Ensuring Microchip Quality: Advances in Wafer Level Reliability
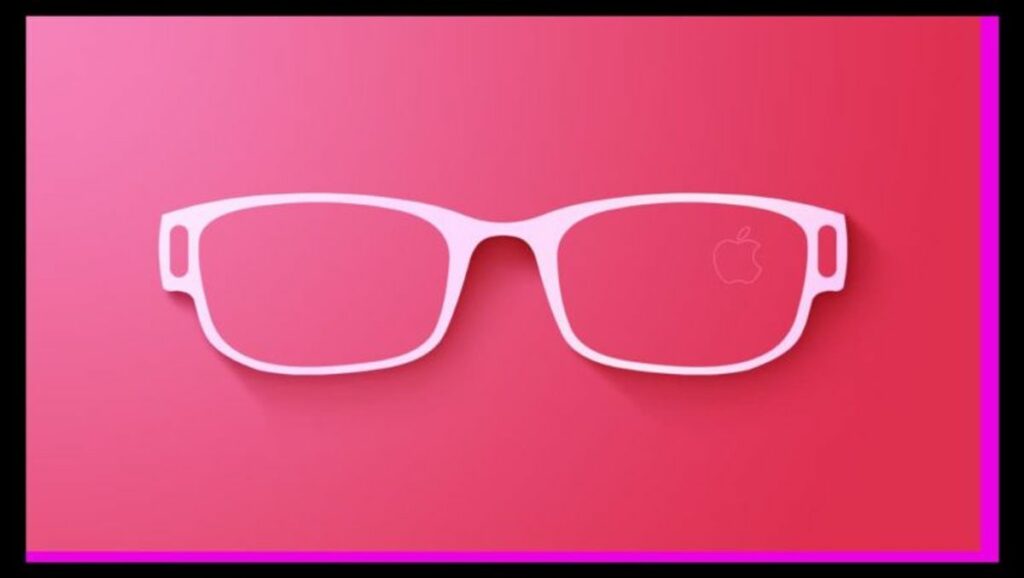
The semiconductor industry is at a pivotal juncture with the increasing demand for high-quality microchips and the challenges associated with ensuring their reliability at the wafer level. This article delves into the latest advancements and considerations in wafer level reliability, examining the supply dilemmas, inspection techniques, and the future of chiplet integration and packaging. Experts from various sectors provide insights into overcoming obstacles and enhancing the quality and security of silicon wafers, a critical component in modern electronics.
Key Takeaways
- The industry must address the silicon wafer supply dilemma, ensuring future availability while overcoming challenges in substrate flatness and thickness.
- Safety standards and thermal integrity, particularly in 2.5D structures, are paramount for enhancing wafer level reliability and reducing material defects.
- Advancements in wafer inspection and traceability, including the inspection of 3D wire bond structures and the use of nanoimprint technology, are critical for quality assurance.
- The evolution of chiplet integration highlights the need for lessons from automotive chipmakers, mixed-foundry chiplets, and government involvement in secure silicon.
- Future directions in wafer level packaging will focus on heterogeneous integration, optimizing cost and time-to-market, and extending chip design methodologies to advanced packaging.
The Silicon Wafer Supply Dilemma
CdrFrancis Leo on Future Availability
The semiconductor industry is at a crossroads, with systems companies increasingly dictating chip design to meet their specific needs. This shift is a departure from the traditional model where available chips were adapted to systems. CdrFrancis Leo emphasizes the importance of addressing the looming question: Will there be enough silicon wafers to meet the growing demand?
The supply of silicon wafers is critical to the industry’s ability to innovate and scale. As we push the boundaries of technology, the need for high-quality, reliable wafers becomes more pronounced. The industry must tackle challenges such as the ABF substrate shortage and the need for in-line monitoring to ensure a steady supply.
To understand the magnitude of the issue, consider the following points:
- The integration of advanced packaging techniques.
- The rise of specialized processors over general solutions.
- The increasing attention on smaller nodes, such as MRAM technology.
These factors contribute to the pressure on wafer supply, making it imperative to forecast and plan for future needs to avoid crippling advancements in the chip industry.
Challenges in Substrate Flatness and Thickness
The pursuit of ever-more sophisticated technologies has placed a spotlight on the critical parameters of substrate flatness and thickness. These parameters are essential for the next steps in microchip quality and performance. The flatness of a wafer, with its very tight tolerances, ensures that subsequent layers of material are deposited evenly, which is crucial for the functionality of the final semiconductor device.
