Exploring the Future of Electronics: Innovations in Wafer Fab
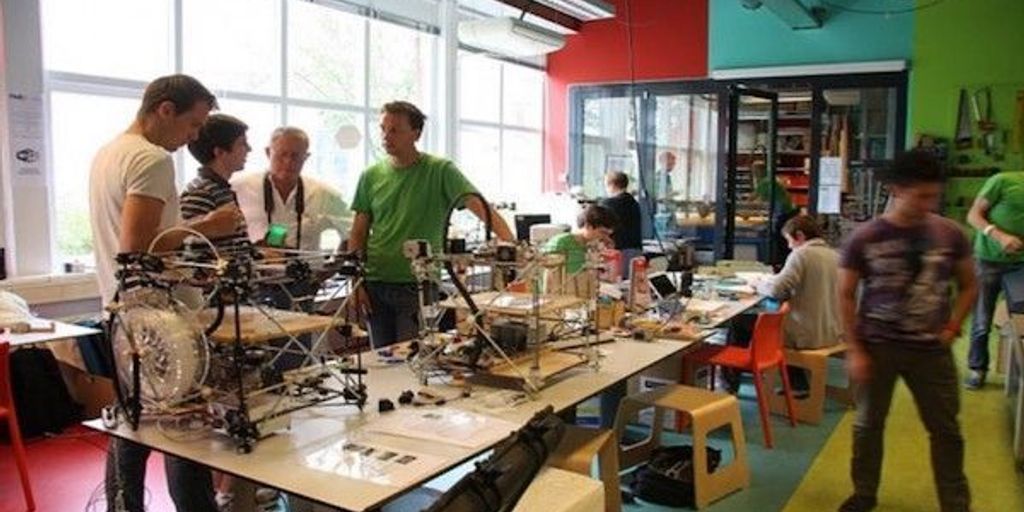
The landscape of electronics manufacturing is rapidly evolving, with wafer fabrication at the heart of this transformation. Innovations in wafer fab, driven by advancements in technology and materials science, are set to redefine the capabilities of electronic devices. This article delves into the future of electronics through the lens of wafer fabrication, exploring the pivotal role of nanotechnology, the challenges and innovations in ultra-thin silicon wafers, and the integration of sustainable practices.
Key Takeaways
- Nanotechnology is revolutionizing wafer fabrication by enhancing material properties, automating processes, and fostering interdisciplinary collaborations.
- Advancements in ultra-thin silicon wafers focus on overcoming manufacturing challenges, refining thickness control techniques, and exploring alternative substrates.
- Sustainable practices are increasingly integral, aiming to reduce environmental impacts and utilize renewable resources in wafer fabrication.
- Emerging technologies such as thin film transfer and advanced lithography are setting new directions for semiconductor devices.
- Collaboration between academia and industry is crucial for innovation in wafer manufacturing, highlighting the importance of knowledge exchange and joint research initiatives.
The Role of Nanotechnology in Wafer Fab
Enhancing Material Properties
Nanotechnology has revolutionized the semiconductor industry by enabling the manipulation of materials at the atomic or molecular level. This capability allows for the creation of wafers with enhanced electrical, thermal, and mechanical properties, which are crucial for the development of more efficient and powerful electronic devices. Nanoscale materials present us with astonishing chemical and physical properties that help materialize applications such as single molecular sensing and more.
Driving Process Automation
The integration of nanotechnology in wafer fabrication has been pivotal in advancing manufacturing automation. Nanotechnology-enabled sensors and monitoring devices provide real-time insights into the fabrication processes, facilitating proactive maintenance and optimization of equipment performance. This not only enhances the efficiency but also the reliability of the manufacturing processes.
Facilitating Interdisciplinary Collaboration
Nanotechnology fosters significant interdisciplinary collaboration, merging fields like materials science, mechanical engineering, and electronics to innovate and enhance wafer fabrication. By promoting collaboration and knowledge exchange within the semiconductor industry, nanotechnology helps in driving innovation and shaping the future of technology.
Advancements in Ultra-Thin Silicon Wafers
Challenges in Manufacturing
Significant advancements have been made in equipment and tooling to address the challenges associated with ultra-thin silicon wafer manufacturing. Specialized wafer handling and support systems have been developed to cater to the fragility of ultra-thin wafers. Cutting-edge thinning equipment with higher precision and automation capabilities aids in achieving the desired thickness and uniformity. Advanced surface treatment and cleaning technologies ensure optimum wafer quality.
