Exploring the Wafer Manufacturing Process: From Start to Finish
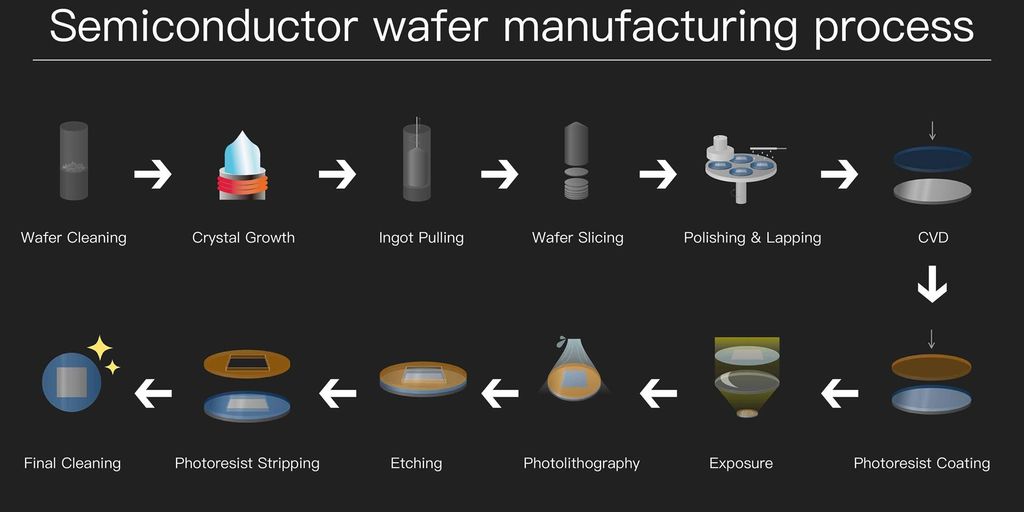
The journey of turning raw silicon into a polished wafer is a fascinating one. This process is the backbone of the semiconductor industry and involves many steps, each crucial to the final product. From growing silicon ingots to slicing and polishing wafers, every phase is about precision and quality. In this article, we’ll take a closer look at the entire wafer manufacturing process, from start to finish.
Key Takeaways
- Silicon ingot growth starts with extracting and purifying raw materials.
- Wafers are sliced and polished to achieve the necessary flatness and smoothness.
- Cleaning and inspection steps ensure that wafers are free from defects.
- Photoresist and photolithography are used to transfer patterns onto the wafer.
- Quality control and final testing are critical to ensure the reliability of the wafers.
Silicon Ingot Growth
Silicon ingot growth is a crucial step in making semiconductors. It starts with heating and melting high-purity silicon in a crucible. The molten silicon is then cooled and solidified into a cylindrical ingot. This ingot is later sliced into thin wafers, which are the main building blocks for semiconductor devices.
Wafer Slicing and Polishing
Slicing Techniques
Once the silicon ingot is ready, it is sliced into thin wafers using a diamond saw. This step, known as wafer slicing or wafer dicing, demands high precision to ensure the wafers are of the correct thickness and free from defects. Accurate slicing is crucial for the performance of the final semiconductor devices.
Polishing Methods
After slicing, the wafers undergo polishing to remove any surface imperfections. This process often involves chemical-mechanical planarization (CMP), which uses a slurry containing abrasive particles and a chemical reactant. The goal is to achieve a smooth, mirror-like surface.
Ensuring Surface Flatness
Polishing is essential to ensure the wafers are flat and smooth. Any tiny imperfections can affect the performance and reliability of the semiconductor devices. The process is done gradually to avoid damaging the wafer, making it one step closer to optimal semiconductor conditions.
Cleaning and Inspection
Cleaning Processes
The cleaning process is crucial to ensure that the wafer is free from contaminants that can cause defects in the final product. The first step involves rinsing the semiconductor wafers with deionized (DI) water to wash away loose particles and initial surface impurities. Chemical and plasma cleaning are commonly used methods to remove more stubborn contaminants. These methods ensure that the wafer is as clean as possible before moving on to the next steps.
Inspection Techniques
After cleaning, the wafer undergoes inspection to detect any defects that may have been missed during cleaning. Optical inspection and scanning electron microscopy are two commonly used techniques for wafer inspection. These methods help identify any remaining particles or defects that could affect the wafer’s performance.
Defect Detection
Defect detection is a critical part of the inspection process. Even a small particle left on the wafer’s surface can cause a short circuit, leading to a malfunctioning chip. Therefore, thorough inspection is essential to ensure the quality of the final product.
Photoresist and Photolithography
In semiconductor manufacturing, photolithography is one of the most important steps. This process involves transferring a geometric pattern from a mask to the surface of a wafer using a photosensitive material called photoresist. The mask contains the inverse pattern of the integrated circuit that will be produced on the wafer.
Etching and Doping
Etching and doping are two separate processes, but they often go hand-in-hand during semiconductor manufacturing. Here are some key points to understand about these processes:
Thin Film Deposition and Annealing
Thin film deposition and annealing are crucial steps in making semiconductor devices. The quality of the thin film can greatly affect the device’s performance. Understanding these processes is essential for anyone involved in semiconductor manufacturing.
Wire Bonding and Packaging
Wire bonding and packaging are key steps in making semiconductors. This process connects the chip to the outside world through wire bonding, then covers it with a protective layer. Wire bonding ensures the chip works well and lasts long. It involves attaching wires to specific bond pads on the chip using ultrasonic energy or heat. This is usually done with wedge bonding, ball bonding, or ribbon bonding techniques. After wire bonding, the chip is covered with a protective layer to keep it safe from damage and corrosion. The protective layer is often made of epoxy, plastic, or ceramic.
Quality Control and Final Testing
Quality control and final testing are crucial steps in semiconductor manufacturing. These tests ensure that the final product meets the necessary specifications and functions as intended, reducing the risk of customer complaints or returns. By performing these tests, engineers and businesses can identify any defects or issues that may have arisen during the manufacturing process and correct them before the product is released into the market.
Conclusion
In conclusion, the wafer manufacturing process is a fascinating journey that transforms raw silicon into the essential building blocks of modern electronics. Each step, from silicon ingot growth to final testing, requires precision and care to ensure the highest quality. This process is not just about making wafers; it’s about creating the foundation for the technology that powers our daily lives. By understanding this process, we gain a deeper appreciation for the intricate work that goes into the devices we often take for granted.
Frequently Asked Questions
What is the first step in making silicon wafers?
The first step in making silicon wafers is extracting and purifying raw silicon from sand.
How are silicon ingots grown?
Silicon ingots are grown using special techniques like the Czochralski process, where a seed crystal is dipped into molten silicon and slowly pulled up to form a large crystal.
What happens during wafer slicing?
During wafer slicing, the silicon ingot is cut into thin, round wafers using a wire saw or diamond blade.
Why is wafer cleaning important?
Cleaning wafers is important to remove any contaminants that could affect the performance of the final semiconductor device.
What is photolithography used for?
Photolithography is used to create detailed patterns on the wafer’s surface, which are essential for building semiconductor circuits.
How are defects detected in wafers?
Defects in wafers are detected using various inspection techniques, including visual inspections and advanced tools like scanning electron microscopes.