In addition to flatness, local thickness variations and surface roughness are topics of significant concern. These variations can impact the electrical properties of the wafer and, consequently, the performance of the semiconductor devices. The mechanical properties of modern wafers are increasingly silicon-like, which presents both challenges and opportunities for material improvement. Researchers are actively addressing these substrate-related challenges to enhance device performance, reliability, and manufacturability.
As we strive to reduce the high density of certain critical defects, two main topics emerge for material improvement: lowering defect entities and refining the mechanical properties to meet the stringent demands of advanced packaging. This includes compatibility with both advanced and legacy nodes, as well as different semiconductor material systems. The table below summarizes the key areas of focus for substrate improvement:
Advances in Multi-Die Wafer Systems
The advent of multi-die wafer systems has brought about a paradigm shift in the semiconductor industry, offering unique flexibility and full traceability. These systems can handle up to 50 different wafers, with a swap time of less than 10 seconds, showcasing full multi-die capability. This rapid changeover is critical in meeting the diverse needs of modern electronics.
In terms of productivity, these systems merge two worlds by processing SMT components and dies directly from the wafer, combining die-attach and flip-chip processes in a single step. This integration not only maximizes performance but also leads to significant cost savings by eliminating the need for die taping and the associated quality and disposal costs.
Sustainability is another key advantage. Direct die processing from diced wafers negates the entire die-taping process, reducing tape waste. In a 24/7-SiP production environment, this could translate to saving 800 km of tape annually. Moreover, the high placement accuracy of up to 10 μm @ 3 σ ensures comprehensive quality management, reinforcing the system’s maximum performance.
Enhancing Wafer Level Reliability
Riccardo Vincelli on Defining Safety Standards
Following Riccardo Vincelli’s insights on safety standards, the semiconductor industry faces the critical task of ensuring that these standards are not only well-defined but also universally adopted and rigorously enforced. Safety and reliability are paramount, as the slightest defect can lead to catastrophic failure in applications ranging from consumer electronics to automotive systems.
To achieve this, a multi-faceted approach is necessary. It involves stringent testing protocols, continuous monitoring of manufacturing processes, and the implementation of robust quality control measures. Below is a list of key components in enhancing wafer level reliability:
- Development of comprehensive testing methodologies
- Adoption of advanced metrology tools
- Integration of real-time monitoring systems
- Enforcement of strict quality control standards
These components are essential in minimizing the risk of defects and ensuring that every chip meets the highest safety standards. As the industry progresses, the collaboration between chipmakers, equipment suppliers, and regulatory bodies will be crucial in maintaining the integrity of these standards.
Ed Korczynski on Thermal Integrity in 2.5D Structures
The thermal integrity of 2.5D structures is a critical aspect of microchip quality that cannot be overlooked. Ed Korczynski emphasizes the importance of maintaining a balance between thermal performance and the physical constraints of these advanced packaging solutions. The debate on whether a 2.5D device is more akin to a shrunken printed circuit board or an expanded chip highlights the unique challenges faced in this domain.
One of the primary concerns is the management of heat dissipation within the densely packed components. The integration of multiple dies on a single substrate necessitates innovative cooling strategies to prevent thermal hotspots that can lead to device failure. Research, such as the work by Pohl et al., has explored the electro-thermal behavior of components to optimize their performance in these complex environments.
Further complicating the issue is the need to address the transition temperature of materials like VO2, which are used for their thermochromic properties. Adjusting the insulator-to-metal transition (IMT) temperature without compromising the transition rate or introducing significant hysteresis is a challenge that researchers like Cui et al. are actively investigating. The goal is to achieve a balance that allows for efficient thermal management while maintaining the material’s functional integrity.
Improving Material Quality and Defect Reduction
The pursuit of reducing defect density is a critical aspect of enhancing microchip quality. By focusing on buffer layer optimization, manufacturers aim to improve yield and performance. This requires meticulous adjustments throughout the manufacturing process to ensure the lowest possible defect entities.
Material advancements are also pivotal. The mechanical properties of modern wafers are increasingly silicon-like, which presents challenges in maintaining flatness and managing local thickness variations. Addressing these issues is essential for the next wave of material improvements.
In the realm of defect management, the following points are key:
- A holistic approach, starting early in the design cycle, can lead to faster yield ramps and enhanced reliability.
- The integration of AI and ML in test and metrology is promising, but collaboration and time are needed to unlock their full potential.
