored for specific applications. These platforms efficiently address the testing needs of diverse electronic devices, reflecting the industry’s move towards adaptable solutions. The following points highlight the advantages of portable and modular ATE systems:
- Tailored testing capabilities for a wide range of electronic products
- Reduced capital expenditures through cloud-based testing platforms
- Enhanced collaboration across global teams via centralized data management
- Improved time-to-market for new products
The growth in modular and customizable ATE platforms signifies a promising area for growth and development within the test and measurement equipment market.
Future Directions for ATE Development
As the landscape of electronics continues to evolve, the Automated Test Equipment (ATE) market is poised for significant transformation. The push towards modular ATE platforms is a testament to the industry’s need for adaptable and scalable testing solutions. These platforms offer the flexibility to efficiently address the testing needs of diverse electronic devices, a trend driven by the rapid pace of technological innovation.
The growth of IoT and connected devices catalyzes ATE demand, underscoring its vital role in supporting the industry’s quality assurance and efficiency requirements. Similarly, opportunities in automobile electronics testing drive ATE market expansion, with modern vehicles incorporating increasingly sophisticated electronic systems.
Key Market Projections:
- Market Growth: Projected to reach approximately USD 12.5 Billion by 2033.
- CAGR: Estimated growth at a CAGR of 4.80% from 2024 to 2033.
- Segmentation:
- Products: Non-Memory ATE holds the largest share (64.2%), followed by Memory ATE and Discrete ATE.
Looking ahead, ATE development will likely focus on enhancing precision and integration capabilities to meet the complex demands of advanced semiconductor technologies. The industry’s trajectory suggests a substantial market expansion potential, with ATE becoming increasingly critical across multiple sectors, including aerospace, defense, and healthcare.
Conclusion
The ascent of Automated Test Equipment (ATE) marks a transformative era in the realm of electronics manufacturing, where quality and efficiency are paramount. As we have seen, the integration of advanced functionalities within ATE systems is not only a response to the growing complexity of electronic devices but also a testament to the industry’s commitment to innovation. The demand for rapid, precise, and versatile testing solutions is at an all-time high, driven by the relentless pace of technological advancements and the proliferation of electronic products in sectors such as consumer electronics, automotive, and aerospace. The ATE market’s growth trajectory, underscored by the development of modular and portable platforms, signifies a promising future for both manufacturers and consumers. In this dynamic landscape, ATE stands as a cornerstone, ensuring that the electronic devices we rely on meet the highest standards of performance and reliability.
Frequently Asked Questions
What is the role of Automated Test Equipment (ATE) in electronics manufacturing?
ATE plays a crucial role in electronics manufacturing by executing detailed and precise tests to ensure device reliability and performance. It is essential for verifying the functionality of increasingly complex and miniaturized electronic components.
How do handlers contribute to the ATE ecosystem?
Handlers are critical components in the ATE ecosystem, facilitating rapid testing to maintain production pace while ensuring quality. They work alongside other components, such as Industrial PCs and Mass Interconnect systems, to enhance the efficiency of ATE systems.
What components make up an ATE system?
An ATE system typically consists of a system controller, a tester processor, and an FPGA. The controller coordinates the testing process, while the FPGA includes hardware accelerator circuits to generate commands and data for the device under test (DUT).
Why is there a growing demand for non-memory ATE systems?
The increasing complexity of electronic devices and the need for higher precision in testing to ensure functionality and reliability drive demand for non-memory ATE systems. These systems provide comprehensive testing capabilities for non-memory semiconductors.
What are the benefits of modular ATE platforms?
Modular ATE platforms offer cost-effective, flexible, and scalable testing solutions that can quickly adjust to new testing requirements. This adaptability is essential due to the variety of electronic products and the fast pace of technological innovation.
How does the ATE market respond to the trend of miniaturization in electronics?
The ATE market is innovating to create smaller, more portable devices that are not only space-saving but also capable of performing complex tests on miniature electronic components. This supports the demand for on-the-go and on-site testing capabilities.