Innovative Techniques for Thickness Control
The industry has witnessed remarkable innovations that tackle the challenges associated with ultra-thin silicon wafer manufacturing. Advanced wafer thinning techniques, including grinding, etching, and polishing, have been developed for precise thickness control. Thin film transfer technologies, such as bonding and layer transfer, offer alternative approaches to obtaining ultra-thin wafers.
Exploring Alternative Substrates
The journey towards ultra-thin silicon wafer manufacturing continues to evolve. Ongoing research focuses on further improving thickness control, uniformity, and defect reduction. Advancements in thin film transfer technologies and exploration of alternative substrates hold promise for future advancements.
Sustainable Practices in Wafer Fabrication
Reducing Environmental Impact
Sustainable wafer fabrication is increasingly focusing on reducing the environmental impact of manufacturing processes. Innovations include the use of recycled materials and advanced techniques to capture hazardous gases, such as membrane separation and cryogenic recovery. These efforts are crucial for climate-friendly chip manufacturing.
Utilizing Renewable Resources
The shift towards utilizing renewable resources in wafer fabrication is evident. Facilities are integrating more sustainable energy sources like solar and wind power to minimize carbon footprints. This transition not only supports environmental sustainability but also enhances the long-term viability of manufacturing operations.
Promoting Sustainable Innovation
Promoting sustainable innovation involves continuous improvement in materials and processes. The industry is adopting practices like recycling silicon carbide and improving process efficiencies. These innovations are essential for maintaining competitiveness in the rapidly evolving semiconductor industry.
Emerging Technologies in Wafer Fab
Thin Film Transfer Technologies
The adoption of thin film transfer technologies is pivotal in the evolution of semiconductor devices. These technologies enable the production of ultra-thin and high-quality films essential for advanced electronics. Key benefits include improved device performance and increased manufacturing flexibility.
Advancements in Lithography
Lithography continues to be a cornerstone of semiconductor manufacturing, with new advancements pushing the boundaries of what’s possible. The integration of extreme ultraviolet (EUV) lithography has been a game changer, allowing for smaller, more complex patterns. This technology is crucial for the next generation of microprocessors and memory devices.
Future Directions for Semiconductor Devices
The semiconductor industry is constantly evolving, with research focused on scaling down device sizes and improving efficiency. Future directions include the development of 3D NAND technology, which offers significant advantages in terms of storage capacity and speed. The exploration of new materials and architectures is also expected to drive innovation in this field.
Collaboration and Knowledge Exchange in Semiconductor Industry
Role of Academic and Industrial Partnerships
Strong partnerships between academia and industry are crucial for fostering innovation in semiconductor technology. These collaborations often lead to breakthroughs in research and development, as academic institutions provide theoretical insights and novel approaches, while industrial entities offer practical applications and scalability.
Impact on Innovation
Collaborative efforts in the semiconductor industry significantly accelerate the pace of technological advancement. By sharing resources, knowledge, and expertise, companies and research institutions can tackle complex challenges more effectively and bring innovative solutions to market faster.
Case Studies of Successful Collaborations
Several case studies highlight the benefits of collaboration in the semiconductor industry:
- Intel and Micron Technology partnership on 3D XPoint technology
- Collaboration between IBM and Samsung on 7nm chip technology
- Joint development by TSMC and Synopsys on advanced node technologies
These examples demonstrate how collaborative efforts can lead to significant technological advancements and market success.
Automation in Wafer Manufacturing
Real-time Monitoring and Control
Automation enhances precision and efficiency in semiconductor manufacturing, significantly impacting the quality and consistency of wafer production. Real-time monitoring systems, often powered by advanced sensors and AI, provide critical data that allows for immediate adjustments and ensures optimal operating conditions throughout the fabrication process.
Proactive Maintenance Strategies
Proactive maintenance is crucial in minimizing downtime and extending the life of equipment. By utilizing predictive analytics and machine learning, manufacturers can anticipate equipment failures before they occur and schedule repairs during non-operational periods, thus maintaining continuous production flow.
Enhancing Equipment Performance
Advanced automation technologies, including robotics and AI, play a pivotal role in improving the performance and capabilities of wafer fabrication equipment. Robotic systems are particularly effective in handling delicate wafers, reducing human error, and increasing throughput. This integration of technology leads to more cost-effective and efficient production processes.