- Identifying and mitigating sources of silent data corruption requires improved manufacturing screening and in-field repair strategies.
As technology evolves, the defect profile changes, necessitating new repair supports and increasing the complexity of design-for-test (DFT) insertion and verification. The industry must also address the challenges posed by macroscopic defects, which can be mitigated by precise control using techniques like focused ion beam (FIB) and nanoindentation.
Innovations in Wafer Inspection and Traceability
Jem on Inspecting 3D Wire Bond Structures
The inspection of 3D wire bond structures is a critical step in ensuring the quality and reliability of microchips. The hermetic sealing process is pivotal in assessing the operational viability of these intricate assemblies. Illustration 1 depicts the semiconductor chip, showcasing the delicate nature of the wire bonds, which are finer than human hair and can number in the hundreds for larger chips.
When considering the complexity of 3D advanced multi-die packages, such as Intel’s EMIB or TSMC’s CoWoS, the challenge of inspection becomes evident. Each wire, potentially requiring re-tuning, represents a point of potential failure. Moving away from traditional wiring methods is essential for progress in this area.
The technology readiness level for these structures is still in a rather theoretical state. However, advancements in single crystal nanobeams and thin film technologies suggest promising directions for enhanced sensitivity and reliability in strain sensor applications. The table below summarizes some of the key findings from recent studies:
Material Type | Application | Measurement | Electrical Property | Reference |
---|---|---|---|---|
Microwire | Strain switching | Mechanical deformation | Resistivity change | [74] |
Thin film | Piezoelectric strain sensor | Mechanical strain | Piezoelectric effect | [75] |
Micro- and nanocrystals | H2 concentration sensor | Chemical concentration | Resistivity change | [102] |
Nikolay on the Impact of Nanoimprint Technology
The advent of nanoimprint technology has marked a significant milestone in the microchip industry, particularly as we approach the sub-2nm scale. Nikolay’s insights reveal a transformative approach to patterning at the nanoscale, enabling unprecedented precision and consistency. This technology not only enhances the resolution of microchip features but also promises to streamline the manufacturing process.
Key benefits of nanoimprint technology include:
- Reduction in manufacturing complexity
- Lower production costs
- Improved throughput
- Enhanced resolution and alignment accuracy
As we delve into the specifics, it becomes clear that nanoimprint technology is not just a tool for the present but a foundation for future advancements. Its impact is quantifiable, with significant improvements in various aspects of wafer production and inspection. The table below summarizes the improvements observed:
Metric | Before Nanoimprint | After Nanoimprint |
---|---|---|
Feature Resolution (nm) | >5 | <2 |
Alignment Accuracy (nm) | ±10 | ±1 |
Throughput (wafers/hour) | 50 | 200 |
Production Cost Reduction (%) | 0 | 20 |
The integration of nanoimprint technology into existing production lines is a testament to the industry’s commitment to innovation and quality. As we push the boundaries of what’s possible in microchip fabrication, the role of such advanced techniques becomes increasingly crucial.
Ensuring Full Single-Die-Level Traceability
The semiconductor industry is increasingly focusing on the traceability of individual dies, recognizing its critical role in the supply chain and quality management. Full single-die-level traceability ensures that each die can be tracked from its origin on the wafer through to its final position on a circuit board. This level of detail is vital for identifying and addressing defects, as well as protecting intellectual property against reverse engineering.
Implementing such traceability systems offers unique flexibility and consistent sustainability in production. For instance, a wafer system capable of handling multiple wafers can swap them in less than 10 seconds, streamlining the process and reducing waste. Moreover, the ability to process dies directly from the diced wafer eliminates the need for die-taping, saving significant resources over time.
The integration of traceability with security measures is also essential. As the complexity of chips increases, with the integration of chiplets from multiple foundries, ensuring the provenance and security of each component becomes paramount. This approach not only addresses immediate quality concerns but also lays the groundwork for future advancements in secure silicon technology.
The Evolution of Chiplet Integration
Allen Rasafar on Lessons from Automotive Chipmakers
The automotive industry has long been at the forefront of integrating complex electronic systems, and chipmakers are taking note. Allen Rasafar’s insights into the sector reveal a focus on robustness and longevity, which are critical in automotive applications. These principles are now being applied to the broader semiconductor industry, particularly in the context of chiplet integration.
