Exploring the Impact of Wafer Size on Chip Performance
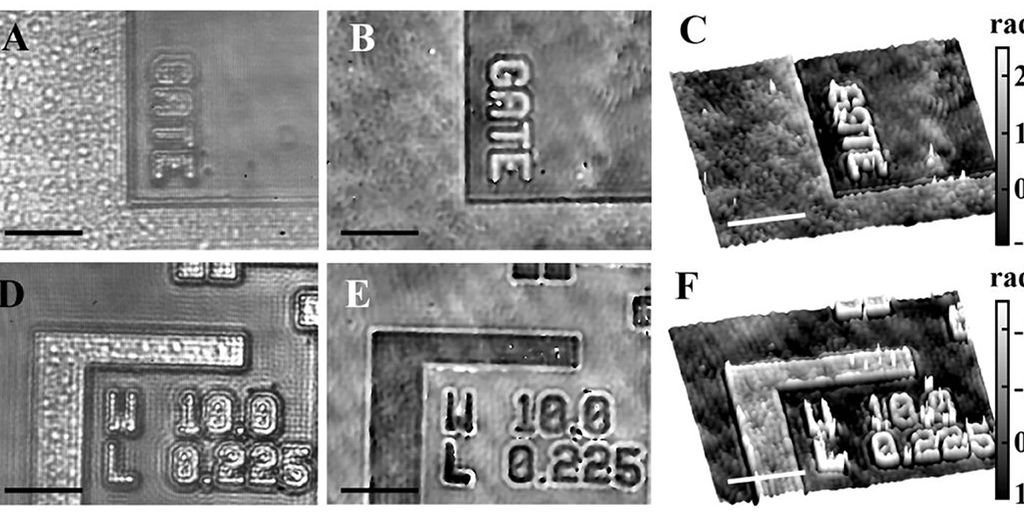
In the semiconductor industry, wafer size plays a crucial role in defining the performance and economic feasibility of chips. As technology advances, the implications of choosing a specific wafer size extend beyond simple manufacturing concerns to strategic business decisions and design considerations. This article explores how wafer size impacts chip performance, fabrication technology, economic strategies, and future industry trends.
Key Takeaways
- Wafer size significantly influences the number of die per wafer, affecting production efficiency and cost-effectiveness.
- Larger wafers can improve wafer utilization and potentially enhance supply chain dynamics by increasing the rate of product fabrication.
- The choice of wafer size is strategically driven, focusing on investment and long-term business implications rather than just technical aspects.
- Design considerations for wafer-scale chips require a holistic approach to architecture, considering integration density and system co-design.
- Future trends in wafer size will likely focus on balancing technological capabilities with economic and supply chain factors.
The Basics of Wafer Size and Chip Performance
Understanding Wafer Size
Wafers are characterized by their diameter and thickness. The diameter of wafers has steadily increased over the years to improve productivity and reduce cost. This growth in size allows for more chips to be produced from a single wafer, enhancing manufacturing efficiency.
Factors Influencing Chip Performance
Several factors influence the performance of chips, including material composition, structure, and production processes. The interplay between these elements is crucial for optimized semiconductor manufacturing, ensuring the functionality and efficiency of the chips.
Correlation Between Wafer Size and Performance
The size of the wafer directly impacts the number of dies per wafer, which in turn affects the cost per chip. A larger wafer size can lead to significant cost savings, making it a critical factor in the economic considerations of semiconductor production.
Technological Advancements in Wafer Fabrication
Innovations in Wafer Production
The semiconductor industry has seen significant advancements in wafer production, primarily driven by the need for higher efficiency and greater throughput. Innovations such as epitaxy, which adds a thin layer to enhance the wafer’s electrical properties, and advanced lithography techniques, have been pivotal in improving the performance of semiconductor devices.
Impact of Larger Wafers on Fabrication
The shift towards larger wafer sizes, such as 300mm, has been a key factor in scaling production capabilities. Larger wafers allow for more chips to be produced per wafer, effectively reducing costs and improving production efficiency. However, this shift requires substantial investment in new manufacturing equipment and technology.
Challenges in Scaling Up Wafer Size
While the benefits of larger wafers are clear, the transition poses several challenges. These include the need for new fabrication facilities, increased capital expenditure, and the potential for higher initial defect rates. Managing these challenges is crucial for semiconductor companies aiming to leverage the advantages of larger wafer sizes.
Economic Implications of Wafer Size Choices
Cost Analysis of Different Wafer Sizes
The economic impact of wafer size is significant in the semiconductor industry. Wafer size certainly dominates the cost of developing a semiconductor product. For instance, using a 200 mm wafer will generally be less expensive than a 300 mm wafer, considering both the cost of the wafer itself and associated FAB and OSAT costs.
Investment Considerations for Semiconductor Companies
Choosing the right wafer size is often more about investment and strategic considerations than technical ones. The decision on wafer size affects the entire end-to-end semiconductor production flow, making it crucial for companies to spend ample time analyzing the pros and costs.
Strategic Decisions in Wafer Selection
The choice of wafer size impacts various aspects of semiconductor manufacturing, from cost to yield. Semiconductor companies must balance factors such as die per wafer and wafer utilization to optimize costs and production efficiency. Larger wafers can mean fewer unusable areas at the edges, which is a critical consideration for high-demand products.