Future Directions for Wafer Fab
Potential of 3D NAND and Advanced Packaging
The semiconductor industry is on the brink of a significant transformation with the potential of 3D NAND and advanced packaging technologies. These innovations promise to dramatically increase storage capacity and speed, while reducing power consumption. The integration of 3D NAND is expected to revolutionize memory storage systems, making them more efficient and scalable.
Impact of High-NA EUV on Wafer Fab
High-numeric-aperture extreme ultraviolet (High-NA EUV) lithography is set to redefine the limits of wafer fabrication. This technology enables finer patterning, crucial for next-generation semiconductor devices. The adoption of High-NA EUV will facilitate the production of smaller, more powerful chips, essential for future computing needs.
Long-term Tech Forecast and Innovations
Looking ahead, the semiconductor industry faces exciting prospects with continuous innovations. Key areas of focus include enhancing chip performance, reducing energy consumption, and integrating novel materials. The long-term technology forecast suggests a robust pipeline of developments that will sustain the industry’s growth and technological evolution.
Challenges and Innovations in Thin Silicon Wafer Manufacturing
Addressing Production Challenges
Manufacturing ultra-thin silicon wafers presents several significant challenges. One major obstacle is the delicate nature of the wafers, making handling and fragility issues paramount. Additionally, attaining precise thickness and uniformity during the thinning process is complex. Controlling wafer warpage, bowing, and reducing defects and impurities are key challenges to overcome.
Developing New Materials
The industry has witnessed remarkable innovations that tackle these challenges. Advanced wafer thinning techniques, including grinding, etching, and polishing, have been developed for precise thickness control. Thin film transfer technologies, such as bonding and layer transfer, offer alternative approaches to obtaining ultra-thin wafers.
Enhancing Device Performance
Significant advancements have been made in equipment and tooling to address the challenges associated with ultra-thin silicon wafer manufacturing. Specialized wafer handling and support systems have been developed to cater to the fragility of ultra-thin wafers. Cutting-edge thinning equipment with higher precision and automation capabilities aids in achieving the desired thickness and uniformity. Advanced surface treatment and cleaning technologies ensure optimum wafer quality.
Conclusion
As we look towards the future of electronics, the innovations in wafer fabrication stand as a testament to the relentless pursuit of advancement in the semiconductor industry. The integration of nanotechnology has not only enhanced the capabilities of wafer manufacturing but also set a new standard for sustainability and efficiency. The exploration of ultra-thin silicon wafers and alternative substrates promises to revolutionize the design and functionality of future electronic devices. By embracing these innovations, the industry is poised to overcome existing challenges and unlock new possibilities, ensuring a future where electronic devices continue to evolve at an unprecedented pace. This journey of innovation underscores the importance of continued research and collaboration to drive the semiconductor industry forward.
Frequently Asked Questions
What is the role of nanotechnology in wafer fabrication?
Nanotechnology plays a critical role in wafer fabrication by enhancing material properties, driving process automation, and facilitating interdisciplinary collaboration. It enables the manipulation of materials at the atomic or molecular level, leading to innovation and improved performance in semiconductor manufacturing.
How are ultra-thin silicon wafers impacting the semiconductor industry?
Ultra-thin silicon wafers are crucial for the development of advanced electronic devices. They require precise manufacturing techniques to control thickness and reduce defects, which are significant challenges that drive innovations in the industry.
What sustainable practices are being implemented in wafer fabrication?
Wafer fabrication is adopting sustainable practices such as reducing environmental impact, utilizing renewable resources, and promoting sustainable innovation to ensure eco-friendly production processes.
What emerging technologies are shaping the future of wafer fab?
Emerging technologies such as thin film transfer technologies, advancements in lithography, and the development of new semiconductor devices like 3D NAND are shaping the future of wafer fabrication.
How does collaboration benefit the semiconductor industry?
Collaboration between academic and industrial partners fosters knowledge exchange and drives innovation in the semiconductor industry. It leads to successful collaborations that can tackle complex challenges and propel technological advancements.
What are the future directions for wafer fab technology?
Future directions for wafer fab technology include the potential of advanced packaging, the impact of high-NA EUV lithography, and ongoing innovations that could redefine semiconductor manufacturing through 2040 and beyond.