Chiplets have become a cornerstone for innovation, especially when it comes to managing power delivery and enhancing yield with advanced lithography techniques. The table below highlights the significance of chiplets in automotive applications, as discussed by Jerry Magera:
Aspect | Importance in Automotive |
---|---|
Power Delivery | Essential for 2nm devices |
Yield Management | Critical with EUV and stochastics |
System Integration | Key for electronic complexity |
Rasafar’s commentary on the industry’s shift from focusing on individual chips to entire systems echoes the sentiment expressed in the title ‘Thinking Big: From Chips To Systems‘. This holistic approach is not only optimizing the design and manufacturing processes but also ensuring that the end products meet the stringent safety and performance standards required by today’s consumers.
Christopher Wendt on Mixed-Foundry Chiplets
The race toward mixed-foundry chiplets is heating up as the semiconductor industry seeks innovative solutions to meet the ever-increasing demand for computational power. Christopher Wendt’s insights shed light on the complexities and potential of combining chiplets from different foundries to create more powerful and versatile semiconductor devices.
Key benefits of mixed-foundry chiplet integration include enhanced performance, reduced time-to-market, and cost savings. However, this approach also introduces challenges such as ensuring compatibility and maintaining quality across different manufacturing processes. The following list highlights the main considerations for successful mixed-foundry chiplet integration:
- Compatibility of electrical and physical interfaces
- Synchronization of design and testing methodologies
- Quality assurance across disparate production lines
- Intellectual property management and security
As the industry navigates the race toward mixed-foundry chiplets, collaboration and standardization will be crucial to overcoming these hurdles and fully realizing the advantages of this innovative approach.
Serge Leef on Government’s Role in Secure Silicon
Serge Leef emphasizes the importance of government involvement in the advancement of secure silicon technologies. The government’s role is pivotal in providing the necessary funding and support for the development of sub-3nm designs and heterogeneous integration (HI), which are likely to be dominated by a select few companies. The rest will turn to HI for their needs. Ensuring the provenance, traceability, and security of chiplets, especially when they originate from multiple foundries, is a critical aspect that requires attention.
In addressing chiplet security, Leef outlines a multi-layered approach. The supply chain, protection against side channel attacks, reverse engineering, and on-board security measures for chiplets are all vital considerations. The interposer, while offering opportunities, also presents challenges as it can contain sensitive information. A comprehensive security architecture across HI is necessary, and awareness of architectural requirements is crucial.
Leef also points out the potential risks associated with interposer-based architectures, such as the exposure of the interposer communications infrastructure. To mitigate these risks, shifting sensitive elements like routing tables to trusted facilities in the USA is a strategy under consideration. Furthermore, organizations like NIST are actively working on establishing standards for secure silicon.
- Importance of government funding and support
- Challenges in securing chiplets from multiple foundries
- Multi-layered security approach for chiplets
- Risks in interposer-based architectures
- NIST’s role in standardizing secure silicon
Future Directions in Wafer Level Packaging
Trends in Heterogeneous Integration
Heterogeneous integration (HI) represents a significant shift in the semiconductor industry, moving beyond the limitations of Moore’s Law to address the increasing complexity of next-generation computing. The integration of diverse technologies within a single system is not only a technical challenge but also a strategic opportunity to enhance performance and reduce costs.
The development of HI involves a multidisciplinary approach, combining various technologies each with its own cost implications and application suitability. This integration allows for smaller, high-yielding chips and optimal process selection, which can lead to significant cost reductions. Moreover, the scale of integration has evolved, with a focus on system-level verification and fan-out wafer-level packaging, which offers advantages over traditional flip-chip packaging.
As we embrace the ‘Beyond Moore’ era, HI is crucial for mitigating development costs while improving performance. The die size challenge, driven by the need for high performance, can be addressed through HI, resulting in lower power consumption, reduced latency, and increased bandwidths. The table below summarizes the key benefits of HI compared to traditional packaging methods:
Benefit | Traditional Packaging | Heterogeneous Integration |
---|---|---|
Cost | Higher | Lower |
Performance | Limited by single technology | Enhanced by multiple technologies |
Power Consumption | Higher | Lower |
Latency | Higher | Lower |
Bandwidth | Limited | Higher |
Optimizing Cost and Time-to-Market with Chiplets
The integration of chiplets into wafer-level packaging represents a significant shift in the semiconductor industry, aiming to balance performance with economic efficiency. Chiplets offer a pathway to cost optimization by allowing for higher fab yields of smaller individual dies, which can translate into substantial savings in fabrication costs. This modular approach also facilitates the use of lower-cost nodes for specific integrated circuit (IC) functions, further enhancing the economic benefits.