Wafer Size and Its Impact on Semiconductor Yield
Yield Optimization Strategies
In the semiconductor industry, yield optimization is crucial for maximizing profitability and efficiency. Strategies often involve enhancing fabrication techniques, improving material quality, and fine-tuning equipment calibration. These efforts are directly influenced by the choice of wafer size, as larger wafers may introduce complexities that require specialized handling and process adjustments.
Benefits of Larger Wafers on Yield
Larger wafers offer the potential to produce more dies per unit area, which can significantly increase the gross die yield. This advantage is tempered by the need for more sophisticated wafer handling systems to maintain yield rates. The benefits extend to the supply chain, allowing for faster production rates and potentially lower costs per die.
Limitations and Yield Loss Factors
While larger wafers can increase the number of dies, they also bring challenges such as higher initial defects and yield loss during scaling. The process of perfecting semiconductor techniques to accommodate larger wafers takes time, and the learning curve can initially lead to decreased yield. However, as processes mature, the yield can improve, aligning closer to that of smaller wafers.
Design Considerations for Different Wafer Sizes
Architectural Design for Wafer Scale Chips
The architectural design for wafer scale chips must address the significant challenges in design space exploration, system implementation, and tool chain development. These challenges arise due to the extended integration density and programmability that wafer-scale chips offer.
Trade-offs in Chip Design
Designing chips for different wafer sizes involves balancing several factors. Key considerations include die-to-die bandwidth and the number of die per wafer, which directly impacts cost efficiency and production scalability.
Co-design of Larger Systems
In the co-design of larger systems, the interaction between wafer size and system architecture becomes crucial. Larger wafers can enhance wafer utilization, reducing the unusable area at the edges, which is particularly beneficial for larger die sizes.
Future Trends in Wafer Size and Industry Impact
Predictions for Wafer Size Evolution
The semiconductor industry is poised for significant changes in wafer size, with predictions leaning towards larger diameters to enhance production efficiency and meet growing demands. The global semiconductor wafer market size is estimated to be valued at USD 27.35 billion in 2030, indicating a robust growth trajectory influenced by evolving wafer sizes.
Potential Industry Shifts
As wafer sizes increase, the industry may witness shifts in manufacturing dynamics and supply chain configurations. Larger wafers could lead to more centralized production facilities, requiring adjustments in logistics and distribution strategies.
Adapting to Future Wafer Sizes
The transition to larger wafer sizes necessitates strategic planning and adaptation by semiconductor companies. This involves investment in new technologies and reevaluation of production processes to accommodate the changes in wafer dimensions and associated manufacturing challenges.
Case Studies: Successes and Challenges with Various Wafer Sizes
Examples of Successful Wafer Size Implementations
Several case studies highlight the benefits of larger wafer sizes in semiconductor manufacturing. For instance, larger wafers allow for more die per wafer, which can significantly reduce costs and increase production efficiency. Successful implementations have shown that the transition to larger wafers can be a strategic move to enhance competitiveness and meet higher demand.
Challenges Faced by Industry Leaders
Adopting larger wafer sizes is not without its challenges. Industry leaders have encountered issues such as increased capital investment for new equipment and the need for revised fabrication processes. The complexity of scaling up to larger wafers requires careful planning and execution to avoid yield loss and maintain quality standards.
Lessons Learned from Wafer Size Changes
The semiconductor industry has gleaned important lessons from the shift to larger wafer sizes. Key takeaways include the importance of strategic planning and the impact of wafer size on the entire production flow. Companies have learned that while larger wafers can offer significant advantages, the decision to switch must be balanced with considerations of cost, yield, and market demand.
Conclusion
In this article, we have explored the multifaceted impact of wafer size on chip performance, highlighting how it influences everything from cost efficiency to production yield and design considerations. As we’ve seen, the choice of wafer size is not merely a technical decision but a strategic one, deeply intertwined with investment considerations and market demands. Larger wafers can enhance die per wafer ratios and reduce the unusable edge area, potentially lowering costs and increasing production efficiency. However, the transition to larger wafers also requires significant investment in new manufacturing tools and processes, making it a critical decision for semiconductor companies. Ultimately, the selection of wafer size is a balancing act that requires careful analysis of both the potential benefits and the associated costs, ensuring that the chosen size aligns with the company’s strategic goals and market position.
Frequently Asked Questions
What is the impact of wafer size on chip performance?
Larger wafer sizes allow for more dies per unit area, enhancing fabrication and assembly throughput, which can positively impact the supply chain and overall chip performance.
How does wafer size influence semiconductor yield?
Larger wafers can improve yield by reducing the relative amount of unusable edge area, although the benefits are more pronounced for larger die sizes.
What are the economic considerations of choosing a wafer size?
Wafer size affects the cost of development, with larger wafers generally increasing the cost due to higher material and processing expenses. Companies must balance these costs against potential yield and throughput benefits.
What are the challenges in scaling up wafer sizes?
Scaling up wafer sizes involves significant challenges including the need for new fabrication tools and technologies, and potential yield loss due to increased complexity.
How does wafer size impact the design of semiconductor chips?
Larger wafer sizes necessitate considerations for die-to-die bandwidth, integration density, and system programmability, posing challenges in design space exploration and system implementation.
What future trends are predicted for wafer sizes in the semiconductor industry?
The industry is expected to gradually move towards larger wafer sizes as technology and processes improve, which will likely lead to shifts in design strategies and manufacturing practices.