In contrast to the traditional monolithic design, which often leads to higher costs and longer time-to-market due to complex chip design and larger chip sizes, chiplets provide a more flexible solution. The partitioning of dies enables more dies per wafer and a higher yield, which are crucial factors in cost reduction. Additionally, the ability to optimize the node per chiplet and the potential for higher density interconnects contribute to a faster time-to-market.
The table below summarizes the advantages of chiplet integration in terms of cost and time-to-market:
Advantage | Description |
---|---|
Higher Yield | More dies per wafer lead to optimized costs. |
Flexibility | Customization and speedy upgrades are possible with specialized processing elements. |
Economic Efficiency | Use of lower-cost nodes for certain IC functions reduces overall costs. |
Time-to-Market | Finer bump or pad pitch and node optimization per chiplet accelerate product development. |
As the industry continues to evolve, the role of chiplets in achieving power-performance-area-cost plus time-to-market (PPACt) objectives is becoming increasingly recognized. The Open Compute Project highlights wafer-level packaging (FOWLP) and chiplet integration as key strategies for improvement, IP reuse, performance, and cost-effective manufacturing.
Extending Chip Design Methodologies to Advanced Packaging
The transition to advanced packaging represents a paradigm shift in how we approach chip design. Advanced packaging technologies, such as 2.5D/3D integration and fan-out methods, demand a holistic co-design strategy that encompasses not only the chiplets themselves but also their communication, security, and reliability within the package. This necessitates a detailed understanding of the substrate and assembly processes involved.
Key considerations in extending chip design methodologies include addressing thermal and thermo-mechanical constraints, ensuring robust power delivery, and optimizing for test and repair. The table below outlines some of the advanced packaging platforms and their characteristics:
Packaging Platform | Integration Type | Key Features |
---|---|---|
EMIB (Intel) | 2.5D | Bridge-based interconnects |
CoWoS (TSMC) | 2.5D/3D | Silicon interposer technology |
Fan-Out | 2.5D | Redistribution layer (RDL) enhancements |
Si Interposer | 2.5D | High-density connections |
As the industry moves forward, the National Advanced Packaging Manufacturing Program (NAPMP) aims to support these co-design efforts, ensuring that the advanced packaging platforms are not only technically feasible but also economically viable. The goal is to create a simpler and flatter hierarchy of dielets, whether they are stacked or integrated side by side, to form complex systems that meet the evolving demands of the market.
Conclusion
In summary, the advancements in wafer level reliability are pivotal for the future of microchip quality. The insights from industry experts such as CdrFrancis Leo, Riccardo Vincelli, and others highlight the multifaceted challenges and developments in silicon wafer supply, safety, and inspection techniques. The push towards sub-3nm designs, the adoption of chiplets, and heterogenous integration are reshaping the landscape of chip manufacturing. With the government’s role in funding and the need for integration, traceability, and security, the industry is poised for significant transformation. Equipment and processes are evolving to meet the demands of finer substrates and higher density chiplets, aiming for optimized costs and faster time-to-market. As we look to the future, the focus on reducing defect densities, improving mechanical properties, and ensuring full traceability will be crucial in maintaining consistent sustainability and reliability in the ever-advancing world of microchip technology.
Frequently Asked Questions
Will there be enough silicon wafers to meet future demands?
CdrFrancis Leo has expressed concerns about future availability, indicating that while current supply meets demand, the industry must address potential shortages as technology advances and consumption increases.
What are the safety standards for wafer level reliability?
Riccardo Vincelli emphasizes the importance of defining rigorous safety standards to ensure the reliability and integrity of microchips, which are critical in various applications including automotive and data centers.
How does 3D structure affect wire bond inspection?
Jem discusses the challenges in inspecting 3D wire bond structures, highlighting the need for advanced inspection techniques to detect defects and ensure the reliability of complex chip architectures.
What impact has nanoimprint technology had on wafer production?
Nikolay points out that nanoimprint technology has gained a solid foothold, offering improved patterning capabilities and contributing to the evolution of substrate quality and precision in wafer production.
How is thermal integrity maintained in 2.5D chip structures?
Ed Korczynski addresses the growing challenges in maintaining thermal integrity, particularly in 2.5D structures, and underscores the need for innovative solutions to manage heat dissipation in densely packed chips.
What can data center chipmakers learn from the automotive industry?
Allen Rasafar suggests that data center chipmakers can benefit from the automotive industry’s experience in chiplet integration and reliability, which can inform their own practices for achieving high-quality microchip production.